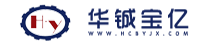
碟式分离机是一种立式离心机,转鼓装在立轴的上端,由电动机通过传动装置驱动而高速旋转,其转速一般在6000~12000r/min之间。由于碟式分离机工作转速很高,转鼓部件的质量偏心会引起分离机工作时的强烈振动,因此,转鼓部件装配后应进行动平衡校正,并在规定的部位去重。通常,第一次的去重量希望小一点,以便今后复较动平衡时有去重的地方,这就必须提高转鼓部件内各零件的加工精度。转鼓内装有进料分配器和一组层叠在一起的碟形零件----碟片,碟片上点焊有间隔片或间隔条,使组装在一起的碟片与碟片之间保持很小的间隙。需要分离的物料(悬浮液或乳浊液)通过位于转鼓中心的进料管加入转鼓,经进料分配器上的分配管均匀地分布到各碟片中间。当悬浮液(或乳浊液)在碟片之间的间隙中高速旋转时,因密度不同被分离为重相和轻相,重相在离心力作用下向碟片大端滑移,脱离碟片,积聚在转鼓内壁直径大的部位,形成沉渣(或液层)。轻相则向碟片小端滑移,经出液口排出转鼓。碟片的作用是缩短固体颗粒(或液滴)的沉降距离,扩大转鼓的沉降面积,提高分离机的生产能力。
1 碟片的加工工艺分析
由上述可见,碟片作为转鼓部件内数量较多的零件(一般为80~150片左右),它的加工精度直接影响到转鼓的动平衡和分离机的使用性能,因此各分离机生产厂家都十分重视碟片的加工工艺。
碟式分离机内的碟片呈锥形,大端或小端有凸缘,凸缘上开有装配时定位用的键槽。锥面中性层处开有供物料通行的进液孔,不同用途的分离机进液孔的数目各不相同,国产碟片式分离机的孔数一般为3~8个。为了保证装配后两碟片间有供分离物料通行的间隙,碟片的锥面焊有间隔片或间隔条。由于碟式分离大多用于食品、医药和化工行业,因此,碟片大多用奥氏体不锈钢制作,常用的材料有1Cr18Ni9、0Cr18Ni9等,材料的厚度一般为0.5~2mm。根据碟片的结构形状及设计要求,碟片加工时常用到的工序有强力旋压、冲裁、点焊、抛光等。
由于碟片是薄壁件,加工过程中非常容易变形,因此,各加工工序中变形的控制是保证碟片加工精度的关键所在。下面就强力旋压和抛光工序作一些分析。
1.1 碟片的强力旋压
强力旋压是碟片的成形工序,也是决定碟片质量的主要工序。工件旋压前应正确选取旋轮与胎模间的间隙。碟片强力旋压时,材料每点的变形对其它未变形部分的影响很小,变形后工件的凸缘尺寸基本上保持原有尺寸。
实际加工中,由于毛坯的厚度存在偏差,旋轮运动副中也存在误差,实际间隙需在理论计算值的基础上作修正,不然碟片的凸缘易起皱(俗语称为“起木耳边”)、前倾或后倒,并使碟片贴模不好----产生较大的回弹。
所采购的板材批次不同,板料厚度会有偏差,每次旋压前应对板料毛坯进行实测,取得平均数据,计算出碟片的理论壁厚,调整旋轮与胎模间的间隙时,应在理论壁厚的基础上适当减去补偿量(不同的旋压机补偿量是不一样的,需经过试模取得数据),这样才能旋压出合格的碟片。
另外,主轴的转速会影响旋压件成形表面的粗糙度,选择转速时应避开共振区。
1.2 碟片的抛光
抛光是碟片加工工艺流程中另一重要工序,碟片的表面质量主要通过抛光工序获得。碟片的加工工艺流程中一般需安排两次抛光,第一次安排在点焊之前,对碟片的内外锥面作一次整体的抛光;第二次安排在点焊之后,可抛出间隔片或间隔条的表面,顺带去除点焊时可能产生的毛刺。
目前不锈钢零件常用的抛光方法有机械抛光、电解抛光、电化学抛光等,每种抛光方法各有优缺点。碟片抛光用的较多的是机械抛光法,有些分离机生产厂家直接采用手工机械抛光,具体操作方法:工人手持工件,纤维或布抛光轮加上相应的抛光膏,将工件压在旋转的抛光轮上进行抛光,可达到Ra0.8μm的表面粗糙度。这种抛光法的优点是对设备要求低,操作简单,抛光速度快;缺点是劳动强度大,碟片容易产生不规则变形,影响零件的精度。如果条件允许,可制作一些简单的胎模,抛光时将碟片固定在胎模上进行,以防碟片受力变形。也可设计专用的抛光机对碟片进行抛光。
近年来也有一些分离机生产厂家尝试用电化学抛光的方法对碟片进行抛光。电化学抛光是利用金属电化学阳极溶解原理进行修磨抛光的,碟片基本上不受外力的作用,抛光过程不会产生变形,但需合理选择电解抛光液的配方、电流密度、抛光温度及抛光时间等参数。
2 结论
由此可见,强力旋压参数与抛光方法对碟片的加工质量起着决定性的作用,必须合理选择。但要加工出高质量的碟片,除了需重视上述的工序之外,还应注意各道工序中定位基准的选择,尽量统一基准,以保证进液孔及间隔点或间隔条的几何精度,使碟片组装成碟片组后能有较高的装配精度,进而保证转鼓的装配精度,减小不平衡去重量。