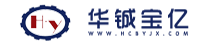
大庆油田某采油厂于1986年建成投产,共建有脱水站3座。脱水站油系统全部采用两段脱水工艺:一段采用游离水脱除器进行油、水初步分离,二段采用复合电脱水器进一步脱水。脱水处理后,净化油含水率小于0.3%直接外输,污水含油量小于1000mg/L进入污水沉降罐。
含油污水进入污水沉降罐后,在重力作用下进行油、水沉降分离。分离出的污水供站外集油系统掺水使用,其余部分输往含油污水处理站处理后回注;分离出的污油通过收油泵定期回收进入正常生产流程进行脱水处理。但是,自2003年开始,经常出现收油时电脱水器运行不稳定的情况,主要表现为电脱水器脱水效果不好、含水超标、脱水器电流上升及频繁放电,导致电场瘫痪,严重时甚至烧毁电脱水器的控制系统。至2005年,污水沉降罐内的污油已基本无法利用电脱水器进行脱水。
污水沉降罐内这种难于处理的污油称为老化油。为解决老化油问题,有必要研究效率高、流程简洁、便于操作、处理成本较低的老化油处理工艺技术,确保油气集输处理系统安全平稳运行。
1 老化油物理及化学性质分析
1.1 老化油含水分析
回收污水沉降罐内老化油,用80℃恒温水浴加热,经自然沉降并冷却至室温,去掉沉积水后,采用离心法分析上部“渣油”状老化油含水率。在所取样品中,老化油含水率低至21.42%,高达28.28%,具体如下表所示:
取样序号 | 老化油量/mL | 游离水质量/g | 乳化老化油质量/g | 乳化水质量/g | 乳化油含水率/% |
1 | 150 | 3.0 | 130.697 | 28 | 21.42 |
2 | 150 | 4.5 | 129.540 | 29 | 22.39 |
3 | 200 | 8.0 | 171.587 | 43 | 25.06 |
4 | 250 | 17.6 | 208.644 | 59 | 28.28 |
1.2 老化油硫化物含量分析
利用离心机对老化油样品进行离心处理,老化油分成3层:上层是黑色的原油层,中间是水层,下部是黑色的机械杂质。将下层的黑色机械杂质分离出来,用能谱仪分析,确定其为FeS颗粒。
取老化油及油水界面层样品,测试其硫化物及SRB(硫酸盐还原菌)含量。测试结果:油水界面层中硫化物含量为103mg/L,SRB含量为7×105个/mL;老化油中硫化物含量为156mg/L,SRB含量为2×105个/mL。
1.3 击穿电压和界面张力测试
将老化油与净化油按不同比例混合,配置不同FeS含量的油样。对混合油样进行击穿电压和界面张力测试,测试温度50℃,测试结果如下表所示:
混合样中老化油比例/% | Fes含量/mg/L | 击穿电压/V | 界面张力/mN/m |
0 | 0.2 | 44500 | 29 |
10 | 16.0 | 31000 | 42 |
30 | 50.0 | 17500 | 49 |
50 | 79.0 | 12500 | 51 |
70 | 108.0 | 9800 | 62 |
90 | 141.0 | 6500 | 73 |
100 | 156.0 | 3500 | 81 |
由上表可以看出,随着FeS含量的增加,击穿电压降低,界面张力增加。净化油击穿电压为44500V,界面张力为29mN/m,而老化油的击穿电压仅为3500V,界面张力高达81mN/m。
2 老化油处理工艺技术
2.1 热化学脱水工艺技术
将老化油加热到一定的温度,并在老化油中加入适量的破乳剂。破乳剂吸附在油水界面膜上,降低油水界面薄膜的表面张力,从而破坏乳状液的稳定性,改变乳化液的类型,以达到油、水分离的目的。
利用1000m³立式金属罐一座,建成独立的老化油热化学处理系统。针对老化油中富含FeS颗粒、导电性强、表面张力大等问题,研制了高效老化油破乳剂,破乳剂中含有硫化物去除剂配方。
2.1.1 运行参数
加药量3000mg/L;处理温度75~80℃;脱水后原油含水率≤5%;脱水后污水含油量≤1000mg/L。
2.1.2 流程说明
利用收油泵(流量30m³/h,扬程60m)回收污水沉降罐内老化油,加热后进入1000m³老化油罐,同时加入老化油破乳剂;启动老化油罐前循环泵(流量50m³/h,扬程60m),循环加热老化油,以保证老化油温度达到80℃以上,同时,确保老化油与老化油破乳剂充分混合;老化油经过一段时间的静止沉降后,将脱出的游离水从老化油罐底部出水口回收至污水沉降罐,由于油水界面层主要是不溶于水也不溶于油的FeS颗粒悬浮物,遇油水界面层需切换流程外排;通过捞油化验油水界面层上部老化油含水,若含水小于5%,则启动收油泵收油,并将回收原油掺入外输管道外输。
若老化油温度下降较快,但含水仍较高,则需要重新启动循环泵循环加热,重复以上过程。
2.2 离心脱水工艺技术
热化学脱水主要采用重力沉降法脱水,离心脱水则以离心分离替代重力沉降,从而提高油、水分离的速度和效果。通过现场试验,确定采用两级离心分离技术处理老化油。
离心分离装置主要由卧螺式离心分离系统、碟片式离心分离系统和加药系统三部分组成。老化油首 入卧螺式离心分离机,在絮凝剂的作用下实现固、液分离,分离出来的含水油进入碟片式离心机,在破乳剂的作用下实现进一步脱水。该处理方式的创新点是在较低的转速下实现固、液分离,在较高的转速下实现油、水分离。
2.2.1 设备及运行参数
卧螺式离心机转速3500r/min,功率35kW,处理量5m³/h;碟片式离心机转速6000r/min,功率26kW,处理量5m³/h。
加药量20mg/L;处理温度70℃;脱水后原油含水率≤0.3%;脱水后污水含油量≤50mg/L。
2.2.2 流程说明
用收油泵将老化油回收至1000m³老化油罐,通过循环泵循环加热,将老化油升温至试验温度,然后进入卧螺式离心机处理,脱除的固体杂质直接装袋运送至质量安全环保部门指定地点,含水油进入碟片式离心机脱水;碟片式离心机出水进入净化水罐,出油进入净化油罐,排渣重新进入卧螺式离心机处理。
若碟片式离心机出油、出水指标较差,则将净化水罐中的水输入卧螺式离心机,净化油罐中的油输回至老化油罐循环加热再处理;若碟片式离心机出油、出水指标合格,则将水输回至本站污水沉降罐,油直接外输。
2.3 微生物处理技术
老化油中的硫化物及SRB含量较高。SRB是一种硫化细菌,它能分解硫酸盐,产生的代谢产物为H2S、HS-或S2-,H2S会腐蚀金属管道和设备,生成Fe2+,S2-与Fe2+反应生成FeS,大大增强了原油的导电性,从而导致电脱水器运行不稳。
基于这一认识,采用一种新的技术思路,即,采用微生物来抑制和消除老化油中的SRB及硫化物。其主要机理是利用生物竞争淘汰法来消除老化油中的SRB,并通过细菌作用,将SRB产生的FeS氧化成SO42-。
通过室内试验,从SOB菌、B.B菌等多种菌中筛选了TD菌种处理老化油。TD菌株是严格自养和兼养性厌氧菌,细胞呈球杆状,菌体大小0.3~1.5μm,单个、成对或短链状排列,运动活泼,无芽孢。
2.3.1 运行参数
加药量:60mg/L;处理温度:55℃;生物作用时间6d;脱水后原油含水率≤0.3%(电脱水器出油);脱水后污水含油量≤500mg/L。
2.3.2 流程说明
利用1座200m³净化油缓冲罐作为老化油反应罐,利用收油泵回收污水沉降罐内老化油(提前用70℃掺水将老化油预热),同时加入TD菌种;TD菌种与老化油在老化油反应罐中发生作用,静止沉降。老化油反应罐由罐底伴热盘管加热维温,罐内温度呈缓慢下降趋势。4d后开始取样,测试老化油酸碱性,若老化油显中性,则利用污油泵将老化油输至游离水脱除器进入正常流程处理。
3 老化油处理技术影响因素分析
3.1 热化学脱水技术影响因素分析
恒温水浴,脱水温度分别为60℃、70℃、80℃,脱水试瓶若干,试验药剂分别为常规的油溶性破乳剂、水溶性破乳剂,以及老化原油处理剂(ALDT),加药量分别为被处理油样的1%、3%、5%。当脱水温度为60℃时,破乳剂脱水效果很差。
随着温度上升,脱水速度加快;油田常规使用的破乳剂对老化油的脱水作用效果甚微,ALDT型老化油处理剂脱水速度较快,脱水效果较好。因此,温度和破乳剂是影响热化学脱水效果的主要因素。
3.2 离心脱水技术影响因素分析
从污水沉降罐回收老化油至1000m³老化油沉降罐,通过循环加热,1000m³老化油沉降罐内老化油温度缓慢上升,每小时升温约0.5℃。当油温升至50℃时,调整加热炉燃烧器开度,保持罐内油温不变,试验不同絮凝剂、破乳剂加入量的脱水效果;然后,油温每升高5℃,重复以上试验,摸索较佳生产运行参数。
温度及加药量对离心脱水工艺中卧螺离心机和碟片式离心机脱水效果的影响规律见下表:
处理温度/℃ | 卧螺式离心机 | 碟片式离心机 | |||
絮凝剂加入量/mg/L | 固体含油量/% | 破乳剂加入量/mg/L | 原油含水率/% | 污水含油量/mg/L | |
50 | 100 | 5.0 | 100 | 26.3 | 360 |
200 | 4.6 | 200 | 19.5 | 170 | |
300 | 3.7 | 300 | 16.4 | 160 | |
500 | 3.1 | 500 | 10.2 | 130 | |
1000 | 2.3 | 1000 | 6.5 | 80 | |
55 | 100 | 4.5 | 100 | 17.5 | 210 |
200 | 3.7 | 200 | 10.5 | 120 | |
300 | 3.0 | 300 | 5.0 | 75 | |
500 | 2.3 | 500 | 2.0 | 50 | |
1000 | 2.2 | 1000 | 1.8 | 50 | |
60 | 20 | 2.0 | 20 | 5.0 | 50 |
50 | 1.8 | 50 | 4.7 | 40 | |
80 | 1.6 | 80 | 4.6 | 35 | |
100 | 1.5 | 100 | 4.6 | 30 | |
65 | 20 | 1.9 | 20 | 2.3 | 50 |
50 | 1.6 | 50 | 2.4 | 43 | |
80 | 1.4 | 80 | 2.5 | 37 | |
100 | 1.3 | 100 | 2.9 | 35 | |
70 | 20 | 1.6 | 20 | 0.28 | 45 |
50 | 1.4 | 50 | 0.26 | 36 | |
80 | 1.3 | 80 | 0.25 | 35 | |
100 | 1.2 | 100 | 0.24 | 33 |
由上表可以看出,在相同的温度下,随着加药量的增加,处理效果提高。处理温度大于等于60℃后,在较小的加药量下就有较好的脱水效果,当处理温度为70℃,加药量为20mg/L时,可以直接达到商品油外输的要求。因此,温度是影响离心脱水效果的主要因素。
3.3 微生物处理老化油技术影响因素分析
3.3.1 TD菌种浓度对硫化物及细菌的影响规律
采集污水沉降罐的老化油,按不同比例依次投加TD制剂,放置于50℃恒温水浴中。共进行10d微生物处理试验,每隔2d分别对样品中的SRB细菌和硫化物进行测定。从测试结果可以看出,加药浓度大于等于60mg/L时,药剂对老化油除硫化物和杀菌效果明显,较佳作用时间为6d,老化油中硫化物去除率可达90%,细菌去除率可达99%。
3.3.2 TD菌种浓度对击穿电压的影响规律
每隔2d取生化处理试验中的老化油,装入试验器中,进行击穿电压测试。从测试结果可以看出,在加药浓度60mg/L条件下,反应6d后,老化油击穿电压提高了643%。
3.3.3 TD菌种浓度对界面张力的影响规律
每隔2d取生化处理试验中的老化油,利用表面张力仪对界面张力进行测试,从测试结果可以看出,在加药浓度60mg/L条件下,反应6d后,老化油界面张力降低了58%。
3.3.4 环境因素对TD菌种处理老化油效果的影响
为了确定TD菌种的适用范围,测试了pH值、温度对TD菌种活性的影响规律。
(1)pH值对老化油处理效果的影响
采集污水沉降罐中的老化油,测试pH值为7.32,分别用HCl、NaOH调制不同的pH值,然后投加TD制剂,投药浓度为60mg/L。在55℃恒温条件下处理时间为6d,测试硫化物及细菌的含量。从测试结果可以看出,在除硫化物方面,较佳pH值范围为6.0~8.5;综合考虑,微生物作用于老化油的pH值范围为6.0~8.5。
(2)温度对老化油处理效果的影响
采集污水沉降罐中的老化油,投加浓度为60mg/L的TD制剂后,放置于不同温度的恒温水浴中,测试硫化物的变化情况。从测试结果可以看出,在40℃和90℃时,老化油中硫化物含量下降缓慢,说明TD菌种在低温、高温时活性降低。在50~80℃试验条件下,随着处理时间的延长,硫化物含量逐渐降低,当处理时间超过6d时,硫化物降低幅度趋于平缓。由此可知,微生物活性在50~80℃范围内受温度影响不大。
试验说明,TD微生物作用于老化油的较佳加药量为60mg/L,处理温度为55±5℃,较佳静止沉降时间为6d。考虑到现场生产情况的复杂性,为保证处理效果,可适当提高加药量。
4 老化油处理工艺适应性分析
4.1 老化油处理工艺技术经济对比
热化学脱水工艺、离心脱水工艺、微生物处理技术,这3种老化油处理工艺技术经济对比见下表:
对比项目 | 热化学脱水 | 离心脱水 | 微生物处理技术 |
运行参数 | 破乳剂加入量3000mg/L; 处理温度75~80℃; 处理时间12~20d | 破乳剂加入量20mg/L; 絮凝剂加入量20mg/L; 处理温度70℃; 处理时间:即时 | 微生物投加量60mg/L; 破乳剂投加量20mg/L; 处理温度55℃; 处理时间6d |
处理指标 | 脱水后原油含水率5%; 脱水后污水含油量1000mg/L | 脱水后原油含水率0.3%; 脱水后污水含油量50mg/L; 污泥中含油量2% | 脱水后原油含水率0.3%; 脱水后污水含油量500mg/L |
处理成本/元/m³ | 155 | 24 | 5 |
4.2 老化油处理工艺适应性
热化学脱水工艺运行费用高,处理周期长,但流程简单,技术成熟,适用于老化油产生数量较少的站场,特别是现场有富余沉降罐的站场,流程基本不需改造。
微生物处理技术运行费用较低,但是,需要和电脱水器配套进行脱水,同时,需要控制老化油掺入量。因此,该技术仅适用于老化油产生数量少的脱水站。
对于现场老化油数量较多的战场,建议采用两级离心分离技术。在低转速下有效去除老化油中的固体杂质,高转速下实现油、水分离。该技术虽一次性投入较高,但处理速度快,运行费用相对较低,处理后的老化油可以达到净化油的指标直接外输。
5 结论及建议
自2005年开始,在十年的时间里,试验了多种老化油处理工艺,其中,热化学脱水、离心脱水和微生物处理技术在现场取得了较好的应用效果。但是,各种老化油处理工艺仅仅是一种应急措施,应从根源上解决老化油的产生,建议:
(1)加强生产管理和改造力度,杜绝管道穿孔、跑、冒问题,减少油泥进入生产系统的可能性;对联合站污水沉降罐增建连续收油装置,及时回收污油,避免污油长期存放形成老化油。
(2)加强科研公关力度,采用物理方式对油井、管道、容器进行清蜡、解堵、除垢,减少各种酸的应用,以减少老化油的形成。或者在集输、污水、注水系统加注微生物抑制剂,从根本上避免老化油的产生。