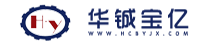
石化行业的原油储罐,每隔5年左右需清罐一次,即使经过二次蒸馏拔油处理,底层含油污泥的量至少仍占其储存容量的1%以上,再加上浮渣泥与落地泥,数量十分可观,而这种污泥中含有大量的苯系物、酚类等恶臭有毒物质,不能直接排放,处理不当还会造成二次污染。因为其巨大的危害,20世纪90年代以后,一些发达 除了对含油污泥实行严格的法规,还深入研究了其处理处置技术。总体来讲,含油污泥的生物处理技术处理周期长,工艺条件苛刻,物化处理技术简单,国内外学者研究较多,目前各油田对含油污泥初步处理采用药剂法较多。药剂法能回收油泥中的油,但药剂法处理后含水率高的油泥已成为该方法的遗留问题。本实验主要研究药剂法除油后的罐底泥泥渣与浮渣油泥混合,离心处理制成泥饼的优化条件,以脱水率为指标,确定达到较佳分离效果时的操作条件。
1 实验部分
1.1 实验原料及试剂
实验原料:某油田罐底泥和该油田污水处理厂的浮渣油泥,采样时间2012年8月和2013年4月,油泥理化性质如表1所示。
表1:某油田罐底泥和浮渣油泥
油泥 | 罐底泥 | 浮渣油泥 |
颜色 | 黑色 | 黑色 |
嗅味 | 恶臭 | 恶臭 |
含水率/% | 60~85 | 45~70 |
含油率/% | 10~30 | 6~11 |
w(杂质)/% | 5~10 | 15~40 |
p(20℃)/(g/m³) | 0.75~1.20 | 0.98~1.70 |
实验试剂:十二烷基苯磺酸钠,分析纯;碳酸钠,分析纯;聚丙烯酰胺。
1.2 实验设备
电热恒温鼓风干燥箱;电子天平;恒温水浴锅;离心机。
1.3 实验步骤
预处理是将罐底泥用复配化学药剂进行处理,静止分层回收浮油,得到处理后的泥渣与含有药剂的废水。具体方法如下:按照配方向罐底泥中依次投加十二烷基苯磺酸钠(4g/L),碳酸钠(1g/L),聚丙烯酰胺(30mg/L),其中药剂体积比为1:2:1,药剂与污泥液固质量比为6:1。50℃水浴条件下,搅拌20min,自然静置分层,除浮油,得到处理后的罐底泥的泥层(泥渣)与废水层(离心助剂)。以罐底泥的泥渣为实验对象。
将泥渣掺入一定量的浮渣油泥,适当搅拌后,离心处理,处理后的水可作为油田回注水,残渣可用于制煤。离心处理中考察以下影响因素:离心时间、离心速度、泥渣和浮渣油泥质量比、处理量和离心助剂用量。其中,离心助剂为化学药剂法处理后的含有药剂的废水(废水中含有十二烷基苯磺酸钠、碳酸钠、聚丙烯酰胺),加入离心助剂目的是加速含油污泥的破乳分层。其中,含水率的测定方法如下:
(1)取小坩埚若干个,放入温度为105℃的烘箱中,烘干1h后取出,放入干燥器中降至室温称重(ma)。
(2)分别称取5g左右处理后的泥渣或浮渣泥(mb)放入小坩埚中,放入105℃的烘箱中,烘干4h后取出,放入干燥器中降至室温后称重(mc)。
计算含油污泥的含水率公式如下:
W=[mb-(mc-ma)]/mb×100%
式中,ma为坩埚质量,g;mb为未处理污泥样品质量,g;mc为烘干后污泥样品和坩埚质量,g。
混合泥脱水率ξ计算公式如下:
ξ=(m0+m1+m2-m3)/(m1×W1+m2×W2)×100%
式中,m0为坩埚质量,g;m1为处理后的泥渣质量,g;m2为浮渣泥质量,g;m3为离心后混合泥与坩埚总质量,g;W1为处理后的泥渣含水率,%;W2为浮渣泥含水率,%。
2 结果与讨论
2.1 离心时间的考察
浮渣油泥和处理过的含油污泥泥渣各称取2.5g,混合后加入5mL离心助剂,为使离心助剂和含油污泥混合充分,连续搅拌5min后,倒入离心管中,离心转速3500r/min,污泥离心时间分别为10、15、20、25、30min,在不同的离心时间下处理含油污泥,做出离心时间-脱水率曲线,分析得出较佳离心时间。调质-离心技术能够提高含油污泥的脱水率,这是因为污泥颗粒上的水滴的附着力小于其做圆周运动的向心力,离心因此起到了泥水分离的作用。一般来说,离心时间越长,油、水、泥三相在离心力的作用下分离的越充分,离心时间从10min延长到20min,脱水率从50.72%增加到78.00%,离心时间为20min时脱水量达到峰值(脱水率78.00%),达到峰值后脱水率随离心时间延长增加并不明显。因此,较佳离心时间为20min。
2.2 离心转速的考察
设定离心转速分别为2000、2500、3000、3500、4000r/min,在不同转速下处理含油污泥。离心转速由2000r/min增加到3000r/min时,脱水率从49.86%增加到83.33%,根据Stock公式,当离心速度增大时,沉降速度也随之增加,从而使分离效果增强。随离心速度增加,脱水率达到极值后基本保持不变。综合考虑,某油田污泥在实验室小试时,较佳离心转速为3000r/min。
2.3 离心助剂加入量的考察
对两次取样的某油泥进行测定,密度分别为0.75g/cm³和1.2g/cm³,自然状态下的含油污泥状态稳定,类似于胶体物质。药剂法处理时油泥中加入的复配药剂中含有絮凝剂,离心分离出来的水层就含有絮凝剂,实验将其作为分离的助剂加入离心油泥中,目的是促进油泥絮凝固体的形成,利于离心分离,同时可以节约药剂用量。离心助剂的加入体积分别为4、6、8、10、12mL。
离心助剂加入量从4mL增加到8mL时,脱水率从46.42%增加到86.04%,这是因为,离心助剂量增加,对污泥颗粒的絮凝作用增强,污泥颗粒粒径增大。根据Stock公式,可知污泥颗粒粒径增大,沉降分离效果提高。离心助剂加入体积由8mL增加到12mL,脱水率的增加幅度在2%~3%,考虑到投入离心助剂量的增加同时增加能耗,因此,较佳离心助剂加入量为10mL。
2.4 前处理对离心的影响
离心前的搅拌处理属于调质,在不同的搅拌时间3、5、7、9、11min时,测定含油污泥脱水率。搅拌前处理能够提高含油污泥的脱水率,搅拌3min时,含油污泥脱水率仅为40.52%,搅拌时间延长到5min以上,脱水率能提高30%~40%,而且离心前处理搅拌时间越长,搅拌越充分,药剂与油泥接触越彻底,污泥颗粒的絮凝作用越强,从而使污泥颗粒粒径增大。另外,搅拌可以加速含油污泥表面泥沙的脱落,有利于油滴从含油污泥中分离,实验证明含油率为10.08%的罐底油泥和浮渣油泥经离心处理后含油率为5.24%。综合考虑,离心前的搅拌处理时间为9min。
2.5 处理量的考察
浮渣泥和处理过的含油污泥泥渣按质量比1:1混合,然后分别取2、4、6、8、10g混合后的污泥处理。对于小型实验用的离心机(分离因数1960)来说,处理量在2~4g时,脱水率在88.11%~87.54%;但当处理量由4g增加到10g,脱水率迅速降低至49.93%。由此可见,进行工程试验时,为了获得较好的脱水效果,需要进行处理能力的考察。另外,离心机的处理量增大也会增加电力消耗。综合考虑,对应小型实验用的离心机来说,处理量选为4g。
2.6 泥渣与浮渣泥配比对脱水率的影响
加入离心助剂处理后随泥渣的比例增加,脱水率随之增加,这是因为处理后泥渣中还有一定量的药剂。实验不考察浮渣泥的脱油率,因为相对罐底泥来说,浮渣泥含油率较低,脱水后的污泥将制作型煤,留有一定量的油可以提高煤的热值。因此,综合考虑,药剂法处理后的泥渣与浮渣泥质量比为4:1,此时脱水率达到92.17%。
3 结论
处理后的罐底泥泥渣含水率86.84%,浮渣泥含水率52.37%。将处理后的罐底泥泥渣掺入一定量的浮渣泥,离心助剂采用药剂法分离出来的上层液,适当进行搅拌后,离心处理,离心较佳工艺条件:加入离心助剂量为10mL,预处理搅拌时间为9min,离心处理量为4g,罐底泥处理后泥渣与浮渣泥质量比为4:1,离心时间为20min,离心转速为3000r/min。在此较佳工艺条件下,脱水率可达92.17%。