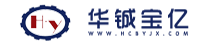
1 离心机简介
某公司SAN珠料生产过程中采用一种型号CHP5000MA卧式螺旋卸料沉降式离心机(以下简称离心机),自1992年投入使用,用于SAN珠料的脱水干燥。
1.1 离心机的基本参数
转鼓转速2450r/min;分离因数Fr=3122;长径比λ=3;转鼓半锥角α=10°;差转速△n=44r/min(转鼓超前);转鼓内径D=620mm;转鼓长度L=1860mm(有效长度);单头、右旋螺旋叶片。
1.2 离心机基本结构
离心机由进料管、液力耦合器、三角皮带轮、左右轴承、螺旋输送器、转鼓、行星差速器、溢流挡板、机壳、扭矩机械保护装置等部件组成。差速器是离心机上不可缺少的、精密、复杂核心部件,作用是在螺旋与转鼓之间形成一个较小的转速差。差速器的可靠性直接影响离心机整机的工作能力和可靠性。该机采用渐开线行星齿轮差速器。
变速装置为动轴线轮系(也称周转轮系),双级2K-H型传动,转鼓与变速箱内齿b1相连,二者同步转动,一级行星轮架H1上装有2个相同的行星轮c1,它同时与中心轮a1、内齿轮b1啮合,行星轮c1既有自转又有公转,其公转数就是二级行星传动中的中心轮a2的转数;第二级行星轮c2与中心轮a2、内齿轮b2啮合,第二级行星轮架H2带动螺旋输送器,这样螺旋与转鼓产生相对运动。
2 故障描述与原因分析
该离心机近年来故障频发,平均1~3个月就要进行一次较大检修,严重影响装置长周期运行。通过多次对该离心机解体检修发现,设备损坏主要集中在一级行星齿轮、二级行星齿轮、行星齿轮滑动轴承等处。
2.1 行星齿轮失效分析
行星齿轮为高速旋转件,承受齿轮啮合力和径向推力。观察行星轮断口截面,发现其由旧裂纹发展而来。在各行星轮上,均发现有较多的微小裂纹,应为长时间运转过程中,不断承受交变应力导致行星轮疲劳破坏。
2.2 行星轮滑动轴承失效原因分析
解体差速器发现,滑动轴承表面有较多腐蚀坑和径向沟槽,有大量径向微小裂纹,但强度明显不足,甚至拆除后发生断裂损坏。分析原因有4个。
(1)滑动轴承为高速旋转件,承受摩擦力和径向离心力。差速器润滑为密闭系统,运行中存在一定的温度,同时在脉冲载荷、摩擦力、径向离心力等的作用下,滑动轴承表面受冲刷、气蚀影响,产生腐蚀坑和微小裂纹。
(2)当滑动轴承表面径向裂纹形成后,破坏了润滑油油膜的形成,降低了润滑效果,造成滑动轴承受力集中,局部应力增大,导致腐蚀坑和微小裂纹进一步发展,轴承损坏。
(3)滑动轴承油孔堵塞、油不清洁、装配有毛刺、使用的工具抹布不干净等也可能造成滑动轴承损坏。
(4)行星轮滑动轴承与轴之间的润滑油,受到离心力的作用,如果离开摩擦区将造成润滑不良,也可能造成滑动轴承损坏,因此泄油不能太快,否则油会通过端面流失,造成润滑油不足。径向间隙过大,也会加快润滑油的流失。
3 处理措施
3.1 行星齿轮改造
3.1.1 内齿圈的设计加工
为了尽可能减少行星轮与内齿轮之间的冲击,在不产生内啮合齿轮干涉的前提下,应尽量减少齿轮间隙,有效控制温升和噪声,提高齿轮寿命。为了提高齿圈的强度和耐磨性,选取35CrMo优质合金钢先做调质处理,硬度达到285HV,然后做氮化处理,硬度提高到700HV,热处理后进行磨削加工,制造前后对原材料多次探伤检查,确保齿轮质量。
3.1.2 行星齿轮选材
行星齿轮选20CrMnTi渗碳淬火,太阳轮圆柱齿轮38CrMoAl调质氮化,这样处理可以达到提高表面硬度增加耐磨性、提高心部强度的目的。
3.1.3 行星齿轮加工精度控制
如果齿轮精度低,在滑动轴承和轴间产生的交变应力将造成滑动轴承快速磨损,使机构失效。所以行星齿轮的精度应严格控制在3~4级,每组行星齿轮的公法线误差<0.01mm,重量差<0.8g。
3.1.4 行星齿轮平衡精度控制
对一、二级行星齿轮零部件分别做平衡处理,平衡精度G2.5级,整机平衡精度G2.5级。
3.2 行星轮滑动轴承的校核
滑动轴承失效的主要原因是磨损和咬焊,因此防止其失效的关键在于轴颈和轴瓦间能否形成油膜,并保证在运行中油膜不发生破裂。滑动轴承的设计主要是在轴承直径d和长度l确定以后进行工作能力的计算,即满足3个条件:
(1)p≤[p]
(2)v≤[v]
(3)pv≤[pv]
对于不同材料制造成的滑动轴承,以上3个许用条件不同,但至少应满足2个条件:
①许用比压一般取[p]=3M~4.5MPa
②比压与轴承线速度之积pv≤100M~150Mpa·m/s
3.2.1 行星轮离心力计算
(1)一级行星轮。行星轮质量G1=3.5kg,中心距a1=120mm,转速n1=2111r/min,一级行星轮离心力可用下式计算:
Fc1=G1×a1×(π×n1/30)2=3.5×0.12×(π×2111/30)2=20504N
(2)二级行星轮。行星轮质量G2=8.45kg,中心距a2=125mm,转速n2=2406r/min,二级行星轮离心力可用下式计算:
Fc2=G2×a2×(π×n2/30)2=8.45×0.125×(π×2406/30)2=65985N
3.2.1.2 一级传动行星轮滑动轴承参数计算
一级行星齿轮滑动轴承参数如下:直径d1=123mm,长度l1=54mm;一级行星齿轮对滑动轴承径向压力:Fa1=Fc1=20504N;一级行星轮相对于齿轮架转速:因为nH1=2111r/min,na1=0r/min,所以△nH1=2111r/min。
一级行星轮滑动轴承比p1=Fa1/(d1×l1)=20504/(123×54)=3.1MPa
一级行星轮滑动轴承轴承线速度v1=πd1△nH1/(60×103)=π×123×2111/(60×103)=13.59m/s
一级行星轮滑动轴承pv值为:p1×v1=3.1×13.59=42.13MPa·m/s
同前文叙述比较,p,pv值均满足许用条件。
3.2.1.3 二级传动行星轮滑动轴承参数计算
二级行星齿轮滑动轴承参数如下:直径d2=111mm,长度l2=107mm;一级行星齿轮对滑动轴承径向压力:Fa2=Fc2=65985N;二级行星轮相对于齿轮架转速:因为nH2=2406r/min,na2=2111r/min,所以△nH2=295r/min。
二级行星轮滑动轴承比p2=Fa2/(d2×l2)=65985/(111×107)=5.56MPa
二级行星轮滑动轴承轴承线速度v2=πd2△nH2/(60×103)=π×111×295/(60×103)=1.71m/s
二级行星轮滑动轴承pv值为:p2×v2=5.56×1.71=9.51MPa·m/s
同前述比较,p2值比许用值偏高,而线速度较低,二级传动行星轮滑动轴承是重载低速,因此在选择轴承材料时要考虑更大承受载荷材料。
3.2.2 行星轮滑动轴承材料的选择
分析进口滑动轴承材料,其中Cu为87.16%,Sn为5.68%,Zn<0.2%,Pb为6.32%,接近于锡青铜。
因为国内无完全一样的材料,因此在本次改造过程中,滑动轴承采用新型轴承DU轴承(国内一般称之为聚四氟乙烯复合轴承),DU轴承耐重载低速,在0.005m/s时,压力35M~56MPa,摩擦因数0.01~0.09,温度可达280℃。DU以钢为瓦背,中间为多孔性青铜(Cu89%,Sn11%)、浸渍聚四氟乙烯(PTFE)和Pb(20%)的混合物,厚约25um。也可以在滑动轴承表面电镀厚2~5um巴氏合金,承载能力为42M~52MPa。
在滑动轴承加工制造过程中,经过精加工的DU滑动轴承表面使用专用的模具进行研磨,磨料采用W5,研磨后滑动轴承表面粗糙度Ra<0.4um。由于差速器运行过程中温度较高,产生较大热膨胀,行星轮轴、销轴与滑动轴承采用间隙配合,间隙0.08mm;滑动轴承外表面的键槽顶部与行星轮内孔键槽底部间隙0.04mm;滑动轴承内孔的圆度、圆柱度<0.02mm;滑动轴承内孔对行星轮的同轴度<0.02mm;滑动轴承与轮架的轴向间隙0.1~0.14mm。差速器组装到位后,整机径向跳动≤0.05mm。
4 结论
经过对差速器行星轮及滑动轴承的改进,以及对工艺操作的优化,大大改善了差速器的运行状态。改造完成连续运行3个月后,对离心机差速器运行状态进行检测,差速器温度64℃,温升<40℃,均在规定范围内。连续运行1a,未发生因差速器引起的设备故障。因此,本次改造提高了差速器的运行周期,离心机整机运行稳定,符合企业长周期生产要求。