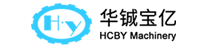
In order to fully understand how a decanter centrifuge operates, we must first define what a centrifuge does. In many industrial jobs, solid material often mixes with liquids, contaminating water supplies or turning mud into sludge.
A decanter centrifuge is useful in that it separates solids and liquids, and has become an essential component of water waste facilities and the chemical, oil, and food processing industries. Moreover, without a centrifuge, many of these companies would become so inefficient they could not function.
There are several types of decanter centrifuges currently utilized in the industry, the most common of which are vertical, horizontal and conveyor centrifuges. The principle behind a decanter centrifuge is based on the theory of gravitational separation.
For example, if you fill a glass with a mixture of mud and water, over time the weight of the mud will cause it to settle down at the base of the glass. With the mud congealed at the bottom, the water will be forced upwards, creating a clear separation between the two.
A decanter centrifuge, as well as a tricanter centrifuge, employs the same principles of gravitational force. However, unlike the glass mixture, the process is expedited through the use of continuous rotation.
In fact, rotation provides anywhere from 1000 to 4000 times the normal gravitational force, reducing the time required for separation from hours to seconds.
The concept of rotational separation is similar to rides found at amusement parks and county fairgrounds. In these rides, placing yourself at an angle allows you to overcome the gravitational forces induced by rotation.
Similarly, a decanter centrifuge is essentially a bowl tube that rotates at an extremely high speed. The bowl tube is equipped with an internal conveyor which moves in the same direction but at a different velocity.
How the Decanter Process Works
Step 1
The slurry is inserted into the centrifuge through a connecting pipe and onto a conveyor.
Step 2
Utilizing an internal feed compartment, the conveyor ushers the slurry through a nozzle into the bowl area.
Step 3
The bowl rotates at high speeds to induce gravitational forces.
Step 4
High speed rotation separates the solid material from the liquid in a matter of seconds.
Step 5
The conveyor delivers the solid material upwards where it is discharged through a nozzle.
Step 6
The solid material removed, the purified liquid is released from a separate output.
The Main Sections of Decanter Centrifuges
1. Inlet zone
The inlet zone accelerates the feed slurry up to the speed of the bowl. A properly engineered inlet zone keeps any degradation of the feed solids to a minimum as well as avoiding disturbance of the sediment in the bowl.
A number of feed zone specifications are available for decanter centrifuges, each designed to ensure maximum performance in conjunction with a specific process.
2. Screw conveyor
The key to good decanter performance lies in the efficient, effective scrolling of the sedimented solids. The design of the screw conveyor is therefore crucial.
You must have the expertise needed to match the demands involved in specific industrial processes with specific configurations of flight pitch, lead angle and differential speed, in order to secure the best possible results.
3. Solids Discharge Section
Depending on the application, the consistency of the separated solids can vary from a dry powder to a paste. The configuration of the discharge zone is therefore chosen to enable such “cakes” to exit as effectively as possible.
Innovative designs enables erosion-prone components used in the solids discharge zone to be replaced on site at low cost and with a minimum of disturbance to production.
4. Liquid Discharge Section
In a two-phase decanter, the liquid level is regulated by dam plates. In a three-phase centrifuge when operating in a three-phase mode, each phase discharges over a set of dam plates into separate baffled compartments in the casing.
In certain applications, a centripetal pump discharge that utilizes the pressure head developed by the rotating liquid phase is used to pump the liquid from the decanter.
Crucial Factors That Determine Performance of Decanter Centrifuges
1. The centrifugal force required for sedimentation of the solids
2. The clarification area necessary to “capture” the solids
3. The differential speed required to transport the solids out of the decanter
4. The hydrodynamic design, which determines the exact parameters for the turbulence
5. The design of the conveyor and beach sections, which are important for efficient solids transportation.
In specifying a decanter centrifuge for a particular application, a series of other specific design considerations has to be taken into account:
1. The pitch of the conveyor
2. Feed zone design
3. Beach angle
4. Bowl surface
5. Abrasion resistance
6. Materials used in construction
Centrifuge Applications and Uses
The ability to purify a liquid makes decanter centrifuges ideal for waste water treatment facilities, as well as oilfield sites for solids control applications. However, there are variety of industries for which such centrifuges play an important role.
Most recently, the use of centrifuges has been popularized in the hemp manufacturing industry. Centrifuges are utilized during the extraction of oils from hemp. Users benefit from cannabis and CBD extraction equipment with effective process solutions in centrifugation.
Similar to other decanter equipment, centrifuges are simple to install and do not require a foundation to build upon. Their efficiency saves time and materials and is an essential component for many blue collar industries.
Advantages and Limitations Over Competitive Processes
Generally the decanter centrifuge has more advantages than disadvantages; however there are some limitations when compared to other processes.
Advantages
1. Decanter centrifuges have a clean appearance and have little to no odor problems.
2. Not only is the device easy to install and fast at starting up and shutting down, but also only requires a small area for operation compared to other competitive processes.
3. The decanter centrifuge, as well as the 3 Phase Centrifuge, is versatile as different lengths of the cylindrical bowl section and the cone angle can be selected for different applications. Also the system can be pre-programmed with various design curves to predict the sludge type, while some competitive processes, such as a belt filter press, cannot change the belt type to operate for different sludge types. Its versatility allows the machine to have various functions such as operating for thickening or dewatering.
4. The machine can operate with a higher throughput capacity than smaller machines. This also reduces the number of units required.
5. The device is simple to optimize and operate as it has few major variables and reliable feedback information.
6. The decanter centrifuge has reduced labor costs compared to other processes, as it requires low continuous maintenance and operator attention.
7. Compared to some competitive process such as the belt filter process, the decanter centrifuge has more process flexibility and higher levels of performance.
Limitations
1. The decanter centrifuge cannot separate biological solids with very small density differences, such as cells and viruses.
2. The machine can be very noisy and can cause vibration.
3. The device has a high-energy consumption due to high G-forces.
4. The decanter centrifuge has high equipment capital costs. Hard surfacing and abrasion protection materials are required for the scroll to reduce wear and therefore reduce the maintenance of the scroll wear.