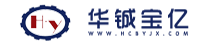
随着工业的不断发展,工业废水的排放量与日俱增。高效低耗的有机废水的处理技术成为了非常重要的研究课题。膜生物反应器(MBR)是一项将生物处理过程与膜分离过程有机结合在一起的一种水处理技术,比传统生物处理技术具有显著的优势,已经在废水处理领域发挥了重要作用。该工艺与传统工艺相比,具有出水水质好、出水可直接回用、设备占地面积小、活性污泥浓度高、剩余污泥产量低和便于自动控制等优点。但是其广泛应用存在两个主要问题:运行能耗高和膜污染,而膜污染却会导致运行能耗的增加。因此减缓膜污染成为这个领域研究的一个重点问题。
目前,MBR系统主要采用的大多数污水处理企业通过定期用水反冲洗的方式减缓膜污染,延长其化学清洗周期,提高系统的污水处理效率。尽管完全用水反冲洗操作简单方便,但是这种方法的耗水量过大,且存在水资源浪费的问题。研究表明用气反冲洗过程中产水的气泡高速浮升产水的泡振作用和气泡尾迹的混掺作用及气泡在浮升过程中出现的尾迹效应有助于提高反冲洗的效果。基于这些情况,提出新型的气水联合反冲洗和全气反冲洗的方式,以解决反冲洗耗水量过大的问题。气水联合反冲洗为先用水反冲洗一定的时间再接着用气反冲洗,全气反冲洗为完全用气代替水进行反冲洗。
1 试验装置与方法
1.1 试验装置
为了提高MBR系统的处理效果,延长膜的使用寿命,减低耗水量。本研究在已有的专利基础上,对传统的平板膜MBR进行了优化,将平板膜改为陶瓷平板膜,反冲洗系统改为水洗、气水反洗、气洗三种。
实验采用改进型MBR系统。膜池为矩形水槽,尺寸为L*W*H=700*350*700mm,其中共安置6片陶瓷平板膜,单个膜片面积均为0.25㎡,两片膜为一组,共分三组。第一组为全水反冲洗,简称为全水组;第二组为全气反冲洗,简称为全气组;第三组为气水联合反冲洗,简称为水气组。实验中所用的进/出水管和曝气管皆为硅胶透明软管,后简称为气水管。气水管包括气水总管和气水支管,总管与支管采取枝状布置。支管数量与膜组件的分组数量一致,并通过三通在膜组件的上方与其相连接。气水总管一端与上述三支支管相连,另一端通过支管分别连上空气压缩机、抽吸泵A和抽吸泵B,以实现出水和对膜片进行反冲洗。在每根支管上安装一个电磁阀,控制管路的开关,通过电磁阀的配合使用,可以使水泵和气泵单独作用于一组膜,节约设备成本。此外,在组件自带的曝气管上连接鼓风机,对污水曝气,给好氧微生物提供氧气。真空压力表置于膜组件与抽吸泵之间,以此监控跨膜压差(TMP)。
1.2 试验方法
试验用水采用药剂调节河水模拟受污染的河道水,未经处理的水质的指标为pH为7.5~8.5,COD为200~250mg/L,氨氮为4~7mg/L,总磷为2~4mg/L,浊度为4~5NTU。通过对比不同反冲洗方式下膜片的污染情况及出水水质,探究一种较佳反冲洗方式并得到其较佳运行参数。
试验中表征膜污染的指标为膜通量和跨膜压差,表征处理效果的指标为浊度和氨氮浓度。膜通量由单位时间出水量计算得到,跨膜压差由真空表读数得到,TDS用便携式TDS笔测得,浊度用便携式浊度仪测得,氨氮浓度用纳氏试剂分光光度法测得。
2 试验结果分析
本试验装置运行参数如下:MBR气水比20:1,进水pH为7.5~8.5,温度保持20~25℃,陶瓷膜单片膜面积为0.25㎡,稳态膜通量为60L/(㎡·h),改进型MBR曝气周期为12h,在该条件下运行,利用膜通量和跨膜压差的变化趋势来探究不同反冲洗方式对膜污染的改善情况。
2.1 膜污染情况研究
2.1.1 膜通量变化情况分析
反冲洗时间分别采用20s、30s和40s,反冲洗时间为20s时,全水组、水气组和全气组平均膜通量分别为50.7、51.5和48.0L/(㎡·h);反冲洗时间为30s时,全水组、水气组和全气组平均膜通量分别为60.3、58.2和56.9L/(㎡·h);反冲洗时间为40s时,全水组、水气组和全气组平均膜通量分别为55.5、54.5和51.1L/(㎡·h)。对比发现,传统反冲洗时间30s对于膜通量的稳定有较好的效果,其次是40s反冲洗时间,再者是20s反冲洗时间。
另外,不同反冲洗方式对平均膜通量的影响表现为:反冲洗时间为20s时,采用水气组优于全水组和全气组,水气组对应平均膜通量较全水组、全气组分别高1.58%、7.3%;反冲洗时间为30s和40s时,采用全水组优于水气组和全气组,其中反洗时间为30s时,全水组对应平均膜通量较水气组、全气组分别高3.6%、6.0%,其中反洗时间为40s时,全水组对应平均膜通量较水气组、全气组分别高1.8%、8.6%;全气组对应的膜通量均处于较低的状态。
反洗时间为30s时,三种反洗方式的MBR膜通量均值较高,故暂优先考虑反洗时间为30s。由于反洗时间40s时,水气组与全水组对应膜通量接近,考虑到全水组耗水量较大,且水气组平均膜通量与全水组差距较小,故反洗时间40s也纳入考虑范围。
2.1.2 跨膜压差情况分析
跨膜压差=真空表读书(取正)+(生化池液面高度-抽吸泵进水口高度)。
跨膜压差定义为驱动水透过膜所需的压力,为进水压力和过滤压力的差值。孔径较小的膜所需的跨膜压差也较大,在水温较低,通量较高以及发生污染时,跨膜压差也较高。
反冲洗时间为20s、30s和40s,全水组、水气组和全气组平均跨膜压差分别为0.0359、0.0364和0.0367MPa;反冲洗时间为30s时,全水组、水气组和全气组平均跨膜压差分别为0.0386、0.0358和0.0379MPa;反冲洗时间为40s时,全水组、水气组和全气组平均跨膜压差分别为0.0443、0.0444和0.0449MPa。
反冲洗时间为20s时,全水组跨膜压差率先在36h出现下降趋势,随后上升,于180h时同水气组和全气组同时下降,跨膜压差整体来看波动幅度大、变化不稳定,故同样不考虑此反洗时间。
反冲洗时间为30s时,三种反冲洗方式都在装置运行开始阶段就出现下降,检查管道密闭性后,压差出现回升。后期水气组跨膜压差较为稳定并于144h时回到初始压差值,全水组跨膜压差于144h回升后又在180h处下降,于216h时回到初始压差值。对比而言,水气组恢复较快,且恢复后很长一段时间内跨膜压差保持稳定。
反冲洗时间为40s时,三种反冲洗方式对应的跨膜压差整体均较稳定。全水组运行72h后较早出现下降趋势,随后于144h处回升至稳定值。水气组跨膜压差初始值偏低,但随后即稳定在0.045MPa左右,在运行144h时有小趋势下降并于216h时恢复至稳定值。全气组在108h时有小趋势的下降并于216h时恢复初始值。对比发现,此反冲洗时间装置运行过程中,水气组跨膜压差较晚出现下降趋势,同时在极短时间内恢复稳定值。
结合对膜通量变化的分析,综合考虑,反洗时间采用40s,反冲洗方式为气水联合反冲洗较为合适。
2.2 出水水质情况研究
改进型MBR运行中反冲洗时间为40s,反冲洗方式为气水联合反冲洗:传统MBR运行中反冲洗时间为30s,反冲洗方式为全水反冲洗。
本试验进水采用的是河水进行配制的实验用水,且在48h与336h处进行加试剂调整水质。上述两种反洗方式的出水水质各项指标数值几乎一致,可见本试验装置的改进对出水影响不大。其中,出水浊度稳定后数值保持在0.3~0.5NTU,两次投加试剂后氨氮的去除率分别为92.5%和62.2%,整体而言,本试验装置处理效果较为稳定。
3 装置运行能耗情况
改进型MBR设备主要的能耗为电耗和反冲洗用水,包括水泵和气泵。以下对设备的电耗和反冲洗用水量进行分析,对比该改进型MBR设备和传统MBR设备产生的能耗。
(1)改进MBR设备运行参数为膜面积0.25㎡,膜通量60L/(㎡·h),MBR气水比20:1,抽停比10min:2min,反洗周期12min,反洗时间30s。实际产水量为0.69m³/d,其吨水耗电量为1.19kW·h,日反冲洗耗水量为0.240L/d。
(2)传统MBR设备运行参数为膜面积0.25㎡,膜通量60L/(㎡·h),MBR气水比20:1,抽停比10min:2min,反洗周期12min,反洗时间30s。实际产水量为0.684m³/d,其吨水耗电量为1.20kW·h,日反冲洗耗水量为0.475L/d。
4 结论
(1)对比全水反冲洗、全气反冲洗、气水联合反冲洗三种方式,全水反冲洗的耗水量为0.475L/d,气水联合反冲洗的耗水量为0.240L/d,而全气反冲洗的耗水量尽管为0,但是其对应的膜通量较气水联合反冲洗低7%左右。气水联合反冲洗是耗水较少、处理效果良好的反冲洗方式。
(2)反冲洗时间选用20s、30s、40s三种情况,考量膜通量和跨膜压差的变化情况,当反冲洗时间为40s时,气水联合反冲洗对膜污染的缓解效果较好,成功延长了膜的使用周期。