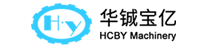
How to reduce the moisture content of Multi-Disk Screw Press?
The water content of this sludge dewatering machine is generally 80%, and the reasons for the high water content are generally as follows:
Objective reasons:
Sludge properties: The nature of the sludge is an objective reason, what type of sludge is, the organic content of the sludge, or is the sludge chemically municipal? These are all determined by the nature of the sludge itself. Different types of sludge do affect the moisture content.
Process reasons:
1. the manufacturer's manufacturing process is not up to standard: Some manufacturers in order to cut corners, the manufacturing process is not closed, to some extent affect the sludge dewatering rate.
2. the manufacturer debug flocculation is not up to standard: flocculant selection error or not accurate, resulting in poor flocculation effect, to some extent affect the moisture content after dehydration.
3. The manufacturer's machine setting is not up to standard: the sludge dewatering machine is a fully automatic product controlled by PLC electrical cabinet. When setting the machine operation, it is necessary to set the screw running parameters of the machine and adjust the gap of the back pressure plate.
How to reduce the water content in case the moisture content of the sludge is too high?
1. Reduce the organic matter content of sludge: For the objective reasons of sludge, the content of organic matter in the sludge should be checked for organic matter content and reduce organic matter, because the organic matter is too hydrophilic to the mud, resulting in low dehydration efficiency and too thick Not suitable for handling.
2. Preferred manufacturer supplier: Select the excellent sludge dewatering machine manufacturer to pass the screw shaft length and technical parameters.
3, automatic dosing device: integrated intelligent dosing device, the manufacturer configured flocculant and debug the dosage and dosing frequency.
4. set the spiral operating parameters: mainly including the speed adjustment, too fast or too slow, will lead to mud premature or too late concentrated extrusion, affecting dehydration efficiency.
5. adjust the gap of the back pressure plate: generally should not exceed 4mm, too tight or too loose will affect the dewatering efficiency, should be adjusted by the manufacturer.