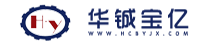
近年来,随着工业化进程的加快和经济的迅猛发展,污泥处理问题日益突出。
污泥脱水处理是城市生活污水、水厂排泥水、工农业废水处理工艺中的重要环节,经浓缩脱水后的污泥,体积大为减小,不但减轻了对环境的二次污染,也为污泥资源的综合利用创造极为有利条件。卧式螺旋卸料沉降离心机(以下简称卧螺机或离心机),因其分离后固、液分离效果好、脱水后泥饼含水率低、自动化程度高、操作环境好、处理量大等优点而备受水处理行业青睐。根据离心机的使用情况,结合调试和国内污水处理行业的使用经验,就污泥处理行业中影响离心机分离效果的因素作以下探讨。
首先必须知道卧螺离心机的结构及分离原理:卧螺离心机主要由转鼓、螺旋、差速系统、进料系统、驱动系统以及控制系统等组成。
离心机是利用固、液两相的密度差,在离心力的作用下,加快固相颗粒的沉降速度来实现固液分离的。具体分离过程是为待处理的污泥经进料管连续加入离心机时,由螺旋芯管处的分料装置送入转鼓混合腔,由于转子(螺旋和转鼓)的高速旋转和摩擦阻力,料液在转子内部被加速并形成一个圆柱状液环层;在离心力作用下密度较大固体颗粒沉降到转鼓内壁,固相被螺旋推送到转鼓锥端的干燥区进一步脱水,然后经出渣口排出,液相形成一个环,环形液层深度是通过转鼓大端的溢流调节片来调节的,分离后的液相经溢流孔排出,渣和分离液分别被收集到机壳内,然后由重力卸出机外,实现污泥的浓缩脱水。
其次是对影响离心机的效果因素作深一步的探究。
1 影响离心机效果的因素
影响离心机处理效果因素分为两大类:不可调节的机械因素和可调节机械因素。
不可调节机械因素主要包括:转鼓直径和有效长度、转鼓半锥角、螺距、螺旋类型、差速器类型等方面;可调节因素:转鼓转速、差转速、液池深度、污泥处理工艺等因素。
2 不可调节的机械因素
2.1 转鼓直径和有效长度
转鼓直径越大和有效长度越长,其有效沉降面积越大,污泥处理能力越大,物料在转鼓内停留时间越长,且在相同转速下,其分离因数就越大,分离效果越好;但受到材质和制造水平限制,离心机转鼓直径不可能无限地增大,因为随着直径的增加,可允许的速度会由于材料坚固性降低而降低,并且转动惯量增大,振动烈度相应增大,使得动平衡性变差,从而使离心力也相应降低。通常在污水处理上所用离心机转鼓直径为350~900mm,长径比L/D为2.5~4.5为宜。
另外,相同处理量情况下,大转鼓直径离心机可以较低的速差进行。由于大转鼓直径的螺旋输渣能力较大,要达到相同的输渣能力,小转鼓直径的离心机必须提高速差来实现。
通常因固相物料的高速摩擦和腐蚀卧螺离心机锥转鼓的固相出渣口,装有耐磨材料,制成便于更换的耐磨套。固相出渣口是径向出渣,出渣孔的大小既要减少排渣阻力,避免固渣卡死在转鼓内,又要考虑转鼓锥段强度,出渣孔的个数一般为6~12个,出渣孔的断面面积在强度允许条件下,一般都开得较大。
为了有效保护卧螺机的转鼓,除在出渣孔设耐磨套外,在转鼓内表面设置筋条或在内表面拉槽,可防止沉降在转鼓内壁的固相物与转鼓的相对运动而产生磨损。设置筋条与拉槽相比,前者不但更有利于防止沉渣滑移,而且可减少沉渣对转鼓内表面造成的磨损,制造也方便,所以大多数卧螺离心机转鼓内部采用设置筋条的方法。筋条一般宽为15~20mm,厚为2~3mm,数量为8~24块,并且用间接焊接方式焊在转鼓内表面上,可有效减少转鼓磨损,延长转鼓的正常使用时间。
2.2 转鼓半锥角
沉降在离心机转鼓内侧的固形物被沿转鼓锥端推向出料口,由于离心力的作用,受到下滑移的回流力作用。半锥角越大,固形物受离心力挤压越大,螺旋推力的扭矩越大,叶片磨损越大,甚至产生固形物回流现象,而导致螺旋推料器无法排渣。如果半锥角小,其有效沉降面积将大为减小,进而降低离心机的使用性能。液池深度一定时,锥角大,干燥区长度(即污泥脱离液面到排渣口之间的距离)短,其脱水时间便短,固渣含液量高,但其沉降区长度大,沉降面积增大,分离液含固形物少,质量相对好些。反之,如果锥角小,则干燥区长度大,脱水时间长,固形物的含液率就低,分离液的质量也差些。
从以上分析可知,转鼓半锥角是离心机设计中较为重要的参数。从澄清效果来讲,要求锥角尽可能大些;而从输渣和分离效果来讲,要求锥角尽可能小些。由于输渣是离心机正常工作的必要条件,因此设计必须首先满足输渣条件。对于难分离的物料,半锥角一般在5~15°内,以便降低沉渣回流速度。对污泥的分离,半锥角在8~20°以内就能保证固形物顺利输送,又能使分离液质量好。
2.3 螺距
螺距即相邻两螺旋叶片的间距,是一项很重要的结构参数,直接影响输渣的成败。在螺旋直径一定时,螺距越大,螺旋升角越大,物料在螺旋叶片间堵塞的机会也越大,同时,大螺距会减少螺旋叶片的圈数致使转鼓锥端物料分布不均匀而引起机器振动加大,因此对于难分离的物料,输渣较困难。螺距小些一般为转鼓直径的1/4~1/6有利于输送。对于易分离物料,螺距大些,一般为转鼓直径的1/3~1/5,以提高沉渣的输送能力。
2.4 螺旋类型
螺旋是离心机的主要构件,它的作用是输送沉降在转鼓内侧的固体和顺利排掉固体,它不仅是卸料装置,也是决定设备的生产能力,使用寿命和分离效果。螺旋的类型根据液体和固体在转鼓内相对移动的方式不同,分为逆流式和顺流式。逆流式离心机的加料腔在螺旋中部,也就是位于干燥区和沉淀区之间的边界附近,以保证液相有足够的沉降距离,分离后固体泥渣向转鼓小端推动,直至排出。分离液向转鼓大端运动,从柱锥形转鼓大端排出。它是卧螺离心机的基本形式,应用范围广,适应性强,能用于固相脱水,液相澄清,粒度分级等分离过程。污泥处理多选用此种机型。顺流式离心机由于进料口在转鼓端部,避免逆流式的湍流,保证固形物沉淀不受干扰,离心机全长起沉降作用,扩大沉降面积,悬浮液在机内停留时间增长,从而使分离效果提高。顺流式离心机特别适用于固液密度差小,固相沉降性能差,固相含量低的难分离物料,多用于液相澄清,应用范围窄,进料悬浮液含固量不能太高,否则排液管易堵塞,需定期冲洗。
螺旋在推料过程中,螺旋输送器的叶片,特别是锥段部分,易受到某些物料的磨损。为了减少和避免螺旋片的磨损,对柱锥状螺旋叶片的推料面进行硬化处理,如喷涂高硬度的合金或焊接合金块或采用可更换的扇形耐磨片,耐磨片的材料可根据不同物料及工况所确定。对有严重磨损又有腐蚀的物料需选用耐磨又耐蚀的特殊材料,以确保设备长期无故障运行,并减少设备的维修费用。
目前,高效型螺旋结构在污泥处理中效果显著。即在离心机锥端的螺旋出料端设置一个特殊的挡板,可使卧螺离心机处于超深度池状态,增加对固相的压榨力,并且只输送下部固体,而将上部含液高的固体留在压榨锥段外侧,实现压榨脱液,使出渣更干,清液中含固体更高。
污泥分离中BD板的 性体现在:更大的进料量;更长的澄清段;上清液更清;减少了物料被搅乱的机会;排出的固渣更干。
经过调试和各污水厂的运行情况得出BD板在污泥处理上的优缺点如下:
(1)液池深度加深,固形物在转鼓中澄清时间长,出液更清。
(2)有机固形物可进一步的压缩,使出渣更干。
(3)在处理量相同时,固形有机物回收率更高。
(4) 缺点是固形物中无机物占绝大部分,其比重又较大,且不可压缩,在转鼓及差速及进料量不匹配的状况下,偶尔出现堵塞转鼓的现象。但毕竟瑕不掩瑜。
随着电脑的应用可以将离心机螺旋推料器、叶片倾角、螺距、叶片间距、转鼓长径比、转鼓直径、半锥角等参数经过优化设计后,经过电脑仿真模拟处理来确定不同物料的处理量和分离的效果,得出较佳参数值,缩短设备调试时间,节省人力、物力,并提高实际生产中处理能力和生产质量。
2.5 差速器
卧螺离心机中,沉渣在转鼓内表面的轴向移动都是靠螺旋与转鼓之间的相对运动即转速差来实现的,而转速差是靠差速器来调节的。差速器是卧螺离心机中复杂、重要的部件,其性能高低、制造质量等决定了整台卧螺离心机能否正常可行的运行。
差速器的结构形式很多,有机械式、液压式、电磁式等,因液压式差速器液压元件多、回路多、制造复杂,特别是回油路易泄漏,卫生状况差,在污泥处理中处于被淘汰的边缘。而电磁式传递扭矩小,不适合高转速、大处理量、大扭矩的要求,也逐渐被淘汰。常用的是机械行星齿轮传动差速器。机械行星齿轮差速器又分为圆弧摆线针轮差速器、渐开线圆柱齿轮差速器、谐波齿轮传动差速器等。渐开线圆柱齿轮不但结构紧凑、体积小、承载能力高,且传递效率高达99.8%,所以凡传递扭矩大于3000N·M以上的差速器,大多采用渐开线圆柱齿轮差速器。
因摆线针轮传递效率稍低,以及承载能力较小的原因,目前一般都只在转鼓直径为Φ400mm以下规格的离心机中使用。
3 可调节的机械因素
3.1 转鼓转速
分离因数与转鼓转速的平方正正比,转速越高,分离因数越大,离心机的分离效果将越好。同时较高的转速对材料的要求高,机器的磨损增大,动力消耗、振动及噪音都相应增加。目前一般在污泥处理中选用转速:如当转鼓直径=450mm,长径比=3.0~4.5时,无论从处理流量和分离效果来看,转速为3000~3800rpm为较佳值。
3.2 速差
速差直径影响排渣能力,出渣干度和分离液的固形物含量。提高速差,有利于提高排渣能力,但泥渣脱水时间缩短,分离后出渣含液率大,同时螺旋对澄清区液池的扰动大,分离液的清度相对差一些。降低速差,固形物厚度加大,泥渣脱水时间增长,分离后泥渣含液率就降低,分离液清度也相对好些,但会增大螺旋推料负荷,增大推料的扭矩,应防止排渣量减小而造成离心机内泥渣不能及时排出引起的堵料现象,否则易使分离液中含大量泥渣,这时必须减小进料量,或提高速差。因此,应根据物料性质、处理量大小、处理的其他具体要求及离心机结构参数来综合确定速差大小,这就是离心机现场调试的必要性。随着离心机控制中变频器的广泛应用,通过调节频率Hz来控制电机或马达的转速,来间接调节速差,速差调节越来越方便。
3.3 液池浓度
液池深度是工艺优化的一个重要参数,直接影响离心机的有效沉降容积和干燥区长度,进而影响离心机处理效果。转鼓内液池浓度的深浅靠大端轴颈上的溢流调节片来调节。液池深度深时,沉降面积增大,物料在转鼓内停留时间也相应增加,离心机的澄清效果好,处理量也大。但同时转鼓内的干燥区长度缩短,导致分离液含渣量升高。相反,减少液池深度时可获得较高的出渣干度,但要以牺牲分离液质量为代价。因此根据污泥处理不同工艺的要求,合理地调节液位调节片的高低,达到泥渣干度与分离液质量较佳组合。可加工多组,根据变化来现场调节液池深度。
3.4 主轴承润滑
高速重载离心机的主轴承发热比较严重,当被分离的物料温度高达50~100℃时,螺旋和转鼓传递给主轴承的热量较高,再者是高转速时摩擦生热,从主轴承的要求和使用来看,也确实这样,所以主轴承的润滑十分重要。为此,有些卧螺离心机的主轴承采用油润滑,不断带走主轴承热量,并控制润滑油的温度,确保润滑油的粘度值,保证轴承良好运行。此外,一些卧螺离心机选用润滑性能良好的耐温较高的润滑脂来润滑主轴承。但不管是稀油循环润滑还是油脂润滑,油品的性能对润滑效果影响都十分明显,作为污泥处理的企业必须严格按离心机制造厂家提供的规格牌号选用润滑油或润滑脂,才能保证主轴承的长期、高效工作。
4 结语
污泥处理时,影响离心机分离效果的因素很多,并且各个因素又相互影响,交叉立体作用,因此蛋白分离效果是以上所述各个因素综合作用的结果。既然污泥处理与人民生活息息相关,污水处理的质与量问题日益严重,离心机选型问题就要迫切解决。离心机的选型必须综合污水处理工程项目的实际情况,运行参数要求,从分离后污泥处理的工艺。所要求的较佳出渣干度,固体回收率,还是分离液高清度,并结合国内外各厂家各种卧螺离心机的使用性能和经济成本综合考虑。