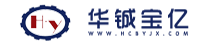
传统的污泥处理处置技术复杂,处理设备多样。其中,污泥干化耦合发电技术作为 鼓励发展的一种污泥处理处置技术,在国内污泥处理市场占据重要地位。该技术利用电厂的热源介质对污泥进行干化,再协同燃煤焚烧发电,实现污泥无害化、稳定化、减量化、资源化的“四化”目标,同时提升并利用污泥的热值,降低电厂的煤炭消耗,减少碳排放。
污泥干化过程中产生的挥发性有机化合物如烷类、芳烃类、脂类以及恶臭气体如NH3、H2S等的处理。不同于废水和废固的治理,这些恶臭气体易逃逸、扩散性强、影响范围广、收集治理难度大。在已有的污泥干化项目应用中,无可避免地会有臭气治理不理想的现象,这种现象同时也存在于其他污泥处理工程中,如污泥厌氧消化、污泥堆肥等。一方面,污泥存储、干化、输送等各个工艺环节都会产生恶臭废气,废气中含有的恶臭气体如NH3、H2S等成分,虽然阈值较低,但是很容易引起周边人员的身体不适;另一方面,臭气的收集及处理系统的选择存在不合理性。
臭气的收集及处理技术的选择直接影响着臭气治理的效果。本文基于华东某电厂200t/d污泥干化耦合发电项目,介绍了污泥圆盘干化系统的设计、臭气的收集及技术的选择,结合本工程实际运行情况,提出改进建议,为类似工程项目提供借鉴。
1 臭气处理工艺比选
1.1 臭气处理方法分类
臭气处理的方法主要包括:物理法、化学法和生无法。其中,物理法包括活性炭吸附法和吸收法;化学法包括等离子法、氧化法和焚烧法;生物法包括:生物过滤法、生物洗涤法及植物液法。
1.1.1 活性炭吸附法
活性炭吸附法一般适用于恶臭组分浓度较低,废气量大的环境,对苯系物及硫化物具有较好的脱除效果。
1.1.2 等离子法
等离子法是利用高压电磁脉冲电晕放电,产生大量的高能电子、O、OH等活性粒子,将恶臭物质进行氧化降解为微小或无害化的物质。
1.1.3 焚烧法
焚烧法是利用高温作用下,臭气被分解产生CO2和H2O,达到除臭的效果。
1.1.4 生物过滤法
生物过滤法是利用附着在填料上的微生物作用,将臭气物质作为营养物质进行吸收消化,进而达到对恶臭气体的去除效果。但是,生物除臭效果较差,需结合活性炭法才可满足深度脱臭的要求。
1.2 臭气处理方法的选择
主要从投资成本、运行成本、除臭效果、技术成熟度和除臭技术在应用过程的不利影响等方面进行综合评判,选取合适的除臭技术。
从投资成本分析,新建除臭系统会增加整个项目的成本,而利用电厂锅炉进行焚烧时,只需考虑污泥干化地点到锅炉之间的管道成本,本项目利用玻璃钢材质风管进行输送,且两者之间的距离较短,成本投入较小。
从系统运行成本来看,活性炭法具有一定的使用周期,运行一段时间后,活性炭吸附效果下降,需定期更换活性炭材料,增加运行维护成本;生物过滤法在使用过程中也需定期更换填料。等离子法的电耗则相对较大;利用电厂进行焚烧臭气,工艺简单,电耗低,维护简单,处理效果明显且稳定。
从除臭效果分析,无论是活性炭法、等离子法、生物滤池法,还是氧化法,对臭气成分的处理具有选择性,对臭气浓度也有要求。对于锅炉而言,几乎不存在这样的限制,锅炉温度高达1000℃,废气中的臭气能完全被分解产生CO2和H2O。
从臭气处理成熟度上考虑,各种技术在臭气处理方面都有较多的应用,尤其是利用电厂锅炉对臭气进行焚烧。从除臭技术的不利影响来看,活性炭吸附需要考虑炭脱附,等离子法会产生臭氧污染,生物过滤法可能会因填料的腐化产生新的臭气污染,而利用电厂锅炉进行焚烧,臭气成分被彻底分解,不会产生新的污染问题,且在处理过程中不会对锅炉的原有系统产生不利影响。
综上,利用电厂的锅炉对污泥干化系统产生的臭气进行焚烧处理是较佳选择。
2 工程案例
2.1 工程概况
华东某电厂现役二、三期4×330MW燃煤机组,采用亚临界汽包锅炉汽轮发电、双曲线冷却塔-循环水冷却、电除尘-气力干除灰、水冷渣-链条式输送、石灰石-石膏湿法脱硫,该机组于2005年投运。
为满足电厂发展战略及当地环保需求,电厂接纳当地污水厂转运来的板框压滤污泥,其含水率在55%~65%之间。
根据当地污泥处理处置的要求,电厂规划建设2条污泥干化生产线,单条污泥干化生产线处理规模为每天100t含水率60%污泥。污泥消纳采用的技术路线:首先通过圆盘干化技术将污泥的含水率干化至35%,然后干化后的污泥输送至输煤皮带于燃煤混合后,作为燃料进入炉膛燃烧发电。
其中,圆盘干化系统由几个子系统组成,包括湿污泥存储与输送系统、干化系统、干污泥存储输送系统、干污泥上料掺配系统、蒸汽输送及疏水回用系统、废气收集处理系统、冷凝废水处理系统、循环冷却水系统及DCS控制系统。
2.2 圆盘干化系统臭气源分析
圆盘干化系统废气主要产生于3个过程:储存过程、输送过程及干化过程。首先,湿污泥料仓内的污泥存储过程中,发生消化反应,产生以NH3、H2S为主的恶臭气体,同时产生少量的醇类、胺类等有机臭气。污泥输送过程,由于污泥发生扰动,污泥与污泥之间裹挟的臭气被释放,成分与储存过程产生的臭气相似。
污泥干化过程中,产生的废蒸汽臭气浓度较高,成分较复杂,一方面污泥中原来含有的低沸点的臭气成分被释放;另一方面,高分子气体被分解产生含臭味的低分子气体。
2.3 圆盘干化系统臭气收集及处理工艺
整套系统以定点微负压和整体微负压相结合的方式进行臭气收集。
定点负压是在系统运行下,保证干化机内部-100~500Pa的微负压,湿/干污泥储存及输送设备内部微负压,避免臭气向周围环境逃逸。但是,在污泥卸料和输送过程中臭气无可避免地会从设备内逃逸到厂房内,故厂房内采取整体微负压设计,维持厂房内机械排风,自然进风,避免臭气进一步扩散到周边环境。结合现场情况,臭气的收集工作主要分为三部分。
部分:两条生产线的干化工艺尾气,通过除尘冷凝后通过同一台离心风机输送至锅炉前端的送风机入口。
第二部分:湿污泥卸料车间、污泥干化车间、湿污泥/干污泥料仓、湿污泥输送、干污泥输送等设备相对集中,利用同一离心风机将臭气收集并输送至锅炉前端的送风机入口。
第三部分:干污泥上料系统中污泥输送距离长度达300m,输送高度32m,利用同一台离心风机收集上料系统设备内部臭气,并将收集的臭气输送至锅炉前端的送风机入口。污泥干化系统产生的所有臭气送入锅炉进行焚烧处置。
2.4 圆盘干化系统臭气处理效果
根据现场测定,污泥干化生产车间周边环境无臭味逃逸,满足《恶臭污染物排放标准》恶臭污染物浓度限制要求。车间内有毒有害气体及粉尘等卫生条件满足《工业企业设计卫生标准》以及《工作场所有害因素职业接触限值》等相关标准。电厂大气污染物排放也符合相关标准要求。
3 结论与建议
3.1 结论
整个污泥圆盘干化系统可以将污泥的含水率从60%降至35%,各子系统稳定运行,同时干污泥输送系统的设计实现了长距离及较高高度输送,系统运行过程中厂房周边臭气排放满足相关 标准,厂房内臭气有效抽吸处理,保证系统运行时人员健康。
利用电厂锅炉对污泥在存储、输送、干化过程中产生的废气进行焚烧,可有效分解废气中的臭气组分,同时可节约电厂的投资及运行成本。另外,对于电厂的锅炉及超低排放环保设备的运行不会产生影响。
3.2 建议
厂房内部臭气收集效果具有一定的局限性,通过增加换气次数进行厂内臭气的收集有明显效果,但相应地会增加风机功耗,如果风机能耗有较大限制,则应严格控制系统设备的密封性和微负压状态,减少设备本体及连接件臭气的逃逸及无组织排放。通过本项目在运行过程中的调整,每小时8~10次换气量能达到 的效果。
利用定点抽吸方式,针对污染臭气源进行定点抽吸,能有效防止臭气向四周扩散,同时减少系统抽风量,降低风机运行能耗。