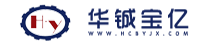
1 前言
二乙基硫代磷酰氯(俗称乙基氯化物)是有机磷农药的重要中间体。近年来随着国内有机磷农药新品种的不断开发和推广应用,对乙基氯化物产品的需求平稳增加,而且对乙基氯化物产品质量要求越来越高。以五硫化二磷为原料,采用硫化钠溶液精制法生产的乙基氯化物,具有质量好,收率高等特点,基本能满足有机磷农药生产的要求。在此工艺生产过程中,粗乙基氯化物精制后固体硫磺的分离,各厂采用众多不同的分离设备。从总体看仍不够完善,生产操作工人劳动强度大,劳动条件差,而且分离出来的硫磺含湿量较高。这不仅是生产技术上的问题,而且也是企业管理上的薄弱环节。
卧式螺旋卸料沉降离心机为自动连续操作式的离心机。它的分离及卸料是靠转鼓的离心力场和转鼓与螺旋推料器借助行星差速器所产生的转速差来实现的。该机具有分离因数高,分离效果好,适应性广等特点。与其它脱水机械相比,又具有结构紧凑,占地面积小,单位产量耗电量较少,运行费用低等优点,而且操作简单,运行平稳,易于维修。该机的另一个特点是适用于固相颗粒粒度变化范围较大,低浓度和中等浓度悬浮液固相的脱水或液相的澄清,其范围约为:固相粒度0.005mm~2mm,悬浮液浓度2%~50%,温度0℃~80℃,对照乙基氯化物固液分离的生产工艺要求,卧式螺旋卸料沉降离心机能满足其生产条件。
2 分离原理及参数调整
试生产选用四川省江北机械厂生产的WL-350B型卧式螺旋卸料沉降离心机,其转鼓大端直径350mm,转鼓有效长度875mm,电机功率11kW,生产能力1m³/h~3m³/h(以悬浮液计)。
2.1 分离原理
被分离的悬浮液经进料管连续不断地输入螺旋推料器内加料仓,经初步加速后从加料仓径向的四个加料孔抛入转鼓与螺旋组成的环形空间。在转鼓的离心力场作用下,悬浮液很快在转鼓内分为两层:固相粒子(重相组分)沉降于鼓壁形成外环,被澄清的液相(轻相组分)浮在固相层内壁形成液流环。当料层达到一定厚度时,澄清液从转鼓大端溢流孔流出。沉降在鼓壁的固相在螺旋推料器以一定差转速的推动下,脱离沉降区,沿锥面向小端卸渣孔移动,同时继续排出渣中一些水分,使渣进一步得到干燥,直到由小端卸渣孔卸出。整个分离卸料过程都是连续进行的。
2.2 主机转速和差转速的调整
江北机械厂WL-350B型卧式螺旋卸料沉降离心机出厂时,主机转速n=3500r/min,差转速△n=-28r/min(滞后)。实际生产中根据被分离物料的性质,按下述原则选择主机转速和差转速:对易分离物料,即物料的固液相比重差大,浓度大,固相松散,悬浮液粘度低,转鼓适宜用低转速(低分离因数),螺旋用大差转速;反之,转鼓宜用高转速(高分离因数),螺旋用小差转速。经试生产证明,乙基氯化物生产中固液相分离属前一种情况,需对两种转速进行适当的调整。
2.3 液层深度的调节
该机出厂时配有两组半圆环溢流挡板,用以调节三种不同的液层深度。一般对易分离物料适宜用小的液层深度,不装或装上内径较大的溢流挡板;反之,用较大的液层深度,装上内径较小的溢流挡板。本工艺生产基本属前一种情况,其较佳液层深度仍需根据具体物料在试验中确定。
3 生产试用结果与初步体会
根据被分离物料的特性,经试验调整好有关参数后投入试生产运转。经生产实践证明,只要按机器使用要求操作,就能实现长周期稳定运行,满足生产工艺的要求。
(1)减轻了生产操作工人的劳动强度。整个分离过程是自动连续进行,分离出的硫磺从主机下面的出渣口自动排出。由于该机无需滤布,一方面省去了生产工人清洗滤布的操作,另一方面又减少了因清洗滤布而产生的生产废水,有利于环境保护。
(2)分离出硫磺的含湿量下降。经实际生产与分析化验结果看,用该机分离出硫磺含湿量与真空过滤分离法相比,一般要下降十个百分点左右。这样相应提高了产品的回收率,增加了经济效益,同时也减少了对环境的影响。
(3)生产操作过程应按设备的生产能力、使用要求认真精心操作。水洗精制工序也应严格按工艺要求操作,避免粗放式操作,以求该机能长期正常运行,减少停机检修时间。
(4)该机系高速运转设备,在分离过程中有部分气体飘散出来。因此,该机应安装在通风良好的环境,或采用密闭强制通风法,以保持良好的操作环境。