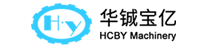
As for the problem of excessive vibration of disc separator, it may be due to improper assembly, damage of mechanical parts such as spring, bearing or transmission gear, long-term use of drum without dynamic balance, insufficient slag discharge in production or the last time the sediment in drum was not cleaned up, etc.
As for the heavy phase oil leakage of disc separator, no matter it is domestic or imported separator, if the operation is improper, the oil leakage will occur. There are many reasons for oil leakage, the direct reason is that there is no stable separation interface in the drum or the separation interface is suddenly damaged, the separation interface moves to the heavy phase surface, and a large amount of oil is discharged from the heavy phase to the centripetal pump. The oil leakage is easy to occur when the separator was fed the oil. Low hot water temperature or insufficient warm-up time, unstable physical and chemical properties of the oil, unstable oil inlet flow, low oil temperature or unstable heating, oil emulsification caused by mixing with a large number of water in the pipeline, high back pressure regulation on light phase oil pipe, all of these will cause heavy phase oil leakage of the separator. Because the proportion of the new oil is not easy to be stable, so the operation of feeding oil is very important.
Under the normal working condition of the disc separator, sometimes the separation balance will be broken due to the sudden increase of slag discharge, and the heavy phase oil leakage will occur after partial slag discharge. Increase the time of slag discharge or shorten the period of slag discharge, increase the pressure of operating water or increase the water inlet valve, increase the amount of oil input or increase the back pressure, continuously discharge the slag manually, reduce the oil temperature and water temperature, the small piston was suddenly flexible because of using hard water, these factors may cause the slag discharge and oil leakage.
When the separation effect is not good, first check whether there are external conditions: the oil is too dirty, the amount of water or alkali is not appropriate, the oil temperature or water temperature is not appropriate, the oil and alkali or water are not fully mixed, and the back pressure of light phase is too low. In addition, too much sediment in the drum caused by too long running time of the separator will also cause poor effect of the separator. In addition, when the separator worked for a long time, there will be too much sediment in the drum, it caused the low efficiency of the separator.
In regard to the electricity of the separator is too high, if the starting electricity is too high, check whether there is too much oil in the hydraulic coupling of the cross shaft. If the electricity is too high under the condition of non slag discharge during operation, it will be accompanied by drum leakage or friction of parts in the machine (such as centripetal pump part), at this time, the oil inlet shall be stopped. In case of drum leakage, stop the machine for inspection.
In the actual production, the factors that affect the stable operation of the separator are mostly external. It is often said that most of the problems of the disc separator are not the faults of its own mechanical parts. As a machine that passively performs separation operation, the installation, assembly and normal idling of the separator are only the premise of separation work. To maintain the stability of separation work, it is more necessary to adjust external factors, create conditions that are easy for the separator to work, and ensure that the quality of peripheral oil, water quality, oil quantity, oil temperature, water temperature, operating water pressure, reaction and mixing effect and other factors to meet the process requirements.