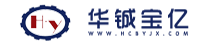
1 卧螺沉降离心机概况
某石化公司中高密度聚乙烯产品主要采用了德国的淤浆法工艺进行生产,该生产工艺将会采用一种高密度聚乙烯装置进行生产,在搭建后可保证该公司设计生产能力达到30万吨/年。其中,实现高密度聚乙烯中己烷溶剂和聚乙烯粉料的分离,则会主要使用卧螺沉降离心机。在该离心机实际使用过程中,由于存在离心重量超限、设备运行振动幅度较大等问题,造成了离心机经常产生各种各样的故障问题,严重影响着企业产品的生产效率。转子作为离心机中的关键部件,转子运行中出现的质量问题及更换周期较长将是影响着产品生产效率的关键,而当前转子则主要采用依赖进口,实现转子的国产化生产已成为企业自主掌握其核心部件生产能力的重要趋势。实现转子的国产化生产,将解决:
(1)吸取消耗进口设备的核心技术,提高企业在转子的设计生产工艺等方面的关键技术。
(2)可根据实际情况有针对性的对转子的结构、材料及生产工艺进行自主调整,而不依赖进口的现有部件。
(3)缩短维修周期,降低设备维护成本,提高离心机的工作效率。
(4)通过离心机的转子国产化的研究,有助于对离心机整台国产化提供了借鉴和参考。
高密度聚乙烯装置使用的是德国安德里茨公司SC4-1型卧螺沉降离心机。4台离心机备有1套转子,备用转子与在用转子交替使用,每套转子平均使用周期为2~3年。由于进口转子及国产化较困难,如果同时出现两台离心机故障大修,对生产带来极大隐患。面对这一情况,工厂决定对离心机转子进行国产化。
2 卧螺沉降离心机工作原理
卧螺沉降离心机在作业过程中主要采用了离心原理。通过将所需处理的悬浮液倒入至离心机中后,在螺旋加速的作用下带动转鼓的运转,利用转鼓产生的强大离心力,将悬浮液中较小密度的液相离心甩出,较大密度的固相则拦截在离心机筒中,以此实现悬浮液的离心分离作用。其中,该设备中主要利用差速器来将螺旋与转鼓进行过渡连接,以提高整个离心机的作业功率。因转鼓和输送螺旋的转速不同,分离后的沉渣经输送螺旋推动,不断推向转鼓的小端,从出渣口排出,分离后的液体经分离叶片,由转鼓的溢流口流出。
3 卧螺沉降离心机技术要求
主要技术参数(设计值)如下:能力=79m³/h,粘度=0.001Pas,固相密度=0.95g/cm,液相密度=0.7g/cm,固相质量浓度=23.73M%,转鼓转速=2050rpm,差速比=40,公称能力=78m³/h,公称转速=2000rpm,转鼓直径(DT)=914.5mm,转鼓切线长度=904.5mm,转鼓锥体长度=904.5mm,转动件重量=3400kg,轴承处轴径=220mm,粉料排出处直径(DA)=625mm,溢流堰处直径(DW)=810mm,开口宽度=120mm,开口数量=4,输送螺旋节距=191mm。
在转子结构尺寸及材料的设计过程中,所涉及到的工作包括:重点分析转子离心作业原理、结构尺寸,并实际的转子尺寸进行测绘分析,国内转子的材质进行理化试验分析,结合国内外资料的调研分析,确定了自主设计的国产转子结构尺寸、公差范围及零部件的材质情况。
离心机转子的转速跟转子的材料和强度有关,一般采用强度好、重量轻的超硬铝合金(LC4)超速离心机采用钛合金(TiC4)。一般来说,对同一离心机重量轻、容量小的转子转速要高,反之转速要低。
离心机中转子主要与定子及其他部件进行有效配合,实现离心机的通电及不同转速的调节,是整个离心机中的核心部件。同时,在作业过程中转子也承受着来自多方面的冲击力作用,保证其结构尺寸的合理性、结构强度等对提高离心机运行安全至关重要。
另外,还对关键部件和关键部位不断进行细化研究。经过研究讨论发现转子的关键技术主要包括两大方面:一是转子的整体机械性能;二是气封的耐磨性。
4 离心机转子的应用分析
4.1 进口离心机转子存在的缺陷和存在的问题
(1)离心机分离后的澄清液溢流高度种类少,不能满足各种工况的浆液分离,造成粉料中夹带的己烷较多,对后续的粉料干燥带来安全隐患。
(2)离心机内转子轴承油封耐磨与耐腐性能较差,使用寿命为1年,油封磨损后润滑脂无法注入在内转子轴承上,造成内转子轴承损坏停机。
(3)离心机转子气封弹簧选择的弹性补偿量较小,浆液由气封通道溢出,造成离心机扭矩升高,对离心机稳定运行带来严重隐患。
(4)离心机内转子与外转鼓由于长时间推送粉料,磨损量较大,降低了离心机的分离效果。
(5)离心机在减速停机过程中,由于内部结构的振动问题,造成了转子原有的振动平衡被打破,增加了离心机的振动幅度,造成了离心机振动超过了其自身设备,出现了停机现象。
4.2 国产化转子的综合机械性能设计
离心机进料浆液粘度大,长时间运行分离效果变差,所以对转子的综合机械性能要求很高。为了使转子具有良好的综合机械性能,采取了以下几个关键技术措施:
(1)溢流堰的高度选择,增加了溢流堰的宽度,由原来的3种溢流堰型式,改成5种溢流堰型式。浆液无论怎么改变澄清液都能从对应宽度的溢流口溢出。
(2)将原有内转子铸铁式油封型式改成铸钢式油封,大大提高了油封的耐磨性,防止浆液进入到内转子轴承内损坏轴承。
(3)将转子干气密封型式中的弹簧由细丝改成粗丝,增肌了气封的密封性能,提高了浆液的密封性能,增加了离心机的安全性。
4.3 转子的检查
4.3.1 转鼓部分检查
(1)转鼓内壁加强筋、凹槽检查,厚度检查。
(2)转鼓外壁检查。
(3)滤饼卸料口、耐磨片、衬环、刮板检查。
(4)母液卸料口、溢流堰检查。
4.3.2 输送螺旋检查
(1)螺旋外直径检查。
(2)螺旋叶片外刃背面磨损状况检查。
(3)螺旋叶片前沿磨损情况检查。
(4)进口区域螺旋叶片后沿磨损情况检查。
(5)进料口磨损情况检查。
对表面堆焊耐摩层的零部件,磨损量(径向)≤10mm。
4.3.3 转子同心度检查
转鼓和输送螺旋必须进行同心度检查,端轴径径向偏差不超过0.02mm;固体端螺旋轴径和进料端平衡轴径的径向偏差不超过0.02mm。
4.3.4 转子动平衡实验
同心度检查完后,螺旋和转鼓分别作动平衡实验。动平衡转速接近实际运行转速,动平衡精度应达到ISO1940/1 G2.5。
转鼓螺旋径向间隙=1mm,转鼓径向跳动=0.08mm,螺旋径向跳动=0.08mm,振噪声功率级=85dB(A),主轴承温度为环境温度+40℃。
计算G2.5时离心机转鼓残余不平衡量:
转鼓外直径Φ=1.01m,转鼓转速=2020rpm,重量=2000kg。
(1)A=2.5×10000/2020rpm=12.37
(2)B=A×2000kg/2=12376
(3)残余不平衡量=B/Φ2=24.5g/mm
计算G2.5时离心机转子残余不平衡量:
转子外直径Φ=0.66m,转鼓转速=2070rpm,重量=1000kg。
(1)A=2.5×10000/2070rpm=12.07
(2)B=A×1000kg/2=6038.6
(3)残余不平衡量=B/Φ2=18.29g/mm
5 国产化后取得的意义
由于国外的转子整体上具有设计更加合理、性能更加稳定等特点,较多技术具有一定的借鉴性。在实现转子的国产化中,不仅能通过国内的检测受到实现对国外转子材质成分进行分析,提高国内原材料理化试验检测能力;同时,可有针对性的分析转子的设计及制造加工工艺,掌握转子的核心加工技术,实现转子的自主设计,增强国内相关领域的技术水平,也将给企业及 带来更大的经济效益。另外,该转子的国产化也将有效解决当前 在转子生产制造领域的技术壁垒,并为国内相关技术人员积累重要的技术经验和财富,所带来的成效巨大。
6 结论
目前离心机转子已投入使用,运转平稳,平均运行周期约3年左右。通过对转子运行过程产生的不平衡机理进行分析研究,在设计及工艺方面进行了严格控制,有效突破转子运行过程中的核心平衡问题,这也打通了转子的国产化生产通道,为以后相关进口设备的国产化提供了参考,有值得推广的意义。