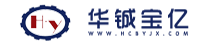
卧式螺旋沉降离心机简称为卧螺离心机,它是一种高效的离心分离设备。卧螺离心机一般可分为卧式螺旋过滤离心机和卧式螺旋沉降离心机。卧螺离心机是一种卧式螺旋卸料、连续操作的沉降设备。
卧螺离心机在环保应用方面主要指对工业和民用污水处理过程中产生的污泥进行脱水。当今环境问题成为全世界共同关注的焦点,在此背景下,卧螺离心机的价值得到体现。以前污水处理厂大多以自沉降或采用带式压滤机进行污泥的脱水浓缩,试验证明,污泥含水率从98%降到80%,其体积可以缩小10倍。正因如此,卧螺沉降离心机由于其先天具有处理量大、自动化操作、脱水效果好等特点,在环保领域得到了广泛的使用和推广。卧螺离心机单品销售额占到了所有离心机产品的一半左右,奠定了其不可替代的地位。在国外,污水处理设备首选卧螺离心机。
虽然不同生产厂家的不同规格或型号的卧螺离心机具有不同的设备结构、设备材质、规格和运行调整机构等,但其基本设备原理是相似的,现以宁波市城市排水有限公司南区污水处理厂使用的德国福乐伟机型为例对其进行简单介绍,并就实践中的一些运行技术进行浅泛的探讨,建立脱水机运行管理的基本原则,以便于各位同行更好的指导生产运行。
1 卧螺离心机介绍
1.1 基本结构及脱水原理
卧螺离心机主要由转鼓、螺旋、差速系统、液位挡板、驱动系统及控制系统等组成。
卧螺离心机是利用固液两相的密度差,在离心力的作用下,加快固相颗粒的沉降速度来实现固液分离的。具体分离过程为污泥和絮凝剂药液经入口管道被送入转鼓内混合腔,在此进行混合絮凝(若为污泥泵前加药或泵后管道加药,则已提前完成絮凝反应),由于转子(螺旋和转鼓)的高速旋转和摩擦阻力,污泥在转子内部被加速并形成一个圆柱液环层(液环区),在离心力的作用下,比重较大固体颗粒沉降到转鼓内壁形成泥层(固环层),再利用螺旋和转鼓的相对速度差把固相推向转鼓锥端,推出液面之后(岸区或称干燥区),泥渣得以脱水干燥,推向排渣口排出,上清液从转鼓大端排出,实现固液分离。
1.2 影响卧螺离心机使用效果的因素
1.2.1 不可调节的机械因素
(1)转鼓直径和有效长度。转鼓直径越大,有效长度越长,其有效沉降面积越大,处理能力也越大,物料在转鼓内的停留时间也越长,在相同的转速下,其分离因数就越大,分离效果越好。但受到材料的限制,通常转鼓直径介于200~1000mm,长径比介于3~4。
(2)转鼓半锥角。转鼓半锥角是离心机设计中较为重要的参数。从澄清效果来讲,要求锥角尽可能大一些,而从输渣和脱水效果来讲,要求锥角尽可能小些。对于难分离的物料(如活性污泥)半锥角一般在6度以内,以便降低沉渣的回流速度。
(3)螺距。螺距即相邻两螺旋叶片的间距,是一项很重要的结构参数,直接影响输渣的成败。对于难分离物料如活性污泥,输渣较困难,螺距应小些,一般是转鼓直径的1/5~1/6,以利于输送。
(4)螺旋类型。螺旋是卧螺离心机的主要构件,它的作用是输送沉降在转鼓内侧的沉渣和顺利排掉沉渣,它不仅是卸料装置,也决定了生产能力、使用寿命和分离效果。
1.2.2 可调节的机械因素
(1)转鼓转速。转鼓转速的调节通常通过变频电机或液压马达来实现。转速越大,离心力越大,有助于提高泥饼含固率。但转速过大会使污泥絮凝体被破坏,反而降低脱水效果。同时较高转速对材料的要求高,对机器的磨损增大,动力消耗、振动及噪声水平也会相应增加。
(2)差速度(差数比)。差速度直接影响排渣能力、泥饼干度和滤液质量,是卧螺离心机运行中重要的需要根据运行情况进行调节的参数之一。应根据物料性质、处理量大小、处理要求及离心机结构参数来确定差速度大小。就是说,在现场要根据情况寻找到较佳的处理量、处理效果需求的差速值范围,以实现满足泥饼干度的情况下尽可能高的处理能力。同时,在一定范围内,差速度的控制和絮凝剂投加量的控制互为补充,在要求达到一定泥饼干度情况下,当差速度降低时,可同时节省絮凝剂投加量。对于具有差速度自动调节功能的离心机,差速度的参数设定要结合长期的使用情况确定,并根据可能发生的各种变化随时修正。
(3)液环层厚度。液环层厚度是设备优化的一个重要参数,直接影响离心机的有效沉降溶剂和干燥区(岸区)长度,进而影响污泥脱水的处理效果。液环层厚度增加,会使沉降面积增大,物料在机内停留时间也会相应增加,滤液质量提高,但同时机内的干燥区(岸区)长度缩短,导致泥饼干度降低。相反,调低液环层厚度可获得较高的泥饼含固率,但要以牺牲滤液质量为代价。因此应合理地调节液位挡板的高低使泥饼干度与滤液质量达到较佳组合。
1.2.3 工艺因素
由于离心机是利用固液两相的密度差来实现固液分离的,因此污泥颗粒比重越大越易于分离。不同污水水质产生的污泥和采用不同水处理工艺得到的污泥会有较大的差异,因此在污泥脱水中会有不同的表现。为改善污泥脱水性能,进行机械脱水前一般应均匀加入适量的有机高分子絮凝剂,如聚丙烯酰胺(PAM),来降低污泥的比阻,使污泥固相和液相分离后更易于脱水。絮凝剂的种类必须与污泥特性、设备类型和运行工况相适应。在一般情况下,能够适合设备的污泥浓度有一定的范围要求,污泥浓度过低或过高均会消耗更多的絮凝剂。在设备正常运转的污泥浓度情况下,絮凝剂的用量和待处理污泥的固含量近似成正比例关系,所以,在一定污泥流量的情况下,絮凝剂的投加量要根据污泥的浓度进行调整。很多时候,由于污泥浓度发生变化,但絮凝剂投加量没有及时调整而使现场运行表现不佳或产生药耗增加。另外,若絮凝剂溶解状况不好导致实际用量不足或絮凝剂配制浓度过低使药液有效成分供应不足,则难以形成相应干度的泥饼,影响上清液质量,而絮凝剂浓度太大,絮凝剂高分子链上的活性基团则会由于相互屏蔽、包裹而使有效成分难以充分发挥功效,从而造成药剂的浪费,由于絮凝剂投加量较多,絮凝体的再分散作用也会破坏絮体稳定性,絮凝效果同样不好。
影响卧螺离心机脱水效果的因素很多,并且各个因素又相互影响,因此处理效果是以上所述各个因素综合作用的结果。离心机的选型应结合工程项目的实际情况进行,运行参数的调整应从脱水后泥饼处置方法所要求较佳泥饼含水率、固体回收率和经济性等因素综合考虑。
2 调试和运行技术分析
污泥脱水的调试工作是按照现有条件,寻找到污泥、设备和絮凝剂三者之间较佳的运行组合参数,三者之间单纯依赖于某一方面或忽视其他方面都会使运行出现问题。
2.1 絮凝剂调整
在污水处理厂工艺、设备调试时,由于受到水质、水量、水处理工艺运行状态等因素的影响,待处理污泥的性质可能会发生很多变化,这种变化对污泥脱水机和絮凝剂的依赖性会产生波动。污泥龄或污泥存放时间会影响到污泥性质,如污泥浓度、污泥有机质含量(或灰分含量)、污泥密度、污泥有机质含量(或灰分含量)、污泥密度、污泥颗粒规格(污泥自身骨架结构状况)等对絮凝剂和脱水机的依赖波动会更加明显,因此在现场要根据情况及时调整来保证能够正常进行污泥脱水。
产生这种变化的主要原因是:
(1)由于污水厂进水负荷变化,导致沉淀池(初沉池或二沉池)停留时间发生变化,沉淀池中的悬浮物实际沉淀时间发生变化,导致污泥密度和浓度发生变化。
(2)由于沉淀池向污泥脱水车间排放的待处理污泥流量或排泥周期发生了变化,导致实际污泥浓度发生变化。
(3)由于现场运行的异常情况(如维修等)导致污泥发生变化,或由于季节性原因,特别是气候交替导致污泥性质和浓度发生变化等。
2.2 卧螺离心机设备处理能力的控制
任何卧螺离心机都有一个处理能力要求,可从以下两方面进行参考:
(1)可处理干固体负荷,即每小时处理的不挥发固体重量,以kgDS(干固体)/h表示。
(2)可处理水力负荷,即进入设备的污泥流量,以m³/h表示,它与进泥浓度(固含量)的乘积即为干固体负荷。
在正常污泥浓度情况下,应保证处理干固体负荷在设备厂商标定的设备理论负荷的70%~90%为好,要避免设备利用率过低,同时避免设备长期在高负荷下运转而造成设备损耗加快,维护周期缩短。
2.3 分离因数的调整
分离因数表示离心力场的强弱,它通过调整离心机的转速来控制。提高分离因数,可使生产能力和分离效果提高,但也增大了功率消耗及转鼓和螺旋的磨损,应在较低的分离因数下满足生产能力和分离要求,可参考设备说明和实际运行状况来确定,离心机转速的控制要以实现设备正常稳定运转和正常污泥脱水处理效果为基准。因离心脱水是以离心力强化脱水效率,虽然分离因数大,脱水效果好,但并不成比例,达到临界值后分离因数再大,脱水效果也无多大提高,而动力消耗几乎成比例增加,运行费用大幅度提高,机械磨损,噪声也随之增大。而且随着转速的增加,对污泥絮体的剪切力也增大,大的絮体易被剪碎而破坏,影响污泥干物质的回收率。
2.4 扭矩(差速度)的调整
扭矩(差速度)大小决定了处理能力和泥饼干度。提高差速度,排渣迅速,处理能力增加,但出渣含水率高,回收率低;降低差转速,泥饼干度增加,表现出螺旋扭矩大,处理能力降低。所以在满足处理能力和处理效果这一对矛盾中,要找到处理能力和处理效果这一对矛盾中,要找到极佳扭矩(差速度)值,可以根据实际情况进行上下调整,结合污泥流量和泥饼干度、上清液状况来确定。
原则上要以较大的处理能力结合较佳的处理效果为原则来确定差速度参数,在絮凝剂用量合理、离心机转速固定、进泥浓度相对稳定情况下,设备处理能力和脱水效果完全取决于差速度的控制。
2.5 絮凝剂加药点的调整
不同的絮凝剂加药点会直接影响药泥混合、反应状况,从而影响到絮体的状态、强度和泥水分离状态,影响絮凝剂的消耗量和污泥处理效果。
目前部分厂商生产的离心机采用了物料混合液进入离心机位置可调的方式,具体的调整可根据实际情况决定。
3 污泥脱水运行管理和工况调整的基本原则
为了实现较佳的处理效果、较大的处理能力和较低的药剂消耗,应该依照以下原则进行现场管理。
(1)污泥脱水机的处理能力控制。在适当的范围内,结合污泥流量、絮凝剂流量和差速度进行调节,避免由于负荷突然增加造成设备过载使系统频繁波动和影响处理效果,同时又能够实现较大的设备处理效率。
(2)污泥浓度发生变化。要及时调整絮凝剂流量和差速度,既要保证处理效果又要避免浪费,污泥流量加大或污泥浓度增加,絮凝剂流量跟着增加,差速度相应加大;污泥流量下降或污泥浓度降低,絮凝剂流量跟着降低,差速度相应减少。
(3)泥饼干度。要结合扭矩数据来确定较佳差速度数值范围,原则上在不造成离心机堵塞和满足处理能力情况下尽量使用较低差速度来实现更好的处理效果和节省絮凝剂消耗。
(4)絮凝剂的型号和消耗量既取决于药剂的品质和污泥性质的匹配,也取决于与设备结构类型和运转工况的匹配,只有3者得到较佳的运转组合,才能实现较低絮凝剂消耗情况下,较佳的处理效果和较高的处理效率。
(5)所有现场管理和操作人员所要做的工作。要做到不断观察、及时调整和善于总结,尽量在可能发生的各种变化中寻求所有工况参数较佳的、相对稳定的完美配合。一般情况下,这种观察和调节1~2h就应该进行一次,要严格避免开机后就将设备运行工况参数坚持很久或一个班次而不进行任何调整的局面出现,现场的操作人员懒惰或责任心不强是造成污泥脱水车间长期运行效率不高、处理效果波动大和药耗浪费的主要原因之一。
4 卧螺离心机运行与调试记录
4.1 设备条件
南区污水处理厂污泥脱水项目采用福乐伟公司生产的Z53-4/454脱水机组,共4台,3用1备,每台机组设计处理能力要求为:污泥进料量≤60m³/h,污泥含固率≥0.7%,脱水后的污泥可达含固率20%以上,而固体回收率要达98%以上,污泥处理量为420kg/h。
4.2 絮凝剂型号
南区污水处理厂污泥脱水系统使用的是纳尔科和汽巴公司提供的干粉状高分子絮凝剂,型号分别是纳尔科9908和汽巴7652。
4.3 样板化验
在调试期间,所有样板(包括进料污泥、脱水泥饼)由宁波市城市排水有限公司监测分中心来负责化验。
4.4 调试记录
南区污水处理厂项目小组于2011年2~7月对污泥处理系统进行运行调试前日常运行参数记录准备,以及调试中运行参数的调整与分析等,相关记录如下。
4.4.1 调试前日常运行参数
时间/月日 | 0318 | 0321 | 0408 |
转鼓转速/r/min | 2410 | 2414 | 2401 |
差速/r/min | 4.2 | 3.8 | 5 |
扭矩/% | 25 | 25 | 25 |
进料流量/m³/h | 25 | 26 | 27 |
污泥含固率/% | 1.5 | 1.6 | 1.5 |
绝干污泥量/kg/(h·台) | 375 | 416 | 405 |
絮凝剂流量/m³/h | 0.68 | 0.68 | 0.68 |
絮凝剂浓度/% | 0.2 | 0.2 | 0.2 |
絮凝剂投加量/kg/h | 1.36 | 1.36 | 1.36 |
泥饼含固率/% | 20.5 | 21 | 21 |
污泥固体回收率/% | 98.5 | 98.5 | 98.5 |
实际绝干污泥产生量/kg/h | 369 | 409 | 400 |
单位绝干污泥耗药量/kg/t | 3.69 | 3.33 | 3.4 |
4.4.2 转鼓转速设定调整
在其他参数不变的情况下,主要调试转鼓转速运行于哪个参数点时,其进泥流量(处理量)可提高、泥饼干度不变或有所提高;在回收率不得下降的前提下,差速运行于哪个范围(是否在安全的理想区域)需要增加絮凝剂量。
本次调试将转鼓转速由调试前额定转速75%调整至85%,并且在出水清液温度的情况下,将处理量由27m³调整为29m³。2011年7月21日调试运行参数如下:
项目 | 调试前 | 调整后 | 调整后 |
时间 | 09:00 | 10:00 | 10:30 |
转鼓转速/r/min | 2410 | 2731 | 2727 |
差速/r/min | 4.3 | 5.5 | 5.3 |
扭矩/% | 25 | 25 | 25 |
进料流量/m³/h | 25 | 27 | 27 |
污泥含固率/% | 1.8 | 1.8 | 1.8 |
绝干污泥量/kg/(h·台) | 450 | 486 | 486 |
絮凝剂流量/m³/h | 0.68 | 0.68 | 0.68 |
絮凝剂浓度/% | 0.2 | 0.2 | 0.2 |
絮凝剂投加量/kg/h | 1.36 | 1.36 | 1.36 |
泥饼含固率/% | 20.5 | 21 | 21 |
污泥固体回收率/% | 99.5 | 98 | 98 |
实际绝干污泥产生量/kg/h | 447.8 | 476 | 476 |
单位绝干污泥耗药量/kg/t | 3 | 2.86 | 2.86 |
本次调试将转鼓转速由调试前额定转速75%调整至85%,经观察分析,泥饼含固率略有上升,固体回收率略有下降,但在标准值之上,其他参数未变化;而由于转速的提高,可以提高进泥量2m³,相对提高约7%,若再提高额定转速至95%,则回收率降低,因此一般认为转速调整为85%左右比较适宜。
4.4.3 恒扭矩值设定调整
在其他参数不变的情况下,主要调试扭矩设定于哪个参数点运行时,其进泥流量(处理量)可提高、泥饼干度不变或有所提高,在回收率不下降的前提下,差速运行于哪个范围(是否在安全的理想区域)需要增加絮凝剂量。
本次调试将扭矩值由调试前25%调整至30%及35%。2011年7月25日调试运行参数如下:
项目 | 调试前 | 调整后 | 调整后 | 调整后 | 调整后 |
时间 | 10:00 | 10:30 | 11:00 | 14:00 | 14:30 |
转鼓转速/r/min | 2731 | 2731 | 2731 | 2731 | 2731 |
差速/r/min | 5.1 | 4.8 | 4.6 | 4.0 | 4.2 |
扭矩/% | 25 | 30 | 30 | 35 | 35 |
进料流量/m³/h | 27 | 27 | 27 | 27 | 27 |
污泥含固率/% | 1.8 | 1.8 | 1.8 | 1.8 | 1.8 |
绝干污泥量/kg/(h·台) | 486 | 486 | 486 | 486 | 486 |
絮凝剂流量/m³/h | 0.68 | 0.68 | 0.68 | 0.68 | 0.68 |
絮凝剂浓度/% | 0.2 | 0.2 | 0.2 | 0.2 | 0.2 |
絮凝剂投加量/kg/h | 1.36 | 1.36 | 1.36 | 1.36 | 1.36 |
泥饼含固率/% | 21 | 22 | 22 | 22.8 | 22.9 |
污泥固体回收率/% | 98.5 | 98 | 98 | 96.5 | 96.5 |
实际绝干污泥产生量/kg/h | 478.7 | 476 | 476 | 469 | 469 |
单位绝干污泥耗药量/kg/t | 2.84 | 2.86 | 2.86 | 2.9 | 2.9 |
本次调试将扭矩由调试前额定扭矩25%调整至30%,经比较分析,固体回收率略有下降,但还在标准范围以内,其他参数未变化;而由于恒扭矩设定值的提高,可以提高泥饼干度,提高率约1%;若扭矩再提高至35%,泥饼干度略有提高,提高率约0.9%,而回收率降低至标准线以下,只有96.5%左右,且药耗也有增加。此次调试认为恒扭矩一般设定为30%左右比较理想。
4.5 调试结论
(1)调试前运行参数。离心机运行参数设定:转鼓速度设定为设计转速的75%,即2410r/min,在差速为3.8r/min,及设定恒扭矩为25%的状态下,进料污泥浓度为1.6%,其处理量达25m³/h,相当于污泥处理量为486kg/h,泥饼干度可达含固率20.5%,而固体回收率也达到98.5%。单位绝干污泥耗药为3.4kg左右。
(2)调试后运行参数。离心机运行参数设定:在转鼓速度设定由原来转速的75%(2410r/min),调整为转速的85%(2730r/min),差速为4.6r/min左右,及设定恒扭矩为30%的状态下,进料污泥的浓度为1.8%,其处理量可达27m³/h,相当于污泥处理量为486kg/h,泥饼干度可达含固率22%,而固体回收率也达到98%。单位绝干污泥耗药为2.8kg左右;通过转鼓转速及恒扭矩两个参数的两次调试,在其他参数基本未变的情况下,提高了处理量10%左右,恒扭矩设定值的提高,相应的提高了泥饼干度约1%左右;两个关键性指标得到了明显的提高。
(3)主要技术经济指标调试前后比较。因处理量上升10%,而对应电耗上升3%,总体能耗下降7%,药耗下降也达7%,综合电耗与药耗共下降10%左右。由于单位处理量的上升,设备的利用率也上升,因此损耗率明显下降,相应的维护保养期限延长,从而节省了设备维护的成本。