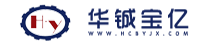
碟式离心机因其高转速、高效率、大处理量等优点,在石油、化工、医疗和环保等领域被广泛使用,其碟片间流场内沉降分离过程是影响碟式离心机分离性能的关键。碟式离心机碟片间的薄层多相流动主导着碟式离心机性能。
对于碟片间薄层流场的流动特性,国际上不少学者利用理论计算和试验尝试探究其流动规律。本文研究主要针对离心力场下薄层流场内的两相沉降过程,以多相流理论为基础,建立碟式离心机碟片间隙内流场及多组碟片间薄层流场的三维流动模型,并以CFD模拟,通过理论计算悬浮液内颗粒的受力情况及沉降速度,结合数值模拟分析多组碟片间薄层流场内两相流动性;通过对比轻、重相的相对流动性,研究了离心力场下薄层流场内重相在连续相的沉降过程。研究结果对优化碟式离心机结构、提高离心机的性能、拓展离心机新的应用、实现技术突破,具有重要的意义。
1 离心力场下薄层流动模型及可行性验证
1.1 碟式离心机转鼓内薄层流动模型
碟片间薄层流场结合了超重力沉降和浅池原理,即悬浮液中的颗粒在离心场下作沉降运动,其生产能力正比于沉降面积。此流动过程的优势是利用碟片将沉降池均分为若干薄层流动场,以此降低离心机内悬浮液的沉降高度,在一定的离心机高度下增加碟片数,从而增加沉降面积,进而加速悬浮液在离心场下的沉降过程,有效地提高了离心机的离心分离性能。
通过CFD模拟研究转鼓内薄层流场,并做假设如下:
(1)转鼓内充满液体且流动稳定;
(2)液相为连续不可压缩流体;
(3)固相为密度均匀等粒径球形颗粒,且运动过程中不发生絮凝、破碎和变形;
(4)不考虑重力;
(5)不考虑沉渣挤压作用带来的热影响。
使用ANSYS15.0前处理软件ICEM建立5层碟片间两相流动区域及转鼓成渣腔的三维流动模型,进料口与定距筋条作网格局部加密处理,以提高结构化网格质量。
1.2 流动模型的边界条件
根据OCM305标准碟式离心机分离处理5号喷气燃料油(RP-5),相关标准依据国内航空使用的重煤油标准。碟式离心机转鼓内的主要结构及重煤油的相关物理特性见下表:
碟片组高度(m) | 0.11 | 油相密度(kg/m³) | 814 |
碟片厚度(mm) | 0.3 | 水相密度(kg/m³) | 998.2 |
碟片锥角(°) | 45 | 水粒径(μm) | 10 |
转鼓内径(mm) | 235 | 流量(m³/h) | 1 |
油相黏度(mPa·s) | 6.919 | 水相体积分数(%) | 1 |
水相黏度(mPa·s) | 1.003 | 转速(r/min) | 6000~10000 |
研究碟式离心机碟片间两相流动场,由于无需考虑涡黏性各项同性假设,湍流模型比雷诺应力模型更加精准。在碟片间两相流动场中,物料受离心作用处于高速旋转运动且其流场为强制涡。因此模拟中采用RSM湍流模型,其计算原理是质量守恒方程、动量守恒方程、应力运输方程。碟片间两相流动属于多相流动,采用Eulerian模型能够精准地研究碟片间两相流动性及其分离性能。计算模型对两相间的相互作用,计算模型中不仅包含了不同相间的相对运动,而且不同相间相对运动的速度大小不同,因此计算模型能够比较全面地分析碟片间两相流动过程。
1.3 数值模拟的可行性验证
对碟式离心机的理论分析和模拟研究均是建立在一定的假设基础上,与实际分离情况并不完全吻合,需要进行数值模拟的可靠性验证,验证试验能够充分考虑到理论、模拟中忽略到的相关影响因素,因此是研究中不可或缺的一部分。由于碟式离心机转鼓内碟片间薄层流场的复杂流动性,一般仪器均无法对转鼓内部流动进行准确的实时测量。
因此通过对含水煤油的试验模拟,根据全自动微量水分测定仪测出进出口的水分含量,并计算出离心机的分离效率,计算结果对转鼓转速及进料量对分离效率的影响进行讨论,根据试验结果来验证数值模拟方法的可靠性。
测试在相同进料量下,不同转速的分离效率。由测试结果可知,碟式离心机的分离效率与转速成正比,模拟与试验的分离效率值有所偏差,且转速越大偏差值越小。存在偏差的原因在于试验物料含杂杂质,且不是单一粒径,转速较小时小粒径的重相较难进行离心沉降分离,而随着转速增加,模拟与试验的偏差值逐步减小,两者的平均偏差为26.6%,在试验误差范围内,证明了数值模拟具有较好的可靠性。
测试在同一转速下,不同进料量的分离效率。由测试结果可知,碟式离心机的分离效率与流量成反比,碟式离心机的进料量越大,分离效率越低;模拟与试验的分离效率值有所偏差,且进料量越大偏差值越大。物料的轴向进料速度对碟片间薄层流场的沉降有所干扰,进料量越大越不利于物料的离心沉降分离。存在偏差的原因在于试验过程中流量计数值波动较大,数值模拟中主要取流量的平均值进行计算。当碟式离心机处理量较小时,其模拟与试验的偏差值也较小,两者的平均偏差为18.7%,在试验误差范围内,进而表明了数值模拟的可靠性。
2 薄层流场内颗粒的沉降速度
2.1 薄层流场内颗粒的受力情况
通过建立离心机转鼓内薄层流场中分散相颗粒的分离模型,进一步分析薄层流场内分散相颗粒在离心力场下沉降分离的运动情况。由于薄层流场内的分散相颗粒粒径很小(一般在3~15μm),可忽略惯性力的影响;由于薄层流场内分散相的浓度很低(一般不大于10%),可忽略颗粒间的相互作用以及其布朗运动;由于薄层的流场的流速很大(一般在5000~12000r/min),且边界层的厚度相对较小,相对于中层大流速可忽略其边界层对离心机内薄层流动的影响。因此研究碟式离心机内薄层流场内分散相颗粒,主要考虑其受到的离心力、重力、浮力、离心浮力、流体阻力作用。
经测试,分散相颗粒的离心力和阻力与其在薄层流场内径向位置有关。
2.2 离心沉降速度的理论分析
在离心力场下颗粒做沉降运动,分散相颗粒由中性进料孔进去碟片间薄层流场后做加速运动,在连续相中所受阻力随速度不断增大,直到阻力与离心力相等时即达到重力沉降的饱和稳态速度。
2.3 离心沉降速度的数值模拟
碟式离心机转鼓内流动分布符合旋转流场的一般规律。物料在碟式离心机转鼓内的离心沉降过程是在多组碟片间薄层流场内进行的,物料由中性孔进入碟片间薄层流场,由于轻重相所受离心力与密度差的影响,大部分轻相从碟片内端出口流出,重相从碟片外端出口流出,从而完成了在碟片间薄层流场内的离心沉降分离过程。
物料进入中心孔后做加速沉降运动,中心孔内中心线上颗粒所受的离心浮力、离心力与阻力平衡,其沉降速度为零;由中性孔往大端,颗粒所受离心浮力与离心力不断增大,在离心力场下的沉降速度沿碟片间薄层流场朝外;由中心孔往内端,颗粒所受阻力大于离心浮力与离心力之和,在离心力场下的沉降速度沿碟片间薄层流场朝内。研究结果表明,中心孔内多层碟片间的进料逐层增多,碟片间薄层流场内物料的相对沉降速度往内、外端逐渐增大。
碟式离心机内转鼓作逆时针旋转运动,物料由中性孔进入碟片间薄层流场后做离心加速运动直到相对稳定速度,其相对稳定速度小于碟片旋转速度;沿碟片旋转方向,定距筋条前侧物料沿筋条侧壁面往碟片内端流动,定距筋条后侧物料具有较好的跟随性,其相对速度基本为零;相邻两个定距筋条中间区域薄层流场内,流体受水平剪切力作用,物料的相对稳定速度大于碟片旋转速度。研究结果表明,物料由中性孔进入薄层流场内,在定距筋条外侧物料流动相对滞后,在相邻两个定距筋条中间区域的物料流动超前于碟片旋转运动。
3 薄层流场内轻重相分布情况
碟式离心机中性孔内重相体积分布由 层往上逐步升高;中性孔内中心线往碟片内端的重相体积分布较小于中心线往碟片外端。研究结果表明,碟式离心机中性孔内重相体积分布不均,中性孔上端重相体积分布较大,轻重相分界面较为明显且径向位置在中性孔中心线附近。
碟片间薄层流场内轻重相形成较明显的分界面,碟片间薄层流场内向下表面往上重相体积分布逐步升高,大部分轻相沉积在薄层流场的下表面,重相堆积在薄层流场的上表面;碟片间薄层流场内由碟片外端往碟片内端重相体积分布逐步升高,大部分轻相从碟片内端流出; 层碟片间薄层流场内重相体积分布较大。研究结果表明,各层碟片间薄层流场内重相体积分布不均,大量重相进入 层碟片间薄层流场进行离心沉降分离,碟片间薄层流场内形成明显的轻重相分界面,重相堆积在碟片下表面。
沿碟片逆时针旋转方向,中性孔前后侧的重相体积分布较小,往碟片外端的重相体积分布较大;定距筋条后侧重相体积分布较小,定距筋条前侧的重相体积分布较大;相邻两个定距筋条中间区域的薄层流场内,重相体积分布沿逆时针方向逐步减小,且碟片内端重相体积分布较小。研究结果表明,碟片间薄层流场内重相体积分布不均且轻重相分界面较为明显,重相堆积在定距筋条前侧,中性孔前后侧重相体积分布较小,大部分轻相从碟片内端流出。
4 水滴粒径对分离性能的影响
由于物料中液滴的粒径大小不同,对碟式离心机分离效率的影响较大。在液滴粒径为10~30μm的范围内,分离效率随液滴粒径的增加而显著增加。在粒径达到30μm以后,离心机的分离能力达到了极限,轻相出口的重相体积分布不再随粒径增加而明显增加。
5 结论
(1)转鼓内径重相的离心力和阻力与其在薄层流场内的径向位置有关,多层碟片间的进料量自下往上逐层增大,碟片间薄层流场内物料的相对沉降速度由中性孔向端口逐步增大。
(2)靠近碟片外端口物料流动具有相对滞后性,定距筋条间区域的物料流动超前于碟片旋转运动。
(3)碟式离心机中性孔内重相体积分布不均,中性孔内上端重相体积分布较大,轻重相分界面较为明显且径向位置在中性孔中心线附近。
(4)碟片间薄层流场内重相体积分布不均且轻重相分界面较为明显,重相堆积在定距筋条前侧,大部分轻相从碟片内端流出。
(5)各层碟片间薄层流场内重相体积分布不均,大量重相在 层碟片间薄层流场进行离心沉降分离。