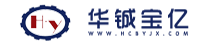
1 关于老化油回收方法的探讨
(1)老化油的来源。回收的老化油主要来自以下三个渠道:一是污水站斜板罐内回收的老化油;二是矿回收点从各地回收的落地原油;三是污水沉降罐内的含水污油。
(2)老化油影响脱水电场的原因。从大庆油田采油一厂聚413站收油记录、矿化油点收油记录、中七联外输岗收油记录来看,每当回收这些老化油时,经常出现脱水电场分离不好、含水超标、脱水器电流上升及频繁放电,最终导致电场瘫痪的现象。从实际生产操作及监测看,人为操作的因素完全可以排除,脱水电场不稳、脱水效果不好的主要原因是进入电场的老化油没有破乳造成的。没有破乳的原因有三方面:一是温度低;二是破乳剂用量低;三是原油的油品差。
2 应对措施
(1)针对温度低采取措施。提高脱水温度,由52℃提高到55.7℃,但脱水效果没得到好转。
(2)针对乳剂用量低采取措施。增加破乳剂用量,药量由200kg/d增加到550kg/d,采取措施后没收到好效果。温度从52℃提升到55℃没有起绝对作用,药量从200kg/d增加到550kg/d也没起绝对作用,说明目前的温度、药量不是影响脱水电场的主要因素,影响脱水电场的主要因素是原油的油品差。
(3)针对原油的油品差采取的措施。原油的油品差主要是胶态的硫化压亚铁(FeS)影响老化油的破乳,对于硫化亚铁影响脱水电场的问题曾用不同的方法进行研究,中七联采取的收油措施为改造加药流程,使用化学药物、改造收油流程,间接回收老化油、按比例控制排量,回收老化油。
3 回收老化油方案的对比
(1)改造加药流程,使用化学药物。为了驱除老化油中的FeS以利于回收老化油,中七联配合设计院从2005年2月25日~2005年3月25日进行老化油回收实验。
在2#罐加油水分离剂,在1#罐加FeS驱除剂,加药后观察含水超标及外输水质情况。
(2)改造收油流程间接回收老化油。为解决老化油的回收、缓解中七联罐存,3月26日从中七联外输岗收油泵出口接一条去聚413队2#计量间出口干线,使回收的老化油进入聚413站。
该流程3月26日开始运行,由于初期没有掌握好合适的收油量,使去聚413站收油量过大,导致413站收油次数多、瞬时量过大,致使中七联多次垮电场,外输含水多次超标。仅4月份就收油19次,收油3760t,平均每次收油198t,该流程在初期阶段没有达到预期目的。
(3)按比例控制排量,回收老化油。从以上探讨的各种方法中,总结失败的教训,收集整理正常收油时的数据进行分析研究,确定出合理的收油量,同时找到老化油与净化油的合理配比,按照配比进行控制收油量,实施后效果很好。
从实际收油统计表及收油量、电场、含水之间的关系曲线上分析,当净化油与老化油的比例为小于或等于11%时,电场比较平稳,脱水效果较好。当收油时间短、瞬时量大,净化油与老化油的比例大于11%时,含水高。正常生产时加药量为350kg/d,加药比0.5/10万,收油时加药量可以增加到400~500kg/d,加药比0.7~0.8/10万时电场稳定,脱水效果好。当各单位在同一时间集中收油瞬时量过大时,电场不稳,脱水效果不好。
4 结论
对影响脱水电场稳定的各项原因进行分析后,提出回收老化油的最佳方法如下。
(1)收油时小班工人要严密监视外输仪表的瞬时排量,及时调整,使老化油进入油系统的比例不超过11.1%。
(2)各单位收油时间尽量错开,以免同时收油,造成老化油瞬时量过多。
(3)根据老化油的收油量适当增加加药量。正常生产时加药比为0.5/10万,当收油时加药比可以增加到0.7~0.8/10万。
经紧密与413站、收油点联系,协商将泵排量控制在30m3/h以下(25t/h),错开收油时间,收到较好效果,脱水电场平稳、含水不超标。
5经济效益评价
采用定量控制方法回收老化油,既方便又经济,方便是指根据来油量大小随时调解收油量,保证配比小于或等于11%。
(1)节约加药量。经济是指不用机械的增加药量。此前分离不好时最高加药量550kg/d,目前正常生产时来液量70000t/d,加药量350kg/d,收油时加400~450kg/d,平均每次少加150kg/d,每月按15次加药可节约2.25t。每吨药按8000元计算,每月节约折合人民币1.8万元,每年药量节约21.6万元。
(2)避免净化油量的损失。电场不稳,外输油不合格,平均每年回罐15次,平均每次回罐225t/h,回收率只有90%,每年将损失338t净化油。每吨净化油按800元计算,将挽回损失27万元。
(3)节约能耗。少回罐也避免重复收油,平均每次回罐按225t/h计算,用收油泵回收时间至少10h,每小时耗电8.4kW·h,每次收油耗电84kW·h,每度电按0.5元计算每年可节约630元。
因此采用定量控制、合理配比回收老化油是一种非常实用的创效方法。