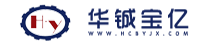
1 工程背景
1.1 污泥处理工艺
绍兴污水处理厂的物化污泥和生化污泥集中送至污泥均质池混合后分配到污泥浓缩池,经浓缩后污泥含水率降到96%左右。浓缩后污泥通过潜污泵输送到储泥池,由螺杆泵将污泥与药剂输送到带式压滤机或离心机脱水,脱水后污泥含水率下降到80%左右,再通过G型螺杆泵、柱塞泵送到料仓,通过车辆运输到污泥发电厂进行无害化处置。
1.2 污泥处理设备
污泥处理的主要设备为带式压滤机和离心机,其中带式压滤机27台、离心机22台。单台带式压滤机的处理量为14m³/h,按22开5备计,总处理量约为7400m³/d,产生泥饼约1500m³/d。二期污泥处理2台760系列的离心机,单台处理量为45m³/h,按1开1备计,处理量约为1080m³/d,产生泥饼约200m³/d。三期污泥处理20台530系列离心机,单台处理量为30m³/h,按14开6备计,处理量约为10080m³/d,产生泥饼约2000m³/d。
1.3 实际运行情况
污泥处理设备在运行过程中产生了一些问题,其中二期2台进口离心机问题较为突出。该离心机于2003年安装运行,随着时间的推移,机器部件磨损加剧、控制系统元器件老化严重,离心机工艺指标远达不到设计要求。
2 进口离心机主要问题及优化改造
2.1 存在的主要问题
二期离心机运行中存在的主要问题见下表:
主要问题 | 造成后果 |
上清液管出水不畅 | 离心机上清液管因处理的污泥中含有较多的Fe2+、药剂而具有较强的黏度,并且有较多气泡产生,造成离心机出水不畅,上清液停留在离心机转鼓中,同时也会进入另外一台离心机的转鼓里,造成离心机扭矩过高和脱水机故障。 |
离心机电气跳闸多 | 离心机的控制柜变频器、程序模块老化严重,控制系统故障率高, 造成离心机经常性报警停机 |
离心机振动大 | 离心机运行中由于磨损和轴承缺油造成转鼓旋转不平衡、轴承卡死,使离心机振动加大 |
离心机转鼓积泥,扭矩高 | 离心机转鼓内积泥后,螺旋无差速,不能将污泥从转鼓内排出,出现无差速故障和过扭矩故障,导致离心机故障停机 |
2.2 解决办法
2.2.1 上清液出水不畅问题的解决
污泥处理二期离心机因受房屋高度限制,安装位置相对低下,下水管的落差不到2m,而且下水需经过200m的DN300出水管输送到提升泵房,造成离心机上清液出水不畅,管内污泥堵塞使污泥处理量下降,严重影响了离心机的正常运行。为保证离心机的正常处理效率,增强离心机的运行稳定性,特提出污泥处理二期离心机出水改造方案,共进行了两次改造。
次改造是在离心机房外侧设置中转池,将2台离心机出水总管引入中转池,池内安装2台潜污泵,正常时1用1备。改造完成后离心机投入运行,发现仍存在两个问题:一是由于中转池较浅,泵机的自动控制液位上下幅度小,泵机启停频繁;二是泵房液位浅造成气泡封堵在管道内,使离心机出水管运行一段时间后仍然堵塞,同时两台离心机的出水管相互干扰,影响正常运行。
第二次改造是在现泵房侧再增设一座比原泵池深1.5m的泵池,将2台潜污泵移装到深的泵池中,使运行液位通过潜污泵浮球自动控制在离心机出水管口之下,管道内的气泡全部流入泵池,同时将两台离心机的出水管分开,分别接入泵房中。
通过二次改造,彻底解决了离心机上清液出水不畅的问题,使离心机能同时满负荷运行。
2.2.2 离心机电气跳闸问题的解决
因离心机使用时间已达到16年,电气元器件老化严重,同时出现故障后,部分备件已停止生产,维修无法达到正常运行要求,造成离心机电气跳闸多。
为彻底解决此问题,通过与设备厂家合作,采用全新的控制系统进行替换。具体方案如下:
(1)电气部分。重新制作2台2TOUCH电控柜、1台公用电控柜等。其中2台2TOUCH电控柜替换现场的DSC电控柜。2TOUCH电控柜通过网线与主背驱电机变频器的通信模块相连,以监控主电机变频器。同时,背驱变频器通过直流母线与主电机变频器相连,可以将背驱变频器运行时产生的电能回馈给主驱变频器,以达到节能降耗的目的。公用柜接入两台离心机的状态信号,并根据用户需求控制外围的公共设备。
(2)机械部分。在离心机上安装两套新的振动传感器及速度传感器。与原设备相比,需要在离心机上增加一套振动传感器并更换振动、速度传感器的类型。两套振动传感器分别监测离心机两端轴承的振动值,以 保护离心机。
通过USB接口完成数据的导入或导出(更新及备份),参数可存档和移植。主要改造分为原电控柜的拆除,在原电控柜拆除前对电缆线芯进行标记、新电控柜的安装、更换新的振动及速度传感器。
2.2.3 离心机振动、扭矩问题的解决
在离心机运行过程中存在频繁跳闸的问题,一年内2台离心机运行故障统计见下表:
设备 | 振动故障 | 扭矩故障 | 停进料 | 信息/操作 | 总报警 |
1#离心机 | 8 | 6 | 2 | 2 | 18 |
2#离心机 | 6 | 7 | 1 | 0 | 14 |
(1)振动故障
离心机振动过大引起的报警停机的原因及措施如下:
一是离心机进料口存在问题。二期泥处理车间由2台离心机和10台带式压滤机组成,贮泥池分为2格,中间不连通,离心机由于处理量大,运行时贮泥池内污泥含水率及液位波动大,进泥量与加药量调整困难,使离心机的负荷波动大。采取将两座贮泥池连通的方式,使贮泥池内污泥的含水率及液位保持基本恒定。
二是离心机由于长期运行,污泥中含有沙粒等杂物,运行中使螺旋叶片磨损,离心机的动平衡被破坏,造成振动故障。采用定期对螺旋瓦片进行检查维修更换,并进行动平衡测试后恢复运行。
(2)扭矩故障
一是根据离心机本身特性及污泥特性,经过摸索,转速在1800r/min左右、扭矩设定在8kN/m、差速运行在5~7r/min时,分离效果比较好。按照离心机的差速控制器模型计算,差速为6.7r/min时刚好处在死区。如果保持在此区间内较长时间,背驱电机正反转频繁切换,使运转不平稳,且各个数据容易出现大的跳动。根据差速控制器模型调整运行参数,使离心机可以快速地跳过死区,以达到运行稳定的目的。
二是离心机在自动控制模式下,差速随着扭矩调节的曲线跳动范围比较大,说明污泥含固率一直在变化,当含固率变化太快时,离心机本身提高差速已经来不及将扭矩降到安全值范围以内,就会出现扭矩停机。解决办法:采用认为干预,适当减少进泥量。
三是污泥含固率变化频繁,将离心机运行模式开启到差速控制模式时,由于差速固定,当污泥含固率提高时,扭矩就会上升,当污泥含固率变化过大时,就会超过扭矩报警值。通过将差速随着扭矩变化而变化的反应时间降低,使其能尽快降低扭矩,保证离心机稳定运行。
(3)处理量较小
在改造前进泥处理量<45m³/h,只达到了额定负荷的60%左右,需进一步提量,在解决上述问题后,开展了离心机提量运行试验,流量达到额定值,实现离心机的正常运行。
2.2.4 离心机本体磨损问题及解决
离心机在一定时间运行,相应的螺旋、轴承等容易磨损,特别是760系统离心机,其动平衡要求非常高,需对机器本体开展维修与保养工作。拆下离心机主机到维修工厂进行保养,对轴承座、转鼓、螺旋、主轴承和螺旋轴承及密封件进行拆解、清洗;对转鼓内径、螺旋外径、轴承座的轴承档、大端端盖和小端端盖的轴承档尺寸进行检测,在加工机床上对螺旋推料叶片外径尺寸进行测量,检查螺旋叶片的磨损情况,将局部磨损部位修复到出厂要求,对螺旋外径进行加工,调整整体尺寸,镶嵌可更换的耐磨硬质合金,包括不锈钢基体和硬质合金块,对大端盖板和小端盖板缺陷采用高科技冷焊补焊机进行补焊或镶套,完成了更换前后主轴承及螺旋轴承、所有密封件、传动皮带等大修保养工作。
3 结论
通过对二期离心机上清液管堵塞、离心机控制系统老化、离心机运行中存在的主要问题进行分析,提出增设上清液中转池、更新改造控制系统、开展离心机配套外围系统及本体维修保养等解决措施,使离心机实现了正常连续运行,在此过程中设备管理与维修人员积累了丰富的经验,同时也为其他离心机运行单位在处理此类问题上提供了借鉴。