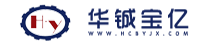
1 前言
污水处理装置所称的“三泥”,通常是指油泥、浮渣和剩余活性污泥,具有污染物成分复杂,恶臭严重,含水率高,稳定性好,脱水难度大,处理难度大等特点。通常,石化行业普遍采用沉降分离和机械脱水等方法,对“三泥”进行初步减量化处理。“三泥”减量化处理的好坏,决定了污水处理成本的高低;同时,对进一步深度处理工序(如焚烧工艺、热萃取工艺等)的能耗也将造成直接影响。另外,若不能及时有效地处理“三泥”,将导致污水处理装置内部物化、生化以及深度处理单元功能的降低,进而致使外排水质超标。
长期以来,广州石化炼油污水处理装置外排水质的合格率偏低(2007年为77%,2008年为86.2%,2009年为78.8%),一个主要的原因就是该装置自身产生的大量“三泥”无法得到及时有效处理。2009年,广州石化启动了炼油污水“三泥”综合治理改造工程,对炼油污水“三泥”系统进行了彻底改造,并通过严控隔油、浮选、生化等工序的工艺参数,优化“三泥”处理流程,强化“三泥”沉积分离脱水等措施,大幅降低了“三泥”数量,在离心脱水机低负荷运行等不利条件下,仍然解决了“三泥”的处理难题,不但使广州石化污水外排合格率 达到100%,而且使“三泥”的外委处理量大幅降低,经济效益和环保效益明显。
2 改造前现状及分析
2.1 改造前现状
公用工程部炼油污水处理装置主要接收并处理广州石化炼油区所有炼油装置及罐区生产过程中产生的污水,包括预处理单元和一、二级生化单元、深度处理单元等,设计处理能力为600m³/h。
改造前,炼油污水处理装置每天产生浮渣60~70t,部分送到焦化装置处理,部分外运处理,每月外运处理量约1500~2000t。油泥(隔油池、浮选池、后絮凝、兼性池)不定期由有资质的清池队伍清理,一次清池油泥量在300~1000t之间,全部外运处理。每天产生的剩余活性污泥脱水前约为40t,剩余活性污泥脱水采用带式压滤机进行处理,型号为BSD1000S7,设计处理量为6m³/h。脱水后干泥量约为3t,全部外运处理,每月外运处理量约100t。
2.2 存在问题
2.2.1 “三泥”产量大,带式压滤机处理能力不足
广州石化炼油污水处理装置氧化沟容积为4628×2m³,有效容积按4000×2m³计算,正常排泥量应为816t/d,每月正常排泥量约为24000t;按脱水前剩余污泥含水率为99.9%,以及脱水后污泥含水率为90%计算,每月应产干泥244.8t。但2008年,干泥月均产量仅为135.29t,只占理论计算产泥量的55.3%,“三泥”处理严重不足。
2.2.2 脱水后干泥含水率偏高
在污泥处置减量化过程中,脱水污泥含水率是一个极其重要的指标。污泥中所含水分的质量与污泥总质量之比为污泥含水率。污泥含水率越高,脱水后污泥的体积越大,处理效果就越差。改造前,炼油污水处理装置脱水后的干泥含水率偏高,在90%左右,脱水效果差,污泥减量化不明显。
2.2.3 “三泥”直接外运,处理费用高
带式压滤机无法处理浮渣和池底泥,“三泥”未经处理直接外运,费用成本巨大。2007~2009年,广州石化炼油污水“三泥”处理费用见下表:
时间 | 活性污泥(t) | 浮渣回炼(t) | 浮渣外运(t) | “三泥”处理费用/万元 |
2007年 | 1106.36 | 7419.7 | 3370.06 | 187.50 |
2008年 | 1623.53 | 3118.12 | 11295.56 | 478.35 |
2009年 | 1468.02 | 1619.87 | 13009.06 | 521.99 |
注:活性污泥处理费用为720元/t,浮渣外运费用为320元/t,两项合计,即为“三泥”处理费用。
2.2.4 生化单元处理压力大,外排污水不能稳定达标
由于浮渣不能及时有效地加以收除,浮选能力下降,生化单元进水水质恶化,且极不稳定,生化单元不断受到冲击。与此同时,剩余活性污泥不能有效处理,导致生化微生物新陈代谢速度降低,污泥老化严重,处理能力不足。生化系统受冲击时,需大量排泥置换恢复污泥活性,否则将影响整个系统的平稳运行,致使外排污水不能稳定达标。
2.2.5 “三泥”(浮渣)回炼焦化问题
2007年以前,广州石化焦化装置小给水时,将浮渣当作小给水送进待冷焦的焦炭塔,每次历时1h,约处理浮渣25t,全天处理浮渣约50t。由此带来的环保问题如下:
(1)污泥回炼时,焦炭塔内的温度只有350℃,且呈不断下降趋势,没有稳定的热源供给,在卸顶、底盖和除焦时恶臭气味严重,工作环境恶劣,不能满足职业卫生要求。
(2)污泥回炼后,冷焦水携带浮渣,冷焦水池清理周期变短,清池频繁,实际上是污染转移。
因此,从2008年起,焦化装置逐渐减少甚至停止回炼浮渣。而在带式压滤机无法正常处理情况下,只能大量外委有资质的单位进行浮渣处理,这无疑增加了运行成本。2008年和2009年,浮渣外运处理量分别达到1.13万t和1.3万t。
2.2.6 带式压滤机严重老化
带式压滤机始购于上世纪90年代,因工作环境恶劣、维护检修频繁等原因,设备老化严重,系统运行负荷下降,已不能满足正常生产需要;且设备滤网容易堵塞,必须经常用水冲洗滤网,造成新鲜水消耗量增大。该带式压滤机为敞开式,设备运行时,污泥散发恶臭气味,操作及检维修人员工作环境恶劣;同时,污泥散发的恶臭气体对电气、仪表等设备腐蚀严重,设备故障率较高。
3 技术改造及工艺优化
3.1 技术改造
针对炼油污水处理装置“三泥”处理单元存在的上述问题,2009年对“三泥”处理单元进行改造,采用集中收集、集中浓缩脱水、 化学调质和离心机械脱水处理等工艺,使处理后污泥的含水率降到85%左右,实现了污泥的减量化;增加了一套“三泥”热萃取装置(目前仍在开工调试阶段),有望真正实现污泥的资源化和无害化处理。
改造后,核心单元离心机采用LW400×1750NY卧式螺旋卸料沉降离心机,设计处理量为10m³/h,日产干泥25t。该离心机密封性能优良,污泥脱水处于全密封状态,操作环境清洁卫生,具有节能环保、处理量大、操作维护方便等特点。
广州石化炼油污水处理装置“三泥”综合治理项目一期离心脱水机调试过程中,出现分离液带渣、带泡严重的情况,需经常停机清理沙井溢出的浮渣和含油污水集水池内的浮渣,污泥脱水效果不佳。经多次技术攻关后,排除了因设备及工艺介质干扰等因素,处理量仍只有设计负荷的30%~40%,影响了“三泥”的正常处理。
对此,对离心机脱水污泥絮凝剂进行筛选试验,分别对比两家不同生产厂商提供的药剂:
(1)离心机原药剂,聚丙烯酰胺(阳离子),相对分子质量大于等于700×104。
(2)新药剂,聚丙烯酰胺(阳离子),相对分子质量大于等于900×104。
离心机脱水絮凝剂试验结果:
序号 | 项目 | PAM新药剂(相对分子质量≥900×104) | PAM旧药剂(相对分子质量≥700×104) |
1 | 进料量(t/h) | 7.5 | 3.5 |
2 | 加药量(t/h) | 0.60 | 0.60 |
3 | 配药浓度(%) | 25 | 30 |
4 | 液相出水(mg/L) | 136 | 1270 |
5 | 固相出泥含水率(%) | 82.3 | 87.5 |
6 | 停机次数 | 无 | 频繁 |
7 | 离心机转速(r/min) | 2370 | 3000 |
对比试验结果表明,使用新型阳离子聚丙烯酰胺,明显优于原有使用药剂,处理负荷在原有基础上提高一倍以上,满足装置满负荷运行要求;离心机转速大幅降低,可调空间增大,有效保护和延长设备的使用寿命;解决了离心机脱水残液带渣问题;脱水污泥含水率略有下降,减少了干泥体积;药剂投加量也相应减少。
3.2 源头减量化控制
污泥浓缩是污泥脱水的初步过程。污水处理过程中产生的污泥,其含水率通常很高,尤其是二级生物处理过程中的剩余活性污泥,含水率一般为99.2%~99.8%,这对污泥的处理、利用及输送都造成了一定困难,必须对其进行浓缩。浓缩后的污泥近似糊状,含水率降为95%~97%,体积可减少为原来的1/4,但仍保持了流动性,可以用泵输送,从而降低了运输费用和后续处理费用。因此,在进行“三泥”综合治理项目改造的同时,对活性污泥储罐、罐底泥储罐、6个污泥浓缩斗、8号浮渣罐的脱水工艺进行优化,增加了中、高、低位脱水流程,使污泥的体积大幅降低,并使浓缩后污泥的性质完全达到离心机物料的标准。同时,进一步加大了浮渣和污泥从生产系统中的排除量。
4 技术改造及工艺优化效果
改造后,统计2011年1~3月数据,脱水后干泥含水率为83.22%,按带式压滤机脱水污泥含水率为90%计算,干泥含水率下降6.78%,污泥体积比改造前减少40%,污泥减量化效果明显。
2010年,“三泥”处理单元完成改造后,继续对操作工艺进行优化,通过对离心脱水药剂进行筛选,优化污泥离心脱水前重力浓缩流程等,确保了离心机既能处理活性污泥,也能处理浮渣。2010年,浮渣外运量(996.48t)较往年大幅减少。2010年“三泥”处理费用为176.60万元,较2009年节约345.39万元。同时,基本解决了污水装置“三泥”的后路问题,2010年炼油污水处理装置外排污水合格率 达到100%。
5 结论
(1)通过对炼油污水处理装置“三泥”处理单元改造及工艺优化,浮渣及活性污泥经重力浓缩、脱水后,进入离心机脱水处理,并投加高效PAM絮凝剂,离心脱水后污泥含水率小于等于85%,消除了带式压滤机脱水污泥含水率高且不能处理浮渣的问题,基本解决了污水装置“三泥”的后路问题,减少了“三泥”的外委处理费用,一定程度上实现了污泥的减量化,也为炼油污水处理装置外排污水的稳定达标创造了条件。
(2)广州石化炼油污水处理装置工艺改造中,增加了一套“三泥”热萃取装置,待其调试开工后,经热萃取处理系统处理后的产物的含水率将小于5%,可送至CFB锅炉直接焚烧。届时,将真正实现污泥的减量化、资源化和无害化处理。