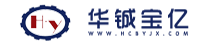
某远洋船舶主机型号为MAN B&W 8L460C,额定功率8400kW,缸径460mm,行程560mm,额定转速500r/min,配备2台阿法拉伐S型滑油分油机。
船舶在前次航行过程中出现分油机排渣口跑油故障,值班人员赶到机旁还未来得及消除警报,分油机已经自动停机。排渣口跑油导致分油机不能正常工作,无法对滑油进行分离清洁,含有水分和杂质的滑油会使其润滑及冷却效果变差。分油机长时间停机会对主机安全可靠运行造成巨大危害。
本文对分油机排渣口跑油故障进行分析,确定故障原因,并提出相应的使用管理注意事项,为传播轮机人员提供参考。
1 分油机原理及工作流程
阿法拉伐S型滑油分油机的特点是不设比重环,采用集成化程度高的EPC50控制系统单元。分油机主要由分油机本体,水阀组SV10,SV15,SV16,气阀组V1,V4,V5,水分传感器MT50,温度传感器TT1,TT2,压力传感器PT1,PT4,PT5,转速传感器ST,三相异步电机,滑油供给泵及蒸汽加热器等组成。
工作流程如下:
(1)为快速将滑油中的水分及杂质分离出来,让需要净化的滑油进入分油机高速旋转,将待净化滑油置于一个巨大的离心力场中。
(2)滑油、水分、杂质的密度不同,离心惯性力也不同,会沿转动轴的径向重新分布。
(3)受离心惯性力较大的杂质和水分被甩到分离筒的外围,受离心惯性力较小的净油在分离筒的中心附近汇聚。
(4)滑油中的净油、水分、杂质按照本身密度的不同从里到外分成3层。
当分油机正常运行时,待净化滑油从分油机顶部接管不间断地进入分离筒中,净化后滑油通过分油机上部油泵出油管排出。分离出来的水通过分油机上部水泵出水管排出。杂质在分离筒的外延,通过排渣操作从排渣口排出。
净油出口管路装有MT50水分浓度传感器,能精确检测净油中的含水量,从而控制排渣周期。
分油机排渣过程:
(1)气阀V1动作,停止向分离筒内进油。
(2)水阀SV10开启,适量增加水封水,将油水分界面往里缩,减少排渣时的油损耗。
(3)水封水加注完毕后,水阀V15动作,分油机加注开启水。
(4)开启水加注标定时间设置为3s,泄放滑动底盘下部的工作水,使滑动底盘下落至下位打开排渣孔,实现分油机排渣。
分油机排渣结束后,水阀V16动作,开始加注关闭水,加注关闭水设定时间为15s,滑动底盘下部的空间重新充满水使托盘重新闭合。水阀SV10动作,加注水封水,时间为标定值,分油机打开进油阀,重新进油、分离。
2 故障现象及分析
分油机在运行过程中出现故障警报,并在1min内自动停机。查看EPC50单元控制面板,发现净油出口压力PT4偏低警报,造成分油机转速下降,进而自动停机。检查外围系统,发现水压、气压正常,重启分油机后不久又重复出现此警报。根据分油机结构及工作原理,分油机跑油的原因主要有以下几点。
(1)淡水、压缩空气压力不足。淡水压力不足,使得分离筒底部工作水腔的水量减少,导致排渣口不能按规定时序开启和关闭。如果在非排渣时序排渣口异常开启,分离筒的油就从排渣口排走。气压正常值为2~6bar,若气压不足,将导致各气动阀门开启时间和大小均与设计值不符。这导致分离筒底部工作水腔水量不足,分离筒关闭不严,造成排渣口跑油故障。
(2)分油机转速不足。分油机转速不足,分离筒本体就不能产生足够大的离心力,分油机工作水腔内的水不能靠离心力托起水环,无法实现托盘的开启和封闭。导致分油机转速不足的原因有很多,包括摩擦片损坏、电机故障、皮带打滑、立轴磨损等。
(3)分离筒中O型圈老化。分油机本体中有许多O型圈,尤其是分离筒的各油腔水腔间有大量O型圈,通过O型圈实现各液腔间的密封作用。如果O型圈老化严重,就会使得密封效果不佳,导致水压无法建立,排渣口不能密封。密封不佳将导致排渣口不断有油被甩出,排渣口的检查装置就会检测到排渣口跑油,从而发出故障报警。
(4)分离筒主密封环被大块渣滓卡阻,分离筒关闭不严。工作水腔的泄水孔被堵塞,不能正常泄水,导致工作水腔密封不严,排渣口跑油。
(5)滑块无法正常下移,导致工作水腔的泄水口堵塞,油从泄水口跑掉。
(6)分离筒底部水腔结垢严重。分油机工作温度较高,分离筒底部水腔容易结垢。结垢严重将导致水腔内部水压无法建立,甚至造成节流排水孔不通畅,从而影响排渣口的开启与闭合。
3 故障定位及排除
由于该船长期在海上作业,分油机一直在运行。每次值班人员巡视分油机时,水、气阀组未见异常,油温、油压均在正常范围内,分油机电机运转正常。故障发生后尝试重新启动分油机,发现分油机一进油就出现PT4压力低警报,初步判断为分离筒无法形成有效水封,油水分界面外移,导致油从排渣口跑掉。
根据分油机结构,水封水的密封效果是靠分离筒与滑动底盘的良好密封保证的,其中主密封环是水封水的密封环,在分离筒盖上阻止水封水泄露。在分油机正常分油时,滑动底盘由底腔工作水托起,贴合分离筒盖,由主密封环密封贴合面。若密封环损坏,则不能进行有效密封,使得分离筒内的油水与排渣口直接相通,油很容易从分离筒与活动底盘的间隙中泄露。只有少量的水进入滑动圈上部,导致分离筒与滑动底盘无法紧密地贴合在一块,从而造成分离筒内的油从排渣口跑掉。
在对分油机进行拆解的过程中,发现分离筒底部有明显杂质,拿出后发现是小木片。取出密封环发现密封环被木片压出一个口子,已经变形。密封环受损使得分离筒无法形成有效水封,导致排渣口跑油。
清洁并装复分油机零部件,启动分油机后仍出现同样的警报。再次检查系统,给分油机供水的压力水柜水压正常,说明分油机工作水压正常。拆卸分油机检查分油机内各道密封圈,均属于正常工作状态。再次检查控制水系统,发现水阀组的节流孔板安装错误,由于工作人员在拆卸过程中对水阀组进行清洁,误把SV10与SV16对调,导致安装错误。调换后,分油机工作正常。
4 管理注意事项
分油机是保证主机正常运行的重要辅助设备,在实际的管理过程中需要加强巡视检查,在操作过程中要细心谨慎,严格按照说明手册操作设备,从而减少类似故障的发生,提高分油机的正常使用效率。因此,在日常操作管理中要注意以下事项。
(1)分油机是高速运转的设备,工作条件要求较高。必须严格按照使用手册的要求,提供适当的水压、水温,尤其须定期检查工作水的水质,定期清洁水阀组滤器,确保滤器处于正常工作状态。定期检查油底壳的油位是否在正常液位范围。
(2)在日常管理过程中,应记录每次更换备品、备件的时间。根据服务说明书,在相应的维修周期内及时对分油机进行拆解、清洁,并视情使用分油机的小修包或大修包,适当更换分油机中的O型圈。如果要长期停用分油机,须定期拆卸分油机,对立轴上部轴承涂抹润滑油,防止没有添加润滑油就直接启动分油机,造成轴承异常磨损。
(3)在值班过程中,应经常检查油、水、气压是否正常,观察孔是否有泄露。用点温计检查电机外壳温度,用听棒检查分油机振动是否异常,使待净化滑油加热温度及进油量保持在恒定范围内,确保良好的分离效果。
5 结束语
对于四冲程的中速柴油机,滑油含有许多的残留炭粒和金属磨粒等污物,需要分油机对滑油分离清洁。分油机的好坏直接影响船舶主机的安全性和可靠性,因此,只要主机在运行,分油机就必须保证持续运转。
阿法拉伐S型滑油分油机是高自动化设备,EPC50控制系统也具有强大的处理功能,能够按照使用者的要求,实现自动排渣操作并设置较大、较小的排渣间隔周期。由于此类型分油机无比重环,滑动底盘不再使用弹簧控制排渣口的开启与关闭,而是采用工作水腔的形式。这不仅提高排渣的工作效率,而且降低分油机的故障率。在管理过程中,应对分油机定期进行维护保养,根据部件的工作情况进行清洁、检查和换新,并保证良好的工作水质,降低分油机故障率。