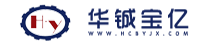
近年来,随着国家大型炼化一体化项目的开展,国内PTA的产能增长迅速,促使国内PTA行业之间的竞争渐渐加剧。相对较老的装置只有通过不断的进行系统优化才能提高企业在市场中的竞争力。
嘉兴石化有限公司一期采用英威达技术于2012年投产。相对于现有工艺技术而言,该装置仍有许多的地方需改进与优化。PTA氧化单元是以钴、锰、溴为催化剂,乙酸为溶剂。实际生产中氧化催化剂的使用量较多而且成本偏高,同时氧化单元离心机分离效果的优劣在优化催化剂单耗中起到了重要作用。因此,结合装置的现状对离心机分离效果进行简单优化进一步降低催化剂消耗。
1 离心机工作原理
氧化单元离心机的主要作用是反应生成的母液和沉淀剂混合形成沉淀,在离心机的高速旋转下,将催化剂进行分离,回收。
母液进料、沉淀剂、稀碱混合后通过离心机的中央被输送至离心机入口。固体堆积在碟片下侧,经过离心机外围的管嘴,被排放到出料浆料中。液体上升到离心机的中央,并以溢流方式离开装置的顶部。
2 离心机特性分析
离心机分离效果主要是关注溢流液中金属离子的含量以及离心机下线碱洗的时间差。在本文中将溢流液中金属离子含量200mg/kg作为标准进行分析。
2.1 离心机分离效果的主要表征
2.1.1 溢流液中金属离子的含量
金属离子的高低是体现分离效果较直接、较主要的指标。金属离子含量较低,则金属的沉淀率较高,使氧化装置中堆积的耐腐蚀金属得到循环。金属离子含量较高,则催化剂金属的沉淀效率较低,大量金属被损耗。
2.1.2 离心机碱洗的时间间隔
碱洗时间间隔越长,说明离心机分离效果好,离心机在线运行时间越长。
2.2 离心机分离效果的影响因素
2.2.1 离心机进料量
离心机进料量过大,沉淀的固体好多,则会导致离心机管嘴堵塞。进料量过低,则不能满足装置的需求,减弱了离心机的作用。
2.2.2 沉淀剂温度
沉淀剂的温度过低,则沉淀剂可能从溶剂中析出。温度过高,则沉淀剂的腐蚀性将增强。
2.2.3 离心机转速
离心机转速过低,则沉淀物中固液分离不充分。转速过高,则分离后固体质量浓度过大导致管嘴堵塞。
2.2.4 离心机管嘴
离心机管嘴过小,则分离后固体浆料不易通过造成堵塞。
2.2.5 稀碱加入量
稀碱的加入主要是防止发生腐蚀。加入量过低,则离心机的碟片和下游侧设备有可能出现腐蚀。加入量过大,则稀碱进入氧化反应器导致催化剂的活性降低。
2.2.6 DH溶剂加入量
DH溶剂的加入主要是洗涤置换含有稀碱的母液。加入量过低,则洗涤效果比较差。
3 实施对策及效果
3.1 实施对策
(1)离心机中沉淀剂与总金属比例由原来1:1提高至1.6:1。
(2)沉淀剂浓度控制在10%~15%。结合质量浓度的变化,对沉淀剂加入量进行适当调整。
(3)沉淀剂温度控制在40~45℃。
(4)DH溶剂加入量控制在4~8t/h。结合稀碱的加入量,对DH溶剂加入量适当调整。
(5)离心机分离后固体浆料质量浓度控制在3000~3500kg/m³。
(6)稀碱与进料量比例控制在0.013:1。比例可根据化验分析结果适当调整。
(7)进料量一定时,离心机转速控制在3650~3750r/min效果较佳。
(8)转速一定时,进料量控制在24~27t/h效果较佳。
3.2 实施效果
3.2.1 金属离子含量变化
通过采取上述措施,主要从溢流液中金属离子的含量和碱洗时间差进行对比分析。
实施后离心机碱洗时间差为14小时,比实施前的8小时大大的延长。同时实施后的金属离子含量由原来的45mg/kg降至30mg/kg,起点的降低幅度明显。采取相应措施后金属离子含量随着时间推移还是有一定的上升,但总体效果还是有所改观的。
3.2.2 氧化单元CTA质量
减少装置中金属离子的损失可能会造成金属离子的活性降低,进而导致氧化单元CTA中4-CBA的波动。因此,对氧化单元CTA中4-CBA进行了跟踪。
措施实施后,氧化单元CTA中4-CBA含量在允许范围之内可控,质量比较稳定,未给精制单元带来问题。
4 结语
采取上述的优化处理措施不难看出,金属离子损失、离心机碱洗时间差均得到了很大改善,并且氧化单元CTA中4-CBA含量符合生产要求。
离心机分离效果的极大改善,不仅降低了装置中能源的消耗,而且提高了企业的经济效益和社会效益,为更好地建立节能、低耗、绿色、环保的企业树立了新的榜样。