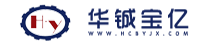
污泥脱水的目的是将污泥中15%~25%的水分分离出来,减小污泥体积以便降低处置难度。污泥与吸附水和毛细水之间存在结合力,实现固液分离必须克服这种结合力。应根据各种形式的结合力,制定有针对性的处理措施,以取得更好的脱水效果。研究表明,污水处理工艺选择的差异、脱水方式差异等都可能导致污泥脱水效果不同。
重庆某污水处理厂原有的带式浓缩一体机脱泥效率低,且污泥含水率偏高。该厂于2021年8月完成了离心脱水机改造工程,将带式浓缩一体机改为两台安德里茨离心脱水机。然而该厂污泥有机物含量较高,导致该设备负荷率偏低,调试运行期间发现离心脱水机药耗和电耗都偏高,需要进行运行管理的优化。
1 离心脱水机工作现状
1.1 离心脱水机结构及工作原理
差速系统、螺旋输送器、转鼓及控制系统等是离心脱水机的主要组成部分。其工作原理是污泥在高速旋转的离心力下,利用固体和液体的密度差实现固液分离。
1.2 影响离心脱水机脱水效果的因素
影响脱水效果的主要机械因素包括离心脱水机的转鼓转速、差速系统、控制系统等自身性能。同时,污泥龄、污泥浓度、污泥中有机物含量及丝状菌长度等污泥本身的特点都对污泥的脱水效果有影响。
1.2.1 机械因素
(1)转鼓转速。离心分离效果与脱水机的分离因素有关,分离因素与转鼓的转速有关,要想保证一定的离心效果,则转速越快,分离效果越好,越容易实现泥饼含固率提高的目标。但如果转速过快,将会对污泥絮凝体造成一定程度的破坏,从而对脱水效果产生极其不利的影响。另外,转鼓转速的加快会需要品质更好的材料,以避免高转速对机器的磨损。同时,高转速对动力的消耗也更大,机器运行时的噪声和震动也随之增大,所以需要将转鼓转速控制在合适的范围内,以降低该污水厂的运行能耗。
(2)速差。污泥泥饼干度、离心脱水机排渣能力、脱水滤液质量和速差大小有直接关系。速差大,则会导致沉渣脱水时间缩短,导致脱水后的泥饼含水率较高,同时澄清区的液体受到螺旋较大的扰动,降低了絮凝效果,滤液质量也随之下降。但是速差越大,固环层污泥越容易排出,意味着离心脱水机排渣能力随速差增大而提高。速差小,则会导致沉渣脱水时间加长,导致脱水后泥饼含水率有所降低,同时澄清区固体受螺旋的扰动较小,滤液质量也随之提高。但是速差越小,沉渣越容易堆积,厚度也会更大。
因此应结合厂区采购的离心脱水机结构参数、物料性质、运行单位的处理要求、污水厂污泥处理量大小等来确定速差的大小。结合离心脱水机性质,泥饼在干燥区脱水的时间如果过长,对出泥效果的提高并不明显,通常认为4~6s是泥饼在干燥区脱水较为合理的时间。
(3)液环层厚度。离心脱水机的干燥区长度及有效沉降容积均和液环层厚度有直接关系,可以通过拦液板的调节来实现对液环层厚度的控制。
液环层厚度增加,会导致沉降面积增大,物料在机内停留时间也会相应增加,滤液的质量就有所提高,泥饼含固率下降。反之,液环层厚度太薄,离心脱水机干燥区的长度增加,会导致滤液的含固量增大,使得分离液浑浊。
1.2.2 工艺因素
(1)絮凝剂。絮凝剂用量和浓度不足时,污水中的胶体和细小悬浮物难以聚集形成絮体,影响滤液质量。絮凝剂浓度太大时,活性基团紧密聚集,使得许多活性基团吸附效果减弱。如果絮凝体再次分散开,也会降低絮凝效果,因为分开絮凝体已经不够稳定,对提高处理效果没有明显的作用,还导致絮凝剂用量太大,造成了浪费,不符合污水厂节能降耗的运行目标。针对重庆某污水厂的节能降耗,应对絮凝剂投配比进行研究,确定适合该厂的投配比。
(2)污泥性质。实践表明污泥的性质会对卧螺离心脱水机的分离性能产生影响。
污泥絮凝体表面的菌胶团对污水中的有机物有较强的吸附性能,而污泥中的碳水化合物、脂肪、蛋白质等有机物对水分具有很强吸附性能,且在菌胶团表面的大分子胞外聚合物也对水分有较强的吸附性能,因此,降低污泥中蛋白质、碳水化合物、脂肪等有机物含量能够有效增强离心脱水机的泥水分离能力。
2 降低能耗试验结果分析
2.1 研究内容
结合上述对离心脱水机脱水效果影响因素的分析,确定从以下4个方面进行研究。
(1)不同进药量下的脱水效果研究。
(2)不同转速下的脱水效果研究。
(3)不同污泥浓度下的脱水效果。
(4)不同季节、不同温度下的脱水效果。
2.2 试验方案
拟采用控制变量法进行试验研究,具体方案如下。
(1)将每日絮凝剂使用量对剩余污泥处理量的比率定义为投配比。测定聚丙烯酰胺絮凝剂不同投配比下的污泥含水率,以此来确定絮凝剂的较佳配制浓度。
(2)在较佳絮凝剂配制浓度、平均污泥处理量下测定不同的离心脱水机转速2000~3100r/min的出泥含水率,以此来确定较佳转速。
(3)通过稀释或浓缩调整污泥浓度,在较佳絮凝剂配制浓度、较佳转速下,测定出泥含水率,以此评估污泥浓度对脱水效果的影响。
(4)收集日常污泥脱水时的室内温度,分析其与出泥含水率的关系,以此评估温度对脱水效果的影响。
2.3 试验结果分析
2.3.1 不同进药量下的脱水效果
在污泥浓度为4500~5000mg/L的条件下,测得污泥含水率投配比的关系。
随着投配比的增加,污泥含水率呈下降趋势。究其根本原因是随着投配比的增加,污泥原液的絮凝速度加快,絮凝体的紧密度增加,有效地提高了泥饼的含固率。当絮凝剂配制浓度过高时,絮凝剂和水完全混合所需时间很长,且达不到节省絮凝剂用量的目的。
较佳运行工况点应同时满足处理效果要求及投药量节约的双重目的,本次研究中取75g/m³左右。
2.3.2 不同转速下的脱水效果
通过观察重庆某污水厂的运行数据,当离心脱水机转速下降至2100r/min时,离心脱水机运行不稳定,振动和噪声较大。
为了观察出泥效果,本文通过固定离心脱水机转速,对离心脱水机差速、进泥污泥浓度、絮凝剂投配比、污泥处理量等运行参数进行调节,得到了污泥含水率与离心脱水机转速的关系。
要想有较好的出泥效果,离心脱水机转速应控制在2600~2900r/min。当取离心脱水机转速为2700r/min时,差速越小,污泥的脱水时间就越长,对澄清区的扰动就越小,所以降低差速可以提高污泥脱水效果。
2.3.3 污泥浓度对脱水效果的影响
当进泥浓度较高时,则需在单位时间内增加转鼓上的固环层厚度,同时提高差速将泥层推出转鼓,降低污泥在转鼓内的停留时间,增加污泥的含水率。
通过比较不同进泥浓度下离心脱水机脱水效果与分析污泥含水率与污泥浓度的关系可知,随着投药量的降低,系统的可靠性及稳定性也升高;随着进泥浓度升高,污泥产量明显升高。在实际运行过程中,如果要保持离心脱水机稳定高效地运行,进入离心脱水机的干污泥负荷需保持在承受范围的60%~100%。
2.3.4 不同温度对脱水效果的影响
根据实际运行情况,夏季运行的脱泥效果好,到了冬季,脱泥效果下降。污泥含水率与温度的关系如下表所示:
温度/℃ | 含水率/% |
5 | 84.00 |
10 | 81.70 |
15 | 80.60 |
25 | 78.90 |
30 | 78.80 |
35 | 78.65 |
40 | 78.50 |
当气温低于10℃时,离心脱水机的絮凝效果会变差,需要增加絮凝时间来改变脱泥效果;当温度在25℃以上时,混凝效果的影响可忽略不计。
上述分析表明,污泥脱水在冬季运行期间,收到低温的影响,活性污泥本身的微生物种群变化。污泥构成变化、絮凝剂的溶解性能,都会不利于污泥脱水。因此保持冬季污泥稳定生产的前提是确保生化系统内活性污泥的良好活性,应采取相应的加温或保温措施,以保证生产的稳定有序开展。
3 结语
通过研究不同工况条件下的离心脱水机运行效率,找到了较佳运行工况点,能够较大化利用离心脱水机,实现节能降耗的目标。
根据对重庆某污水厂污泥脱水系统絮凝剂投配比、转速差、进泥浓度及温度等试验观察,确定该厂污泥离心脱水机的较佳运行参数如下:污泥浓度为4500~5000mg/L(平均浓度)的条件下,聚丙烯酰胺絮凝剂投配比75g/m³、离心脱水机转速为2600~2800r/min,差速4~6r/min,能较稳定地实现出泥含水率为80%~82%的处理效果。但由于采用化验检测时虽然保证了准确性,但及时性差,对调试的指导意义有限,很难准确地将相关参数进行量化。
污泥脱水是较为复杂的一项工作,不同情况处理方式不同。需要厂区取样人员准确记录泥饼含水率、滤液含固量、泥饼的有机物含量以及脱水机絮凝剂投加位置及含量、转鼓转速、差速、转鼓扭矩、功率等相关运行参数;应结合相关运行数据以及更加科学的分析方法,进一步探索离心脱水机的较优工况,节能降耗。
此外,还可采用物理法和生物法等预处理调理技术进一步研究污泥深度脱水。