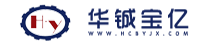
1 前言
炼油厂含油污泥主要由含油污水处理气浮分离所产生的浮渣和池底油泥所组成,年产生量往往达数万吨,其含水率高达96%~99%,需经重力沉降浓缩和机械脱水,才能有效地减少污泥体积(如污泥含水率从98%降到75%时,体积可降到原来的8%)。
含油污泥为黑臭粘稠的浆液,由于性质特殊,其脱水特性和一般市政污水处理厂的污泥大不相同,但目前大多数炼油厂仍沿用与市政污泥基本相同的脱水流程(收集——重力浓缩——化学调质——机械脱水)。故在重力沉降、污泥调质及机械脱水等过程中存在种种问题,特别是脱水水质差,往往为乳状黑浊液,当其返回污水处理系统后,则会影响污水处理的正常运行。
污水处理过程的实质是污染物的相转移,而污泥处理尤其是含油污泥的处理是污水处理过程中十分重要、较为困难、又很费钱的环节。
由于卧螺沉降式离心机具有设备紧凑,占地面积小,调节剂耗量少,处理效率高等优点而逐渐被广泛采用。显然,含油污泥要取得好的离心脱水效果,应在合理的能耗和成本的前提下,达到离心液水质好,泥饼的含水率低的结果。为解决含油污泥普遍存在离心脱水难的问题,实现工业离心脱水液的COD浓度小于2000mg/L的目标,本文对炼油厂含油污泥的离心脱水技术进行了研究。
2 离心脱水原理
污泥离心脱水的动力是离心力,由于在离心机中可以做到离心力比重力大数千倍甚至更多,且控制方便,故离心脱水工艺可高效稳定地运行。
污泥粒子与水相之间存在密度差是含油污泥离心分离的前提,要提高和保证离心分离效果,应从增大污泥粒子粒径和密度,减少粘度,提高离心因数着手。
3 含油污泥的微观研究
污泥脱水过程实际上是污泥的悬浮粒子群和水的相对运动,因此有必要对含油污泥有关离心脱水的特性进行微观研究。
采集污水池底油泥和气浮池表层浮渣A样品,用20%甘油溶液现场固定后,在显微镜下观察发现:
(1)所有污泥粒子粒径均在3μm以上,所含的液态油为5~30μm的分散油珠。
(2)浮渣A中的粒子多为黑色无定形,大多粘连成片,直径大于50μm的占90%以上,而油珠夹带其中,并以“泥包油”为主。
(3)80%的池底油泥粒子的直径在3~10μm,大多外层被薄薄的一层透明油膜包裹,属“油包泥”,说明是亲油的焦粉等。直径在10~50μm间的粒子外层无油膜,只有少数呈无定形且粘连。两种污泥的悬浮粒子粒径分布见下表:
泥样 | 悬浮粒子粒径分布(%) | ||
3~10μm | 10~50μm | >50μm | |
气浮池表层浮渣A | ≤2 | ≤8 | ≤90 |
池底油泥 | ≥80 | ≥15 | ≤5 |
对炼油厂3种主要含油污泥及其中的总固形物组成分析结果见下表:
名称 | 密度(20℃)(g/cm³) | 含水率(%) | 含油率(%) | 灰分(%) | 总固形物(%) | 热值(J/g) | 总固形物的组成/% | ||
沥青质+胶质 | 灰分 | 其它 | |||||||
气浮池表层浮渣A | 0.999 | 93.8 | 1.87 | 1.86 | 4.89 | 2137 | 24.41 | 38.4 | 37.19 |
气浮池表层浮渣O | 0.989 | 91.0 | 5.29 | 0.82 | 5.21 | 4249 | 33.75 | 16.1 | 50.15 |
池底油泥 | 1.004 | 92.2 | 1.75 | 1.28 | 5.14 | 2037 | 24.0 | 24.6 | 51.4 |
其它成分包括焦粉、其它不溶于石油醚的有机物和挥发性物质等。
由上表可知,含油污泥中的总固形物主要是由有机物组成的,无机固体(灰分)含量低:以无机铝盐为絮凝剂所产生的浮渣A的灰分含量为38.4%,池底油泥为24.6%,而以有机絮凝剂所产生的浮渣O的灰分含量只有16.1%。含油污泥中的有机质,除“油”以外,还有沥青质、胶质和结晶石蜡等有机物。
通过上述对含油污泥的微观研究,对提高其离心脱水效果的对策而言,有如下启示:
(1)污泥脱水前必须进行调质,作用是使高度分散的污泥颗粒、油珠或乳化油间进行电中和、网联架桥,从而使污泥颗粒间发生凝聚,变成大颗粒以至大块凝聚体,从而改善其固液分离性能。含油污泥主要成分是有机物,其粒子质轻、常温下呈固体或半固体而易变形,是导致其脱水难的根本原因。故对其进行两相分离的调质时,还应该考虑提高粒子密度、增加它与水的密度差。
(2)因含油污泥的粒子较大,在选用絮凝剂时,不要求它有较强的电中和功能,而希望它有较好的架桥和卷扫作用,故宜选用阳离子度不高的有机絮凝剂。
(3)含油污泥粒子通过投加絮凝剂网联结合而成的凝聚体,结构往往不很紧密,应根据分离要求通过试验确定其离心因数。
4 化学调质技术的实验室探索
污泥的调质是通过一定手段调整其固体粒子群的性状及排列状态,使之适合于不同脱水条件的预处理操作。显然,污泥调质能显著改善污泥的泥水效果,提高机械脱水性能。
污泥调质方法主要有物理法和化学法,前者采用投加助剂或加热等手段实现对污泥的改性,而后者在大多数情况下是选择投加絮凝剂。含油污泥调质方法的选择和确定,除考虑含油污泥的性质和特点外,还取决于脱水泥饼如何处理或利用。本课题主要对含油污泥的水、固两相分离的化学调质和离心脱水技术进行探索。
4.1 试验方法
在装有100mL含油污泥浓缩液的具塞量筒中,加入絮凝剂后上下颠倒10次,在剂和泥充分混合后倒入200mL离心试管中,在DL-5型微电脑离心机上进行模拟离心脱水,通过试验确定离心转速为1980r/min,离心时间为在1980r/min下稳定60s,测定离心液的透光率(在波长680nm下)和COD浓度来评定效果。
4.2 絮凝剂的筛选
筛选试验主要以浮渣A为对象,同时为保证所选出絮凝剂的“广谱”性,在絮凝剂耐油筛选试验时采用浮渣O为试验对象,试验采用新鲜原料污泥(保存2~3d),均在试验前取于现场排泥泵出口。试验时采取措施使污泥的密度大于1g/cm³。用优选法确定各种絮凝剂的较佳用量。
由于絮凝效果和污泥性质有关,为此,从收集的32种国产絮凝剂中,通过初选、精选、耐油性试验和适应范围试验,筛选出6种高效、易溶、适应性宽、成本合理的絮凝剂:阳性CPAM-2,阳性CJX-103,阳性XHY-C,阴性HPAM-2,阴性T-1150,阳性PAC。
(1)采用HPAM-2、CPAM-2、XHY-C、CJX-103、T-1150这5种絮凝剂,离心液的COD浓度都能达到500mg/L以下。
(2)使用这5种絮凝剂时,经阳离子型絮凝剂处理所得的离心液清亮,透光率在84%以上;用阴离子絮凝剂处理的离心液略呈乳白色,透光率在66%左右,但两者的COD浓度无明显差别。另外,这5种絮凝剂的电荷极性对含油污泥的调质效果基本没有影响,其中的阳离子絮凝剂的阳离子度都在中等或中等以下。阴离子型药剂的成本较低。
(3)属强阳离子型的无机聚合铝PAC絮凝剂不适用于含油污泥调质。
4.3 不同含油污泥化学调质后的离心脱水效果
采用CPAM-2作为絮凝剂,分别对不同含油污泥进行离心脱水试验,结果见下表:
污泥 | 0.2%CPAM-2 投加量(%) | 离心液水质 | |||
种类 | 含油率(%) | 密度(20℃)(g/cm³) | COD(mg/L) | 透光率(%) | |
1号池底油泥 | 1.86 | 1.002 | 10 | 531 | 82.0 |
1号浮渣A | 1.57 | 1.001 | 10 | 801 | 73.0 |
1号浮渣A+活性污泥 | 1.06 | 1.002 | 1 | 324 | 88.5 |
2号浮渣A | 2.83 | 0.996 | 10 | 上层为油渣,且下层污水中有大量悬浮物 | |
1号浮渣O | 9.98 | 0.981 | 10 | 上层为油,油层下是结构紧密的泥渣层,下层是清澈的污水层 |
上表中试验结果表明,加入一定量的CPAM-2絮凝剂后:
(1)密度大于1g/cm³的1号池底油泥可直接离心脱水。
(2)1号浮渣A密度略大于1g/cm³,就可顺利进行离心脱水,但密度小于1g/cm³的2号浮渣A无法进行离心脱水。
(3)在1号浮渣A中混入等体积的活性污泥后,密度大于1g/cm³,离心脱水效果明显变好,絮凝剂投加量只需原来的1/10就可以做到泥饼密实、离心液清澈透明(透光率达88.5%),COD浓度只有324mg/L。据分析,加入活性污泥后,一方面,由于混合污泥整体密度增加,离心脱水可以顺利进行;另一方面,因活性污泥中含有大量微生物,其细胞外的荚膜类似于高分子絮凝剂的电位隧道,具有负的Zeta电位,其本身就是很好的阴离子生物絮凝剂,故使絮凝剂用量明显降低。
(4)密度小、含油率较高的1号浮渣O,无法进行水、固两相分离的离心脱水。
5 粉焦调质助剂的应用研究
Jonathan Zall等曾用飞灰等作为含油污泥的调质助剂,使易变形的半固体粒子形成刚性污泥骨架,从而显著改善含油污泥机械脱水性能。由于镇海炼油化工股份有限公司的泥饼出路是去焦化装置,故考虑用粉焦作为助剂来改善含油污泥的离心脱水效果。粉焦价廉易得,是焦化装置副产品,密度大(>1.26g/cm³),粒子坚硬,且与含油污泥有很好的吸附和亲和性,适合作含油污泥的调质助剂。
5.1 可行性和条件试验
5.1.1 质量要求
作为污泥调质助剂,要求调合操作方便,调合污泥性质稳定。虽然粉焦对含油污泥的吸附和亲和性能好,但当其粒径过大时仍会发生沉降;当其干燥时,因其中的空隙充满空气,则不易和污泥调合。通过对原粉焦产品的性质测定和调合试验,确定作为助剂粉焦的质量要求为:含水率20%~30%,粒度80~200目。
5.1.2 粉焦投加量的确定和投加后对絮凝剂用量的影响
粉焦的投加量关系到该调质技术的可行性和经济性。分别用3号浮渣A(含水92.3%、含油2.39%、密度0.996g/cm³)和2号浮渣O(含水86.1%、含油4.98%、密度0.989g/cm³)为试验泥样,用CPAM-2作为絮凝剂,分别投加不同比例的粉焦(粉焦含水20%)和絮凝剂,进行离心脱水试验。结果见下表所示:
污泥样和粉焦投加量(%) | 絮凝剂用量(μg/g) | 减少絮凝剂比例(%) | 离心液COD浓度(mg/L) |
3号浮渣A | |||
0.74 | 140 | 30 | 652 |
1.07 | 140 | 30 | 421 |
1.47 | 120 | 40 | 411 |
1.81 | 100 | 50 | 392 |
2.21 | 100 | 50 | 386 |
2.54 | 100 | 50 | 383 |
2号浮渣O | |||
3.29 | 80 | 60 | 641 |
3.61 | 80 | 60 | 514 |
4.35 | 80 | 60 | 596 |
5.01 | 80 | 60 | 472 |
试验表明,在不投加粉焦,只投加200μg/g絮凝剂时,离心后不能分层或泥渣层在上,水层在下,无法实现离心分离。上表表明,粉焦能显著改善含油污泥(3号浮渣A)离心脱水效果,并能减少絮凝剂用量。随粉焦投加量的增加,离心液水质也略有提高,并可减少絮凝剂用量30%以上,这是由于它能吸附和亲合污泥微粒,减少总粒子数所致。如果污泥(2号浮渣O)含油率过高,所需粉焦量增加,因而粉焦调质只适用于含油率不高的污泥。一般粉焦投加量控制在1.5%~2.0%,絮凝剂用量可减少30%~50%。
5.2 粉焦调合搅拌设计参数的确定
为含油污泥和粉焦调合寻找工业应用混合搅拌的设计参数,在六联搅拌器上通过试验比较,选定浮渣和粉焦调合的搅拌转速为300r/min。分别搅拌1~15min后,用CPAM-2调质并进行离心脱水,考察离心效果(离心液水质),结果见下表:
搅拌时间(min) | COD(mg/L) |
1 | 不分层 |
3 | 分层不明显 |
5 | 523~587 |
10 | 630~894 |
15 | 582~861 |
试验表明,在搅拌时间大于等于5min时,粉焦能和含油污泥充分混合并取得好的离心脱水效果。据此条件以及搅拌桨叶和水体间的尺寸等数据,经计算得到粉焦调合所需的搅拌速度梯度G和GT值(即速度梯度G和反应时间T的乘积,无量纲)如下:
G=2.88×102/s
GT=(5.18~8.64)×104
5.3 离心参数的确定
在实验室考察不同离心速度、时间对分离水质的影响,试验方法同前。
在3000r/min高速下,离心液水质随离心时间的增加迅速变差,这是因为离心力过大使絮体不断解离,导致水质下降;而在1020r/min低速时,水质随时间的增加慢慢变好,但效果并不理想;而在1980r/min下15~250s内效果较好且稳定。故适宜的离心速度应取1980r/min。据此计算出相应的离心分离因数α=588,已知工业用卧螺离心机的转鼓直径,则其适宜转速应为n=1500r/min左右。由于实验室仅能模拟离心机的分离作用,其余离心参数只能在工业试验中考察。
6 工业应用试验和效益分析
6.1 工业应用试验
污泥调质采用CPAM-2絮凝剂,加剂量均为200μg/g,必要时投加粉焦,粉焦投加量为污泥质量的1.5%,用专门设计的粉焦搅拌罐混合后,混合泥料进入LWD430型国产卧螺离心机,该机转速、进泥量、差转速等参数可以在不停机情况实现无级控制,直至离心液水质较好。
在原料污泥含水率变化较大(91.2%至97.8%)的不利条件下,通过控制适当的离心参数(离心机转速不大于1600r/min,和实验室模拟试验结果基本吻合),只要含油污泥的密度大于1.0008g/cm³时,通过化学调质就能顺利进行离心脱水;当其密度基本为1g/cm³时,离心效果受到影响;而当其密度小于1g/cm³时,离心液呈黑浊浆状,甚至在泥饼出料处排出污水。
通过用粉焦调质后,离心脱水效果明显改善,离心液COD浓度达到1880mg/L以下,实现了工业离心脱水液的COD浓度小于2000mg/L的预期目标。
因此,粉焦作为轻质含油污泥的调质助剂技术上是可行的,能从根本上改善和保证含油污泥的离心脱水效果。
6.2 效益分析
采用投加调质助剂粉焦的技术,只需增加相应的搅拌设备,就能使含油污泥离心脱水工艺长周期稳定运行,解决了含油污泥脱水难的问题。另一方面,粉焦是炼油厂的副产品,价格十分低廉,经适当加工,就可以作为一种含油污泥调质助剂商品,据估算,每吨升值在200元以上,还有一定的社会效益。含有粉焦的泥饼,热值增加(粉焦热值为36.2kJ/g,高于一般煤),有利于泥饼的焚烧,在送焦化装置后,转化为价格较高的焦炭产品。
投加调质助剂粉焦技术只适用于含油率低的浮渣,据多次测定,浮渣A的密度均在0.998g/cm³以上,故粉焦投加量在1.5%~2.0%间就能满足要求。
以年产生32kt以浮渣为主的含油污泥离心脱水工艺为例,年需调质助剂粉焦640t,每年所增加的成本为40.9万元,经济增益为57.7万元,年净经济收益16.8万元。
需要指出的是,为避免粉焦在运输、加工和使用过程中对环境卫生的不利影响,必须考虑相应设施的自动化和密闭操作。
7 结论和建议
7.1 结论
(1)以浮渣为主的炼油厂含油污泥含有大量的沥青质、胶质、石蜡等“油固体”,是含油污泥脱水难的主要原因。
(2)由于含油污泥粒子的特殊性质,宜采用有机高分子絮凝剂,而絮凝剂的电荷极性对其影响不大。同时要考虑絮凝剂的广谱性、易溶性和经济性。
(3)浮渣在混入等体积的剩余活性污泥后,能显著改善离心脱水效果,并节约90%左右的絮凝剂。
(4)对密度低、含油率小于3%的轻质浮渣,用含水率为20%~30%、粒径80目以上(粒径不大于0.175mm)的粉焦作为污泥调质助剂,可根本解决含油污泥的脱水难题,达到“水清、泥干”的效果,并有利于泥饼的回收利用,明显减少絮凝剂用量,增加泥饼热值。该技术有一定的经济效益、环境效益和社会效益。
(5)对以水固两相分离为目标的含油污泥的离心脱水,是要使大部分有机物(包括油)进入泥饼,其离心分离因数宜低(α=588左右),相当于工业卧螺式离心机转速在1260~1600r/min。
7.2 建议
(1)重视含油污泥的调质技术,特别是对高含油污泥调质和三相分离脱水技术的研究。
本文仅对含油较低的以浮渣A为主的含油污泥的两相分离的离心脱水技术进行了探索。由于含油污水气浮处理工艺中有机絮凝剂的推广应用,将使含油污泥中数量较多的浮渣含油率成倍增加,因此,建议开展对高含油污泥的“油—无机固体—水”三相分离的调质技术进行研究,开发如调理剂、破乳剂或乳化剂、固体增湿剂等产品和相应的调质技术和设备。
(2)稳定进入离心机泥料的性质。由于含油污泥的特殊性质,其离心机械脱水的前一工序——重力沉降浓缩一般分为三层(上层是含油较高的油渣、中层是污水、下层是密度较大的污泥)。如设计不当,往往使进入离心机前的污料含水率和粘度变化大,导致离心工艺参数的频繁调整。必须根据所处理含油污泥的重力沉降特性,改进重力浓缩工艺,以确保离心脱水效果的稳定性。