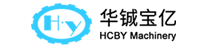
Horizontal decanter centrifuge is composed of shell, drum, conveyor, gearbox, reverse conveyor, etc. When the material is fed into the high-speed rotating drum, under the action of centrifugal force, the solid phase and liquid phase will be effectively separated.
1. The necessity of prolonging the operating time of centrifuge
Due to the high speed and vibration of the centrifuge, the centrifuge needs to be stopped for maintenance every three months, the maintenance cost is very high. If we want to ensure the safe and stable operation of the centrifuge and reduce the maintenance cost, the operating time must be extended.
2. Analysis of factors affecting the operating time of centrifuge and countermeasures
2.1 Improve the quality of oil seal and repair the defects of oil seal gripper
Due to a large amount of corrosive acid in the material, the oil seal was found to be hard and inelastic during maintenance. The surface of the oil seal gripper was pitted. In both cases, the bearing will be damaged by acid corrosion, the operating time of the centrifuge will be shortened.
Measures: change the oil seal from domestic to imported fluororubber parts to improve the acid resistance level. Conduct quality inspection and acid resistance test before warehousing. Repair the surface corrosion of the seal gripper with a highly corrosion-resistance repair agent and then finish machining with lathe.
2.2 Adjust the total displacement of rotor
The bearing temperature of the centrifuge is always in a high state (above 55℃). Through field measurement, it is found that the total displacement of rotor is only 0.25mm, too small, which is one of the causes of bearing damage.
Measures: add adjusting gaskets, adjust the total displacement of rotor to 0.6mm. After test run, the bearing temperature drops obviously.
2.3 The motor has no effective positioning
During the on-site inspection and confirmation, it was found that the positioning plate of the motor (made of cast iron) was broken. Under the action of the centrifuge force, the motor was easy to be offset, so that the motor pulley and the drum pulley were not in the same straight line, causing uneven stress on the centrifuge drum and vibration, which results in the decrease of the service life of the centrifuge.
Measures: because the original design positioning plate material is cast iron, the weldability is very pool, and it can not be rewelded. Through the field study, it is decided to add three positioning blocks to fasten the motor.
2.4 The air supply pressure of gas seal is low and unstable
In the field inspection, it is found that the inlet filter screen is blocked due to the dirty air, which causes the fluctuation of air source pressure. Thus it can not effectively prevent acid corrosion of the bearing.
Measures: select clean instrument air as air source, rearrange the pipes, add pressure reducing valves, and increase the charging pressure of air seal system. After adjustment, no acid was found in the gas seal system during the maintenance of the centrifuge, thus protecting the bearing and prolonging the operating time of the centrifuge.
3. Conclusion
After the above improvements, the centrifuge is only stopped for maintenance once a year.