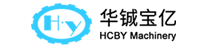
1. Structure and working principle of horizontal decanter centrifuge
1.1 Structure of horizontal decanter centrifuge
Horizontal decanter centrifuge is mainly composed of drum, screw, differential gear, feed inlet, liquid outlet, solid outlet, liquid level baffle, drive system and control system.
1.2 Working principle of horizontal decanter centrifuge
Due to there is a density difference between solid phase and liquid phase, the centrifuge realizes the solid-liquid separation by accelerating the settling speed of solid particles under the action of centrifugal force. The sludge and flocculant solution are fed into the mixing chamber in the drum through the inlet pipe to be mixed and flocculated. Because of the high-speed rotation and frictional resistance of the rotor (screw and drum), the sludge is accelerated inside the rotor and forms a cylindrical liquid layer. Under the action of centrifugal force, the solid particles with higher density will settle to the inner wall of the drum, and be pushed to the cone section of the drum by the screw. After dewatering, the sludge will be discharged from the slag outlet, and the liquid will be discharged from the liquid outlet.
2. Model selection and structural parameters analysis of horizontal decanter centrifuge
2.1 Characteristics of industrial sludge
The main characteristics of industrial sludge are as follows:
(1) High impurity content. Compared with domestic sludge, the content of fiber and mechanical impurities is higher.
(2) High solid content. The SS concentration in the industrial sewage is generally between 800-1200mg/L, and the dry mud volume per ton of sewage is up to 0.7-1.1 kg.
(3) It is easy to produce corrosive gases such as ammonia and hydrogen sulfide. Because many industrial raw materials contain chemical agents and organic substances, ammonia and hydrogen sulfide and other gases will be produced during decomposition, which are highly corrosive.
2.2 Selection of centrifuge
According to the characteristics and management requirements of the sludge, it is necessary to choose horizontal decanter centrifuge with compact design, high separation efficiency, good airtightness, continuous and automatic feeding.
2.3 Analysis of structural parameters
2.3.1 Drum diameter and effective length
The diameter and effective length of the drum determine the effective settling area of sludge in the process of centrifugal dewatering, which directly affects the treatment capacity of the centrifuge. The centrifuge with large drum diameter and long effective length has a larger settling area, which prolongs the residence time of the sewage in the drum. Under the same rotating speed, the separation effect is better.
2.3.2 Half cone angle of drum
The size of the half cone angle of the drum directly affects the slag conveying speed and dewatering effect. For industrial sewage, the half cone angle is usually controlled between 8°-10°, which is conducive to improving the slag conveying efficiency.
2.3.3 Rotating speed of drum
The rotating speed of the drum directly determines the separation effect. When the water content of the mud cake is high and the curing effect is poor, the rotating speed of the drum should be increase to increase the centrifugal force, so as to increase the solid content of the mud cake. However, the rotating speed of the drum should not be too large, otherwise it will destroy the sludge flocculation and affect the dewatering effect. In practical application, it is found that the proper rotating speed of the drum is 2200-2400r/min.
2.3.4 Differential speed
Differential speed is the relative speed between the drum and the screw. When the solid content of the feedstock is more than 3%, the differential speed should be increased appropriately, so as to quickly discharge the sludge. When the solid content of the feedstock is less than 3%, the differential speed should be decreased, so as to prolong the sediment time, increase the sediment thickness, and improve the solid content rate and sludge recovery rate.
3. Frequent problems and solutions in operation management
3.1 Frequent problems in the early stage of commissioning
3.1.1 Turbid filtrate and low sludge recovery rate
The sludge recovery rate mainly depends on the concentration of suspended solids in the dewatering filtrate. If the concentration of suspended solids is high, the filtrate will be turbid. Some sludge will not form mud cake, but will be discharged with the filtrate and return to the sewage collection system, which will reduce the sludge treatment efficiency of the centrifuge.
In the early stage of commissioning, in addition to considering whether the ratio of sludge and agent is reasonable, the height of the liquid level baffle in the centrifuge is also need to considered. The height of the liquid level baffle directly affects the effective settlement volume and the length of the drying zone of the centrifuge. When the depth of the liquid layer in the drum is too small, the solid particles will be discharged with the liquid, the sludge recovery rate will be reduced. Therefore, when the ratio of sludge and agent is reasonable, but the filtrate is still turbid, it may be effective to appropriately increase the height of the liquid level baffle.
3.1.2 Blockage of the drum
(1) One kind of blockage occurs in the start-up period, the motor will overload and five an alarm. After inspection, it is found that there is dry sludge in the drum. When the amount of the sludge is small, it can be washed by water. When the amount of the sludge is large, it is necessary to open the cover and pull out the screw for washing.
(2) One kind of blockage occurs in the operation process, which is a human-made operation problem. When the sludge concentration is high, and the differential speed is low, it will extend the sediment time, and the sediment layer will be too thick, resulting in the blockage in the drum. At this time, the differential speed can be increased to eliminate the fault.
(3) Another kind of blockage is caused by the accumulation of solid impurities in the industrial sludge, such as common plastic waste. As the plastic sheets are flexible and not easy to be broken by the cutting machine, it will be attached to the inner wall of the drum and form blockage after long-time accumulation. In order to solve the similar problems, we can change the cutting machine from extrusion cutting to blade cutting, and regularly wash the drum.
3.2 Frequent problems in operation
3.2.1 Change of sludge properties
The degree of sludge corruption in industrial sewage has a great influence on sludge properties. When the fiber in the sludge is short (usually accompanied with corruption), the sludge will have high viscosity, and will be difficult to be dewatered. The change of temperature also has a great influence on the sludge properties. When the temperature is low, the negative charges of the activated sludge are less than when the temperature is high. The activated sludge contains more viscous substances, and has higher hydrophilia, so the activated sludge will be difficult to settle. Therefore, it is necessary to decrease the feeding rate, and increase the dilution ratio of the agent, so as to increase the contact area between the sludge and the agent and improve the dewatering effect.
3.2.2 Improper application of flocculants
In the aspect of sludge dewatering, cationic polyacrylamide is generally used to reduce the specific resistance of the sludge, so that the sludge will be easy to be dewatered. Improper application of flocculants will result in poor sludge dewatering effect, low sludge recovery rate and waste of agents.
Therefore, the molecular weight of the polyacrylamide should be no less than 10 million, and the ionic degree should be 50%-70%.
3.2.3 Influence of corrosive gas
In the process of industrial sludge dewatering, corrosive gases such as hydrogen sulfide and ammonia are often produced, which are harmful to the centrifuge. The components of the control system such as inverter, LCD screen and controller will be broken down due to corrosion. Therefore, it is better to place the control cabinet in another room, so as to avoid corrosion, and prolong the service life.
4. Conclusion
(1) Horizontal decanter centrifuge is suitable for industrial sludge treatment.
(2) The key to the operation and management of horizontal decanter centrifuge is to keep the balance of sludge, centrifuge and flocculants.