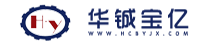
锦州石化精细化工公司磺酸盐装置主要用于分离105车间的滤渣,再经过减压蒸馏,得到磺酸盐,即润滑油添加剂。LW355×1160-NC型卧式螺旋沉降离心机是装置分离过程中的关键设备,它的运行质量对整套装置尤为重要。
此设备在连续运转过程中经常出现振动过大、泄漏以及螺旋输送器叶片磨损严重等问题,极大影响了磺酸盐装置的正常生产,且分离效果不好。经仔细检查、分析、论证,针对该离心机出现的上述故障作了一系列的技术改造工作,确保了正常生产。
1 螺旋输送器改造
用于磺酸盐介质分离的卧式离心机,由于其高速转动过程中物料与机体间的相互作用,作为主件的螺旋与转鼓内壁的物料存在严重的边缘直线硬磨损(径向磨损),且具有很强的冲刷性质的软磨损(轴向磨损),从而导致白钢转鼓的出料口处因出料过程中的动态磨损,转鼓被横向切断。在检修的过程中,对螺旋的工作现状及磨损的过程和原因进行了认真分析和研究,并查阅了相关的处理工艺,同时征询有关表面处理专家和专业焊接人员的意见和建议,认为应用现有手段进一步提高螺旋叶片耐磨性的工艺方法主要有两种,即进行叶片边缘喷涂和镶焊硬质合金带。
喷涂方法有表面喷涂碳化钨层和喷涂陶瓷层两种。前一种方法该离心机原生产厂即可进行,但碳化钨层薄,耐磨性远不如镶焊硬质合金,且使用的周期短,需多次返厂修复,陶瓷层喷涂是金属材料表面加强的一种新工艺,其耐热、耐磨性好,但耐冲击性及脆性存在缺点。
硬质合金是高温烧结的材料,它具有良好的可焊型和极强的耐磨性,如能够用一定尺寸的硬质合金块在螺旋叶片边缘镶焊成加强带,完全可以从根本上解决螺旋叶片的磨损问题,工艺上只要在车削加工中创造必要的条件就可以为焊接提供保证。因此,采用将原间断焊接改为在受磨损的锥形叶片边缘全面加焊硬质合金带的方法,在工艺上和实际操作上具有可行性。
为保证上述工艺方法的实现,进行重新设计。硬质合金刀头尺寸、形状的选择:螺旋叶片总厚度为6mm,为保证焊接的强度和质量,确定镶焊的厚度为4mm,高度为25mm,为尽可能减少曲率影响,采用合金块长度为14.5mm(此时曲率影响为0.05mm),为保证焊接强度,选用直角梯形块,为焊接和归圆留有余量。螺旋叶片材质为1Cr18Ni9Ti,具有较好的可焊性,为保证焊接和焊后尺寸及形状符合要求,确定对原螺旋叶片在准备焊接范围车去25mm(单边),并通过车削加工车成带有台阶的焊片,作为焊接补件补焊到螺旋叶片上。使用铜焊,焊接成硬质合金带,并进行修磨处理,做动平衡。此项措施的实施收到了很好的效果,设备开工率显著提高,故障明显减少,保证了装置的正常生产。
2 机壳大端改造
离心机大端从机体上盖与下盖的缝隙中向外渗油,其原因在于生产过程中清液较多,从溢流挡板向外溢流时形成压力,从其小孔带压向外喷出,喷到上下机壳的连接处,从而引起清液由上下机壳的缝隙向外泄露。解决措施是:将上下机盖贴合处加一环形挡板,通过焊接方式将其连接到上机盖内侧,在此处形成搭接式的密封,这样由溢流挡板孔喷射出来的清液就直接喷到了后加的环形挡板上,沿环形挡板向下流入溢流口,正常排出机体。这一问题的解决既为磺酸盐厂节约了芳烃及磺酸盐清液,同时也改善了离心机附近及其楼下始终存在油污的恶劣环境,也消除了由此带来的安全隐患。
3 减少进料管壁磨损
由于分离的物料含有较大黏性,混合液中的固相附着力很强,而离心机运行中液相的排出力又很弱,致使进入螺旋内腔的物料部分不能顺畅地投入到转鼓中去,出现了回弹,附着到转鼓筒内壁,时间一久就形成了强硬的粘块,刮磨进料管,导致进料管磨损,加剧了设备的振动,严重时会将进料管磨断。
通过对离心机运行中液相分离过程的动态分析,认为螺旋内筒积料现象与离心机的进料与排液是否顺畅有关,如果能够使离心机的进料量与排出量保持均衡、顺畅,反弹粘料的现象就不会出现。
采取的解决办法是首先调整了进排气通路,再将进料管加工成带夹套的阶梯型,夹套进料端接入氮气,另一端均匀钻出6个排气孔,形成对反弹物料的冲击,消除或减少了粘料现象。
4 改进进出料口的连接方式
离心机是高速回转设备,整机安装采用的是减震固定,其进出口的连接必须采用软连接。
以往,锦州石化精细化工公司的磺酸盐装置在进料口和排液口采用的是弹性软管连接,此部分由于无动力源,因此基本可行。在排渣出口采用不锈钢双法兰膨胀节与下面螺旋输送机的进料方箱连接,由于下面是动力设备,而膨胀节相对较硬,连接后上下全部运行时,离心机、输送机乃至整个装置形成了振动的共携体,出现了振动干涉,增加了设备的损坏频次,加大了故障判断和处理的难度。通过多方查找和分析对比,选用一种氟橡胶衬里软体双法兰膨胀节。经使用后,彻底切断离心机与输送机的振动联系,实现了既密封又抗振、减振的良好效果。
5 保证平衡进料
LW355×1160-NC型卧式螺旋沉降离心机的优点之一是能够连续工作,要使这一优点得到较大发挥,就要保证进料量定量并可调,以满足设备处理量的需要,而锦州石化精细化工公司的磺酸盐装置采用的工艺结构设计由于存在缺陷,采用搅拌釜重力进料,手动阀门控制,物料的黏性及各种杂物的存在导致操作中不断发生堵料现象,迫使离心机总是处于饥饱不均的状态,既影响了分离质量,也降低了生产效率,并导致设备故障频发,一直难以解决。
根据该机的工作特点,采取的解决措施是选用单螺杆泵作为进料泵,变频控制,泵前加过滤器并安装压力传感器,控制无料或断料,开阀冲堵或报警。
6 制定维护措施
以上是对离心机在实际生产中出现的一些故障相应进行的系列改造。根据对上述故障的分析,对此卧式螺旋沉降离心机制定维护措施如下:
(1)每半年对设备检查1次,一年进行1次大修。
(2)润滑:每天必须对两端轴承加注3#锂基脂50g左右,每周必须从差速器输入轴中心注油孔注入3#锂基脂500g左右,每半年清洗换油1次。
(3)制定卧式离心机巡检表。
通过采用以上维护措施,该卧式螺旋沉降离心机运转至今未出现较大异常,保证了磺酸盐装置的正常生产。