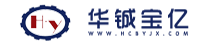
对北京卢沟桥污水处理厂卧螺离心机的常见问题及解决措施、运行成本进行了总结和分析,发现利用平、谷电价时段的间歇运行,相对于连续运行模式可大幅节约运行成本。
一、卧螺离心机的技术参数
卢沟桥污水处理厂的污泥经离心脱水后外运进行堆肥处置,采用的卧螺离心机的主要技术参数如下:
转鼓直径:575mm;转鼓长度:2440mm;转速:2900r/min;转鼓工作转速:2600r/min;转鼓与螺旋差:0~17r/min;离心力:2740g;水力负荷:75m³/h;进泥浓度:12kg·m³;固体负荷:500kg·h;转鼓电机功率:75kW。
二、常见问题及解决措施
2.1 开机报警或振动报警
离心机开启时低差速报警引起主电机停机或者离心机开启时振动较大、声音异常,造成报警停机。上述两种情况均为上次停机前冲洗不彻底所致,即冲洗不彻底会导致两种情况发生:一是离心机出泥端积泥多导致再次开启时转鼓和螺旋输送器之间的速差过低而报警;二是转鼓的内壁上存在不规则的残留固体导致转鼓转动不平衡而产生振动报警。
在上述两种情况下停机后,按复位键直至转速上升至300r/min以上松开,待转速升至600r/min时开始小水量冲洗。如果低速冲洗无效则打开机盖,用自来水管伸进转鼓内进行人工冲洗,直至冲洗干净。
停机前有效的冲洗方法:先在工作转速下高速冲洗,目的是洗出停止进料后还留在转鼓内的大量固体,冲洗水流量为120%的工作流量;滤液相对清澈后,调转速至1000~1200r/min继续冲洗至滤液清澈,然后降至600r/min左右低速冲洗,目的是将紧贴在转鼓内壁和螺旋输送器上的固体清洗下来,冲洗水流量为30%的工作流量;反复2~3次即可。当离心机转鼓转速降到300r/min时,则停止用水冲洗。刚开始冲洗时,不要马上关闭刀闸阀,等刀闸阀漏水时再关闭,这样冲洗就比较干净。需要特别注意的是,冲洗水的流量必须随着转速的下降而减少,同时把两侧的水管都打开,以避免液体从进料管处的间隙处溢出,造成冲洗水导流管被堵塞,甚至把离心机的轴淹没。
正常停机冲洗时,判断冲洗是否达到预期效果主要参考扭矩值,如果扭矩值<1kN·m,则说明冲洗得比较干净。非正常情况下检查冲洗是否达到预期效果,可以使中心齿轮轴保持不动,用手转动转鼓,看其是否转动灵活。如果转动不灵活,使转鼓在转速>300r/min下旋转并且用水彻底冲洗干净。该工作需要在停车后立即进行,因为在未启动的机器中清除潮湿和松软的沉淀物比较容易。
2.2 轴温过高报警
检查发现,主要是由于润滑脂油管堵塞导致润滑不充分、轴温过高。在卢沟桥污水处理厂运行初期,严格按照厂家提供的维护保养手册进行主轴承的润滑。但是由于离心机的润滑脂投加装置为半自动装置,相对人工投加系统油管细长,间隔周期长,投加1次润滑脂容易发生油管堵塞的现象。一旦发生,需要人工及时清理。经与厂家沟通,厂家建议采用3倍于手动润滑的用脂量,即每4h加脂5min,每个油嘴的加油速度约6g/h。其主要原理是较频繁地加油以保证细长油管的有效畅通。
当然,润滑脂亦不能加注过多,否则亦会引起轴承温度升高。
2.3 溶、配药系统漏斗处堵塞
聚丙烯酰胺的水溶液呈胶粘状态,并且其溶解性较差,加上溶药系统的稀释水流量不够,因而压力不够,很容易造成PAM锥形溶药漏斗堵塞。运行中将设计为1用1备的两台增压泵并联、同时工作,发现絮凝剂堵塞漏斗的现象明显降低。为确保运行的稳定可靠,将增压泵由ISG25-125管道泵改造为ISG40-125管道泵,压力不变(保持0.2MPa),流量由4m³/h增加到12.5m³/h,功率由0.75kW增加到1.5kW,改造后该类故障再未发生。
2.4 主机报警而停机
开启脱水机或运行过程中调节脱水机转速,主电机变频器调节过大或过快,容易造成加(减)速过电压现象,导致主电机报警。运行中发现,一般变频调节在2Hz左右比较安全。
开始启动脱水机时,在主电机没有稳定时(启动指示灯闪动)不要进泥或进水,否则亦会造成主电机报警现象。主电机转速稳定后,刀闸阀保持在关闭状况,进泥3~5min,再开启刀闸阀,期间可观察扭矩,扭矩过大时可提早一些开启刀闸阀,以免造成大量滤液进入输送机。
脱水机在冲洗状态下,尤其在高速冲洗时,也易造成加(减)速过电压现象,所以在高速冲洗时脱水机旁应有运行人员监护。
2.5 脱水机不出泥
在脱水机正常运转的情况下,相关设备正常运转,但出现不出泥现象,滤液比较浑浊,差速比较高(8.5r/min左右),扭矩也较高(达7.0kN·m左右),无异响,无振动,高速和低速冲洗时扭矩左右变化不大,亦出现过扭矩忽高忽低(0~2.8kN·m)的现象,再启动时困难,无差速。
此种情况多发生在雨季,由于来水量大,对曝气池的污泥负荷冲击大,导致剩余污泥松散、污泥颗粒小,而污泥颗粒越小,比表面积越大(呈指数规律增大),则其拥有更高的水合强度和对脱水过滤更大的阻力,污泥的絮凝效果差且不易脱水。此时,如不及时进行工艺调整,则离心机可能会出现扭矩力不从心的现象(过高),恒扭矩控制模式下差速会进行跟踪。一旦差速过大,很容易导致污泥在脱水机内停留时间短、固环层薄;另一方面,转速差越大,由于转鼓与螺旋之间的相对运动增大,对液环层的扰动程度必然增大,固环层内部分被分离出来的污泥会重新泛至液环层,并有可能随分离液流失。这种情况下有可能产生脱水机不出泥的现象。
一旦发生类似情况,则需要打开机盖,将转鼓大端上清液堰板做上记号拆下、螺栓按原位拧上(防止冲洗时进污泥或颗粒),接着盖上转鼓的外罩,进行高低速冲洗,直至出水清澈。然后打开机盖,用手从转鼓大端上清液出口伸进去确认是否冲洗干净。冲洗干净后把堰板按原位装上,盖上机盖。
在进泥浓度较低且污泥松散的情况下,采用高转速(2600r/min左右)、低差速(1.2r/min)和低进泥量(35m³/h)运行能够有效解决不出泥的问题,并且运行效果也不错。高转速是为了增加分离因数,一般来说污泥颗粒越小密度越低,需要的分离因数较高,反之需要较低的分离因数;采用低差速可以延长污泥在脱水机内停留时间,污泥絮凝效果增强的同时在转鼓内接受离心分离的时间将延长,同时由于转鼓和螺旋之间的相对运行减少,对液环层的扰动也减轻,因此固体回收率和泥饼含固率均将提高,低进泥量亦增加固体回收率和泥饼含固率。
三、运行模式
卢沟桥污水处理厂现有卧螺离心机3台(2用1备)。脱水机理论水力负荷为75m³/h,固体负荷为500kg/h。自卢沟桥污水处理厂开始运行以来,脱水机一直采用连续运行方式。为了充分利用谷、平电价的成本优势,并极大限度提高单机处理能力,卢沟桥污水处理厂对离心机连续或间断运行方式以及投运的台数进行了对比研究。连续运行即单台或2台离心机连续24h运行,间断运行就是在电价的谷、平阶段提高脱水机单台处理能力或增加脱水机运行台数,在保证生产运行需要的情况下,减少或避开电价峰段的运行时间,以降低脱水机的综合运行成本。
其他因素的对比如下:
①输送机。连续运行时输送量为3.33~3.75m³/h,间断运行时输送量为8.53~9.59m³/h(3台),5.69~6.40m³/h(2台)。输送机设计额定输送量为15m³/h(厂家提供数据),因此间断运行的输送能力完全可以保证。间断运行还可以避免输送机连续运行,减少其磨损。同时,3台脱水机同时运行也避免了1”脱水机下面的输送机干磨的问题。
②人工。连续运行需要24h有人值守,间断运行值班人员操作时间约为12h,而且多为夜班操作,白班可以节约出1名值班人员从事其他工作。
③3台脱水机间断运行,没有备用设备,如果出现设备故障可改成连续运行或2台脱水机间断运行以保证生产需要。
④冲洗水源。现在脱水机冲洗使用的是自来水,如果通过管线改造使用中水或二沉池出水,将大大节约用水成本。由于卢沟桥污水处理厂中水处理能力为500m³/d,仅能满足绿化和冲厕的需要,因此考虑使用二沉出水冲洗离心机。
如果使用自来水对脱水机进行冲洗,3台脱水机间断运行成本节约53元/d,2台脱水机间断运行成本甚至比脱水机连续运行成本约高出17元/d。改变现有运行方式的意义不大。如果经过改造、使用二沉出水对脱水机进行冲洗,2台脱水机间断运行成本节约422元/d,3台脱水机间断运行成本节约741元/d。从经济效益角度,建议采取3台脱水机间断运行的方式。如果某台离心机出现故障,可改为连续运行方式。日前,卢沟桥污水处理厂正在进行技术改造。
⑤絮凝剂溶液装置。卢沟桥污水处理厂脱水用絮凝剂溶配装置药罐容积为2m³,溶配1罐药所用时间约为1.5h。从实际运行情况看,絮凝度浓度为0.3%时每台脱水机的投药量为600~700L/h,浓度为0.4%时每台脱水机的投药量为500L/h左右。依此计算在1个溶配药周期内1套溶配药装置运行不能完全满足3台脱水机同时运行,为了保证运行效果,需要2套溶药设备同时运行。
⑥剩余污泥泵。卢沟桥污水处理厂剩余污泥泵额定流量为144m³/h,3台脱水机同时运行总的进泥量为174m³/h。因此,在3台脱水机同时运行时需要2台剩余污泥泵在程控状态下运行。
四、结语
①掌握了正确的调控理论和方法,卧螺离心机完全可以取得良好的污泥脱水效果。
②在同等条件下卧螺离心机相对于带式脱水机电耗要高。
③利用谷、平电价的成本优势间断运行卧螺离心机,相对于连续运行模式可大幅节约运行成本。