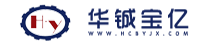
1 引言
无机陶瓷膜是近年来发展起来的一种新型膜材料,它具有耐高温、耐腐蚀、抗折强度好、不易堵塞等优点。从而被广泛应用在水处理、食品安全、化工处理等领域。但是,无机陶瓷膜的成本较高,从而导致其不能被广泛的应用到实际的生产和生活中。针对这一发展瓶颈,本文综述了如何降低陶瓷膜成本的技术路线。
2 无机陶瓷膜制备过程和影响成本因素
2.1 无机陶瓷膜制备过程
首先将原料、粘结剂、成孔剂用精密增力电动搅拌器使粉料混匀;再将烧杯置于恒温水浴锅中加热搅拌,蒸发掉多余的水分;然后陈化、挤泥机挤压成型、坯体干燥、烧结而制成性能优良的支撑体。支撑体制备完成后利用溶胶-凝胶法在支撑体上涂膜。
2.2 影响无机陶瓷膜制备成本的因素
影响无机陶瓷膜制备成本的因素主要由原料的选取、生胚加工过程、溶胶-凝胶的制备和烧结方法等步骤构成。
3 降低无机陶瓷膜制备成本途径
无机陶瓷膜具有梯度孔结构的陶瓷材料,是由支撑体和分离层两部分组成。由于膜层容易破损,因此需要较高抗折强度的支撑体作为支撑。而支撑体除了具有对膜层的支撑作用外,还应该有良好的孔径分布及孔结构,以实现对处理水的初步截留和分离,从而降低对膜层的水力冲击与负荷。
3.1 制备支撑体低成本的途径
3.1.1 原料的选取
近几年,国内一些大型企业主要以Al2O3为骨料制备无机陶瓷膜。由于在实际生产过程中原料用量大、成本高,一些研究工作者例如:张杰利用废弃资源粉煤灰和煤矸石,采用挤压成型法制备多孔陶瓷膜支撑体,以降低其原料成本,研究低温烧结,降低工艺成本。刘晶利用廉价的工业废弃物粉煤灰(SiO2和Al2O3为主要成分)和天然矿物白云石为原料,通过原位反应烧结工艺制备了钙长石-堇青石基多孔陶瓷膜。张学斌等为了降低多孔陶瓷的成本,并开发多孔陶瓷膜的新功能、新用途,以廉价非金属矿物(天然沸石、硅藻土和粉煤灰等)为原料,采用合适的制备工艺,以高温除尘和工业废水处理为主要研究方向,制备出新型的多孔陶瓷膜,并对其性能进行了表征。由此可见,原材料的选择可以降低无机陶瓷膜的制备成本。
3.1.2 添加烧结助剂
支撑体是无机陶瓷膜制备过程中的前提和基础,对于纯α-Al2O3而言,一般烧结温度需要1700℃以上,这样的高温条件不仅给实际操作带来麻烦,还大大提高了支撑体的制备成本,对于生产十分不利。研究发现,向骨料中加入合适的烧结助剂,可以降低支撑体的烧结温度,它主要分为两大类:液相型和固相型。液相型助剂(高岭土、钾长石、玻璃、磷酸铝等),可在1000~1500℃下熔融形成液相,毛细管力作用下液相在颗粒间流动,从而润湿并包围粉体颗粒,将颗粒粘结起来。固相烧结助剂(如变价氧化物TiO2、CrO3、Fe3O4、MnO3等),在1200~1400℃下形成固溶体,降低烧结温度。针对这个问题,韩磊等研究以工业硅藻土细粉为原料,硅酸钠为烧结助剂,采用发泡注凝法在1000℃保温2h制备多孔硅藻土陶瓷,其耐压强度为(1.13±0.08)MPa,比未添加硅酸钠的提高了约113%。孙小娟等以α-Al2O3为骨料,选取造孔剂羧甲基纤维素、复相烧结助剂二氧化钛和氧化铜,在1200℃温度下烧结制备支撑体,得到较佳配比下制备的支撑体孔隙率可达33%,纯水通量5107.68L/(m²·h·MPa),抗折强度104.4MPa,微观结构良好。因此,为了降低成本,通常选用性能优良的添加剂来降低烧结温度。王婕等通过在α-Al2O3添加1.5% CuO、3% TiO2制备管状陶瓷膜支撑体的较佳烧结温度为1100℃,孔隙率达到22%,机械强度为55.82MPa,同时以液相润湿作用促进氧化铝陶瓷的致密烧结。
3.1.3 成型方法
成型是将陶瓷粉料制备成具有一定形状和尺寸的生坯,常用的成型方法可以分为模压成型法、挤压成型法、流涎法、等静压成型法、注射成型法、粉浆浇注法。
此外,不同成型方法对支撑体各项性能指标有显著影响。同帜等通过模压成型法制出的支撑体平均孔径为1.86μm,孔隙率36.97%,在0.1MPa下纯水通量为2115.55L/(m²·h·MPa),抗折强度在19.78MPa,耐酸碱度为99.83%和99.86%。张帅等通过挤压成型法制得支撑体孔隙率为31.85%,纯水通量为5107.68L/(m²·h·MPa),抗折强度为104.429MPa,酸碱腐蚀质量损失分别为0.88%/0.92%的性能优良的支撑。李茂模等采用等静压成型技术和特殊的研磨、造粒控制技术,研制出直径超过200mm的薄壁电子真空陶瓷管产品成品率高,生产成本大大降低。贺毅强等通过注射成型法在1550℃烧结工艺制备的10% Cu/Al2O3复合材料具有良好的抗弯强度532MPa和断裂韧度4.97MPa·m1/2。王延庆等通过粉浆浇注法将铁粉与树脂粘结剂混合而成的粉浆浇注进硅橡胶模具中翻制试样的型坯,再对型坯进行烧结制取内部孔隙均匀的金属骨架状型坯。在前人研究的基础上综合分析,挤压成型法是制备管状多孔陶瓷一种常用的方法,主要是生产出来的产品光洁度好、坯体强度高且气孔分布均匀,工业化大规模批量生产能力强,生产成本要比其他方法低很多,完全满足无机陶瓷膜的低成本发展趋势。
3.2 分离层制备过程中降低成本的途径
3.2.1 原料的选取
无机陶瓷膜分离层的制备研究更多的采用廉价的金属无机盐为原料,来取代较为昂贵的金属醇盐。目前,杨志华开展了以廉价的无机盐Al(N03)3·9H2O为原料通过制备薄膜的研究。同帜以廉价无机盐硝酸铝为前驱体,常压、环境温度为60℃,相对湿度70%的环境下,可获得完整的、无裂痕,平均孔径为15.97nm氧化铝凝胶膜。张建松研究动态膜技术通过选用廉价的膜材料达到较为理想的效果。由分析可知,原料的选取可以明显降低陶瓷膜的制备成本。
3.2.2 涂膜次数的影响
通过涂膜液在支撑体上的涂膜过程,对涂膜液覆膜过程中存在的影响因素及成本进行分析。宋成文研究涂膜次数对PAN炭-炭复合膜性能的影响,通过观察未涂膜、涂膜1次和涂膜2次时PAN炭-炭复合膜性能的变化通过调整实验参数制备出了复合效果较好,表面光滑无缺陷的聚丙烯腈炭-炭复合膜。施圣芳以四异丙醇钛为原料,采用溶胶-凝胶法制备出完整的TiO2超滤膜。陆亚伟、陈献富等采用改进的颗粒溶胶工艺,制备出平均粒径为3nm的ZrO2-TiO2复合溶胶然后选择浸浆法,在平均孔径为5nm的管式α-Al2O3底膜上,一次涂膜后便可制得完整无缺陷的ZrO2-TiO2复合纳滤膜。涂膜溶胶中的添加剂含量、涂膜次数及涂膜时间对超滤层完整性有很大影响。涂膜次数过多,会导致膜层过厚而形成开裂影响实验效果并且增加实验成本,消耗大量资源。
3.2.3 烧结温度对涂膜的影响
大多数情况下,多孔陶瓷膜支撑体的制备与分离层的制备是分开进行的,即要进行多次烧结,而烧结过程因耗能较大导致陶瓷膜成本较大。因此,减少烧结次数对降低陶瓷膜的制备成本具有十分重大的意义。杨桂忠采用一步法制备工艺,在支撑体生坯上涂膜后经干燥一步烧结,制备除具有不对称结构的、孔隙率为39%的α-Al2O3陶瓷膜。当涂膜厚度为1.479μm时,截留分子量为75000,通量为4.350m³/(m²·h·MPa),孔隙率为39%。在涂膜过程中选择合适原料,方法同样可以降低烧结制度。如朱明燕研究在膜的制备过程中加入一定添加剂来抑制相变温度,在ZrO2膜中添加Y(N03)3,可以降低烧结温度。Uhlhorn等研究表明,溶胶中加入PVA对膜的微观结构基本无影响,但提高了膜在干燥和烧结过程中的完整性,这样有利于制备性能好,烧结温度低的陶瓷膜。此法制备工艺简单、生产成本低,是适合大规模生产的方法。
3.2.4 制备方法
无机陶瓷膜分离层的制备方法有多种。目前,应用较广的无机陶瓷膜分离层制备方法是:溶胶-凝胶法、固态粒子烧结法、阳极氧化法、化学气相沉积法。
分离层的制备方法应用于不同领域,同帜等以异丙醇铝、五水硝酸锆为前驱体,采用溶胶-凝胶法制备Al2O3-ZrO2复合薄膜表面平整光滑,热性能稳定,颗粒分布均匀、大小均一、结构致密、孔径分布窄,BJH中值为12.403257nm。郝艳霞等通过固态粒子烧结法以硝酸氧锆、硝酸钇为原料采用硬脂酸法制备3mol%钇稳定的氧化锆(YSZ)纳米粉体将所制备的纳米YSZ粉体分散后制备成稳定的悬浮液,通过浸浆成膜采用固态粒子烧结法制备YSZ膜,氮气吸附实验表明,YSZ膜的可几孔直径为87nm。牛冬梅通过阳极氧化法制备得到高度有序、性能优异的二氧化钛纳米管。吴慰采用激光化学气相沉积法在(100)取向Al2O3衬底上制备了第二代高温超导YBa2Cu3O7-δ(YBCO)薄膜。其中,溶胶凝胶法涂膜方式将涂膜液涂覆于多孔氧化铝陶瓷支撑体上在工业中比较常用。此方法主要是将金属醇盐加入有机溶剂中,在高速搅拌下其发生水解-缩聚反应形成溶胶,溶胶干燥后形成凝胶膜,支撑体和凝胶膜在高温焙烧条件下结合便形成陶瓷膜。
4 展望
无机陶瓷膜是高性能膜材料的重要组成部分,属于 大力发展的战略新兴产业,未来前景可观。要使得无机陶瓷膜拥有美好的发展前景,就必须突破低成本高性能无机陶瓷膜的生产技术,而质优价廉原材料的选取、支撑体制备、溶胶-凝胶制备、低温烧结等均是制备低成本高性能无机陶瓷膜的关键技术,这些技术的突破将会大大降低无机陶瓷膜的制备成本,从而使得无机陶瓷膜在各个领域得到广泛的应用。