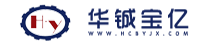
碟式植物油分离机具有体积小生产能力大、连续分离、分离效率高、分离效果好、能耗低、精炼率高、操作简单及劳动强度小等优点,被广泛应用在植物油精炼的脱胶、脱皂、脱蜡等工艺中,是精炼系统中的核心设备。但在实际使用中,由于对其工作原理,转鼓的结构不甚了解,以及操作不当和工艺参数的选择,分离机经常出现跑油、分离不清、油(皂)脚含油过高等情况,给生产造成不必要的损失。处理这些问题,须先了解分离机的工作原理和转鼓结构。本文用故障树分析法对导致分离性能故障的各基本事件及其相互关系进行了分析,以此指导操作者分析故障原因,消除或避免故障。
1 工作原理
被分离物料是在转鼓内碟片组之间完成的。待处理的油料从转鼓中央进液管进入碟片薄层空间内,由于转鼓高速回转产生离心力场,使油料中不同密度的油品(轻液相)、杂质(固相)、油(皂)脚、污水(重液相)获得不同的离心力,轻液相和重液相达到平衡时,则形成一筒状的分界面,固体杂质通过重液相和水封层积聚在转鼓内壁上,重液相和轻液相分别由各自通道被向心泵排出机外。
碟片间的粒子在离心力和流体的冲力同时作用下,向上端移动到达碟片内锥面,并沿碟片内锥面向下滑出碟片移向转鼓内壁。如果粒子在分离时路程短或粒子质量过小不能到达碟片内锥面则粒子将被液流夹带而不能被有效地分离出去。
2 转鼓结构
转鼓是分离机的重要部件,待分离的油料是通过高速回转的转鼓来完成的。同时转鼓上还设有排渣机构,可定期将聚在转鼓内壁的杂质排出机外。
3 故障分析
故障树分析(Fault Tree Analysis-FTA)是把系统或子系统发生的故障状态作为逻辑分析的目标,按事件发生的逆顺序,逐层次进行分析因果关系,至下找出导致这一故障发生的所有直接原因,直至基本的故障事件,把全部故障状态按层次根据相互逻辑关系,相应的逻辑符号联系起来形成树形逻辑图。
把分离机分离性能故障作为顶事件,导致顶事件发生的直接原因为中间事件,顶事件与中间事件用矩形框表示,中间事件与顶事件为逻辑或门关系。逻辑或门是任何一种中间事件发生都将导致顶事件发生。再对中间事件分别向下分析,直至找出导致中间事件产生的全部小割集。
标识 | 含义 | 标识 | 含义 | 标识 | 含义 |
TOP | 分离性能故障 | 3 | 分离温度太低 | 20 | 重液向心泵排出不畅 |
G1 | 油中含有过量的油(皂)脚 | 4 | 加入的冲洗水量太大 | 21 | 排渣间隔时间过长 |
G2 | 油(皂)脚中含有过量的油 | 5 | 转鼓内碟片间积渣 | 22 | 未定期清洗转鼓 |
G3 | 排出的渣中含有过量的油 | 6 | 进油量不稳定 | 23 | 搅拌太强烈 |
G4 | 处理量达不到额定标准 | 7 | 比重环口径过大 | 24 | 水温过低 |
G5 | 转鼓内积渣 | 8 | 油出口背压过高或堵塞 | 25 | 输送泵的型号选择不当 |
G6 | 工艺系统中油(皂)形成不好 | 9 | 酸价过高或油酸败 | 26 | 安装不正确 |
G7 | 重液相(油脚、水)出口不畅 | 10 | 毛油中含渣或含土量过大 | 27 | 连接处密封圈破损 |
G8 | 转鼓内渣腔充满 | 11 | 转鼓内腔积渣 | 28 | 冲洗水压过低 |
G9 | 油品乳化 | 12 | 长时间未清洗转鼓 | 29 | 阀门没打开或开度不够 |
G10 | 向心泵及各腔室连接处漏 | 13 | 软水、烧碱量配比不合适 | 30 | 转鼓内渣阻 |
G11 | 冲洗水量太小 | 14 | 温度不合适 | 31 | 作用弹簧刚度降低 |
G12 | 一次排渣量过大 | 15 | 搅拌速度不合适 | 32 | 尼龙阀座变形 |
G13 | 排渣频繁或连排 | 16 | 反应时间过长 | 33 | 操作水不清洁或水压低 |
G14 | 排渣量过小,排渣不及时 | 17 | 油在批应时有短路 | 34 | 操作水压过高 |
1 | 比重环口径过小 | 18 | 重液相出口堵塞 | 35 | 转鼓平衡腔变小 |
2 | 处理量过大 | 19 | 冲洗水量过少 | 36 | 操作水进水时间过短 |
故障树把系统故障的各种因素联系起来,逐层建立了故障发生的因果关系和逻辑关系,具有层次分明,逻辑严密,形象直观的优点。对生产、维修人员有较强的指导性,也可作为工程技术人员分析问题的一种思路。