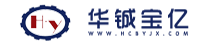
碟式分离机由于占地面积小、处理量大、分离精度高等优点,被广泛用于石油化工、医药及食品等行业的分离及澄清工艺。虽发展多年,但对其研究主要集中在转鼓的强度分析、动平衡和工业应用等方面,流场及分离性能研究较少。长期以来,中国碟式分离机的开发过程依赖于经验,缺乏理论支撑,与国际水平差距较大,且核心技术受国外封锁,严重影响了中国碟式分离机行业的发展和应用。
碟式分离机工作过程中,内部两相流体随着转鼓高速旋转。由于密度不同,轻、重相流体经碟片实现离心沉降分离,经轻、重相出口排出。大量研究表明,转鼓内两相流动及液滴粒径是影响碟式分离机沉降分离的关键因素。受现有测量技术制约,高速运转的碟式分离机内部流场难以直接试验测量,导致对薄层两相流动认识不清。但随着计算流体力学(CFD)的快速发展,CFD已然成为研究碟式分离机内部流场的重要手段,国内外学者对此也开展了一系列研究。本文采用CFD-PBM耦合模型,研究油水混合物在碟式分离机内的流动特性,以及油滴在其内部的聚并与破碎过程,并分析了分离机内部不同位置的油滴粒径分布规律,为揭示碟式分离机机理及指导新型高效碟式分离机设计提供参考。
1 模型及计算方法
1.1 计算模型
多相流模型:由于文章中油-水体系可以视为互不相溶、具有不可压缩性质,故使用Euler-Euler多相流模型来模拟碟式分离机内的两相流动。Euler-Euler多相流模型对多相流每一相都求解动量方程和连续性方程,并通过压力和相间交换系数来实现相间耦合,能够有效地模拟油水两相的流动过程。
湍流模型:油水两相在碟式分离机内部会进行复杂的各向异性的三维旋转运动,前期研究结果表明,采用能反映强旋流动各向异性的雷诺应力湍流模型,对于计算油水两相碟式分离机内的流动可以得到准确的结果。
相群平衡模型:油滴在碟式分离机内部流场中会发生聚并和破碎现象,为清楚描述这一行为,引入群体平衡模型。油滴粒径大小的变化与聚并及破碎过程有关,为考虑多相体系中的粒径分布,需在动量和能量守恒的基础上添加一个平衡方程来描述粒子的平衡,该方程称为相群平衡模型。文章选用Turbulent模型描述油水混合物中油滴的聚并过程,该模型根据油滴直径与涡尺寸相对大小的不同,将聚并机理分为黏性聚并和惯性聚并,从而得到更为 的结果;另外选用Luo破碎模型来计算破碎频率,该模型本身包括了破碎频率以及粒径分布函数,已被证实可以用于液-液两相的模拟。
1.2 结构模型
碟式分离机是高转速设备,轻重相在转鼓内碟片间的组薄层流场内做离心沉降运动,其转鼓内的主要组件包括碟片、碟片架、向心泵、比重环等。物料经加速后由进料道流入转鼓,通过碟片的中性孔流入碟片间隙,高速旋转的分离腔使物料作高速离心旋转运动。轻重相由于密度差的不同导致相对沉降速度不同,轻相液向中心运动并从轻相流道流出,重相液流向碟片大端运动并从重相出口流出。
1.3 计算方法
利用Ganmbit2.4.6软件对5层碟片碟式分离机结构进行三维六面体结构化网格划分,并且规定从下往上对第1层碟片间隙到第5层碟片间隙,由于碟片间隙内的三维流动较为复杂且为主要研究区域,所以对其进行网格加密处理。由于网格数量对数值模拟结果具有极大影响,所以对网格数量分别为20万,100万,143万,197万,300万进行网格无关性检验。通过网格无关性检验发现,在网格数量小于140万时对模拟结果的影响较大,与试验值的相对误差达到15%以上。网格数量为140万时,与实验值的 误差仅在5%。此外,当网格数量继续增大对模拟结果影响较小,因此,为计算经济性和准确性,确定模拟所用网格数为143万。
模拟所用物料与试验一致,油相体积分数为10%的油水混合物,入口边界条件采用速度入口,碟片旋转方向为顺时针(俯视)。轻、重相出口边界条件均为outflow,且轻相出口与重相出口的出流比为1:9。壁面采用无滑移条件,求解方法采用SIMPLE算法,压力方式PRESTO,其余求解方法均为QUICK,时间步长设为0.0005s。
2 结果分析与讨论
2.1 碟式分离机油水分离效率分析
油水混合罐内混合物料通过离心泵加速进入碟式分离机内,在分离机转鼓内高速旋转实现油水分离,分离后的油、水分别流入相应收集罐中。入口流量控制通过控制阀实现,出、入口管道上设置的压力表及流量计可实现进、出液料流量及压力实时监测,转速通过变频电机调节。试验过程中,碟式分离机初始转速n=9500r/min、处理量Q=0.5m³/h及入口油相体积分数为10%的油水混合物。待设备运转稳定后,同时在碟式分离机入口管、轻相出口管进行采样。待测样品的含水量通过卡尔费休水分测定仪(ZKF-1)进行测定,仪器精度为:含水量在5μg至1000μg时,误差小于±3μg;含水量大于1000μg时,误差小于±0.5%。
不同转速下试验、无PBM模型以及加入PBM模型后不同转速下的分离效率,可以看出分离效率随碟片转速的增加而增加。此外,PBM模型模拟所得到结果与试验值的误差在2%~5%,而常规模型与试验值的误差几乎都在7%左右。由此可以发现,PBM模型可以较为准确预测试验结果。这是因为,碟式分离机在工作过程中油滴在其内部必然会发生聚并或者破碎现象。油滴破碎后,粒径变小,所受离心力变小,不利于两相分离,而当油滴聚并后,粒径变大,所受离心力增大,有利于两相分离。而PBM模型可以有效地模拟此过程。
2.2 油滴流动过程的聚并与破碎分析
为了研究分离机工作过程中油滴的聚并与破碎行为以及对分离性能的影响,对转速为9500r/min碟式分离机内油水两相流动情况进行分析。在PBM模型情况下,油相浓集于底部中心区域与轻相出口,表明这两个位置油滴可能更容易发生聚并行为。
2.3 碟片间隙内油滴聚并破碎分析
碟片间隙是油水两相的主要分离区,为深入研究油滴在碟片间隙的聚并与破碎的行为,选取转速为9500r/min下第1层与第5层碟片间隙的油滴粒径分布进行对比分析。经过对比分析可以发现,油滴在每个碟片扇形区域分布规律相似,均为左侧油滴粒径较小,右侧较大,说明油滴在碟片左侧区域的破碎程度较大。原因在于,碟片间隙内的流场被定距筋条所分割,导致油水两相在筋条附近流动受阻,油滴与碟片左侧筋条碰撞造成油滴破碎。此外,可以发现油滴在碟片间隙下表面的聚并程度明显大于上表面,是因为油水两相因为密度差在碟片间隙分离时会出现分层现象。表现为水相主要存在于间隙上部,而油相主要存在于间隙下部,导致了油滴在间隙下部聚并程度更大且聚并区域更为集中。通过观察不同层位碟片间隙内油滴的粒径分布可以发现,第5层间隙内油滴粒径分布与第1层相似,但第5层碟片间隙下部油滴聚并程度明显大于第1层。发生此现象的主要原因是物料在进入碟片间隙进行分离时,由于顶部约束作用,导致油滴在第5层碟片间隙内出现浓集现象,增加了此处油滴聚并几率。
为研究油滴从中性孔进入碟片间隙后的聚并与破碎行为,对第1层中性孔处以及不同间隙内表面油滴的粒径分布情况进行统计分析。从分析结果可以发现,在第1层中性孔处8μm油滴的粒径比接近15%,粒径在60μm以上的油滴占50%左右,而其他粒径油滴的占地基本都在10%以下。在第1层与第3层间隙下表面处油滴粒径的分布大致相同,由于进入碟片间隙内发生聚并现象,8μm油滴的占地均降至5%左右,8~60μm油滴含量几乎为零,此时粒径在60μm以上油滴的数量占地在60%左右。而在第5层碟片间隙下表面处,粒径在60μm以上油滴的占比超过80%。从粒径的变化趋势可以发现,油滴从中性孔进碟片间隙区域后主要发生聚并行为,前几次碟片间隙的聚并与破碎的情况大致相同,上层碟片间隙聚并的程度较大。
2.4 碟片分离机中性孔内油滴聚并破碎分析
中性孔作为油水两相进入碟式分离机碟片间隙内实现分离的关键入口通道,研究油滴在此处的流动特性与聚并破碎行为尤为重要。分别考察第1层、第3层与第5层中性孔处不同粒径油滴分布情况,对其占比进行统计分析。不难发现, 层中性孔处粒径为8~60μm油滴的占地大于第3层与第5层,而粒径在60μm以上油滴的数量则正好相反。第3层与第5层中性孔油滴粒径分布情况类似。主要原因是 层中性孔靠近底部的流道,油水混合物从底部流道流向中性孔时,由于湍流的影响,油滴会发生少量的破碎现象。而进入碟片间隙内,由于碟片间隙很小(间隙为0.58mm),内部可以形成稳定的层流,所以第3层和第5层中性孔油滴粒度分布情况相似。
3 结论
文章基于CFD-PBM模型对碟式分离机内油滴的聚并与破碎行为以及油水分离特性进行了数值模拟研究,并利用自行搭建的碟式分离机实验平台进行验证,主要得出以下结论:
(1)相比单一油滴尺寸模型,采用CFD-PBM耦合模型可以更准确预测碟式分离机油水两相分离性能。
(2)通过分析碟片分离机内油水混合物的流动特性和油滴粒径的分布规律,发现碟式分离机内油滴以发生聚并行为作为主导,平均油滴粒径从入口进入后呈增大趋势,且在油相浓积的区域聚并程度尤为大。
(3)油水混合物从预分离区进入碟片间隙后,由于碟片间隙内形成稳定的层流,各层中性孔处油滴粒径分布基本一致,但第1层中性孔由于受湍流影响,油滴破碎大于其他层位。
(4)油滴在碟片扇形分离区分布规律相似,表现为中性孔前侧区域油滴粒径较小,后侧较大,且油滴在碟片间隙下表面聚并程度明显高于上表面。随着碟片层位增加,油滴聚并程度增强。