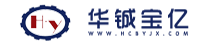
石油的开采、生产、炼化等各个阶段都会产生含油污泥,这些污泥包含了大量的悬浮固体和油,还包含各种化学添加剂等有害物质,如不及时处理,将会对油田的生产和发展以及周围环境带来很多危害。随着 环保要求的日益严格和监管制度的逐步完善,石油化工企业对含油污泥的处理愈加重视,含油污泥减量化、资源化、无害化成为必然的发展趋势。含油污泥成分的复杂性决定了其处理技术的多样性,但减量化是含油污泥处理的关键环节。含油污泥含液率降低之后,可以降低后续污泥处理难度和设备负荷,明显减少后续处置费用。目前在含油污泥减量化过程中常用的设备为叠螺机或两相离心机,但脱水后的油泥含水率在70%以上,且无法实现原油的回收。本文采用调质-三相分离工艺对含油污泥进行减量化处理后,通过化学调质加三相离心机可使含油污泥脱水后的含固率达到40%以上,同时实现油、水、泥的三相分离。文中详细考察了药剂种类与用量,加热温度、离心转速与离心时间对含油污泥减量化效果的影响。
1 实验方法
1.1 含油污泥种类及性质
原油开采和加工过程中产生的含油污泥主要是石油和石油产品在贮罐中沉积的罐底油泥和处理含油废水过程产生的隔油池底泥、浮渣等。本文选取胜利油田某采油厂石油储罐清罐底泥和胜利油田某炼化厂污水处理池底泥,其具体成分见下表:
含油率/% | 含水率/% | 含固率/% | |
清罐底泥(QG) | 12 | 80 | 8 |
污水厂底泥(WS) | 5 | 91 | 4 |
1.2 含油污泥调质-三相分离处理工艺
含油污泥首先经过油浴锅进行加热、搅拌,加热到一定温度后,先后加入一定量的破乳剂、絮凝剂,搅拌反应30min后进行离心分离,对分离出的油、水、泥进行分析测试。
1.3 试剂与仪器
破乳剂:油泥高效破乳剂P-A(含NP-10);专效破乳剂HW-07(含四乙烯五胺聚氧乙烯醚);絮凝剂:三氯化铁(FeCl3),配制成质量分数30%的溶液;阳离子聚丙烯酰胺(CPAM),配制成质量分数2‰的溶液。RE-52AA型旋转蒸发器;TP-214型电子天秤;DF-101S集热式恒温加热磁力搅拌器;TDL-5-A型实验室离心机;OIL460型红外测油仪。
2 结果与讨论
2.1 药剂种类与用量对含油污泥减量化效果的影响
含油污泥乳化状态稳定,直接进行离心处理无法实现油、泥、水的分离,因此需要运用物理、化学方法对其进行调质处理,破坏其乳化状态,促使油、泥、水的分离。本文中采用加热-加入化学药剂的方法对含油污泥进行调质。传统的药剂选择均为单一的破乳剂组合或者单一的絮凝剂组合,本文中考察了不同的破乳剂与不同的絮凝剂进行组合的效果。将含油污泥加热到70℃,设定离心机转速为4000r/min,离心时间设定为10min,实验中考察了8种药剂组合,分别编号(括号中为投加药剂质量分数)为1#P-A(1%)、2#HW-07(1%)、3#FeCl3(1%)、4#CPAM(1%)、5#P-A(1%)+FeCl3(1%)、6#HW-07(1%)+FeCl3(1%)、7#P-A(1%)+CPAM(1%)、8#HW-07(1%)+CPAM(1%)。根据离心后出泥中的含油率、含水率、含固率对含油污泥减量化效果进行评价。
从评价结果可以看出,无论针对污水厂底泥还是清罐底泥,单纯添加破乳剂或絮凝剂时含油污泥的减量化效果较差,破乳剂与絮凝剂配合使用可明显提高含油污泥的减量化效果。这是因为含油污泥溶液充分乳化,污泥颗粒表面吸附同种电荷,性质稳定,使得油、水、泥分离比较困难。由于破乳剂的界面活性高于乳状液中成膜物质的界面活性,加入破乳剂后能在相界面上吸附,并且与原油中的成膜物质形成具有比原来界面膜强度更低的混合膜,因此导致油水界面膜破坏,将膜内水释放出来,水滴互相聚结形成大水滴沉降到底部,达到破乳的目的。加入絮凝剂主要是通过吸附架桥或网捕、卷扫等作用使污泥颗粒聚集并生成絮团,进一步加强油、水、泥的分离效果。
清罐底泥的含油率以及乳化程度均高于污水处理厂底泥,因此经过相同调质处理后,其分离出泥中含固率均低于污水厂底泥,含油率均高于污水厂底泥。基于出泥中的含油率可以判断出,破乳剂P-A的破乳效果要优于HW-07。编号7#、8#测试结果中,添加P-A的污水厂底泥和清罐底泥中出泥含油率可低至2%、4%;而添加HW-07的污水厂底泥和清罐底泥中出泥含油率为2.4%、4.5%,说明在分离过程中添加破乳剂P-A可以将含油污泥中更多的油分离出来。
基于出泥中的含固率可以判断出,针对本文中的两种含油污泥,絮凝剂CPAM的絮凝效果要优于FeCl3。编号5#、7#结果中,同样添加1%的破乳剂P-A,使用FeCl3作为絮凝剂的污水厂底泥和清罐底泥中出泥含固率分别为30%与26%;而使用CPAM作为絮凝剂的污水厂底泥和清罐底泥中出泥含固率则分别达到40%与31%。
2.2 破乳剂的不同用量对含油污泥减量化效果的影响
根据2.1中结论,破乳剂与絮凝剂需要配合使用才能达到较好的减量化效果。将含油污泥加热温度设为70℃,离心机转速设定为4000r/min,离心时间设定为10min,以CPAM(添加量1%)作为絮凝剂,分别研究了破乳剂P-A和HW-07的不同用量对含油污泥减量化效果的影响。
由研究结果可知,随着破乳剂P-A加量的增加,污水厂底泥与清罐底泥分离后出泥中含油率逐渐降低,但在P-A加量超过1%以后,泥中含油率趋于稳定并且在超过2%以后略有上升趋势,因此P-A的较佳用量为1~1.5%。不同用量破乳剂HW-07对含油污泥调质-三相分离后出泥中含油率的影响趋势与破乳剂P-A类似。由研究结果可知其较佳用量为1%。
2.3 絮凝剂的不同用量对含油污泥减量化效果的影响
设定加热温度为70℃,离心机转速为4000r/min,离心时间为10min,以P-A(添加量1%)作为絮凝剂,分别研究了不同添加量的絮凝剂P-A和HW-07对含油污泥减量化效果的影响。
由研究结果可知,随着絮凝剂CPAM加量的增加,污水厂底泥与清罐底泥分离后出泥中含固率呈现先升高后降低的趋势,CPAM的较佳用量为1.5%,CPAM的用量超过2%以后出泥中含固率出现明显的下降趋势。不同用量絮凝剂FeCl3对含油污泥调质-三相分离后出泥中含固率的影响趋势与破乳剂P-A类似。由研究结果可知其较佳用量为2%~2.5%。
2.4 工艺参数对含油污泥减量化效果的影响
2.4.1 不同温度对含油污泥分离效果的影响
通过上述实验确定破乳剂需要与絮凝剂配合使用才能得到较佳的含油污泥减量化效果,较佳药剂组合和用量为P-A(1%)+CPAM(1.5%)。在离心机转速为4000r/min,离心时间10min的情况下,研究了不同温度下含油污泥的减量化效果。
由研究结果可知,随着温度的升高,含油污泥三相分离后出泥的含固率逐渐升高,减量化效果逐渐提高。污水厂底泥和清罐底泥在80℃时出泥含固率分别达到40%和34%,远远高于20℃时的10%和12%。随着温度的升高,含油污泥粘度降低,油水分离趋势增强。超过80℃以后,温度的升高对含油污泥减量化的影响基本不大,因此反应温度应控制在80℃。
2.4.2 不同转速对分离效果的影响
在药剂组合和用量为P-A(1%)+CPAM(1.5%),加热温度为80℃,离心时间为10min的基础上,研究了离心机不同转速对含油污泥减量化效果的影响,分别测试了在离心转速为2000、3000、4000、5000、6000r/min下含油污泥分离后泥中含固率的变化。
由测试结果可知,随着离心机的转速逐渐升高,分离后出泥中的含固率逐渐提高,减量化效果不断增强。污水厂底泥和清罐底泥分离后的出泥含固率分别从2000r/min的24%和20%升高到4000r/min时的41%和34%。经过加热-加药剂预处理之后,含油污泥中的乳化状态已经被打破,油、水、泥已经彼此分开,需要借助离心机的离心力进行加速分离,转速越大,离心力越大,分离效果越好。超过4000r/min后,再提高转速已经不能进一步促进含油污泥的减量化效果,因此较佳离心速度为4000r/min。
2.4.3 不同离心时间对分离效果的影响
在药剂组合和用量为P-A(1%)+CPAM(1.5%),加热温度为80℃,离心速度为4000r/min的基础上,研究了离心机不同离心时间对含油污泥减量化效果的影响。
由研究结果可知,随着离心时间的增加,含油污泥调质-三相分离后的出泥含固率有明显提高,污水厂底泥和清罐底泥分离后的出泥含固率分别从2min的25%和20%升高到10min的39%和33%。乳化状态被打破的含油污泥,游离的油分子、水分子和泥颗粒在离心力的作用下实现聚集、分层。当离心时间超过10min后,再延长离心时间对进一步提高含油污泥的减量化效果作用很小,因此较佳离心时间为10min。
3 结语
含油污泥性质稳定、乳化充分、不易分离,采用加热同时添加破乳剂与絮凝剂可实现含油污泥的破乳,促进油、水、泥的分开,再通过离心分离的方式即可实现良好的减量化效果。
破乳剂P-A(1%)配合絮凝剂CPAM(1.5%)使用,可使污水厂底泥和清罐底泥经调质-三相分离后的出泥含固率分别达到40%和31%。由实验得知,调质-三相分离工艺中反应温度为不低于80℃,离心速度不低于4000r/min,离心时间不低于10min。