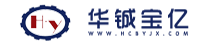
卧式螺旋沉降式离心机是由外壳、转鼓、传送装置、齿轮箱、反向传送装置等组成。物料由入口送到转鼓内,转鼓以高速旋转并通过离心力的作用将固体和液体有效的分开,然后通过螺旋传送装置对固体物料进行回收。某厂回收离心机是卧式螺旋沉降式离心机,它通过离心力的作用,对废液中的产品进行回收,并送回系统继续使用。由于离心机的转速很高(大于3000rpm),因此离心机在平时的运转中振动很大,平均每三个月需要对转子检修一次,每次检修转子需要耗费大量的人力、物力、财力、维修成本高昂,而且离心机检修时间长(平均每次检修时间为3天),每次检修都会造成大量的废液损失。因此,针对“延长离心机运转时间”短这一难题进行原因分析及改进,以拉长运行周期,提高经济效益。
1 延长离心机运行时间的必要性
离心机由于转速高、振动大,在高负荷运转时,运转周期短、检修费用高,且没有备用转子,在检修时使废液中的有效成分不能有效回收,损失较大。离心机每隔三个月都需要停车检修一次,平均每次对离心机进行检修的费用为7.6万元。如果要确保装置安全稳定运行,降低离心机检修费用,必须延长离心机运转时间。
2 影响离心机运行时间的因素分析及对策
(1)通过对离心机的检修记录分析,离心机发生故障的主要部位有两个:①螺旋轴承损坏,且轴承内有腐蚀痕迹;②转鼓轴承损坏。
(2)针对离心机发生故障的两个基本原因进行确认、修理、改造、其方法、措施如下:
2.1 提高油封质量,修理油封夹持器缺陷
由于物料中含有大量腐蚀性很强的酸,检修时发现油封变硬而无弹性;油封夹持器有效配合面有点蚀的情况。这两种情况都会引起轴承进酸腐蚀损坏,造成离心机运转时间缩短。
措施:油封由国产改为进口氟橡胶件,提高耐酸等级,油封购买环节严格按照物流程序购买,入库前进行质量检验,做耐酸实验。油封夹持器表面腐蚀利用耐蚀性较强的修补剂修补后用车床精加工。
2.2 调整转子总窜量
离心机在运转过程中轴承温度一直处于较高状态(55度以上)。经现场测量发现转子总窜量仅为0.25mm,过小,是引起轴承损坏的原因之一。
措施:查阅离心机制造厂家资料,增加调整垫片,把转子总窜量调到0.6mm,试运转后轴承温度明显下降。
2.3 电机没有有效定位
在现场检查确认时发现电机(材质为铸铁)定位板断裂,电机在离心机转鼓的作用下,易发生偏移,使电机皮带轮和转鼓皮带轮不在同一条直线上。造成皮带发出异常声响,使离心机转鼓受力不均匀,产生振动,导致离心机使用寿命降低。
措施:由于原设计定位板材质为铸铁,可焊性很差,已不能重新焊接使用。通过现场研究,决定取消原设计方案。在电机前后轨道方向另加工3个定位块,定位块选取合适位置加工M16螺纹通孔,并用M16×100双头螺栓(2个螺母)对电机机座紧固。通过调整螺栓的活动量来对电机进行灵活准确定位。
增加3个定位块后,紧固螺栓对电机进行了有效的定位,确保了电机在高负荷运转时的牢固性和稳定性。电机皮带轮和转鼓皮带轮不在同一条直线上的问题得到了很好的解决,减少了转鼓的振动,延长了离心机的运转时间。
2.4 气封气源压力低,且不稳定
为了防止酸液进入轴承系统,离心机制造厂家设计了气封系统, 在设备运转时对气封系统充入压力为0.06MP的工厂风,阻断酸途经气封系统进入轴承系统,达到保护轴承的目的。现场检查发现,由于工厂风脏而入口滤网堵塞,造成气源压力波动,并且风压力0.06MP时不能有效阻止酸进入轴承内,从而易导致轴承被腐蚀。
措施:选择干净的仪表风作风源,重新配管,增加减压阀,并把气封系统充入压力提升为0.08MP(多次实验获取的数据)。调整后,离心机检修时没有发现气封系统过酸的现象,从而保护了轴承,延长了离心机运行时间。
2.5 离心机处理能力小
查阅离心机制造厂家资料,离心机额定进料量是1吨/小时。现场流量计显示平均进料量是1.2吨/小时。这说明当前离心机的处理能力小于进料量,引起离心机振动,导致离心机使用寿命降低。
措施:为了兼顾固、液两相的回收率及处理能力的大小,在液相出口设计闸板和调节处理能力的闸板阀。经过反复计算,决定调节闸板阀的溢流直径。使它的溢流直径由4½英寸减少到4英寸。闸板阀的溢流直径减少后,增加了固态的回收率,加大了废液中液相的排出量,大大减少了废液中液相在离心机转鼓内的停留时间。从而使离心机的处理能力满足了当前的正常下料量,减少了离心机的振动,延长了离心机的运转时间。
3 效果检查
自从离心机进行技术攻关改进后,进行了较长时间的跟踪观察。在一年的时间里,离心机不论是在平常运转中,还是在完成系统操作弹性方面,都能达到预期的目标。而且离心机只停车检修一次,确保了生产装置长周期安全稳定运转。
4 结束语
近几年来实践证明,通过技术改进,离心机运行时间短的瓶颈问题得到了全面解决,确保了设备的安全稳定长期运行,取得了良好的经济效益;同时其性能稳定性,基本达到了同行业国际先进水平。