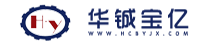
1 前言
随着经济快速发展,城市生活污水、工业废水的排放量急剧增加,污水处理所产生的污泥因其量大、恶臭、病菌含量大等特点对环境产生不可忽视的影响。目前较多还是采用填埋、堆放的方式处理,填埋并没有消除污染,只是延缓了环境污染产生的时间。而污泥焚烧(如投入循环流化床锅炉中燃烧)可实现污泥的减量化、无害化和资源利用的目标。污泥焚烧前的干化设备能有效提高污泥燃烧的利用率。干化机较常用的有圆盘式、桨叶式。本文就桨叶式污泥干化机制造过程中的工艺重点作一些抛砖引玉的探讨。
2 污泥干化机的结构及基本原理
污泥干化设备主要由空心桨叶轴、带夹套的壳体与驱动装置等组成。热介质分别进入空心桨叶轴与内筒、夹套间,污泥由进料口加入,充满楔形叶片间隙,在桨叶轴的转动下,物料一边被桨叶轴、桨叶和夹套内的蒸汽加热,一边向前移动,干燥后由出料口排出。
3 制造的重点过程控制与工艺措施和结论
3.1 内筒、夹套
内筒、夹套按GB150《钢制压力容器》制造,内筒的连接焊缝表面不得有裂纹、气孔等焊接缺陷,一般选用氩弧焊打底、手工焊盖面,焊后进行着色探伤检查。为了避免内筒与夹套焊后焊接缺陷返修困难,内筒与夹套组焊前应单独进行水压试验,合格后再与夹套组焊;夹套与内筒焊缝也应进行磁粉或着色探伤检查。
3.2 空心桨叶轴
空心桨叶轴是干化机的核心部件,桨叶轴的质量直接影响着干化机的效果。桨叶轴在加工过程中主要容易产生的问题:
(1)空心轴轴上焊接桨叶较多,焊接应力较大,分布不均,轴产生焊接变形。
(2)如何有效控制焊接缺陷的产生。
(3)轴头同轴度的有效控制。
针对以上问题,采取的工艺措施:
桨叶轴的焊接变形对轴运行中的危害较大,影响轴的径向跳动超差,轴在实际受载情况下,容易引起轴的断裂。焊接应力和变形的产生原因,简单说因为焊接区域的加热和冷却不均匀,接头各部分金属所处的状态不同,如熔池是液态,靠近熔池的基本金属处于塑性和半塑性状态,而远离熔池的基体金属处于弹性状态,这些区域又随着热源的移动而移动。在焊接不均匀加热和冷却过程中,焊缝金属和靠近焊缝的母材区域内产生了热应变并伴随压缩塑性变形,焊接接头区不均匀的塑性变形是产生焊接变形和应力的主要原因。只要进行焊接,就必然会产生焊接应力和变形。如何尽可能的减小这种变形的产生,主要从装配焊接的顺序和焊接的线能量考虑。根据实践与分析,制定了两名焊工从轴的两侧向中间同时焊接,通过这种对称性焊接,极大地抵消和减小了焊接变形,同时焊接过程中选用线能量较低的焊接方法、规范,可有效地防止和减小变形。采用小直径焊条、小电流焊接,桨叶轴焊后对轴的直线度、径向跳动进行测量,如超差可进行适当的热校正处理,热校正加热温度一般控制在不超过700℃,合金钢禁止采用水急冷等方式。
空心桨叶轴一般内部通入蒸汽或导热油等热载体,工作压力一般低于1MPa,热载体温度一般150℃~200℃,桨叶轴的焊接缺陷(如裂纹、气孔等)是不允许存在的,考虑桨叶比较密集,全部焊完后再检查,返修较困难。对此,采取了桨叶焊后先进行着色探伤检查,确保桨叶合格后再焊接再空心轴上,从而大大减少了试压后不合格而返修的工作量,确保了产品质量。
轴端同轴度偏大超差时,轴转动时会加快填料函体的磨损。为达到同轴度的要求,轴头粗加工时预留轴整体加工时余量,同时轴头与空心轴装配时尽可能提高同轴度要求,避免整体精加工时余量偏小而加工不出。桨叶轴整体组装结束后再进行精加工,确保轴的同轴度一般不大于Φ0.04mm。
3.3 制造中的一些其他控制点
由于轴中间通入的200℃左右的介质,轴承的润滑脂不选用普通锂基润滑脂,而应改用能耐200℃的高温润滑脂,以改善轴承的润滑效果,减少润滑脂的消耗。
干化机组装后应进行整体空载试验,确保电机及控制电器动作连锁、灵敏、准确;主机运行平稳,无异常响声;桨叶轴的转动方向符合要求。
通过对这些关键过程的有效控制,干化机的产品质量提升,性能得到保证。