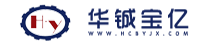
1 引言
碟式分离机是一种多功能、高效率的薄层分离机械,普遍应用于橡胶、制药、食品等行业。同其他分离机械相比,碟式分离机械在结构上有其独特之处,主要表现为:
(1)转鼓由一百多个零件组成,各个零部件之间有精确的相对位置。
(2)立轴由两个滚动轴承支撑,其中上轴承安置在由6根径向弹簧组成的弹性支承上。
(3)立轴系统由1对螺旋齿轮驱动,该对螺旋齿轮用于增速传动。
因而碟式分离机具有同其他机械不同的故障形式,采用通常的方法不能有效地监测和诊断,有必要对碟式分离机的主要故障进行详细的分析。
2 弹簧失效
立轴的弹性支承由轴向弹簧和径向弹簧组成,轴向弹簧主要是用来缓冲安装转鼓时造成的冲击,一般不易失效。径向弹簧直接影响到立轴系统的动力特性,主要作用之一是降低立轴系统的临界转速,使碟式分离机的工作转速位于立轴系统的第一阶和第二阶临界转速之间。第二个作用是缓冲和减振,减少由立轴系统传到机座上的振动。
径向弹簧长期处于较大的交变应力的作用下,如果应力超过了弹簧材料的疲劳极限,就会出现疲劳裂纹,弹簧的刚度就会下降,进而会发生弹簧的断裂。正常情况下,6根径向弹簧的刚度基本相等,弹性支承在各个方向上的当量刚度也基本相等,如果发生某根弹簧的刚度下降甚至是断裂,就会造成各个方向上当量刚度的不一致。这样不但会降低缓冲减振效果,而且会增大其余弹簧的负荷,使振动加剧,后果不堪设想。在各个方向上支承刚度的不同,就会导致振动幅值的不同,在当量刚度下降的方向上,转鼓的振动幅值增大,而在机座上该方向的振动幅值却下降,可以根据这一特性有效地诊断出弹簧的失效。
另一种诊断弹簧失效的方法是:用2只电涡流式位移传感器分别测出2个相互垂直的方向上的振动位移,再用计算机处理并绘制出转鼓的轴心轨迹,正常情况下轴心轨迹是近似的圆,发生弹簧裂纹或断裂后,轴心轨迹会变成明显的椭圆。
然而,在工作情况下,碟式分离机的转鼓被机壳罩住,要安装电涡流式位移传感器就必须拆去机罩,这样既不方便又影响正常的生产,可以采取以下方法加以解决:用2只加速度传感器分别测量垂直方向上的振动加速度,再经过窄带滤波,通带的中心频率等于转鼓的旋转频率,带宽尽可能的窄,以便消除其他振动的干扰,对得到的信号再进行两次积分,便可以得到只与转鼓的选择频率相关的振动位移信号,同样可以用计算机绘制出转鼓的轴心轨迹。
3 转鼓不平衡
碟式分离机的转速很高,一般在7000r/min左右,而且转鼓的尺寸大、重量大,很小的偏心就会引起较大的振动,过大的振动可能造成以下不良后果:一是增加轴承的动载荷;二是影响螺旋齿轮的啮合,增加了齿与齿之间载荷的不均匀性,同时也加大了齿轮承受的动载荷,缩短了齿轮的使用寿命;三是转鼓碰到机壳或进、排液管。因此,转鼓不平衡是碟式分离机常见而且后果严重的故障。转鼓的不平衡主要表现为转鼓旋转频率成分的幅值增大。根据不同的发生原因,转鼓不平衡故障可分为以下两类:
(1)转鼓在使用过程中产生的永久变形。
转鼓高速旋转过程中,转鼓的各个部分处于强的离心力场的作用下,工作较长一段时间(5~6年)后,转鼓会产生一定的永久变形,而且锁紧大螺母在拧紧过程中,用力不当,也可能造成永久变形,这种变形破坏了原有的平衡状态,产生了新的不平衡。另外,物料同转鼓长期直接接触,会腐蚀转鼓,也会造成不平衡。在不太严重的情况下,可以用现场动平衡的办法加以校正。因为这种方法不但简便、效果优良,而且耗时少,对生产的影响也小。
(2)碟片松动。
正常情况下,转鼓体内安装有一百多片碟片,碟片、转鼓盖、锁紧大螺母之间的相对位置是靠准确的相对安装定位尺寸和转鼓盖的压紧力来保证的,各个零部件的不平衡量合成为一个总的不平衡量,在机器出厂前已经校正。
转鼓旋转时,碟片处于离心力场的作用下,如果碟片组件的质心偏移产生的离心力不能克服静摩擦力时,碟片同转鼓体相对静止。如果碟片间的压力不足,转速达到一定时,离心力就会大于碟片间的静摩擦力,碟片就会沿径向产生移动,从而产生新的不平衡。从以上的分析可见,由碟片松动造成的不平衡量是一个不稳定量,因此不能用通常的动平衡方法加以消除。
以前诊断碟片松动的方法主要是通过升速和降速时的幅频曲线。当转速升到4000r/min时,振幅由18μm突跳到40μm,而转速降到4000r/min时,振幅却没有突降。经分析可知,升速曲线上4000r/min时振幅的突跳不是由共振引起的,而是由碟片松动错位引起的,降速时要使错位的碟片复位,只能靠转鼓的变形的减少来实现,而转鼓的变形随转速的降低逐渐减小,因此降速曲线上没有振幅的突降,升、降速曲线画到一起时就形成了一个封闭的区域。该方法对压得比较紧时的松动现象相当有效,对于比较松的情况,就必须结合相频曲线才能达到满意的结果。
4 轴承的失效
大多数碟式分离机采用滚动轴承来支承横轴和立轴系统。在正常的使用条件下,滚动轴承主要有以下失效形式:
(1)点蚀
由于碟式分离机采用了螺旋齿轮传动,所以支撑立轴和横轴的滚动轴承不但要承受径向载荷,而且要承受较大的轴向载荷,滚动轴承的内圈、外圈和滚动体等元件处于复杂的应力状态下,这种应力可以看作是脉动循环交变应力,当应力超过疲劳极限时,在经过若干次的循环以后,元件的表面一定深度处产生裂纹,继而扩展到接触表面,便形成了点蚀,从而引起剧烈的振动和噪声。
(2)永久变形
对于碟式分离机来说,转鼓尺寸较大,不平衡是经常出现的故障,由于转速较高,不平衡所引起的冲击载荷是相当大的,一旦轴承元件上的应力超过了材料的屈服极限,就会造成永久变形。永久变形所引起的振动同点蚀引起的振动的表现形式非常相似,只是永久变形产生的冲击的脉冲宽度要宽一些。
在使用维护和保养不当或密封润滑不良时,滚动轴承也会出现磨损、胶合、内外圈和保持架的破裂等不正常的失效形式。
5 螺旋齿轮的失效
同其它大多数的机器一样,齿轮失效也是碟式分离机的主要故障之一,和其它机器相比,碟式分离机的齿轮传动有独特之处。首先,它的横轴和立轴相互垂直,采用了一对螺旋齿轮传动,主、从动齿轮沿齿槽方向有高速滑动。其次,一般机器的工作转速低于原动机的转速,因而,齿轮主要是用来减速的,而碟式分离机却恰恰相反,它的工作转速很高,因此,这对螺旋齿轮就被用作增速传动,这就决定了它的失效形式主要有以下几种:
(1)胶合
齿轮件的高速滑动会产生大量的热量,对于碟式分离机来说,由于采用了闭式齿轮传动,不利于散热,这就使齿轮和润滑油的温度升高,润滑油的粘度下降,降低了齿面间油膜的承载能力,温度高到一定程度时,油膜受到破坏,齿面间直接接触,虽然青铜有较强的抗胶合能力,但在温度高、齿面间压力大的情况下,也会发生胶合,继续转动就会撕破啮合面,降低啮合精度,产生大量的振动和噪声。提高齿轮的加工精度,降低齿面的粗糙度,采用含有抗胶合添加剂的润滑油可以减少胶合的发生。
(2)磨损
齿面的粗糙度较大,油温较高或者润滑油被水等所污染时,齿面间的油膜不足以将两齿面分离开,齿轮转动时就会出现磨损。另外,对于新机器来说,跑合期结束后,应更换润滑油,否则润滑油中的金属颗粒,会对齿面造成磨粒磨损。
(3)塑性变形
大螺旋齿轮的齿圈大多用青铜制造,因而表面硬度较低,如果存在转鼓不平衡,齿轮偏心或精度不高,碟式分离机工作时将产生较大的振动,从而增加了齿面间的动载荷,很容易造成齿面的接触应力超过齿轮材料的屈服极限,引起齿面塑性变形,降低了齿轮的啮合精度,产生较大的振动和噪声。
(4)点蚀
构成螺旋齿轮副的齿面是点接触,虽然传递的动力并不太大,但齿面间的接触应力仍然是很大的,齿轮旋转过程中,齿面受脉动循环交变应力作用,接触应力超过材料的疲劳极限时,就会出现点蚀。由于青铜疲劳极限低于钢的疲劳极限,因此,往往大螺旋齿轮首先出现点蚀。
在监测齿轮振动时,传感器不可安装在齿轮上面,只能安装在机座上。而齿轮的振动是通过齿轮、轴、轴承这一途径传播到机座上的,因此,测到的振动信号就不只是齿轮振动所产生的信号,而是由齿轮、轴、轴承的振动信号以及一定量的噪声的混合信号。要想从这个混合信号中取出齿轮或轴承的振动信号,必须根据齿轮或轴承的固有特性,再采用解调等手段加以处理。
6 结语
本文系统地阐述了碟式分离机的主要故障,给以后的状态监测和诊断工作打下了一个良好的基础。每一种故障都有其表现形式,为了能够准确地监测和识别碟式分离机的工作状态,首先要从现场测得振动或噪声信号,并对这些信号加以处理,在时域、频域或时频域中提取出每种故障的特征信息,就可以采用有关的理论加以识别。