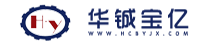
碟式离心机是化工装置的重要设备之一,它是利用悬浮液(或乳浊液)各组分密度的不同在离心力场中迅速沉降分层的原理,实现液-固(或液-液)分离。如其运行不正常则后系统的分离提纯难度将大大增加,从而直接影响到产品的质量。某化工企业装置产能扩大后碟式离心机振值一直较高。其检修周期从原来的平均90天减少至25天。碟式离心机的主要备品备件是靠进口采购,不仅费用高而且采购周期长。本文将从工艺和设备两个方面进行系统分析,提出改进和应对措施,实现装置的安全、稳定、长周期高效运行。
1 工艺方面
1.1 原因分析
由于装置产能的扩大,系统中需要分离的碱含量也随之增加,使碟式离心机处于超负荷运行状态,进而使得碟式离心机的主要部件涡轮、蜗杆加速磨损,从而进一步造成了碟式离心机的高振动。结合生产及拆检情况分析,主要因素有以下两点。
(1)倾析器流出物料中碱含量明显增加。倾析器主要是利用物料中的粗产品和碱相对密度的不同,通过降低物料的流速来达到碱和粗产品分离。碱的抽出是靠倾析器的液位调节器来定时抽出,但由于负荷提高后除碱的液位调节器不能正常工作,从而使碱不能及时抽出而造成碱含量增高。
(2)粗产品中间罐出料中的碱含量高。装置产能扩大后进行的每周两次的粗产品中间罐排碱过程中,每次排出的碱量都超过总体积的1/2以上,滞留在粗产品中间罐中碱量较多。
1.2 应对措施
(1)倾析器系统改造。首先对倾析器的排碱系统进行了改造,通过在其液位调节器的管线上增加一个调节阀,增设自动排碱控制系统,通过自动排碱系统便能将其碱液位控制在较低的液位,从而保证进入倾析器的碱有效地分离脱除,实施此项措施后,倾析器出料中的碱含量降至管理制;其次对倾析器增设伴热装置,将其严格控制在粗产品和碱的较佳分离状态,确保分离脱出效果。
(2)粗产品中间罐系统优化。首先针对装置产能扩大后粗产品中间罐排碱过程中,每次排出量都超过总体积1/2以上的情况,将粗产品中间罐排碱的定期作业频率由每周二次增加至五次,保证了系统的碱从粗产品中间罐得以及时有效地脱除;其次针对粗产品中间罐出料中的碱含量高的情况,将粗产品罐的出料位置提高70cm,使碱在粗产品储罐中充分沉降后和粗产品分离,使含碱量少的粗产品从上部抽出后进入后系统。此项措施实施后使粗产品储罐出料中碱含量达到管理值要求。通过工艺技改和优化操作,系统中碱含量下降了1.2%,有效地降低了离心机的分离难度。
2 设备方面
根据碟式离心机的结构和工作原理,结合长期维护检修经验,影响碟式离心机稳定运行的设备因素及解决对策主要有以下几个方面。
(1)转筒自动清洗效果不好。该型号离心机具有自动周期性清洗转筒内部的功能,使分离筒内部基本没有碱垢残留,否则极易造成因分离筒不平衡而引起高振动。通过长时间分析研究和多次拆检检查,为保证离心机自动清洗效果,避免由于清洗不留底引起离心机分离筒不平衡而引起设备高振动,修改了离心机自动清洗时间程序,适当延长清洗时间,并增加了清洗频次。经现场观察确认,离心机稳定运行周期得到有效延长。
(2)分离筒失衡。分离筒分离盘装配不正确,锁紧螺帽没拧紧造成分离筒失衡;分离筒漏物料,导致分离筒重心偏离,需要根据实际情况更换内部密封垫;不同分离筒部件被互换,在实际使用中,严禁不同设备内的分离筒部件互换;分离筒受损,从而失去平衡。
(3)蜗轮蜗杆磨损严重。由于蜗轮蜗杆磨损严重造成离心机高振动,主要原因是分离筒排渣周期过短,造成蜗轮蜗杆磨损过快。按照设备生产厂家技术要求,离心机分离筒排渣周期为80秒。在离心机实际运行中发现,离心机累计运行20天振值就由1.2mm升至3.0mm以上,排渣时瞬时振值高达5.0mm以上,从而引起经常性跳车。经过反复解体检查、分析研究,结合所分离液体介质的特性,将离心机排渣周期由80秒提高到180秒,减少了因频繁排渣波动引起的蜗轮与蜗杆的磨损,离心机稳定运行时间也由20天提高到50天以上,取得了明显的效果。
(4)轴承和中间轴承桥的使用。碟式离心机一般为高转速设备,要特别注意轴承的选用和安装,若轴承裂碎和轴向径向间隙过大,也将引起离心机高振动。分离筒位置很高,重心也高,由于离心机转速很快,立轴的中部一般都设置一个减振弹簧盘,盘内有8根刚度很大的减振弹簧。当某个弹簧失效时,应同时全部换新。若不能及时更换,可加垫片或适度调节弹簧座螺母,以临时起到减振作用;这样做并不可靠,应尽早换新全部减振弹簧。此外,立轴自身磨损以及底部轴承滚珠损坏;齿轮间隙过大或轮齿磨损掉的金属合金颗粒随着润滑油一起进入蜗轮蜗杆轮齿上,破坏了油膜的形成,导致了蜗轮的加速磨损。滚珠轴承损耗等都会引起碟式离心机的高振动。
3 取得的效果
通过实施以上措施后,系统的碱含量明显降低,碟式离心机的运行状况得到了明显改善,碱分离效果大大提高,碟式离心机的振值稳定在2mm左右,碟式离心机的运转周期也由25天延长至90天,大大降低了运行成本,同时使后续的精制系统,各精馏塔的运行稳定性明显得到了改善,分离效果有了进一步的提高。而且随着精馏塔分离效果的改善,精馏塔的蒸汽单耗降低明显,年节能降低近百万元,产品质量持续保持稳定。