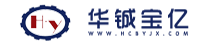
生物接触曝气法是20世纪开创的一种较为成熟的污水生化处理工艺,该工艺具有容积负荷大、耐冲击、适应能力强等优点。随着废水排放要求的日趋严格,废水中的有机物去除率也相应提高,活性污泥数量同比大幅增加,使得污泥处理处置问题日渐凸显,成为废水处理面临的一个新难题。
1 工程概况
南通醋酸纤维有限公司环境监测中心醋酯废水处理装置设计处理废水量为15000t/d,设计进水COD为2000~4000mg/L,运行实际处理废水量约为10000t/d,经过三级曝气处理,出水水质达到《污水综合排放标准》(GB 8978-1996)三级排放标准,平均COD为150mg/L,平均BOD5为48mg/L。污泥处理则是将二沉池污泥经浓缩池浓缩后,采用离心脱水-干化综合处理方法进行处理,脱水后污泥含水率约为88%,部分脱水后污泥经干化处理后得到含水率为7%的干污泥直接外运焚烧,剩余湿污泥外运与煤粉混合后焚烧。目前,污泥处理工艺主要存在的问题是外运污泥多。随着公司的增产,公司的外运污泥量从15年的3600t增长至目前的4700t,污泥处理压力巨大。
2 存在问题及改进目的
2.1 二沉池排泥负荷波动大,导致污泥浓缩效果不佳
浓缩池出水含泥浓度平均值介于3.0%~3.5%。系统产泥由二沉池进行初步沉淀后至浓缩池浓缩。由于上游负荷影响,浓缩池进泥负荷波动较大,浓缩池上清液厌氧上浮情况经常发生,污泥停留时间过长,增加了浓缩处理难度,污泥浓缩效果差,会影响废水生化处理的稳定,导致总磷、COD的升高。
2.2 污泥脱水设备故障率高,稳定性差
该厂污泥脱水系统于2002年投入运行,采用两台处理量为10m³/h的阿法拉伐离心脱水机,经离心脱水处理后,含固率仅为12%左右,与设计含固量15%存在差距。脱水后的含固率偏高,导致湿污泥量较大。这样不仅增加了湿污泥直接外运处理量,而且增加了后续污泥干化的处理难度,提高了整个污泥处理系统的运行成本。
2.3 机械脱水后干污泥转化率低
干污泥转化率低的问题主要归结于两个方面。
2.3.1 存在污泥干化进料量不足的情况
离心机房距离新建污泥干化车间约80m,脱水污泥自离心机输送至干化间的距离长。南通醋酸纤维有限公司污泥黏度高且含残渣多,污泥输送困难。脱水后的湿污泥通过一台功率为3kW的污泥输送螺杆泵输送至干化的湿污泥料仓,橡胶定子容易磨损,导致螺杆泵出力不足。除此之外,废水系统负荷较低时,浓缩池排泥量少,在调配湿污泥时具有滞后性,未预存干化湿污泥用量,导致干化处理负荷不能够得到充分满足。
2.3.2 存在干化装置处理负荷偏低的问题
运行方面,进干化湿污泥含水量不稳定,布泥效果差,造成干化不完全,引起干化频繁故障。设备方面,污泥干化采用干化腔内空气循环对湿污泥进行蒸发处理,4kg饱和蒸汽作为热源,32℃的冷却水作为冷凝水源,对腔内空气二级加热后冷凝除去湿污泥中水分。目前污泥干化的干污泥生产能力约为1.1t/d,含水率仅有10%,热值约为12473.8kJ/kg,适宜用于热电站的焚烧处理。干化目前处理的湿污泥量仅占总泥量的43%左右,远不足以完全处理目前的系统产泥,导致总污泥外运量较多。
随着 对三废处理要求的不断提高,南通醋酸纤维有限公司积极落实节能减排的方针。对现有污泥处理工艺设备进行优化改造,尽可能减少公司的污泥外运总量,是本次工艺设备优化的主要目的。
3 污泥处理系统工艺技术改造
3.1 优化污泥处理分配
针对1#、2#二沉池排泥问题,充分利用现有设施对工艺管线进行了优化,另增一根工艺管道进入浓缩池,实现1#、2#二沉池单独排泥进入浓缩池,互不干扰,保证排泥管道的畅通。同时,为应对污泥负荷变化,充分利用原储泥池,增加二沉池至储泥池的管道,缓解高峰期对污泥的冲击,防止污泥二次进入废水系统。
南通醋酸纤维有限公司充分利用2014年实施的PI实时数据库系统,根据前端进水BOD负荷和除磷剂、助凝剂加药情况,运用Exce和PIdatalink软件制作污泥估测PI应用,估测当日和次日产泥情况,辅助岗位辨识出污泥产生的波动情况,根据系统剩余污泥量合理进行排泥、回流,做好脱水后污泥外运和干化分配优化。
3.2 提升污泥脱水系统稳定运行水平。
将离心机房搬迁至污泥干化间东侧,缩短了污泥输送距离,消除了由于远距离污泥运输引起的脱水污泥至干化通道不畅的问题,提高了污泥运送设备的稳定性。将离心机房与干化车间进行集中,也便于异味气体的集中收集与处理。对老旧的阿法拉伐离心脱水机采用ABB变频器进行自动化升级改造,实现一键启动和一键清洗的功能,同时增加一套PAM自动加药系统。离心机房的搬迁项目提高了污泥处理系统运行的稳定性,解决了湿污泥输送至干化的瓶颈问题,有利于进一步提高干污泥的转化量。
主要新增设备有三。一是增加一台处理能力20m³/h、功率30kW的贝亚雷卧式污泥离心机,以2200r/min、40Hz、差速6r/min的方式运行,出泥含水率为82%左右。二是增添一套6m³的絮凝制备加药系统,其间需要配备絮凝剂加药泵3台,流量为0.4m³/h,扬程为0.2MPa,功率为0.75kW。三是增加一台功率为2.2kW的螺旋输送机,代替原螺杆输送泵。
3.3 提高污泥干化处理能力
3.3.1 将干化湿污泥仓的同步五轴混合器改为异步三轴混合器
干化采用挤压式面条机进行布泥,进料湿污泥的混合均匀情况会直接影响布泥后蒸发面积的大小。原五轴混合器采用单电机驱动,易造成湿泥仓内局部过湿,不便于布泥成型,导致干污泥产量不稳定。五轴螺杆间间距过小,互相挤压,引起螺杆变形,增加了故障率。在原设备基础上,将五轴混合器改为三轴混合器,单电机驱动单根混合螺杆,实现混合器螺杆异步驱动,混合效果更佳,面条机的出泥压力能够稳定保持在135kPa左右。
3.3.2 对干化腔空气换热器进行扩容改造
干化腔换热器主要分为两个部分,一部分是对蒸发后的空气进行先冷凝后预热至90℃左右的空气热交换器,换热器面积为180㎡,另一部分则是对空气进行二次升温至150℃左右的蒸汽热交换器,换热器面积为480㎡。为提高干化处理能力,更换空气换热器,换热面积增大至260㎡,用26℃的冷却水源代替原冷却水,提高冷凝换热效果,同时增开空气换热器人孔,便于换热器定期清洗。改造后,干化腔湿度从原22%左右降低至目前的18%左右。
4 结论
上述一系列的污泥系统改造已于2019年6月全部完成,系统投入运行后,效果较好,浓缩池出泥浓度能够稳定保持在4%以上,脱水系统出泥的含水率降低至83%左右。干化设备干泥产量提高至1.55t/d,占产生污泥总量的58%左右,可直接送至热电厂进行焚烧处理,大大降低了污泥的处理费用,不仅减少了三废的排放,而且取得了良好的经济效益,年减少污泥外运量约2160t,节约费用127万元。