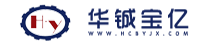
在化工、食品、医药许多工业方面,都涉及悬浮液中固体微粒和液相分离的工艺过程,这个过程无需进行任何化学反应,只需经过机械方法对固液两相进行分离,一般采用沉降分离方法来完成此项工作。例如滤除渣物提取果汁与油料、经过湿法粉磨的超微矿物粉料的脱水和淀粉加工等,都需考虑快速有效的固液分离技术。当前迅速发展的精细化学工业,为高价值地利用碳酸钙、高岭土、瓷土等非金属矿物资源,将矿粉经过湿法碾磨和分级,得到<2μm的微粒粉料,可以作为造纸面布涂料和 光学涂料,这样的粉浆是一种胶体颗粒悬浮液,要使这些微颗粒在重力场中沉降分离,固体颗粒的沉降速度极小,甚至微颗粒受布朗运动的作用,重力沉降几乎不可能。离心沉降则与重力沉降不同,从流体力学可知,颗粒在重力场中沉降,一方面颗粒受重力加速度作用而加速运动,另一方面又由于颗粒所受的液体阻力与其运动速度平方成正比,当阻力和重力达到平衡时,无外力作用情况下,颗粒只能以平衡时的线速度匀速运动,该速度称为颗粒的沉降速度。
国外在20世纪70年代就广泛应用离心沉降设备,使悬浮液处于离心力场中得到快速沉降,螺旋卸料转鼓式离心机就是近年来被认为理想的设备。
固液两相混合的悬浮液,通过输料管送入到转鼓的离心沉降腔内,悬浮液被离心力作用在腔内紧贴转鼓壁形成一定厚度的液环,而液环中的固相微粒,在离心力场作用下迅速向鼓壁沉降,在内壁形成固相物的密集层,不断供入悬浮液体,并继续发生离心沉降过程,固相物依附鼓壁,料层不断增厚,被螺旋卸料器推向转鼓锥形段端侧,而内层澄清液向圆筒形转鼓段的端侧溢出,从而达到了两相分离的目的。实际上,当离心机的分离因数达到相当高的程度,对于不同密度的两种不互溶液体的混合液,亦可进行分离。
为了使很小粒径的固体颗粒得到快速沉降,离心机必须造成足够的离心力场将微颗粒强迫沉降,而所需的离心力则依靠离心机的转鼓的高转速产生,由此可见,转鼓的高转速,仅仅标志其对悬浮液分离难度的有效性,离心机更重要的性能要求,还要把沉降下来的固相物有效地收集,在分离过程中,使超细颗粒不被澄清液带走,而且使收集的固相物的含湿量尽可能低。这就要求卸料装置(螺旋卸料器)的转速和转鼓转速的合理配置。这些技术问题,就有赖于其驱动装置——差速器的合理设计。
美国、德国、英国、瑞士、日本等 的螺旋离心机所采用的驱动装置为齿轮行星差速器,其转鼓转速高达5000r/min以上,分离因数(离心加速度与重力加速度之比),可达6000以上,转鼓与螺旋卸料器的转差率为0.3~4%,对固液密度差>0.05g/cm³的悬浮液分离,收得的粒径>2μm的渣料含湿量低于20%,而且这种离心机的分离效果对进料固相浓度变化不敏感。我国自80年代引进国外装备,不断消化吸收国外技术,陆续设计和生产出多种机型的同类离心机,如WL系列离心机,是目前生产较成熟的产品,但其分离因数一般在500~2400范围,大多采用摆线针轮式差速器。由于转速不高,分离因数值小,其所能达到分离的效果,也只能对界限粒度>10μm的密度较大的固相颗粒进行比较有效的分离。而当前一些工业应用要求对<2μm以下的颗粒进行沉降收集,要改进离心机的性能,技术关键在于提高转鼓的转速,以提高分离因数,由此,作为驱动装置的差速传动装置也由于提高主传动转速而需要考虑以下问题。
(1)要求很小的回转半径,很小的回转质量,和很高的动平衡精度。
(2)由于转鼓转速很高,卸料速度仍需保持在一定范围内,也即使辅传动和主传动输出很小的转速差,则行星机构的传动比应很大。若主传动转速为5500r/min,卸料辅传动转速差为2r/min,则转差率为0.036%,若输入转速差为100r/min,则要求行星机构的传动比>50,实际需要还更大,只有加大传动比,才能准确控制输出的转速差。
(3)保证辅传动提供螺旋卸料器足够的工作扭矩,可能还出现随机的过载情况,同时由于尺寸限制,齿轮机构设计的承载能力安全储备小,所以需要带有扭矩离合器,以保安全。
(4)行星机构很紧凑地封装在圆柱型外壳内,内部装载的润滑油也类同于转鼓内的被分离的液体,在强大的离心力场作用下对壳壁产生很大的离心压力,外壳要有可靠的密封,防止漏油。
目前的大部分离心机上所采用的差速器为摆线针轮行星机构,实际上,摆线针轮传动机构存在着结构性的致命弱点,因为摆线针轮传动是依靠少齿差行星传动方式得到较大传动比的,较大质量的摆线轮的重心偏置,虽然与针齿轮的中心距不大,而且采用成对设计,但其重心偏置,沿轴向相距一个摆线轮厚度,在轴向上的偏心质量,将在高转速下产生进动不平衡力矩。仍不能满足高转速情况下的动平衡要求,要达到离心机的分离因数>6000时,一般转鼓转速要达到5000r/min以上,这个转速对转子体是过临界转速,一般要求差速器的动平衡精度达到G2.5级,由此则要求差速器在此转速下的动不平衡矩必须小于12.5~20g·cm。这样的精度要求,对于摆线针轮行星差速器,既无法达到,也无法校整。
对于上述螺旋卸料式离心机的改进要求,设计了NC系列的齿轮行星差速器,在较多的主机上配套,达到了较好效果,以下作简要介绍。
1 NC系列齿轮行星差速器的结构原理
NC型齿轮行星差速器由两级NGW行星齿轮机构组成,内齿圈B1、B2连接的外壳和离心机转鼓固连,并与主传动皮带轮连接,输入主传动转速。输出轴以花键轴头和离心机的螺旋卸料器轴连接,一级中心轮由辅传动皮带轮通过扭矩离合器和输入轴输入辅传动转速,由行星轮架(系杆)自带的二级中心轮耦合到第二级行星传动机构,进一步减速输出。
设计考虑了输出转速差<2r/min的情况,行星机构的传动比设计为35,57,93和159几个公称传动比,当传动比大时,由于中心轮直径很小,行星轮个数受邻接条件限制,因此传动比>57的情况,可采用2个行星轮,而其它采用3个行星轮结构。
行星机构还有一个显著的优点,可以根据实际需要,很方便地改变各级齿轮的配齿方案,得到所需的各种传动比。
2 差速器额定输出转矩的确定
差速器额定输出转矩是决定差速器能够提供离心机螺旋卸料器满足完成一定产量的排料能力的参数,确定了这参数值后,才能对差速器各级行星机构作准确的设计。所需的输出转矩决定于所配主机的工作能力。要确定这个参数,必须根据转鼓和卸料器的结构特点,螺旋卸料器叶片方向有垂直于鼓壁母线和垂直于回转轴线两种结构。为便于叙述,设转鼓为锥形,半锥角为α,将圆柱形鼓壁部分作为α=0的特例,其计算方法一致。
差速器的额定输出转矩决定于以下计算结构。
2.1 对于螺旋叶片垂直于转鼓回转轴线情况
(1)克服沉降物离心力沿转鼓母线分力所需的转矩。
(2)克服沉降物与转鼓壁摩擦力所需的转矩。
(3)克服沉降物和螺旋杆摩擦力所需的转矩。
2.2 螺旋叶片垂直于转鼓锥段母线情况
(1)克服沉降物产生的离心力沿转鼓圆锥母线方向的分力所需转矩同2.1中(1)的计算。
(2)克服沉降物与转鼓壁摩擦力所需的扭矩。
(3)克服沉降物和螺旋杆摩擦力所需的扭矩。
差速器输出的工作扭矩为三项之和。
3 NC系列行星齿轮差速器的基本参数
NC系列行星齿轮差速器在国内生产的LW、WL各种型式离心机上配套应用,经过长期运转考验,达到了较好效果。可配用的转鼓直径在180~800mm范围,转鼓转速3500~5500r/min,输出差转速为2~80r/min,所配离心机的分离因数可达到4400~5500左右,具体性能参数如表1。表2列出未改进前WL系列离心机所能达到的分离因数指标值。
表1:NC系列行星齿轮差速器的基本参数
型号 | NC1 | NC2 | NC3 | NC4 |
公称传动比 | 35,57,96 | 57,93,159 | 57,93 | 57,96 |
额定输出扭矩/(N·m) | 1400 | 2300 | 3300 | 4200 |
主要尺寸/mm L0 | 340 | 390 | 390 | 420 |
主要尺寸/mm L1 | 200 | 205 | 205 | 220 |
主要尺寸/mm D0 | 225 | 265 | 285 | 350 |
转鼓直径/mm | ≤260 | ≤360 | ≤500 | ≤800 |
驱动功率/kW | 2.2~4 | 3~5.5 | 4~7.5 | 5.5~11 |
转速/(r/min) | 5500 | 4500 | 4000 | 3500 |
可达到分离因数 | 4400 | 4078 | 4475 | 5482 |
表2:未改进前WL系列离心机所能达到的分离因数
型号 | WL-200 | WL-350 | WL-400 | WL-600 | WL-630 |
分离因数 | 2260 | 2390 | 1880~2360 | 1470 | 1400~1700 |
由数据比较可知,采用NC行星齿轮差速器提高了离心机转速,从而提高了分离因数。