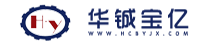
炼油污水处理场在处理炼油污水时要产生油泥、浮渣、活性污泥等固体废弃物。含油污泥主要来源于浮选产生的浮渣、回收的污油脱水产生的油泥、隔油池池底泥的排放等,是石化工业的主要污染源之一,炼油污水中含油污泥的油含量一般为4%~8%,含水率为60%~80%,其余的是固体物质如泥、砂、微生物胶团体、悬浮物和絮凝剂的聚合物等。一般中小型炼油厂年产污泥上万吨。如果不进行处理,直接排放,堆积到自然环境中,其中的有害物质和石油烃类,会随着雨水的冲刷严重污染土壤和环境。污泥长期露天堆放处理,很多低分子挥发性污染物会挥发到空气中,对大气产生污染,同时污泥在厌氧条件下会产生大量硫化氢,对周边空气环境造成影响,甚至对人员生命安全构成威胁。
在处理含油污泥的过程中,用真空过滤机、板框压滤机及传统的静置储存方法进行处理,分离效率低,分离效果差。乌鲁木齐石化公司净化水厂经过多年的摸索实践,发现利用转筒式离心机进行含油污泥的脱水处理是一种能耗少、效果显著的方法。
1 转筒式离心机的工艺流程
通常,含油污泥都要经过初步的预沉降脱水,将大量黑水和污泥分离,减少离心机的处理负荷。经预沉降脱水的污泥进入离心机处理后,分离的清液(离心液)一般用泵打回污水处理系统再处理,干污泥晾晒后或填埋或焚烧。以乌鲁木齐石化公司净化水厂污泥脱水的工艺流程为例介绍如下:将含油污泥 到储存池进行初步沉降脱水,浓缩后的含油污泥由泵打入污泥浓缩罐进一步沉降脱水,脱水后污泥由螺杆泵输送至离心机再次脱水分离。液体(离心液)进入集水池用泵打入污水处理系统处理,固体(离心机出料)运送至堆泥场,污泥干化后外运至废渣坑。
2 存在的问题
2.1 H2S等有毒、恶臭气体溢出
在含油污泥中,往往吸附、溶解了大量的H2S、三苯(苯、甲苯、二甲苯)有机硫等有毒和恶臭气体。含油污泥在通过离心机处理时,在强大的离心力作用下,污泥的稳定态被打破,吸附、溶解在污泥中的硫化氢等有毒、恶臭气体被析出,空气中有浓烈的恶臭味。据测定,离心机机房、离心机出料间内H2S严重超标,特别是离心机出料间内H2S高达100mg/m³以上(安全指标为<10mg/m³)。这类气体的排放,在很低的浓度下,就可以堆人体感官产生刺激和不适,长期呼吸这些有害气体可导致很多疾病发生,直接危害人体健康。在这种环境下工作,对职工身体健康和生命安全带来了威胁,同时由于恶臭味很重,即便戴上防毒面具有时也能感觉到恶臭味,使人感到不适,给调节操作带来了困难。
2.2 絮凝剂选择不合理使用
含油污泥在自然状态下是非常稳定的。通过自然静置沉降能分离出一部分清水,这部分清水一般占总体积的15%~40%,剩余的含油污泥呈稳定的悬浮状态,密度一般在0.97~1.05g/cm³之间。转筒式离心机的处理原理是:混合物料中,如果存在比重不同的物质,离心机高速旋转产生离心力,物料中几种物质所受到的离心力也不同,质量大的污泥被甩到外侧,比重小物质留在中间,通过差速器产生的差速,使得内置螺旋输送机可以将被离心挤压的污泥推向出料口,比重小的水或其他物质从离心液出口溢流出去,固液得以分离。而自然状态下的含油污泥比重接近1g/cm³,而且非常稳定,类似于胶体物质。如果直接用离心机处理,效果很差,往往无法实现固液分离。在含油污泥进入离心机处理之前,投加一定量的絮凝剂,将含油污泥通过物理化学作用絮凝成大颗粒,这种絮凝固体含水率低、比重大,便于离心分离。含油污泥稳定性强,对絮凝剂的选择性也强。选用合适的絮凝剂对含油污泥处理效果的影响比较大,絮凝剂选择不合理,含油污泥絮凝效果不好,离心机就无法发挥作用。
2.3 絮凝剂加注点选择不正确
絮凝剂加注点距离心机的距离实际上就确定了絮凝剂和含油污泥混合反应的时间,大部分絮凝剂对絮凝反应效果都有时间要求。反应时间短,絮凝没有完成,絮凝固体不够密实,比重和水差距不大,离心分离的效果不好;反应时间长,絮凝好的固体颗粒在管线里被继续输送的过程中,会在压力、摩擦力、液体湍流的作用下解体,液体中的悬浮颗粒又回到稳定状态,离心分离效果同样不好。不正确的加注点选择,造成分离效果的明显降低。
2.4 间歇运行后开机震动大
离心机处理效率比较高,有时需要停运待料。但有时开机时震动很大会经常出现刚开机时机体震动超标,离心机连锁停车。有时离心机勉强运行起来,几分钟后,震动会减轻。但有时又出现出料口堵塞现象,影响分离效果。
2.5 对高含固量污泥处理效果差
实践证明,当处理的污泥中含固量高时处理效果不好,这时离心液是黑色液体,这种黑色液体类似胶体溶液,比较稳定,静置沉降分离出来的清水很少。这种黑色液体打入水系统重新处理,会使大量污水都变成黑色,而隔油和浮选都不能有效处理这种黑水,往往对生化单元造成水质冲击。
3 分析与对策
3.1 H2S等有毒、恶臭气体的收集排放
离心机机房、离心机出料间有大量有毒、恶臭气体溢出的主要原因是,离心机运行震动较机泵要高的多,国产离心机一般在设计中没有考虑机体出料口和出料线以及离心液出口和出液线的封闭。离心机运行时,从泥中析出的H2S和其他恶臭气体从这些地方溢出。对出料口和出料线之间以及离心液出口和出液线之间用橡胶柔性接头连接,即避免了离心机震动对其他设施的影响,又防止了恶臭气体从接口溢出。
出料间污泥出口和运泥车不可能封闭,离心机出料口和离心液出口封闭后,H2S和其他恶臭气体会大量从这些地方溢出。通过在出泥和出液线和离心机机体连接的位置增加排气管,并将排气管向上延伸到离心机房顶部以上2m的位置,形成烟囱效应,大部分气体被抽出排向大气,避免了H2S等有毒、恶臭气体在机房和推泥间的聚集。另外,在推泥间增加强制通风机,对室内空气置换。
经实际测定,采取以上措施后,操作空间的恶臭味大大减轻,H2S含量可控制在3mg/m³以下。
目前,很多污水处理装置都配套了消除恶臭气体的装置,将收集的恶臭气体输送到恶臭气体消除装置,将从根本上解决离心机处理含油污泥过程中产生的有毒、恶臭气体对环境污染和对人体的毒害。
3.2 絮凝剂的选择
通过实验,对含油污泥的处理,用无机的聚合铝、聚合铝铁做絮凝剂效果都不理想,通过交流和考察以及絮凝剂筛选小试得知,使用阳离子聚丙烯酰胺做絮凝剂对含油污泥有较好的絮凝、处理效果。对分子量不同的聚丙烯酰胺进行试验,得出使用分子量>1.5×106的阳离子聚丙烯酰胺效果较好。对几种絮凝剂试验结果见下表:
样品名称 | 沉淀颗粒大小 | 沉淀颗粒密实度 | 静置沉淀情况 | 离心后液体比例(%) |
聚合铝 | 无絮状颗粒 | - | 无分层 | 少量混浊清液 |
聚合铝铁 | 无絮状颗粒 | - | 无分层 | 少量混浊清液 |
阴离子聚丙烯酰胺 | 较小 | 松散 | 无分层 | 25%,较混浊 |
阳离子聚丙烯酰胺 (分子量1500000) | 大 | 较密实 | 无分层 | 50%,其中有10%的带油混合物在上层 |
阳离子聚丙烯酰胺 (分子量4000000) | 大 | 较密实 | 无分层 | 55%,其中有10%的带油混合物在上层 |
备注:絮凝剂按200g/t污泥投加,搅拌时间都为3min,静置时间都为15min。
从上表可以看出,分子量>150×104的阳离子聚丙烯酰胺可以产生较好的絮凝效果,但往往分子量越大,价格越高,因此使用时要注意经济效益比较。阳离子聚丙烯酰胺在投加前需要充分搅拌混合,并在搅拌状态下放置4h以上,才能发挥较好的絮凝效果。聚丙烯酰胺溶解性差,配药时容易结块,要求溶药设备有较强的混合搅拌作用。
3.3 絮凝剂加注点位置的确定
不同的絮凝剂絮凝反应时间有一定的区别,不同地方的物料性质差距也较大,同时不同的工况,不同的混合手段都会给加注点的位置造成影响,一般应该先了解清楚絮凝剂的特性,然后在实验室进行反应时间的初步确定,有条件的可以进行实际实验。通过实验室小试,阳离子聚丙烯酰胺絮凝速度较快,加注点不能距离心机进口太远。在距离心机进口0.5m、2m、10m三个位置设加药口投加聚丙烯酰胺,通过对比试验确定,使用距离心机进口2m的加药口的效果较好。
3.4 间歇运行开机震动的分析解决
通过对离心机运行观察和解体检查发现,振动大的主要原因是离心机转筒内存在附着的污泥,造成开机时转筒失去动平衡。造成的原因是停机前水冲洗不彻底,离心机转筒中有些粘度较大的泥没有被洗出来。通过试验,将停机前的水冲洗时间从15min延长到25min~30min。在开机时当离心机空载运行平稳后, 清水运行,平稳后再进污泥,这样会提高离心机运行的稳定性。
3.5 高含固量污泥处理
通过实际运行试验,离心机处理高含固量污泥,需通过重复二次处理的办法解决。 次处理出料处能出大量泥,离心液为黑色水。将这些类似胶体溶液的黑色液体收集后再经过离心机处理,可以产生大量清水,清水可以用泵打到污水系统处理。 次处理加药量应控制在300g/t污泥左右,二次处理加药量应控制在200g/t污泥左右。
4 结语
在解决了运行中存在的问题后,利用转筒式离心机对粘度较大的含油污泥进行脱水处理效果较好,经过离心机分离后,离心出料在堆泥场堆放一段时间后,在空气、阳光的作用下由黑色粘稠状变为黄色粉末状。给运送储存节约了大量的人力、物力、财力。是一种高效、便捷、低能耗的处理含油污泥的有效手段。