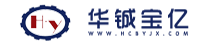
城市污水处理厂产生的污泥(含水率为97%)一般占到污水处理量的0.3%~0.5%。一座处理量为20×104m³/d的污水处理厂产生的湿污泥量将达到600~1000m³/d。湿污泥必须经过脱水后(含水率为75%左右)才能外运进行深度处理或填埋。
济宁市污水处理厂设计污水处理量为20×104m³/d,实际处理量已接近满负荷。采用AB工艺,B段的剩余污泥返回A段曝气池,A段的剩余污泥排到预浓缩池进行重力浓缩,然后直接进行离心脱水处理。因进水污染物浓度比设计值高,湿污泥产量达1400m³/d(含水率为96%~97%)。
污泥脱水分为自然脱水和机械脱水,其中机械脱水又可分为真空过滤脱水、压滤脱水和离心脱水。离心脱水机体积小,运转可靠,车间内臭气少,环境卫生,采用自动化操作,管理简便,生产能力大。离心脱水机对絮凝剂的要求很高,必须使用有机高分子聚合物(PAM)。对离心脱水机性能参数的正确认识以及合理筛选絮凝剂产品,是顺利完成污泥离心脱水的关键。
1 离心脱水机的工作原理及性能参数
1.1 离心脱水机的构造及工作原理
离心脱水机主要由转鼓和螺旋输送器组成。转鼓在高速转动时产生一个强大的离心力。因污泥颗粒比水的密度大,使污泥颗粒沉降在转鼓内壁上形成固环层,水分在固环层内侧形成液环层。固环层的污泥在螺旋输送器的推动下,被排出转鼓形成泥饼,液环层的水分由堰口溢流出转鼓,形成分离液,这样就实现了固液分离。进入离心脱水机的污泥沉降速度与d(颗粒直径)、s-sl(两相物体的密度差)、w2(w角速度)、r(颗粒到回转中心的距离)都成正比,即颗粒直径越大、两相物体密度差越大、转速越高、转鼓直径越大,物料沉降的速度越快。向污泥中添加絮凝剂,使小颗粒污泥聚集成较大的颗粒,提高颗粒直径,则污泥分离得越快越彻底。转鼓直径r不能过大,否则机器的稳定性难以保证,因此通过提高r来提高处理量是有限的。沉降速度与污泥粘度(η)成反比,污泥粘度越高,越不易脱水。
1.2 主转速
主转速即转鼓转速。主转速直接决定了污泥在离心机内部受到的离心力大小,决定了污泥的沉降速度和处理量,主转速上升能够提高污泥的分离速度,获得更为清澈的分离液,分离后污泥更紧密牢固,排出离心机的泥饼更干,同时由于增加了沉降速度,使得离心机的污泥通过能力增加,处理量也随之上升。
但过高的主转速也会带来不利的一面。直接的表现是增加了不必要的转鼓电机功耗,所以离心机没必要在极高转速下运转,只要达到所需的处理效果就可以了。过高的主转速产生了过高的离心力,随之产生了过高的污泥沉降紧密度,增加了螺旋推料的负荷。所需要的主转速高低主要与泥质有关:对活性污泥、泥龄较长的污泥需要高的主转速,初沉污泥需要低的主转速。该厂的离心机主转速一般在1900~2600r/min之间进行相应调整,在保证处理效果的前提下,应尽量降低能耗。
1.3 差速
螺旋的推料差速作用是将转鼓分离沉降好的泥饼连续不断地推向离心机排渣口,使之排出机外。通常螺旋推料的差速比较小,一方面可有效抑制螺旋对水的扰动,另一方面又延长了沉降污泥在离心机内部受压缩的时间,这样才能得到较干燥的泥饼。差速越低,泥饼被推出离心机的速度越慢,对清液的排放形成了扰动,泥饼向清液的渗透面加大,泥饼的含固率提高,但是清液比较浑浊,所以固体回收率降低。差速高时,泥饼被推出的速度加快,泥饼在离心机内的压缩时间缩短,泥饼含固率降低,但能够减轻对清液的扰动,可得到较清澈的分离液,使固体回收率提高。
泥饼的干度和分离液的清澈度是互相矛盾的。调试离心机的目的就是找出兼顾两者平衡点的差速。一般脱水机的差速在2~35r/min范围内调节,初沉污泥高一些,活性污泥低一些。该厂离心机的差速在4.0~5.5r/min之间调整,即可取得较好的处理效果。
1.4 液池深度
液池深度是污泥在离心力的作用下,在转鼓内壁形成的固渣和液体的混合圆环的厚度。因为存在固液密度差,固体在外,液体在内,越往圆环内侧,液体越清澈,但固渣更湿。若液池深度减少,固渣更干,但分离液更浑浊。
离心机液环层厚度一般为50~150mm,具体取决于离心机的规格及进泥泥质。初沉污泥可相对薄一些,以便在保证高固体回收率的前提下,尽量提高泥饼的含固率。活性污泥脱水时,液环层应相对厚一些,否则很难保证一定的固体回收率。混合污泥脱水时,液环层厚度介于二者之间。
1.5 进泥量及进泥含固率
每台离心机都有一个设计进泥量和设计固体物浓度,实际运行中若超过该值,离心机会受到损坏,因而运行中应严格控制离心机的进泥量及固体物浓度在允许的范围内。当进泥含固率升高时,要相应地降低进泥量,以获得较佳的处理效果。离心机使用中可找到一个较佳投泥量,当超过该值时固体回收率和泥饼含固率都会降低。该厂离心机设计进泥量为30m³/h,实际只能达到25m³/h,高于此值则处理效果就会下降。另外,离心机的处理量会随着机器的老化磨损而逐渐降低。目前该厂离心机处理量已下降到20m³/h。
2 絮凝剂的合理选择
离心机使用的阳离子PAM必须经过严格筛选,才能上机使用。具体做法:烧杯试验→上机试验→批量使用。絮凝剂药液的浓度一般为0.1%~0.5%,针对某一产品可先参考其在其他污水厂的使用情况。
2.1 烧杯试验
若配制浓度为0.3%的药液,取一烧杯装入1L的清水,称取3g絮凝剂干粉,缓缓倒入烧杯中,边倒边用玻璃棒快速搅拌(或使用专门的搅拌器以80~100r/min的速度搅拌),搅拌5min,停1min,约0.5h后药品就能充分溶解,呈无色透明,用玻璃棒搅拌会感到有明显的阻力。若把玻璃棒提出水面,可见长15cm左右的拉丝。取20、22、25mL新鲜污泥各一烧杯,用针管量取1mL药液注入20mL的烧杯中,边加药边搅拌。合适的药品在十几秒钟内会有明显效果,污泥成直径为3cm左右的团状,结合紧密,泥水界面清晰,分离的水中有很少量浮泥,则该药品可以上机使用。不同的药品单位投量处理的污泥量越多,效果就越好。若污泥基本不能成团,该药品就不能使用。当然还要继续试验22、25mL的污泥量,寻找较佳投药量。
2.2 上机试验
该厂的配药机容积为4m³,分3级,逐级溢流。若配制浓度为0.3%的药液,所需絮凝剂干粉至少12kg才能装满药箱。将浓度值输入操作面板,配药机就自动吸药和加水,靠一个变频器控制的电机带动螺旋送药,电磁阀控制加水量,从而达到所要求的浓度,配好的药液需稀释后加入离心机。药液配好熟化30min后就可以开启脱水机,将主转速、差速设至经验值,然后进药、进泥,根据出泥情况再调整主转速、差速,直到泥饼含固率为20%左右,分离液的SS为500mg/L左右(用肉眼观察泥饼成拳头般大小,有弹性,分离液中有很少的泥点),这样的效果就可以达到使用要求。
2.3 批量使用
对于上机试验合格的药品,就可以考虑批量购入用于生产。这一过程中要进行细致调整,计算出干污泥投药量。若计算出的干污泥投药量<5kg/t,该药品即合格。干污泥投药量越小,该药品处理效果越好。还要计算干污泥处理成本,相同处理效果的絮凝剂产品,干污泥处理成本越低越好。
另外,絮凝剂的用量受温度影响很大,就干污泥投药量来说,冬季要比夏季高出近30%。
3 运行中的常见问题
在实际运行过程中,有时脱水后的泥饼突然变稀。造成这种情况的原因及解决方法如下:
(1)检查絮凝剂配制系统。几种可能的情况分别是:不配药造成药箱没药;只配水不配药,造成药液浓度过低;未及时添加絮凝剂造成原料短缺。
(2)检查稀释水系统。进泥含固率过高时要多加些稀释水,否则少加一些。该厂的稀释水量在1.0~2.5m³/h之间调整可达到要求。
(3)检查离心机主转速、差速是否正常。
(4)进泥浓度是否太低,例如含固率<2%。若浓缩池的污泥层太薄,应立即停运离心机,待浓缩池污泥含固率提高后再生产。
离心脱水机是个敏感的设备,泥质、絮凝剂浓度稍有变化,就会出现污泥随地流的情况,在生产运行中需要运行人员细心观察,加强管理,不断总结生产运行经验。