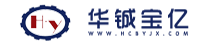
卧螺离心机是一种卧式螺旋卸料、连续操作的沉降设备,广泛用于矿业、石油、化工等行业。其外形尺寸一般为长3.5~4.5m、宽1~1.2m、高1.2~1.5m,整机质量为3~4t,处理能力高达45m³/h。目前对于卧螺离心机的研究基本上以数值模拟为主。杨钊等应用SolidWorks对大长径比卧螺离心机的转鼓-螺旋推料器进行了三维建模,研究了导程、转速、叶片厚度等参数变化对螺旋推料器应力和变形的影响,以实现对离心机的优化。于萍等对卧螺离心机的离心分离场速度进行仿真分析,求解得出分离场轴向速度、周向速度、径向速度与结构特性参数之间的关系,在此基础上对离心场中固体颗粒的运动状态进行仿真,得到其运动规律。董连东等对卧螺离心机内压力场进行数值模拟,研究了应力场分布随转鼓转速的变化关系。付双成等基于Euler多相流模型对卧螺离心机的速度场进行数值模拟与分析,研究了转鼓对沉降分离的作用。姜毓圣等研究了物性参数对卧螺离心机分离性能的影响,对不同颗粒直径、固相密度和液相黏度条件下离心机的内部流场进行了三维稳态计算。何飘等从分离效率的角度对卧螺离心机转鼓内的流场进行了数值分析,通过定义沉降粒度和上浮临界粒度,进一步将分离能力计算与分离效率相关联,使该方法更接近离心机分离工艺的实际情况。张雷基于离心分离理论,应用有限元方法对转鼓和螺旋推料器进行静力分析、模态分析和临界转速计算,研究其结构强度及运行参数对结构强度的影响。荆宝德等采用Fluent软件对卧螺离心机转鼓锥角结构进行设计及优化,得到了优化的锥角参数随物料参数的变化规律。
现有研究主要集中在卧螺离心机的运行参数及物料参数对分离效果的影响方面,对于卧螺离心机核心部件——转鼓的结构参数对分离性能影响的研究较少。本文以某洗煤厂卧螺离心机为研究对象,对转鼓长径比、半锥角等结构参数对卧螺离心机煤泥分离性能的影响进行数值模拟研究。
1 卧螺离心机三维模型创建与网格划分
待处理物料由进料管引入螺旋推料器。转鼓与螺旋推料器以一定的速度差同向高速旋转,物料被加速后进入转鼓,在离心力场的作用下,较重的固相物沉积在转鼓壁上形成沉渣层。螺旋推料器将沉积的固相物连续不断地推至转鼓锥段,经排渣口排出机外。较轻的液相物形成内层液环,由转鼓大端溢流口溢出转鼓,经排液口排出机外。
卧螺离心机结构尺寸较长。为减少网格数量、缩短数值模拟时间,对其模型进行简化,将螺旋推料器的叶片作为无厚度的片体处理。
网格划分可分为结构网格和非结构网格。结构网格即在拓扑结构上相当于矩形域内的均匀网格,其节点定义在每一层的网格线上,且每一层节点数相等,在处理边界问题时更加准确,但对于具有复杂外形的贴体,其结构网格生成比较困难。非结构网格没有规则的拓扑结构,网格节点分布较随意,网格划分更加灵活,但其计算时需要占用较多的计算机资源。数值模拟的精度主要取决于网格质量,并不取决于结构网格还是非结构网格。本文研究的卧螺离心机的螺旋推料器具有很多螺旋叶片,难以划分结构网格,因此采用非结构四面体网格。
为提高计算精度,对主要的计算区域——物料进、出口及螺旋叶片网格进行加密处理。划分好网格后,检查网格质量,网格质量达到要求即可将网格导入Fluent软件设置相应的边界条件,选择湍流模型,求解,进行数值模拟。
2 数值模拟
在卧螺离心机数值模拟过程中,假设:①卧螺离心机内部流体稳态流动;②内部流体为不可压流体;③不考虑离心机内部的热量传递,忽略因旋转、碰撞产生的热量导致的温度变化;④煤泥浆中的煤颗粒均为球形,且在煤泥浆中均匀分布。
卧螺离心机内部是高速旋转的湍流流场,各向异性效应和旋转效应显著,所以本文采用雷诺应力模型计算连续相,采用离散相模型处理多相流,将离散相与连续相进行耦合计算,并利用随机轨道模型模拟颗粒在卧螺离心机中的运动轨迹。当颗粒运动到颗粒出口、转鼓壁面及颗粒侧挡板时,认为颗粒被捕集,作为沉渣从排渣口排出;当颗粒运动到液相出口时,认为颗粒逸散。颗粒密度为1300kg/m³,颗粒直径为20,40,60,80μm,质量分数均为25%。
进行数值模拟计算时,选用压力耦合方程的半隐算法求解压力和速度场。由于卧螺离心机模型采用四面体网格,而压力插值格式适用于四边形或六面体网格,所以本文选择Standard压力插值格式,其余的离散化方式均选择二阶迎风格式。
数值模拟计算步骤:①利用单相流模型,求出清水的稳定流场;②采用DPM,在清水流场的基础上向流场中加入固相颗粒,对离散相与连续相进行耦合计算,利用随机轨道模型求出颗粒在卧螺离心机内部的分布情况。然后对卧螺离心机内固液两相流场的速度、压力及湍流动能进行分析,得到速度场、压力场及湍流分布规律,并分析其流场和分离性能之间的关系;③以相同方式研究不同结构参数和运行参数对卧螺离心机分离性能的影响。
3 模拟结果分析
3.1 转鼓长径比对分离性能的影响
转鼓包括锥段和柱段,其半锥角为θ。本文通过改变柱段长度来改变转鼓长度,从而改变长径比。
为分析不同长径比对离心机分离性能的影响,对煤泥浆从分料口(选取分料口截面中心点)进入螺旋流道的入射速度随长径比的增大而降低。长径比为3.8时,入射速度为40.20m/s;长径比增大到4.5时,入射速度降低为38.30m/s。可见,长径比的增大不仅可以从距离上延长煤泥浆在离心机的停留时间,也可以从速度上延长煤泥浆的停留时间,有利于提高离心机的分离效果,降低排渣的含水率。随着长径比的增大,锥段参考点压力先增大后减小,在长径比为4.3时,压力较大,为1.45MPa,此时对煤泥浆的挤压作用较强,排渣含水率较低。
不同长径比情况下 ,当长径比为4.3时,离心机分离效果较好,且分离效率较高。但较大的长径比会影响生产成本、能耗等,因此在实际选用时应综合考虑各种因素,以获得较大经济效益。
3.2 转鼓半锥角对分离性能的影响
待分离物料进入转鼓旋转分离后,物料在螺旋推料器的作用下,被推往锥段进行挤压脱水排渣,固体渣在锥段仍含有大量水分,所以在锥段需要进一步挤压脱水。半锥角大小直接影响排渣含水率。半锥角过小,对于煤泥浆达不到很好的挤压脱水效果;半锥角越大,对煤泥浆的挤压效果越明显。但半锥角过大会影响渣顺利排出,从而影响离心机的处理能力,甚至造成渣堵塞现象,使离心机无法正常工作。
在其余结构参数不变的情况下,选取半锥角为6,7.5,9,12°,分析半锥角变化对离心机分离性能的影响。煤泥浆进入螺旋流道的入射速度和压力如下:
半锥角(°) | 入射速度(m/s) | 压力(MPa) |
6 | 39.14 | 1.37 |
7.5 | 38.50 | 1.13 |
9 | 38.94 | 1.45 |
12 | 39.14 | 1.36 |
从上表可以看出,随着半锥角增大,煤泥浆进入螺旋流道的入射速度先减小后增大,在半锥角为7.5°时较小,为38.50m/s,此时对应的压力较小,煤泥浆脱水后含水率较高。半锥角为9°时,煤泥浆进入螺旋流道的入射速度较低,与半锥角为7.5°时相差不大,此时锥段参考点压力较大,对煤泥浆的挤压作用更强,有利于煤泥浆脱水。
不同半锥角情况下卧螺离心机分离效率为:锥角从6°增大到12°时,分离效率先增大后减小,当锥角为9°时,分离效率较高。
4 结论
(1)煤泥浆进入螺旋流道的入射速度随转鼓长径比增大而降低,而锥段参考点压力随转鼓长径比增大呈现先增大后减小趋势。在长径比为4.3时压力较大,为1.45MPa,此时对煤泥浆的挤压作用较强,排渣含水率较低;在长径比为4.0,4.3时,卧螺离心机分离效率较高,达0.98以上。因此,当转鼓长径比为4.3时,离心机分离效果较好,且分离效率较高。
(2)在转鼓半锥角为9°时,煤泥浆进入螺旋流道的入射速度较低,锥段参考点压力较大,对煤泥浆的挤压作用较强,有利于煤泥浆脱水,且此时卧螺离心机的分离效率较高。