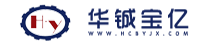
1 前言
炼油厂废水处理过程不可避免地产生大量的隔油池底泥、溶气浮选浮渣及剩余活性污泥等,它们统称为炼油厂“三泥”。这些污泥由不同含量的油、水及固体物组成,是高浓度的污染物,对环境具有极大的危害性。国内外广泛研究的“三泥”无害化处理技术,主要有焚烧、生物降解、溶剂萃取及送焦化处理等,然而这些技术在经济、技术及设备运行维护等方面均存在诸多不足。国内炼油厂一般采用浓缩-机械脱水-焚烧的方法处理含油污泥,焚烧每吨污泥的费用高达300~500元,并且设备故障率高。近年来,某些炼油厂将机械脱水后的污泥直接送入焦化装置,作为急冷油或作为急水使用。但这种方法具有一定的局限性,原因之一是污泥中仍含有大量水,易对焦化操作产生影响,焦化的处理能力低,不能将三泥全部处理掉;另外是某些炼油厂,或者焦化装置生产高品级石油焦,或者没有焦化装置,无法采用此法对污泥进行处理。多年来,国内一直没有一个技术与经济可行的处理手段,大多数企业仍采取将污泥转移给小企业进行处置的方式为主。由于环保法规的日趋严格,污泥处理成为企业环保达标的难题之一,严重制约着企业生产的发展。
针对三泥处理问题,抚顺石油化工研究院经过多年探索性研究工作,开发成功了“热萃取/脱水”处理技术。该技术从资源回收与环境保护的角度出发,在脱除污泥中水分的同时,将固体物全部转移至溶剂油中,使污泥在有价值组分得到了全部回收。萃取后的产物,因不含水分,既可以直接作为焦化的原料加以利用,同时也采用固液分离方式,进行处理。固液分离后的溶剂油,无需再生,可直接回用于“热萃取/脱水”装置。形成的固体物,其体积仅为原污泥量的一小部分,可采用多种途径加以利用,如按比例混入焦化原料中或采用轻溶剂洗脱,回收有和的组分;也可以作为燃料使用,其热值高达8452.1Cal/g。试验结果表明,该技术处理效果稳定、经济合理,与目前常规处理技术相比具有明显的优势。
2 “三泥”物性指标的分析
对于“三泥”中水分的分析,起初引用的方法是在105~110℃下的烘干法,而油含量的分析是以重量法为基础的。烘干法虽然能测出样品中的全部水分,但在测定过程中,不可避免地存在着有机质的挥发、分解,使测定结果失真。根据中石化环保监测总站建立的“石油化工厂废渣中含水率测定方法”、“石油化工厂废渣中含油量测定方法”、以及BG/T260-77,相应建立了“炼油厂三泥中水分的测定方法”、“炼油厂三泥中石油醚萃取物的测定方法”、以及“600℃固体物灼烧残渣的测定方法”等三个分析方法,作为污泥组成分析。其中含水率和石油醚萃取物均采用蒸馏法,比烘干法和重量法能更准确测定出“三泥”中的水和油含量。采用上述分析方法,对数家炼油厂的三泥组成进行了分析,结果如表1。
表1:不同炼油厂含油污泥组成分析结果
污泥来源 | 石油二厂 | 茂名石化 | 乌石化 | 上海炼油厂 |
含油率/% | 11.3 | 5.0~13.0 | 45.0 | 0.9 |
含水率/% | 84.4 | 80.0~90.0 | 43.9 | 95.9 |
600℃灼烧残渣/% | 1.1 | 2.0~4.0 | 7.6 | 2.1 |
从组成分析结果可知,由于污泥来源不同,其组成差别很大。另外,在分析中发现,每一种污泥的三项组分之和,并不等于百分之百,说明污泥组成上还存在着非石油醚萃取物、且在600℃灼烧下易挥发的物质,将其定义为“挥发性物质”。
3 试验内容及结果
3.1 烧杯试验
通过间歇式烧杯试验考察了“热萃取/脱水”技术的可行性,试验结果表明,在适当的操作条件下,该技术可完全脱出污泥中水分,并回收污泥中的油,处理后的固体物仅为原污泥的一小部分,并具有可利用价值。烧杯试验过程:
(1)将一定比例的萃取溶剂油及污泥置入蒸馏烧瓶。
(2)用电炉加热蒸馏瓶,使污泥中水分蒸发,同时记录馏出温度及蒸馏瓶液体温度。
(3)对蒸馏瓶蒸发出的水蒸气及轻质油蒸汽冷凝,收集并记录馏出水及油的体积。
(4)从蒸馏瓶中移出脱水后的固体与溶剂油的混合物。
(5)采用抽滤设备对混合物进行固液分离,并对固体物及溶剂油进行称重。
(6)分析脱出水中油含量及固体物组成等。
3.1.1 不同油/泥比的处理结果
表2:不同油/泥比对固体物组成的影响
溶剂油/污泥 | 固体物组成/% | |||
体积比 | 含油率 | 含水率 | 挥发性物质 | 灼烧残渣 |
0.25/1 | 26.1 | 64.1 | 3.0 | 6.8 |
0.5/1 | 30.9 | 62.4 | - | 8.5 |
0.75/1 | 48.2 | 14.8 | 11.3 | 25.7 |
1/1 | 52.3 | 未检出 | 24.5 | 23.1 |
2/1 | 53.0 | 未检出 | 24.0 | 23.0 |
固体物中水分随溶剂用量减少而增大。在油/泥比大于1的情况下,污泥脱水完全,固体物不含水,可燃性好。
3.1.2 溶剂循环使用的处理结果
在温度一定及油/泥比固定为1/1的条件下,考察了溶剂油直接循环使用的可行性。新鲜溶剂油为茂名公司沙中二线油(沸程范围约为212~320℃),处理对象分别为板框压滤后的“三泥”(组成:油含量13.5%,固含量6.0%,水含量80.5%)及浮选池浮渣(组成:油含量10.3%,固含量3.4%,水含量86.3%)。溶剂油循环使用10次过程中,脱出水中油含量平均为31.3mg,固体物组成及固体物产率的分析结果如表3及表4。
表3:溶剂油循环使用时的固体物组成
三泥来源 | 固体物组成 | 10次循环范围值 | 平均值 |
混合三泥 | 含油率/% | 56.7~64.3 | 61.2 |
含水率/% | 未检出 | 未检出 | |
挥发性物质/% | 10.1~15.7 | 13.2 | |
灼烧残渣/% | 23.6~27.6 | 25.2 |
表4:溶剂油循环使用时污泥产固率测定结果
项目 | 混合三泥产固率/% | 浮渣产固率/% |
十次试验范围值 | 12.8~17.6 | 7.0~8.1 |
平均值 | 15.2 | 7.6 |
无论是处理板框压滤后的“三泥”,还是浮选池表面采集的浮渣,溶剂油直接循环使用后,在处理效果上均未产生明显的变化,表明了该技术中所使用的溶剂无需频繁再生,可直接循环使用。形成的固体物均不含有水分,可燃性好,并且固体物量-污泥相比分别减少了85%和92%。
3.2 小试处理装置验证试验
3.2.1 工艺流程
根据烧杯试验结果及试验过程中确定的脱水温度、溶剂比、脱水速率等参数,设计了一套“热萃取/脱水”小试连续处理装置。污泥与溶剂油,首先在油浆罐内混合成具有一定流动性的混合物。该混合物经预热后,进入“热萃取/脱水”塔,并在塔内温度作用下,同时进行破乳、萃取和脱水三个过程。从“热萃取/脱水”塔出来的水及轻质溶剂油,经油水分离后,水排出系统,油返回油浆罐中。在水分脱出的同时,塔内的固体物及溶剂油混合物,不断地进入沉降罐进行固液分离。沉降后的固体物从装置中排出,溶剂油直接返回油浆罐中,进行下一次处理过程。
3.2.2 试验结果
小试装置试验过程中所使用的溶剂为粗柴油,循环使用15次,处理对象为采自茂名公司炼油厂的浮油,其组成为含油量9.28%、含水量87.59%、含固量为3.13%。
试验过程中对操作条件进行了考察并在较佳条件下进行了稳定性试验。试验结果验证了烧杯试验所得出结论:脱水完全彻底,溶剂油无需再生,可直接循环使用;沉降分离后的固体物中均未检出水,含油量平均值为65.9%,热值为8452.1 kCal/G;污泥产固率平均值为10.5%;脱除水含油量在10.0~28.8mg/L之间,水中COD为130mg/L。
3.3 固体物的处置
采用“热萃取/脱水”技术处理后,污泥中的油及固体物全部转移至溶剂油中,对于固体物的处置,可根据实际情况,采取如下几个途径加以利用。
固体物与溶剂油分离,直接作为焦化装置进料或急冷油,固体物转化为焦炭,这样做的缺点是,“热萃取/脱水”装置需要不断补充新鲜溶剂油。
固体物与溶剂油实施固液分离,对溶剂油进行循环使用。分离后的固体物,不仅体积非常少,而且具有较高的热值(8452.1Cal/g),采用如下方式很容易实现无害化处理。
(1)焦化原料混合送至焦化装置,形成有价值的产品。
(2)采用轻质溶剂洗涤或蒸汽吹脱方式,将残留的油提取出来,形成无害化固体。
(3)作为燃料使用,如炼油加热炉、热电厂其它加热燃烧设备的燃料。
4 技术特点与经济分析
4.1 技术特点
含油污泥中的水,不仅决定污泥体积的大小,同时也是影响污泥处理的关键。不同来源的污泥,污泥中的存在形式也是不同的。炼油厂“三泥”经加药与机械脱水后,含水量一般在80%~85%左右。其中水的存在形式,除少量为游离水外,大部分是以间隙水和内部结合水或附着水的形式,与固体物、油包裹在一起,并在固体物与油表面形成具有强烈憎油性的水化膜,常规的方法难以实现油、水及固体物的彻底分离。
“热萃取/脱水”技术,是一种控制水的溶剂萃取工艺,它不仅可以实现水与油及固体物的彻底分离,而且为污泥中有价值组分的全部回收与再利用打下良好的基础。该技术中,溶剂油既是萃取介质,同时也是稀释剂和传热介质。通过脱水,破坏污泥中油及固体表面的水化膜,消除亲水性界面对溶剂萃取的阻止作用,可以确保污泥充分地分散于溶剂中,增加油及固体与溶剂的接触机会。脱水与萃取同时进行,不仅可以提高萃取的传质效率,保证萃取效果的稳定性,而且形成的固体物难溶于水,很容易加以处理和利用。而单纯的溶剂萃取工艺,却无法克服油及固体表面水化膜的影响,污泥在溶剂中聚集成团,无法分散,萃取过程中易形成乳化液,特别是预脱水后的污泥。
与焚烧及单纯的溶剂萃取这两种典型的工艺相比,“热萃取/脱水”技术具有明显的优势。
(1)可以回收污泥中的油。
(2)溶剂用量低,无需频繁再生。
(3)处理效果稳定。
(4)产生的固体物不含有水,体积仅为原污泥的一小部分,并且可以通过多种途径加以利用,变废为宝。
4.2 经济分析
“热萃取/脱水”处理工艺的经济性,与待处理污泥中油及水的含量有直接关系。不同来源的含油污泥,其组成存在着很大的差异。经济估算以将不同组成的含油污泥彻底分离成油、水及固体三种独立的产生为基础,并与焚烧处理相比较。焚烧处理含油污泥的费用,在我国为300~500元/t污泥,在美国为500~1000美元/t污泥。
5 结论
“热萃取/脱水”处理技术,是一种 的炼油厂“三泥”无害化处理工艺,具有目前含油污泥常规处理技术无法比拟的技术和经济优势,该技术可以将污泥中水分完全脱出,并回收污泥中有价值组分,形成的固体物量仅为原污泥量的一小部分,且具有可利用价值。该工艺操作条件缓和,易于实现装置化,可广泛适用于石油开采及石油化工等行业的各种含油污泥处理,解决企业环保达标问题。