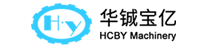
In the municipal sewage treatment, in order to avoid secondary pollution caused by sewage sludge, sludge treatment and disposal has become a very important part. With the continuous improvement of municipal sewage treatment process, more and more municipal sewage treatment plants have eliminated the sludge concentration tank in order to save the occupied area, and directly input the low-concentration precipitated sludge after the aeration treatment to the horizontal decanter centrifuge by screw pump for concentration and dehydration.
Sludge formation
The municipal sewage enters the aeration tank after removing the inorganic particles with high density through the grit chamber. The organic matter in the sewage in the aeration tank is degraded under the metabolism of microorganisms. After sufficient aeration, the sewage is allowed to stand still, and the flocs containing a large number of microbial micelles and ciliate protozoa can be precipitated to form sludge.
This kind of sludge has the characteristics of high organic content, small sludge particles, small relative density, strong water holding capacity, low sludge solid content (measured sludge solid content is between 0.426% and 0.854%) and so on.
Technological process of complete equipment for sludge concentration and dewatering
The complete set of equipment for sludge concentration and dehydration mainly includes: horizontal decanter centrifuge, sludge cutter, sludge feed pump, automatic flocculant dosing system, electromagnetic flowmeter, shaftless screw conveyor and electric control system.
The sludge to be treated is fed into the horizontal decanter centrifuge by the sludge feed pump through the sludge cutter. The flocculant is added into the sludge pipeline before the feed port of the horizontal decanter centrifuge. the sludge amount and flocculant amount are measured by the electromagnetic flowmeter respectively. The sludge cake dehydrated by horizontal decanter centrifuge is transported to the hopper or truck by shaftless screw conveyor, and the separated liquid is discharged back to the original sewage treatment system for secondary treatment.
Selection of flocculant
Flocculation can be divided into two processes: one is the charge neutralization between polymer electrolyte and particle surface, and the other is the formation of flocs by bridging long chains of polymer electrolyte and particles. The main purpose of flocculation is to agglomerate the fine suspension particles and colloidal particles into coarser particles or flocs by adding polymer flocculant. According to Stokes equation, the sedimentation velocity is proportional to the square of the particle diameter. With the increase of particles, the sedimentation velocity increases greatly. Thus, the residence time of sludge in the horizontal decanter centrifuge can be greatly shortened, which provides a strong guarantee for the continuous treatment of sludge dewatering.
It is very important to select suitable flocculant in the sludge dewatering. The selection of flocculant should be based on the principle of high quality, low price, high efficiency and low dosage. Generally speaking, cationic flocculant is suitable to add into organic sludge, while anion flocculant is suitable to add into inorganic sludge. Municipal sludge is mainly organic sludge with a certain amount of negative charge, so cationic flocculant is selected. Theoretically, the larger the molecular weight of flocculant, the higher the flocculation efficiency. But the molecular weight of flocculant is too high to dissolve, and is very expensive.
According to practical application, the molecular weight of flocculant is about 8 million. The best dosage of flocculant is that all flocculants are adsorbed on the surface of solid particles, and the settling speed of flocs reaches the maximum value. However, it is very difficult to find out the best dosage of flocculant. Based on the practical application and previous research results, the dosage of flocculant for municipal sludge is generally 0.3% ~ 0.5% (the ratio of absolute dry flocculant to absolute dry sludge).
Determination of operation parameters of horizontal decanter centrifuge
Separation factor is very important for separated materials. Therefore, when the diameter of the drum is determined, the rotating speed of the drum directly affects the separation effect. Too small speed can not meet the separation requirements, but too large speed also affects the service life of the machine. The practical application of horizontal decanter centrifuge shows that the best separation factor for municipal sludge dewatering is 2000 ~ 2200.
The size of the differential speed mainly depends on the amount of slag to be discharged. If the differential speed is too large or too small, the separation effect will be affected. This time, because the municipal sludge is treated with low concentration, the total solid content is less, and the required differential speed is relatively low. On the premise of meeting the separation requirements of users, 4-6 r / min is selected.
On the premise that the rotating speed of horizontal decanter centrifuge is fixed, the influence on the solid content of mud cake is analyzed by changing the differential rotating speed. Because there is a direct relationship between the differential speed and the amount of slag discharged, it is more practical to select a group of data from the sample which is close to the total amount of sludge solid to discuss. With the decrease of the differential speed from 6 r / min to 3 r / min, the increasing trend of the solid content of mud cake slows down. Therefore, when the differential speed is reduced to a certain value, it is not meaningful to further reduce the differential speed to increase the solid content of mud cake.
When the operating parameters of horizontal decanter centrifuge and the total sludge solid content are basically unchanged, the solid recovery rate increases first with the increase of flocculant dosage, and then decreases when the flocculant dosage reaches a certain amount. So the dosage of flocculant is not the more the better, it has an optimal value. Since the cost of flocculant accounts for the main part of the whole operation cost, the dosage of flocculant should be minimized on the premise of meeting the separation requirements.
Conclusion
For low concentration municipal sludge dewatering, cationic flocculant with molecular weight over 8 million is an ideal flocculant.
When the operating parameters of horizontal decanter centrifuge and the total amount of sludge solid entering the centrifuge are fixed, the solid content of sludge cake increases with the decrease of differential speed.
When the operating parameters of horizontal decanter centrifuge are fixed, the solid content of sludge cake decreases with the decrease of sludge concentration.
After a long period of use, the horizontal decanter centrifuge has stable performance and good operation. It is an ideal equipment for low-concentration sludge dewatering.