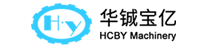
1. Characteristics of centrifuge
According to the functions and structures, the centrifuge can be divided into different types. However, whether they are filtration type, separation type or sedimentation type, they have the following common characteristics:
(1) The drum is a high-speed rotating part.
(2) The separation space is formed with the drum as the main body.
(3) The drum has a special-shaped structure.
(4) The material to be separated is a fluid.
(5) There are some metal or non-metal connecting parts or mating parts in the drum.
The above characteristics of the drum show that the core part of the centrifuge is a composite stress part. Its special-shaped structure leads to the stress distribution of the parts in multiple areas. Due to the cooperation of multiple parts, the galvanic couple may occur.
2. Possible corrosion
The corrosion of the centrifuge can be divided into uniform corrosion and local corrosion. Uniform corrosion is easy to be found, so it will not be discussed in this article. Local corrosion will be discussed in detail.
Local corrosion only occurs locally, which is a very serious and harmful damage, such as hole corrosion, intergranular corrosion, wear corrosion, stress corrosion, and so on.
2.1 Hole corrosion
Hole corrosion is a highly corrosive phenomenon, which mainly exists in the easily passivated metals, such as stainless steel. Due to the possible defects on the surface, there are active ions (such as halogens) in the solution which can destroy the passivation film. The passivation film will be destroyed locally, thus forming galvanic couple, causing hole corrosion. Due to the action of the centrifugal force, the dynamic process of galvanic couple in the hole will be accelerated, so as to ensure the continuity of hole corrosion until perforation. The centrifuge is in continuous operation under many working conditions. Once the hole corrosion is formed, it will lead to serious consequences, affect the strength of the stressed parts. For plastic materials, under the action of the centrifugal force, it will produce instantaneous tearing, and cause serious damage to the centrifuge.
2.2 Intergranular corrosion
Intergranular corrosion will cause the loss of strength and extensibility of parts, resulting in brittle fracture of parts. It is a kind of harmful damage that develops from the surface along the grain boundary to the inside, and there is no sign of corrosion on the outer surface. In daily maintenance, this kind of corrosion is difficult to be found, but when the corrosion reaches a certain degree, it changes the internal structure of the parts, leading to the serious attenuation of the physical and chemical properties of the parts, resulting in sudden burst or fracture.
2.3 Wear corrosion
Wear corrosion means that the surface of the parts suffers from both wear and corrosion. In the normal operation of the centrifuge, due to the solid particles or mechanical impurities contained in the material, the relative movement will be formed on the surface of the contact parts, resulting in wear. Due to the change of the distribution of the formed metal fiber at the wear surface, continuous fiber fracture may occur, resulting in the change of polarity and electronegativity, forming a local corrosion environment. Wear corrosion can be easily observed.
2.4 Stress corrosion
Stress corrosion is the damage caused by certain tensile stress in corrosive environment. It has the following characteristics: residual tensile stress, external tensile stress, corrosive infiltration environment, local defects. Due to the different stress distribution, there will be potential difference. Under the action of electrolyte, current will be formed and ion movement will be produced, resulting in corrosion. Stress corrosion can not be easily observed.
3. Solutions
3.1 Material properties
(1) There is no absolute anticorrosive material, so it is necessary to distinguish the application environment, such as neutral, acid or alkaline, oxidising or reductive, etc. For example, stainless steel is not suitable for concentrated sulfuric acid, but carbon steel is suitable.
(2) In the same application environment, it is necessary to choose the same material or the material with similar equilibrium potential to avoid galvanic couple. Different materials have different equilibrium potential, and the existence of potential difference will form a corrosive environment.
(3) The centrifuge is a kind of high-speed rotating equipment. Under normal working conditions, the parts of the drum will produce larger centrifugal force, so it is required that these parts have good plasticity and strength. In addition to the price, it is necessary to pay attention to the comprehensive properties of the materials, such as cold working properties and hot working properties.
3.2 Structure design
An excellent design can extend the service life of the equipment and ensure the safety of the equipment. As for the structure design, attention should be paid as follows:
(1) Avoid dead angles and ensure smooth flow of fluid. Prevent the formation of corrosive environment with poor oxygen concentration.
(2) In the same environment, use the same material and the same molding process. So as to prevent the generation of galvanic couple, avoid the formation of corrosive environment.
(3) Ensure the uniformity of the parts or increase the compressive stress. Select economic reasonable processing methods to enhance the corrosion resistance of the parts.
3.3 Surface protection measures
In the design of centrifuge, surface treatment methods are often used, such as flange, zinc plating, chromium plating, chemical coating, composite lining and so on. These measures are effective in many environments. But for the rotating parts, it is necessary to pay attention to an important phenomenon: the matrix material and the coating are two kinds of materials, and their coefficient of linear expansion is different. These structures will produce different amount of deformation in the elastic deformation of the rotating parts, resulting in a large number of microcracks and peeling of the composite surface. Therefore, the surface protection of rotating parts should be used carefully.
3.4 Corrosion inhibitor
The application of corrosion inhibitor is also widely used in practical application. For some severe environment, the parts can reach the applicable level by using appropriate corrosion inhibitor. As long as the process permits, the use of corrosion inhibitor should be an effective way.
3.5 Correct process method
Correct design and reasonable material selection are only preconditions to solve centrifuge corrosion. The correct application of processing technology also affects the anticorrosion ability of centrifuge to a certain extent. In the process of machining, many defects are usually left on the parts, such as dislocation, local stress, etc. Therefore, it is an effective way to find the right process method to prevent corrosion.