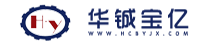
沉降式离心机是后处理工艺的关键设备,其工作原理是:依靠悬浮液中固相和液相重度的不同而实现料液分离,常用于固相比液相重度差较大而固相颗粒较小、含固量较低的悬浮液。因此,沉降式离心机较适合后处理工艺的需求。现用此离心机的主要作用是去除溶解液中的不溶残渣,为后续萃取工艺提供保障。
本次沉降式离心机负载工艺性能验证试验,其目的是:通过对沉降式离心机空载和模拟料液沉降离心分离,摸索出沉降式离心机的基本操作方法及运行参数,了解沉降式离心机的工作性能,从而验证其设计和加工制造的合理性、实用性。
1 试验体系
1.1 模拟原料的选择
试验选用氧化铝(刚玉粉磨料)作为料液的不溶悬浮固体,以硝酸锶调节液相比重和粘度构成Al2O3-Sr(NO3)2水模拟体系。
1.2 模拟料液的配制
1.2.1 所需试剂
(1)Sr(NO3)2化学纯
(2)Al2O3固体微粒,规格:4.5μm和9μm
(3)浓硝酸:分析纯或化学纯
(4)氢氧化钠:5mol/L和1mol/L
1.2.2 配制过程
向无离子水中加入Sr(NO3)2,调节料液密度后加入Al2O3微粉调节溶液的粒径,微粉浓度为300mg/L,粒度为4.5μ(95%)+9μ(5%)。每批料液需配制1000L。具体模拟料液配制参数如下表所示:
硝酸锶的加入量(kg) | 氧化铝的加入量(g) | 料液密度(g/cm³) | 料液pH值 | 料液体积(L) | |
562.5 | 4.5μ | 9μ | 1.403 | 2.35 | 950 |
211 | 14 |
配制过程:
(1)向配制槽中加入850L的无离子水,边搅拌边缓慢加入616mL的浓硝酸,调节酸度pH≈2.0。
(2)边搅拌边向配制槽中加入预先称好562.5kg的Sr(NO3)2固体(每次加入量小于5kg),直至所有固体物完全溶解,此时溶液酸度pH≈1.8。
(3)分别用5mol/L和1mol/L氢氧化钠溶液调节Sr(NO3)2溶液的酸度至pH≈2.35。
(4)将预先称好的211g 4.5μm和14g 9μm的Al2O3固体缓慢加入,搅拌至固体微粒完全分散,取样分析合格后即可作为模拟料液使用。
2 试验设备的主要技术特性
生产能力:500L/h
转鼓内径:Φ500mm
转鼓高度:500mm
轻相出口:Φ395mm
分相口内径:Φ435mm
分相口距转鼓底距离:15mm
清液中不溶物含量:≤5mg/L
清液中不溶物截留粒径:≤1.5μm
排渣转速:20rpm
分离转速:500rpm~2500rpm
电机型号:YD160L8/4/2级
电机功率:2.8/7/9kW
电机转速:3000rpm
电机电压:380V
3 试验流程
设置模拟料液配制槽,料液经取样合格后使其进入料液槽中,在0.18MPa的压空搅拌情况下模拟料液经一级空气提升(用浮子流量计控制流量)到恒液位前置罐,再由二级空气提升(通过质量流量控制器控制流量)输送至沉降式离心机转鼓内,经高速旋转分离后的清液自流入清液槽,来不及沉降分离的料液回流入料液槽。冲渣时用螺杆泵将无离子水升压至1.4MPa后进入离心机转鼓内进行高压冲洗。为便于模拟料液的循环使用,高压冲渣时将渣水排至废液槽,并将清液槽内的模拟料液通过空气提升(用浮子流量计控制流量)输送至有人孔的调料槽(0139V),用不锈钢潜水泵分别将废液接收槽和调料槽内的料液输送至模拟料液配制槽中进行再利用。
模拟料液循环使用流程:模拟料液配制合格后→料液槽→恒液位前置罐→沉降式离心机→清液槽→废液槽→潜水泵→模拟料液配制槽→进行分析和调料(补充Al2O3微粉)。
4 试验方法
4.1 空载验证试验
启动离心机,依次调整转速为:20rpm、1200rpm、2000rpm、2500rpm,各转速状态下至少运行5分钟,正常后再依次下调直至停车。
4.2 水负载验证试验
用无离子水作为物料介质,先将沉降式离心机升速至500rpm运行5分钟,无异常后升速至1200rpm运行5分钟,无异常后通知量槽间和主控室在保证料液槽一级空气提升至恒液位前置罐液位达到满溢流状态下,按沉降式离心机生产能力500L/h的上料流量,开启二级空气提升。待离心机清液口开始出水且上料运行正常的前提下,升速至2000rpm,进行高速沉降分离,当一批料被处理完毕后降速至1200rpm,待清液口不再出水、料液槽不再有回流、离心机运行平稳后降速至500rpm,此时认真观察并记录离心机过临界转速时的振幅及运转状况,待清液口不再出水、料液槽不再有回流后降速至20rpm,直至停车。
由于水负载验证试验的工作介质为无离子水,而无离子水中不含有大量颗粒物,因此在进行此项验证试验时只为验证离心机在相应转速下的承载能力,不进行取样。基于对离心机模拟料液排渣时的安全性考虑,水负载验证试验过程中进行冲渣,在离心机20rpm下用高压水冲洗10分钟,验证离心机冲渣时的运行稳定性。
4.3 模拟料液负载验证试验
该项试验与水负载试验程序基本相同,首先开启沉降式离心机至500rpm运行5分钟,若无异常后升速至1200rpm再运行5分钟,若无异常后升速至1200rpm再运行5分钟,若仍无异常后再按照二级上料流量试验条件(流量:300L/h、500L/h)开始上料。待离心机清液口开始出料,且上料运转正常、取样完毕的前提下,升速至分离转速2500rpm,每隔30分钟取样一次,待一批料处理完毕后同水负载验证试验降速程序,依次降速直至停车。
5 结果与讨论
5.1 空载验证试验
离心机的整个空载验证试验过程中运行稳定,无明显振动及机械碰撞声。
空载验证试验参数如下表所示:
试验内容 | 规定值 | 试验值 | 备注 | |
速度(rpm) | 0~2500 | 0~2500 | 20rpm、1200rpm、2000rpm、2500rpm | |
加速度(g) | - | 0.19 | ||
振幅 (μm) | 升速 | - | 8.9 | 升速至1200rpm过程中 |
降速 | - | 10.4 | 10.4 | |
轴承温升(℃) | 数显仪 | ≤80 | 74 | 通入A3压空进行冷却后高达49.5℃ |
电流(A) | 启动 | - | 9.9 | 额定电流:15.1A~18.8A |
升速 | - | 10.4 | 升速至2500rpm过程中 | |
降速 | - | 54.2 | 1200rpm降速直至停车过程中 | |
噪声(分贝) | ≤85 | 70 | 无明显振动和机械碰撞声 | |
电机功率(kW) | 2.8、7.0、9.0 | 未测量 | 电机运行正常 |
轴承温升高达84℃,通入A3压空进行强行冷却后高达49.5℃,整个过程电机、上轴承、下轴承等离心机各运转部件均运行正常;1200rpm降速直至停车过程中,电流达到54.2A,但离心机就地控制盘柜中未发生异常现象。由此证明:离心机在20rpm、1200rpm、2000rpm、2500rpm空载工况下运行正常。
5.2 水负载验证试验
水负载验证试验过程中离心机运行稳定,无明显振动及机械碰撞声。
水负载验证试验参数如下表所示:
试验内容 | 规定值 | 试验值 | 备注 | |
生产能力(L/h) | 100~500 | 200 | 恒液位前置罐液位:320mm~380mm | |
速度(rpm) | 0~2500 | 0~2000 | 0~2000 | |
加速度(g) | - | 0.19 | 0.19 | |
振幅 (μm) | 上料 | - | 82.9 | 1200rpm上料4分钟后 |
升速 | - | 23.6 | 升速至2000rpm(上料后) | |
降速 | - | 64.8 | 离心机各零部件运行正常,无机械碰撞声 | |
轴承温升(℃) | 数显仪 | ≤60 | 69.85 | 运行1小时后 |
激光测温仪 | ≤60 | 64 | 降速至1200rpm过程中 | |
电流(A) | 启动 | - | 9.8 | 额定电流:15.1A~18.8A |
升速 | - | 13.2 | 升速至1200rpm | |
降速 | - | 53.3 | 离心机就地控制盘柜内未发生异常现象 | |
冲渣体积(L) | ≤200 | 150 | 冲洗10分钟,水压0.5MPa | |
电机功率(kW) | 2.8、7.0、9.0 | 未测量 | 电机运行正常 |
5.3 模拟料液负载验证试验
5.3.1 二级上料流量:500L/h
离心机在1200rpm以500L/h的流量开始上料后,振幅达到263.1μm。离心机降速至500rpm过程中,振幅达到413.2μm,且振动强烈,由此证明生产能力完全可达到300L/h。
5.3.2 二级上料流量:300L/h
5.3.2.1 转速与振幅的对应关系
离心机在2000rpm以300L/h的流量开始上料后,振幅达到63.1μm。离心机降速至500rpm过程中,振幅达到409μm,未发生明显振动,由此证明本离心机在二级上料流量为300L/h的工况下运行正常。
5.3.2.2 轴承温升、电流分别与试验时间的关系
在通入A3压空进行强行冷却后,轴承温升高达68.58℃,整个过程电机、上轴承、下轴承等离心机各运转部件均运行正常;1200rpm降速直至停车过程中,电流达到58.3A,但离心机就地控制盘柜内未发生异常现象。
5.3.2.3 转速对清液中含固量及不溶物截留粒径的影响
自2500rpm降速至1200rpm过程中,清液中含固量逐渐增多至1250mg/L左右,对分离越不利;在分离转速2500rpm状态下分离时间越长,清液中不溶物截留粒径越大,对分离越有利。
5.3.2.4 二级上料流量对清液中含固量及不溶物截留粒径的影响
在二级上料流量为200L/h~350L/h的状态下,清液中含固量保持在0~10mg/L,当二级上料流量为400L/h时,清液中含固量1300mg/L左右;在二级上料流量为200L/h~500L/h的状态下清液中不溶物截留粒径基本保持不变。由此证明:二级上料流量应考虑200L/h~350L/h,若再考虑一批料液的处理时间问题,应选取二级上料流量为350L/h。
5.3.2.5 二级上料流量、转速分别对分离效率的影响
在分离转速为2500rpm、二级上料流量为200L/h~400L/h的状态下,离心机的分离效率基本可保持在较高水平99.85%左右。
5.3.3 模拟料液负载验证试验参数
试验内容 | 规定值 | 试验值 | 备注 | |
生产能力(L/h) | 100~500 | 300 | 恒液位前置罐液位:380mm~450mm | |
速度(rpm) | 0~2500 | 0~2500 | 0~2500 | |
加速度(g) | - | 0.19 | ||
振幅 (μm) | 上料 | - | 63.1 | 2000rpm上料5分钟后 |
升速 | - | 10.9 | 升速至2500rpm(上料后) | |
降速 | - | 40.9 | 离心机各零部件运行正常,无变形现象 | |
轴承温升(℃) | 数显仪 | ≤80 | 68.15 | 运行3小时后 |
激光测温仪 | ≤80 | 66 | 降速至2000rpm过程中 | |
电流(A) | 启动 | - | 9.8 | 额定电流:15.1A~18.8A |
升速 | - | 17.2 | 升速至1200rpm | |
降速 | - | 58.3 | 离心机就地控制盘柜内未发生异常现象 | |
噪声(分贝) | ≤85 | 75~80 | 环境噪音 | |
清液不溶物含量(mg/L) | - | 10.75 | 若加上降速后清液中的含固量则为:10.78 | |
不溶物粒径(mg) | - | 9.11 | 若加上降速后清液粒径则为:42.2 | |
电机功率(kW) | 2.8、7.0、9.0 | 未测量 | 电机运行正常 | |
分离效率(%) | - | 96.26 | 若加上降速后清液口出液则为:96.20 |
离心机在1200rpm以300L/h的流量开始上料后,振幅达到63.1μm,降速至500rpm过程中,振幅达到409μm,未发生明显振动,由此证明本离心机在二级上料流量为300L/h的工况下运行正常、稳定。
6 结论
对沉降式离心机进行空载、水负载、模拟料液负载工艺性能验证,其结果表明:
(1)生产能力可达到300L/h。
(2)在高速分离时,离心机下轴通入A3轴封压空状态下,轴承温度高达68.15℃。
(3)降速至500rpm过程中,振幅达到409μm,表明本离心机在二级上料流量为300L/h的工况下运行正常、稳定。
(4)在Al2O3-Sr(NO3)2水模拟体系下,离心机对清液中不溶物截留粒径和含固量满足工艺设计要求,分离效率达到96%以上。