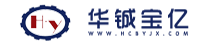
随着工业机械化程度的日益提高,工业噪声污染严重,不仅直接给工人健康和社会环境带来危害,而且还会影响产品质量、使用性能和年限。离心机在高速回转中完成非均相分离和过滤工作,与一般回转机械比,由于转速高,振动和噪声问题显得更加突出。要降低离心机的噪声和振动,除了从传播途径上采取隔振、隔声和吸声等手段外,还应分析找出产生振动和噪声的主要部位和原因,提出改进措施,从根源上解决振动和噪声问题,对提高离心机产品质量和技术水平具有重要的指导意义。
LW-380D并流型卧式螺旋卸料沉降离心机是我国中小型酒精企业进行糟液固/液分离的理想设备,是一种节能型卧螺离心机,单位处理能力可达9m³/h,脱水后稳定的湿糟含液率为75%~80%,有利于二次回用,可使每吨酒精节约10t投料水,且回用水温度一般为60℃。该机的转鼓直径为380mm,转鼓长度为1140mm,转鼓转速为3550r/min,主要由转鼓、螺旋、差速器、机壳、机座等组成,并由电磁调速电机驱动,是一个高转速、多声源的设备,实测机组噪声声压级为91.0dB(A),声功率级为104.9dB(A),振动烈度为11.2,振动和噪声都比较大。因此有必要降低产品的振动和噪声,同时也是提高产品质量和可靠性的一个重要研究方向和内容。
1 振动、噪声测量分析软件系统
噪声测量采用B & K声级计,测量范围为10~140dB。振动则是采用B & K测振仪,频率响应在0.3Hz到1kHz或15kHz之间可以测量位移、速度、加速度,测量轴承座3个方向的振动速度有效值,在规定测点和方向上测得的振动速度有效值作为被测机器的参数,给出其振动烈度值。声强测量分析是采用两只距离相近的传声器同时感应声压信号,利用快速傅里叶分析把声强和两传声器信号的互谱的虚部相关联。
对于机械噪声的测量,一般要确定噪声源及声源所辐射的噪声特性。其测量方法主要取决于声源、环境类型和噪声特性等。在离心机减振降噪的技术研究中,除使用了常规的振动、噪声测试分析仪器和方法外,还使用了某院开发的振动、噪声测量分析软件。该软件可以进行振动与噪声的测试数据分析,包括谱分析、声强测量分析和试验模态测量分析等多功能处理系统,满足了通用机械振动噪声分析的需要。
(1)声强测量分析。用于测量分析某点的声强,得到该点的声压级,声强级的量值,线性谱,A计权后的频谱、倍频程及1/3倍频程谱图等。
(2)声功率测量分析。除具有声强软件包的功能外,可测量某台机器或机器的某一部分的声功率级,得到线性的声功率级,A计权声功率级、倍频程及1/3倍频程声功率级。
(3)三维声强图及等声强图分析。可得到机器的三维声强图及等声强图,由图形直观地显示出各点噪声的大小。
(4)单通道FFT分析。对振动、噪声信号进行FFT分析,可得到功率谱函数。
(5)双通道FFT分析。可用于振动、噪声信号的FFT分析,得到自功率谱、互功率谱分析及噪声与振动信号之间的依赖关系的相干分析。
2 噪声源分析及控制措施
根据机械噪声源的不同,噪声划分为空气动力性噪声和机械性噪声。空气动力性噪声主要是由高速气流、不稳定气流等气流与物体之间相互作用产生的;机械性噪声主要是因为固体的振动而产生的。
2.1 空气动力性噪声分析
为了分析离心机的噪声源,首先使用声强法对机组噪声进行测试分析,测定出机组噪声频谱。可以看出:噪声明显分为两段,即500Hz以下的低频段,这一段以350Hz分量较大,为87.5dB(A);第二段为2000~3500Hz之间的高频段,高峰为91.0dB(A),频率为2200Hz。为了进一步分析声源,在测某点噪声的同时,测其对应的轴承部位的振动,并进行相干分析,可以确定其低频段基本上是由振动引起的,而高频段则可能是高速旋转的转鼓所产生的空气动力性噪声。
为找出机组空气动力性噪声产生的根源,进一步判断分析的正确性,将机壳上盖去掉,暴露转鼓,以转鼓轴线方向为X轴,从转鼓大头端轴承起,到转鼓小头端轴承,共取8个测点位置,在与水平面成0°、30°、60°、90°的表面上取4个测点位置,共取32个测点,测出离心机顶面的三维声强图和等声强图。可以看出:中间共有3个明显的高声强区,分别对应于转鼓溢流孔处和大头法兰、转鼓柱、锥联接法兰和转鼓小头端的差速器部位。
转鼓是高速转动的柱锥体,圆周线速度达82m/s。外表面上的螺钉头和凹的螺钉孔洞产生的空气动力性噪声由两部分组成:16个柱锥法兰联接的圆形螺钉头,在转鼓的高速转动下打击周围的空气介质,引起气体的压力脉动而产生噪声;同时在圆柱的迎风面,压力高、流速较大,而在圆柱的背风面,压力和流速都急剧下降,形成涡流区,因而在转鼓转动的过程中,使得周围的空气介质产生压力脉动而形成噪声。
另外,气流流经圆柱形螺钉头的表面时,在表面上形成附面层,这些附面层在圆柱的背风面脱离圆柱表面而形成旋涡。所产生的紊流附面层及旋涡与旋涡分裂脱体,同时在转鼓大头端的螺钉孔洞也将产生旋涡,而产生涡流噪声。
旋转噪声和涡流噪声的各阶倍频分量比较强。圆周速度越高,则噪声越大。而分离因数决定了圆周速度,降低圆周速度不现实,但可以将转鼓外表面做到尽可能的光滑,以减少对周围空气的扰动,避免涡流的产生。因此,将转鼓大头法兰盘上的16个螺钉孔填平,测量靠近转鼓大头端部的8个测点的声强。可以看出,转鼓大头部位噪声明显下降。再将柱锥联接法兰处16个螺钉头之间用填料填平,外部形成光滑表面,改进结构设计后,整机噪声降低了6dB(A),噪声声功率级降至98.9dB(A),降噪效果显著。
因此建议在离心机结构设计中,减小转鼓大头螺钉孔与螺钉头装配间隙,保证转鼓大头端面平整,避免产生涡流噪声;同时将柱锥联接法兰的螺钉改为埋头螺钉,保证外圆平整光滑,降低空气动力性噪声。
测量中还发现机组传动部分噪声较大,从频谱图中看出高频噪声仍较突出。为诊断该部分的噪声源,采取了分步运行法,首先单运行脱离开的电机,在2000~3500Hz之间无明显的峰值,可排除电机的影响;再将等声强图向差速器方向延伸,增加1组测点。差速器是由摆线轮组成的齿轮箱,一般齿轮噪声频率较高,将差速器皮带轮的三角带去除,让螺旋和转鼓同步运行,齿轮箱不工作,发现噪声谱图无变化,说明并非齿轮箱影响。而差速器两端各由16只内六角螺钉将法兰与壳体联接,这32支螺钉也是高低不平,部分螺钉头露出表面,在高速旋转中产生气流噪声,覆盖住这部分螺钉头形成平滑过渡表面后,该部分的噪声也得到了相应控制。
综上所述,高速旋转体的表面光滑过渡,对控制空气动力性噪声作用明显。仅对转鼓体和差速器表面采取措施,使得机组噪声由104.9dB(A)降至98.7dB(A),降低了6.2dB(A)。机组噪声声压级也降至84.4dB(A),效果显著。
2.2 机械噪声分析
消除高频噪声分量峰值后,500Hz以下低频噪声显得突出,其中350Hz频率分量噪声为87.5dB(A)。为进一步分析,在测定噪声的同时测定该处的振动信号,将两路信号同时采集进行相干分析,频率为62.5、275、350Hz分量的相干系数都在0.85以上。说明低频噪声基本上是由振动产生的,必须采取相应措施降低机组振动,才能进一步降低机组的机械噪声。
3 机组振动分析与控制措施
按照分离机械振动标准,卧式螺旋离心机振动是以转鼓两端的轴承座振动作为考核指标。取离心机轴向为X轴,水平方向为Y轴,垂直方向为Z轴,转鼓大头端轴承编号为1,小头端轴承座编号为2,进行轴承座振动速度有效值测量。两轴承座振动烈度均为11.2,62.5Hz的分量较为突出。主频分量为59.5Hz,则可确定62.5Hz即为转鼓同步的分量,说明是由转鼓不平衡产生的振动,因此,需对转鼓重新进行动平衡,以降低机组振动。
3.1 转鼓动平衡
卧式螺旋离心机转动体由转鼓体和差转速为20~25r/min的螺旋两部分组成。测量轴承座的振动时测振仪的指针摆动较大,周期为2s多,与螺旋和转鼓的转速差为20~25r/min相符,说明转鼓和螺旋均存在不平衡。对于这种复合转子,将转鼓与螺旋分别进行动平衡,采用振动分析方法来进行试平衡,即先让螺旋与转鼓同步运行,确定整个转动体的不平衡量,然后转动螺旋,使之与转鼓相差不同的角度,分别确定转鼓与螺旋的不平衡量。经过反复分析,确定转鼓小头端的不平衡量,在转鼓小头端法兰盘上配重半径为124mm处增加质量40g,以此为0°位置,在差速器上半径为63mm、与0°位置成135°处去除质量16g,在螺旋大头端配重半径为152.5mm、与0°位置成180°处两次焊接质量块59.5g( 次为44g,第二次为15.5g),使得整个机组振动明显下降。可见采用振动分析手段,达到了预期减振效果。若采用高精度的动平衡机对转鼓和螺旋分别进行高精度的动平衡,机组振动还会降低。
3.2 机组的隔振降噪
离心机主机和电机共用支承钢板底座,这种结构不仅要保证底座具有足够的刚性和质量,而且可适当地加筋板,以增加底板刚性。另外机组支承钢板下配置8只JG3-4减振器和1只JG3-6减振器。考虑到各减振器需均匀受力,按隔振理论,应使减振器的刚度中心、离心机的挠力中心和整个机组的重心在同一垂直线上。但由于机组形状限制,难以保证3个中心的重合,也影响了机组的振动。测得各减振器的压缩量相差11mm,说明各减振器受力不均。为此在距机组出渣斗旁减振器250mm处增加1只JG3-4减振器,使得各减振器压缩量之差不超过1mm,机组振动得到改善,振动烈度由11.2降至4.5以下。
4 结论
在卧螺离心机减震降噪技术研究中,除使用常规的振动、噪声测试分析仪器外,还采用了振动、噪声测量分析软件以及谱分析和试验模态测量分析等技术,对产品进行了较全面的振动、噪声分析,找出了振源和声源,并在结构上提出了相应的改进和控制措施,使得机组噪声声功率级由104.9dB(A)降至98.7dB(A);声压级由91.0dB(A)降至84.4dB(A);振动烈度由11.2降至4.5以下,效果显著,实现了产品减振降噪的预期目标。
此项技术对分离机械行业具有普遍性的指导意义,可推广应用于各类离心机。建议在离心机产品整机和零部件的结构设计上都应注意减振降噪问题,如采取减振弹性基础,对动、静零部件间的间距、布局、开孔大小和位置以及多转子的转鼓复合振动都需 的计算和试验等措施,同时还应重视加工、装配、动平衡精度、配套件精度与质量等,实现机组减振降噪目标,为离心机的减振降噪及结构设计优化提供指导,研究成果具有良好的社会效益和经济效益。