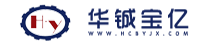
随着油田开发陆续进入中高含水阶段,采出液中的含水率不断升高,包括化学驱在内的各种强化采油措施的相继应用,又使采出液性质变得更为复杂。相应地面系统集中处理站在进行原油脱水时,脱水器、储油罐、污油罐等底部会存在大量含油污泥;在进行污水处理时,沉降除油罐、过滤罐、曝气罐、浮选池及回收水池(罐)底部也会存在着大量含油污泥。与此同时,外围零散油田作为接替储量近年来在不断加大勘探、开发力度,但因产量有限,其采油方式除机械采油外,还有提捞采油,集油过程除管道输送外,还有定期拉油方式,这就不可避免地将产生一部分混合泥土量更大的落地含油污泥。这些污泥成分复杂,属于多相混合体系,一般由水包油(O/W)、油包水(W/O)乳状液以及悬浮固体杂质组成,且乳化稳定性强,粘稠度较大,固相成分难以彻底沉降。
据统计,一个日处理20000m³的油田污水站每天可产生20m³左右的含油污泥。其中,在污水沉降除油段,除油罐的排泥通常有三种方式:一是穿孔管排泥,在罐底设穿孔管,定期排泥;二是水力排泥,在罐底设一个圆锥形的集泥斗或者若干个小集泥坑,用污泥泵将污泥抽出。为了增加污泥的流动性,在罐底周围设一圈冲泥管,在冲泥管上安喷嘴或设孔口;三是人工排泥,清理时需要停产,不需要专门设施,只需在罐底留出较大的人孔,而且要在相对的罐壁两侧都有人孔,以便改善通风条件。在污水过滤段,污泥存在于滤料中,在反冲洗时随反冲洗排水进入回收水罐,回收水罐积存污泥量不断增多,若未及时排出,又会被回收到除油罐,久而久之会造成含油污泥老化,形成恶性循环。
含油污泥成分的复杂性决定了其处理技术的多样性,国内外处理含油污泥的方法主要包括化学热洗涤法、高温热解处理法、调质离心处理法、溶剂萃取法、生物法和微波法等,但各种方法的投资、处理效果和操作成本各异,自然都有一定的适应性和局限性。但总体来看,浓缩、调质、脱水、油水回收、干化及泥饼后续处置是各油田进行含油污泥处理的常规工序,因此,实现减量化处理目标仍是油田地面工程应用技术的主导方向,而降低污泥含水率则是减容的关键。
1 含油污泥组成及浓缩析水特性
含油污泥的主要组成为原油、泥质和水分,其中含油量因污泥来源的不同而各异,水分则大致分为游离水、毛细水、吸附水及内部水等几种存在形式。分别对大庆油田某原油脱水站清淤污泥和污水处理站气浮段产生污泥的组成特性与浓缩析水特性进行了分析。
1.1 含油污泥组成特性
从罐底清淤泥和气浮浮渣泥样品的基本组成特性分析结果,可以看出,含水率高,油、水、泥高强度乳化而形成一种多相体系则是不同类别含油污泥的基本特性,相比于气浮浮渣泥,罐底清淤泥的水含量略低,但油含量高,前者油/泥比约为1:3,后者油/泥比约为5:1,且从DSC曲线分析可知,含油的析蜡特征温度值高,油中蜡质含量占到35%以上,造成体系浓缩脱水后的流动性能差。堆存风干的含油污泥样品外观呈棕黑色,其中,无机盐类的可能组分以碳酸钙、氧化铁及硅铝酸盐为主。
总之,对于油田不同来源的含油污泥,基本都是属于老化原油、水分、蜡质、沥青质、胶体、细菌、盐类、刺激性酸性气体的聚集体,同时还会有投加的各种油田化学助剂及其形成的絮状体,以及设备、管道腐蚀产物及成垢垢质等成分。含油污泥的这种组成特性一方面会由于污泥中大胶体颗粒在脱水器、储油罐、净化污水罐中不断沉积,使清罐周期缩短,清出的大量污泥含水率又高,积存压力大,增加油田地面生产成本投入;另一方面,这类含油污泥的存在导致回注水中悬浮物含量严重超标,堵塞地层,造成油层吸水能力下降,注水压力不断攀升,且会使水井酸化增注措施的有效期缩短,增加措施处理费用和工作量。
1.2 含油污泥浓缩析水特性
在含水率高的同时,悬浮颗粒细小、不利于自然沉降分层是含油污泥的另一主要特点,其中悬浮颗粒的粒径中值在100μm以内,根据Stokes理论,其自然沉降速度应处于中等范围,析水分层能力一般。
在体积标定的玻璃沉降柱(φ80mm×450mm)内,45℃下开展不同含油污泥样品的浓缩析水试验,沉降析水率约在50~60%,表明对污泥先期进行就地集中沉降析水处理,可在一定程度上提高其整体浓缩、减量效果,同时有效减轻后续处置设施的运行负荷及下游大量污水的再回收与处置等一系列问题。但相比之下,罐底清淤泥的平均析水率更低,且析水率随沉降时间变化在更短期内即趋于平衡,表现出更强的乳化稳定性。这是因为,一方面罐底清淤泥体系中的油/泥比大,另一方面,集输系统投往罐中的相关油水处理剂沉淀或形成胶团而发生共淤积,均导致了分散相与连续相间的作用更为显著,这也与前面所分析不同含油污泥样品中悬浮粒子的粒度分布行为相吻合。
2 含油污泥调质破乳实验
实现含油污泥的资源化、无害化和效益化,一直是油田地面工程及石油工业环境污染与防治的追求目标。由此陆续发展的各种含油污泥处理技术也都旨在通过破乳使污泥中的原油分离,并回收至脱水站原油净化或外输系统;污水就地回用或排入污水站水处理系统;固相泥质则堆存风干用于铺路基或垫井场。
2.1 调质破乳原理
调质破乳就是通过加药、升温、搅拌调质,使含油污泥中粘度较大的吸附油发生脱附或破乳,从而促使油质从固相粒子表面分离。这种污泥化学调质缘于一系列新型高效高分子破乳剂及清洗剂的发展,破乳剂和清洗剂可以改变含油污泥颗粒的结构形态,破坏胶体粒子族(团)的稳定性,提高污泥的脱水性能。然而,化学助剂的选择、泥水比、搅拌强度、反应温度和时间仍是影响出油率的重要因素。
2.2 调质破乳实验装置及方法
调质破乳实验装置主要由下锥形调质罐(容积25L)、机械旋桨式搅拌系统(0~500r/min)、加药系统、温控系统(0~80℃)及刮板收油、污水取样、泥质排污等部分构成。
实验过程中,首先将沉降预分离后已知含水量、含油量的含油污泥通过加样口倒入下锥形调质罐,至调质腔与集油腔隔板的高度;设置并启动温控系统加热升温,待温度达到实验温度并恒定后,通过加药-清洗泵投加一定量的破乳剂和清洗剂;设置搅拌强度、启动搅拌器,搅拌、匀化,调质破乳过程开始,并同步开始计时;作用一定时间后,打开带式刮板机,将上层浮油收至集油腔,再分别打开取样阀门和排泥阀门,取污水和污泥样品,分别测定水中含油、泥中含水及含油,计算脱水率和除油率,分析调质破乳效果;实验结束后,利用加药-清洗泵喷洒有机溶剂清洗调质罐,并通过排污管排污。
2.3 调质破乳实验结果
实验研究了浓缩析水预分离后,泥、油、水比例不同的脱水站罐底清淤泥和污水站气浮浮渣泥两种含油污泥(见下表)在不同药剂用量、不同温度、不同搅拌强度及不同作用时间下的调质破乳效果。
污泥类别 | 含泥量(%) | 含水量(%) | 含油量(%) |
罐底清淤泥 | 10.38 | 40.51 | 49.12 |
气浮浮渣泥 | 16.12 | 77.78 | 6.09 |
2.3.1 药剂用量的影响
按照破乳剂和清洗剂2:1的掺混投加比例,分别选择了总投加量为30mg/L、50 mg/L、70 mg/L、90 mg/L和120 mg/L的5种药剂用量,在恒温65℃、搅拌速度300r/min、作用时间40min的实验条件下,从调质破乳后污泥脱水率、除油率及水中含油变化特征可以看出,破乳剂和清洗剂的共同调质,使得污泥体系的乳化稳定性明显被破坏,尤其对于油/泥比例较大的脱水站罐底清淤泥,其油相发生大量的脱附而分离,且随着药剂用量的增大,脱水率和除油率均上升。同时,当药剂投加量在50~90mg/L时,脱出水含油量急剧下降并趋于稳定。
2.3.2 处理温度的影响
分别选择50℃、55℃、60℃、65℃、70℃和75℃的处理温度条件,在搅拌速度300r/min、药剂用量(破乳剂和清洗剂的掺混投加比例为2:1)70mg/L、作用时间40min的条件下,从调质破乳实验后污泥脱水率、除油率及水中含油变化特征可以看出,温度对化学调质作用效果的影响显著,与污泥中含油的析蜡特征参数相吻合,当处理温度达到65℃以上时,两类污泥的破乳脱水率分别能达到20%和35%以上,破乳除油率分别能达到60%和30%以上,且气浮浮渣泥破乳分离污水中的含油量能控制在1000mg/L左右。
2.3.3 搅拌匀化速度的影响
依次设置50r/min、100 r/min、200 r/min、300 r/min和450 r/min的搅拌强度,在恒温65℃、药剂用量(破乳剂和清洗剂的掺混投加比例为2:1)70mg/L、作用时间40min的实验条件下,从调质破乳后污泥脱水率、除油率及水中含油变化特征可以看出,对于等量的药剂投加,搅拌匀化速度过低,在相同作用时间内的调质破乳效果不明显,而搅拌匀化速度过高,则由于构建更充分的二次乳化条件而使体系的破乳过程受到抑制,导致污泥脱水率、除油率有所下降,特别是造成污水含油量大大增加,恶化破乳分离污水的水质。
2.3.4 调质作用时间的影响
在恒温65℃、药剂用量(破乳剂和清洗剂的掺混投加比例为2:1)70mg/L、搅拌速度300r/min的条件下,改变调质作用时间条件:20min、30min、40min、50min和60min,同理,可得调质破乳后污泥脱水率、除油率及水中含油变化特征,可以看出,作用时间延长,化学调质分离的效果不断改善,实验污泥脱水率、除油率及分离水含油量变化的拐点均在30min以上的区间。
总之,调质破乳过程对于提高不同类别含油污泥的脱水性能、实现不同类别含油污泥的减容、减量具有重要作用,针对模拟实验所选污泥样品,认为适合的药剂用量(70mg/L)、65℃左右的温度、适中的搅拌强度(300r/min)与30~60min的作用时间是污泥调质工艺过程的基本操作参数。
3 含油污泥减量化处理工艺
充分重视含油污泥的减容预处理,从而以调质破乳-机械脱水工艺为途径,选择物理化学法相结合的离心分离技术,进行含油污泥的减量化处理工艺设计。
3.1 处理工艺设计及流程描述
按照预处理减容、化学调质破乳、机械离心脱水的工序,设计含油污泥“三段式”减量化处理工艺。
其中,沉降池用于上游来含油污泥的析水减容,然后由提升泵将含油污泥泵入调质罐;调质罐用于减容预处理后污泥的加药调质、搅拌匀化和破乳分离,在罐体入口处加药,对污泥进行调质,增强油和泥的脱附,并罐体内部设搅拌装置,可对罐内调质体系进行搅拌匀化;经调质后的污泥从罐体底部由螺杆泵输送至板式换热器升温,然后经二次加药充分混合,进入后续的离心分离单元进行机械离心脱水、减量;离心机优选卧螺式离心机,调质破乳后的污泥进卧螺机进料仓内,加速后由螺旋上的进料孔进入转鼓内,在离心力的作用下,进入转鼓内的污泥很快分成两层:较重的固相沉积在转鼓内壁上形成沉渣层,沉渣被螺旋推料器推送到转鼓小端面,在锥形段进一步脱水,进而从转鼓小端的出渣口被甩出转鼓;而较轻的液相则形成内环分离液层,作为油水混合物外输;工艺中板式换热器通过蒸汽锅炉进行热源的供给。
3.2 处理工艺单体设备选择
根据所设计“三段式”减量化处理工艺的流程及其描述,下表列出了该处理工艺的主要单体设备。
序号 | 处理单元 | 主要单体设备 |
1 | 减容预处理 | 污泥沉降池 |
污泥提升泵 | ||
排油(水系统) | ||
2 | 调质破乳 | 调质罐(带搅拌) |
螺杆泵 | ||
加药装置 | ||
换热器 | ||
蒸汽锅炉 | ||
3 | 机械离心脱水 | 加药装置 |
卧螺式离心机 | ||
排油(水)系统 | ||
排泥系统 | ||
4 | “三段” | 管道、阀门 |
电气电路与自控 |
4 结论及认识
(1)油田含油污泥因来源不同而具有各异的组成特性,但基本都属于老化原油、蜡质、沥青质、胶体、细菌、盐类及大量水分等的聚集体,悬浮粒子的粒径中值小于100μm,自然沉降析水率不超过60%,乳化稳定性强。
(2)调质破乳在降低含油污泥的稳定性、提高其脱水性能、实现其减容、减量方面有着至关重要的作用。实验结果表明,适合的药剂用量(70mg/L)、65℃左右的温度、适中的搅拌强度(300r/min)和半小时以上的作用时间是调质过程的基本工艺操作参数。
(3)基于预处理减容、化学调质破乳、机械离心脱水的工序,设计了含油污泥“三段式”减量化处理工艺,并综合主体工艺结构及动力源、热源等各方面,按照功能要求选择了主要的单体设备。