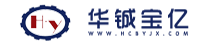
1 前言
随着我国石油产业的不断发展,石油开采及石油炼制过程中同时产生的含油污泥对生态环境及生产开发造成了严重的危害。
炼厂所产生的污泥主要由气浮浮渣及池底油泥组成,一般为黑色粘稠浆液。与一般市政污泥相比,具有年产量大、含水量高、固液难分离的特点。
根据环境保护及三废治理的要求,必须对含油污泥进行安全、高效的处理。污泥脱水可以分为自然脱水及机械脱水,而离心脱水属于机械脱水中的主要方法。卧式螺旋离心机因处理效率高、处理剂耗量少、占地面积小等优点成为处理含油污泥的首选设备。
2 污泥离心机的工作原理及运行参数
2.1 卧式螺旋离心机的工作原理
污泥从进料管进入,经过螺旋推进器达到转鼓。污泥在转鼓中受到离心力的作用,其中污泥中的液相在转鼓中形成液相层,固相被运到转鼓内壁上。固液两相在转鼓的圆柱形部分进行分离。转鼓大的一端装有可调节高度的液位挡板,液相从液位挡板经分离液出口流出。固相则由转鼓小的一端的排渣口排出。
2.2 离心机的运行参数
2.2.1 进泥量
进泥量及流入固体量是离心机的两项重要参数,当进泥量超过设定极限值时,固相和液相的动态平衡将被打破。这将导致离心机扭矩过大,严重时会对离心机造成损害,导致超载停车。因此,应当严格控制离心机的进泥量及固体流入量,并选择合适的进料方法。
2.2.2 转速
离心机转鼓转速由变频器控制,而转速直接影响了离心机的分离因数。一般来说,污泥中固相颗粒密度越大,颗粒越大,需要的分离因数越低;固相密度越小,颗粒越小,需要的分离因数越高。
通常来说,离心机的转速越大,其分离效果越好;但是过高的转速会使离心机扭矩增加,缩短其使用寿命,而且高转速会使离心机的振动和噪声也随之增大。
2.2.3 转速差
离心机的螺旋与转鼓之间的相对转速称为转速差。设定一台离心机的转速差为△n,那么可以认为这台离心机的螺旋相对于转鼓与△n的速度将污泥中的固相输送出离心机。
在进泥量相同的情况下,转速差越大,则污泥中固相在离心机中的停留时间越短,离心机的处理能力越大。但是过大的转速差会使液环层对固环层的扰动增大,固环层中的固相可能重新被泛至液环层,导致离心机的固体收率及泥饼固含量降低;反之,转速差越小,离心机的固体收率及泥饼固含量都将提高,但是降低转速差会使离心机的处理能力下降,而且当转速差小于一定值时,会使离心机中的固环层大于液环层,增加了离心机的阻力,严重时会因扭矩过大造成离心机的损坏。因此,应当根据不同污泥的浓度对转速差进行调节。
2.2.4 液环层厚度
当进泥量一定时,液环层的厚度决定了污泥在离心机中的分离时间。一般来说,液环层厚度的增加有利于提高污泥的固体回收率,但是会增加泥饼中的水含量。反之,液环层太薄会使分离液浑浊,固体回收率降低,可以通过调整液位挡板高度来控制液环层的厚度。
3 离心机参数优化
3.1 离心脱水系统现状
某厂污泥离心脱水系统中的离心设备为意大利贝亚雷斯公司生产的2台离心脱水机,处理量4~8m³/h,干固体负荷为500kg/h。离心机运行参数如下:
转速:3200r/min
进泥含固率:2~2.5%
差速:6r/min
液位挡板高度:148mm
此参数为厂家提供的经验参数。当离心机以该参数运行时,在处理原有陈泥(上游沉积时间长、含固率高达10%的污泥)时效果较好,产泥含水率在75%左右(产泥含水率要求小于85%)。但是该参数可调节余量小,设备震动大,处理量小。之后处理常态化新泥(上游沉积时间短,含固率低2%~4%污泥)时效果较差,产泥含水率在83%~88%,多数情况下产泥含水率达到85%以上。
3.2 参数优化试验
为达到污泥处理目标,以离心机处理量6m³/h为基准,分别对进泥含固率、差速、转速、液环层厚度等进行了考察。
3.2.1 进泥含固率
通过控制污泥浓缩时间对进泥的含固率进行了调整,并且在离心机处理量6m³/h,运行参数为转速3200r/min,差速为6r/min,液环层控制采用148mm液位挡板的情况下记录了离心机处理效果,其结果如下表所示:
浓缩时间/天 | 进泥含固率/% | 干固体负荷/(kg/h) | 干泥含水率/% |
1 | 1.8 | 211 | 87 |
2 | 2.6 | 247.94 | 84 |
3 | 3.3 | 314.7 | 80 |
4 | 3.0 | 372.27 | 76 |
7 | 4.4 | 420 | 72 |
由上表可以看出,随着污泥含固率的升高,产泥含水率呈下降趋势,且效果显著。当进泥含固率达到4.4%时,离心机的干固体负荷为420kg/h,小于离心机的极限值500kg/h,因此进泥含固率应保持在4%左右。
3.2.2 离心机差速
当进泥含固率为4%时,对离心机转速差与离心机扭矩之间的关系进行了分析。扭矩是反映离心机工作状态的数据,扭矩过大说明设备负荷过大。一般来说,离心机日常运行过程中扭矩一般要保持在设计扭矩的30%左右,离心机的转速差应大于8r/min。
在设定处理量6m³/h,进泥含固率为4%,离心机转速为3000r/min,液位挡板高度148mm的条件下,通过调节离心机差速,观察干泥含水量的变化。
差速为13r/min时,干泥含水率基本达到目标值,在此基础上应当尽量降低差速,结合差速与扭矩的关系,确定离心机合理差速为9r/min。
3.3 离心机转速及液环层厚度试验
为了确定离心机转速,在进泥含固率为4%,转速差9r/min,液位挡板高度148mm的条件下,缓慢降低转速,记录了转速与干泥含水率之间的关系。
当转速低于2400r/min时,干泥含水率达到80%,但是分离液比较清澈,可以适当降低液环层厚度进行试验。综合考虑液环层厚度的因素,将148mm的出水堰挡板调更换为146mm后继续进行实验,实验数据如下表所示:
转速/(r/min) | 液位挡板高度148mm | 液位挡板高度146mm | ||
干泥含水率/% | 分离液状态 | 干泥含水率/% | 分离液状态 | |
1800 | 86.8 | 浑浊 | 84.6 | 浑浊发黑 |
2000 | 85.0 | 比较浑浊 | 81.6 | 浑浊 |
2200 | 82.1 | 比较清澈 | 80.3 | 比较浑浊 |
2400 | 80.1 | 清澈 | 79.5 | 清澈 |
由上表可以看出,堰挡板调更换为146mm,转速在2000r/min时,干泥含水率为81.6%,可以满足要求,但是分离液浑浊。综合考虑固体回收率和优化原则,确定合理的转速为2200r/min,出水堰挡板高度为148mm。
4 结论
通过对某厂污泥脱水系统进泥含固量、转速差、转速及液位挡板高度进行考察,得到了优化后的运行参数,满足了该厂离心污泥脱水设备工艺要求。结果表明,经过优化后该厂污泥处理量达到6m³/h,处理后干泥含水量小于83%,满足污泥后续处理的需要。分离液清澈,达到水处理要求且优化后离心机振动、能耗明显降低。
污泥脱水是一项复杂的工作,加药量、污泥性质、温度等因素都会对处理效果造成很大的影响,不同的情况需要不同的处理方式。本文仅仅是提供了一种参数调节的方法与思路,更重要的是需要在日常的工作中不断总结经验、调整参数、改进操作,在污泥处理效果、经济能耗及适用性之间寻找一个符合实际生产的平衡点。