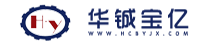
1 离心机主电机系列故障经过
1.1 第一次离心机主电机故障停车及处理经过
该离心机为德国威斯伐利亚离心机,型号为UCC450-00-32,第一次故障发生在4月14日凌晨0:30分,车间班组巡检发现离心机自停,并显示“转鼓主机失效”报警信息,发现主电机发烫,现场有烧焦的糊味。电工检查确认主电机抱轴,盘车不动。遂将离心机断电,紧急联系拆运抢修,解体打开电机前后端盖,发现轴承抱死,轴承内没有润滑油,轴承端盖内孔损坏,测量轴直线度,挠度为3~5mm,并发现轴有裂纹现象,采取的措施是在裂纹处用液压锯将电机轴割开一分为二,两处轴头端面切削为锥形端面,轴心处做连接螺栓,以实现轴向定位,两半轴采用J507焊条进行堆焊后,车削加工处理,更换工厂提供的SKF6210轴承两套,轴承内加注二硫化钼锂基脂,电机组装完毕后,于4月17日进行回装,在检查了各装配精度及要求后,开启运行离心机,运行正常。
1.2 第二次离心机主电机故障停车及处理经过
4月28日凌晨5:00,班组巡查发现离心机主电机再次出现故障,现象与之前完全一样,水洗后离心机无法启动,显示屏报警信息仍是“转鼓主机无效”,机电仪等相关人员确认离心机主电机抱轴,第二次拆走维护,检查后与第一次症状一样,测量轴的挠度为0.2mm,采取措施是车削去除0.25mm材料,之后刷镀0.25mm,恢复轴原先尺寸,前轴承由6210球轴承更换为NU210滚柱轴承,后轴承为6210轴承,并加注3#锂基润滑脂,至29日回装,22:30分离心机开启运行,设备运行平稳,状态正常。
1.3 第三次离心机主电机故障停车及处理经过
5月2日班组巡检发现离心机停车,无法再次启动,亦无法水洗。当时显示屏显示“Failure solids conveyor”。机电仪三方确认离心机主电机轴断裂,轴头断裂,轴承保持架散架,轴承内没有润滑油,轴承端盖损坏,因电机主轴已无法使用,需加工一新轴,材质为27SIMn,电机前轴承安装NU210滚柱轴承,后轴承安装6210球轴承,至5月6日离心机主电机组装完毕,空试10小时,测试正常后装机投用,7日上午离心机开启运行,运行状态及数据正常。
1.4 第四次离心机主电机故障停车及处理经过
5月15日18:00左右,运行班组巡检再次发现离心机自停,遂对自停原因进行检查,将离心机挡板及齿轮箱端盖打开发现主电机断裂,转鼓盘车不动,皮带解除后对离心机转鼓进行盘车,转鼓回转正常,鉴于多次故障,第四次故障后,经过技术分析讨论后,采购新电机,组装后试运行正常,目前运行至今。
2 离心机主电机系列故障原因分析
此次离心机系列故障从4月14日第一次故障至5月15日第四次故障停车,出现四次系列故障停车,从中可发现四个共同点,即四次均出现了电机前端轴承抱死、轴承无油、前端轴承均出现高温、故障前工艺流程未有大的变动等共性问题;四个不同点,即轴承型式、轴承润滑、轴、断口在四次故障中有所不同。前三次故障为原电机轴,第四次故障为加工的新轴;端口位置不同表现为第一次断轴位置在电机前轴承外,第二次断轴位置在前轴承位上。
第一次断轴从断口观察,其瞬断区和扩展区较为明显,可判定为疲劳断裂,第二次断轴其端口因轴头磨损其瞬断区和扩展区不明显。电机主轴断裂无外乎几方面因素所致:1、轴材料问题;2、轴加工问题;3、轴承问题;4、安装问题;5、载荷问题;6、润滑问题;7、失稳问题;8、异物卡阻问题;9、皮带问题;10、差速器问题。现一一分析如下:
2.1 轴材料问题
本次离心机系列故障前两次表现为轴承损坏,但与轴本身都有关系,第一次故障检查后已发现轴有裂纹,且轴挠度达3~5mm,但轴未断裂,说明原电机轴强度是没有问题的,即使在轴承抱死、轴严重弯曲的情况下,轴的材料强度依然保证了离心机的运转。但是第一次处理过程中轴经过割裂、堆焊、车削处理,已改变轴的力学性能。其焊材与母材熔合后的材料力学已发生了改变,其强度、刚度、韧性、抗剪切力等力学指标一定改变,在第二次故障处理过程中,经过车削和刷镀后,力学性能再次发生改变;在第三次加工新轴过程中,并没有采用常用的45#钢,而是采用的27SIMn,轴材质又发生了改变,当然其力学性能也随之改变,更换新轴后其刚度、强度是否符合要求,安全裕度是否符合要求,P、S、H等这些易引起轴断裂的有害材料成分及SI、Mn等有益成分是否符合要求等并未进行检测分析,所以我们有理由怀疑轴的材料不符合要求是导致第二次断轴的这一重要论断。
2.2 轴加工问题
前三次故障处理过程都涉及到轴的加工,第一次涉及车、铣、钻加工、电气焊加工,第二次涉及车削加工、刷镀;第三次涉及车削加工,在每一加工过程中极易造成应力集中问题的出现,譬如说在热加工过程中如何控制马氏体的形成,降低焊接残余应力、避免应力集中,危险截面的出现,车削加工中如何控制车削量、何处设计退刀槽,每一次的车、铣、钻、焊、镀都是对轴的“伤筋动骨”的手术,特别是轴表面加工处理,因轴的表面是受应力较大区域,轴中心受应力较小,在前两次轴的处理过程中,加工过程中都涉及到不同材料的叠加,在其结合面,仔细观察第一次断口的表面特征,会发现轴的中心为瞬断区,裂纹发生和扩展正处于两种材料的结合部,在第一次故障后已发现轴有裂纹,尽管轴已弯曲3~5mm,但因原轴的材料强度、韧性较好,未发生断裂,在第一、二次经过堆焊、车削、刷镀过程中,轴的内部危险裂纹并未彻底消除,反而出现了在经过第二次轴的加工修复后,第三次出现了端轴事故,可以这么说,前三次离心机故障是轴的强度、韧性、抗剪切力不断劣化的一个过程,只是在第三次轴以断裂的破坏形式出现,所以说,轴的加工处理是导致轴断裂的一个重要因素。
2.3 轴承问题
在三次电机轴处理过程中,轴承都出现了无油抱死粘连情况,并更换了不同型号轴承,轴承全部为正规渠道提供,前期通过外观检查、状态及温度检测,可以排除轴承的质量问题。每次离心机故障,检查轴承全部抱死、无油,这说明轴在断裂前轴承温度异常高,但在日常检测过程中却未发现,实际上轴在断裂前是一个快速劣化过程,从危险裂纹的形成、扩展直至断裂这个过程很短,在这个过程中因为轴的扭转导致轴不同心可使支撑位轴承温度急剧升高,特别是在第二次断轴过程中,断口正处于轴承内圈位置,更是导致了轴承的高温,轴承内的润滑油在高温下发生泄漏甚至汽化,橡胶材质的油封高温下出现焦化现象,这也就是为什么断轴后操作工现场闻到“糊味”的原因。所以轴的劣化、扭转是导致轴承损坏的原因,这是一个因果关系,而不是轴承的缺陷导致轴的断裂。
2.4 安装问题
安装设计有两个问题,一是电机皮带轮与转鼓皮带轮的对中,另一个是电机底板的平面度。对于皮带轮的对中,是由皮带轮在电机轴上的位置及电机的相对位置决定的,可调整量非常有限,对中要求是盘车过程中,皮带应正确入皮带轮槽内,外缘与轮槽无过渡挤压,盘车联动运转灵活;皮带的张紧度以按压皮带中部,其挠度在20mm左右为宜,电机底板平面度以水平仪检测为准。在历次离心机检修过程中,电机底板及皮带轮基本按照上述原则进行。假设电机与转鼓皮带轮不在一个垂直立面上,若错位距离较小,则皮带轮的外缘会出现磨损,错位距离较大,则离心机在开车过程中,就极有可能发生皮带转动脱落或断裂的情况,但这两种情况都没有发生,在第一次断轴过程中,对每条皮带进行擦拭检查,除了第一次断轴后,有一条皮带因轴断裂出现磕碰损伤外,其它皮带均处于正常可用范围,因此可排除此安装问题。
2.5 载荷问题
在前两次轴的加工过程中,因轴材料特别是危险截面上的材料发生了改变,且车、铣、焊、镀等加工工艺已改变了材料的力学性能,特别是第二次采用27SIMn材质加工新轴过程中,未对轴加工前后进行热处理、表面强化处理及化学处理措施,以提高轴的抗疲劳和抗剪切强度。由于受条件所限,未对加工后的轴进行材料成分分析及力学性能测试。从离心机的运行参数分析,从4月14至5月15日离心机运行期间,处理泥量基本上在7~12立方每小时范围内,系列故障之前处理泥量长期在12~16立方每小时范围内,说明外部载荷并没有额外增加,可排除载荷问题引起的故障。
2.6 润滑问题
整个离心机系统有5处润滑点,在运行检测过程中并未出现转鼓前后轴承端温度升高迹象,基本上在40℃左右,所以离心机本体内因润滑不畅导致转矩增大进而电机断轴的可能性也可以排除。
2.7 失稳问题
离心机是通过介质密度不同产生不同的离心力实现泥水分离,所以对转子的动平衡是有要求的,离心机在出厂前对螺旋、转鼓分别进行动平衡测试,并且组装完毕后还需要对整体进行平衡测试。失稳是不是导致电机轴断裂的主因,可通过假设法反推一下:假设离心机转子不平衡度增大,则离心机本体、转鼓前后轴承端及电机的震动和烈度一定能通过测振仪检测出来,但这与我们实际检测数据是不符的,在提高离心机震幅、烈度及温度的检测力度与检测频度,不同人员不同仪器对比检测,震幅检测数据基本在0.02~0.05mm区间波动,符合震幅小于0.06mm的优良运行状况;另外烈度的检测,厂家要求是12mm/s以下,实际检测数据都在2~5mm/s波动,截获的烈度数据7.2mm/s,也是完全满足厂家运行要求的;二是甩泥环处4条螺栓冲刷导致的离心机失稳也是不太可能的,甩泥口和分离水口的甩泥环、螺栓、堰板等受到固液介质的冲刷是正常的。实际上,螺栓冲刷较甩泥环出泥导致的转子不平衡度要小很多,在每一次出泥瞬间,出泥是通过下端的一个甩泥环实现的,此处甩泥环积聚的污泥较多,在转鼓高速旋转的过程中,此处产生的不平衡力较之螺栓堰板冲刷引起的不平衡度要大很多,因此通过分析推理可排除失稳问题引起的主电机断轴这一论断。
2.8 异物卡阻问题
离心机主要处理浮选产生的浮渣、底泥、剩余活性污泥及隔油池内浮渣、底泥,通过管道进泥罐搅拌均匀后,进离心机转鼓前要通过3道过滤器过滤,所以出现异物卡阻导致断轴的可能性非常小,且在历次离心机检查维护过程中均未出现异物卡阻问题 ,故此项原因可排除。
2.9 皮带及差速器问题
皮带问题在2.4 安装问题中已阐述,此处不再赘述。关于差速器问题导致断轴的可能性也非常小,如果说差速器内出现偏心轴承损坏或轴套开裂等严重情况,会立刻出现两种后果,一是转鼓盘车异响,二是盘车卡阻,但这两种情况在系列故障中都没有出现,且每次电机安装后离心机都能实现开车,运行检测中也未发现数据及声音异常。所以说差速器问题引起的断轴可能是不存在的。
综合以上问题研判,此次离心机系列故障是由电机主轴引起的,从第一次轴弯曲3~5mm到第二次轴弯曲0.2mm,再到第三次轴发生断裂破坏,这一过程是有着前后紧密联系的,在前三次故障处理过程中,因对轴的加工处理及过程控制不当导致了轴强度、刚度改变,在第三次事故中以疲劳断裂的破坏形式出现,在第四次故障即第二次电机断轴过程中,因对轴材料选型、加工处理不当才导致了第二次电机断轴的发生。
3 预防性措施
由于离心机的技术集成度高,对运行和维护有严格要求,对材料加工和安装有严格限定,所以在日常操作中,应严格按照操作手册进行,特别是设备开停车过程中,做好设备和管道的清洗工作;在日常维护中,应按照厂家的维护手册做好设备的润滑保养,状态检测及清理盘车等工作,涉及轴的加工修复等改变材料属性及力学性质时,应谨慎处理,做好材料选型、加工处理、力学校核试验等工作。
4 结论
自动离心脱水机的平稳运行至关重要,在运行、维护及故障处理过程中,只有严格按照操作及维护手册,做好日常维护保养及运行,在故障处理中做好故障综合研判和技术分析,才能确保故障的有效解决,从而保证离心机的安稳长期运行。