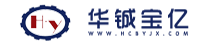
对于炼厂特别是炼油厂来说,其在进行污水处理过程中,所产生的油泥、浮渣以及活性污泥等的脱水一直是一大难题,其中,尤以油泥和浮渣的脱水问题较为突出。以往采用的是真空转鼓过滤机脱水,但由于这一脱水技术效率不高,且需要消耗大量的劳动强度等,极易影响到炼油污水处理后路的畅通,导致大量污泥只得外运处理。直到1995年,中国石化洛阳分公司在洛阳石油化工工程公司等的大力帮助下,才开始将卧式离心沉降式分离机(简称离心机)运用到处理炼油厂的“三泥”脱水以及PTA装置的污泥脱水问题中去,并取得了显著成效。
1 卧式螺旋离心机
1.1 卧式螺旋离心机的工作原理
卧式螺旋离心机也即螺旋卸料沉降离心机,是一种通过借助离心沉降法实现悬浮液的分离,并利用螺旋方式卸料的泥水分离机器。其中,转速较高的转鼓、与转鼓转向相同且转速略低于转鼓的带有空心转轴的螺旋输送器以及差转速器等是其重要的组件。当要分离的悬浮液(比如经蓝芩调醇后的废液等)由进料管、螺旋出料口进入到转鼓中去,在高转速的转鼓所产生的离心力作用下,螺旋叶片会将沉积于转鼓内的固相颗粒不断刮下并推到排渣口处排出。与此同时,液相会在固环层的内侧形成液环层,并经过螺旋通道流出转鼓。
1.2 卧式螺旋离心机的特点
相较于其它的离心机污泥脱水机,卧式螺旋离心机的应用范围相对广泛,并且集强大的生产能力、较高的自动化程度、低耗电以及便于维修等特点于一身。卧式螺旋离心机是当前炼厂运用较为广泛的一种“三泥”处理设备。
2 卧式螺旋离心机的主要参数
2.1 转鼓转速
通过上述卧式螺旋离心机的工作原理不难得出,离心机的转鼓转速越高,其所产生的离心力就越大,不仅有助于促进离心沉降速度的提升,而且还能够在一定程度上将污泥的含水率降到极低。然而并非转鼓转速越高越好,倘若作用力过大,极易导致污泥絮体分解破碎,反而影响脱水效果,并且增加转速,设备的磨损也会大大增加,经过试验该中心的转鼓速度在2600~2850rpm之间较佳。污泥性质较好时,转鼓转速控制在2660rpm,污泥性质较差时,特别是冬季控制在2850rpm。
2.2 差转速
差转速是转鼓转速与螺旋转速之差,其会对排渣能力、泥饼干度以及滤液质量等产生直接性影响,是离心机在具体运行过程中至关重要的可调节参数之一。从某一方面来讲,差转速的大小决定污泥在转鼓内停留时间的多少,对污泥的脱水效果有着十分重要的影响,当进泥量一定时,如果差转速比较低,污泥在离心机停留时间较长,脱水后的污泥会更干,但是由于出泥速度减小后泥层厚度会增加,导致固体颗粒向清液方向的渗透现象加大,清液中的含固量加大,固体回收率降低。如果差转速比较高,污泥在离心机中停留时间较短,脱水后的泥饼含固量降低,出泥速度加大后泥层厚度会减小,导致固体颗粒向清液方向的渗透现象减小,清液中的含固量减小,固体回收率提高;差转速越大,转鼓与螺旋之间的相对运动越大,必然会增加对液环层的扰动程度,固环层内被分离出来的污泥会被重新泛至液环层,并有可能随分离液流失。所以差转速应根据泥饼含水率、固体回收率的情况进行及时调整,在实际运行中可以对应进泥量和进泥浓度,观察螺旋电机的扭矩进行调整,离心机螺旋电机扭矩控制在10%~14%可以得到较好的泥饼含水率和固体回收率,如果泥饼较干、清液含固量较大可以加大差转速,反之可以减小差转速。在生产过程中一旦螺旋扭矩不断上升时如超过25%,应及时加大差转速将转鼓内污泥排出,避免造成螺旋电机过扭矩停车的情况。
3 结束语
总的来说,在处理炼厂“三泥”中,选择适宜的操作参数对于促进离心脱水效果的提升大有裨益。本文所采用的卧式螺旋离心机的操作参数可定为:转鼓速度在2600~2850rpm之间,扭矩控制在10%~14%,差转速为1~5r/min。转鼓速度过高,极易导致絮体中油离解出来,从而使离心液COD增加。而差转速的增加则能明显改善“三泥”的离心脱水效果。