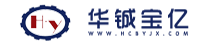
本文中的铜矿湿法冶炼项目均采用粗碎+半自磨+球磨+硫酸浸出(带搅拌)+CCD洗涤+萃取-电积回收金属铜工艺。主要的数据来自于刚果(金)+冈波夫(Kambove)湿法炼铜项目,年产3万t阴极铜,其铜钴矿位于科卢韦齐市(Kolwezi)以东35km处,临近卢阿拉巴河(Lualaba River),地处丹加铜矿带上,主要是孔雀石形式的氧化铜矿,矿石均在地层浅表泥化严重处并含有大量的有机物。
传统上采用板框压滤机来清除在萃取和反萃取工艺段产生的萃取铜矿三相污物,但实际运行下效果不佳,铜矿三相污物没有有效分离导致影响萃取效率,造成萃取剂和溶剂油的浪费,给企业造成较大的经济损失。如今采用了三相卧螺卸料沉降离心机,成功将铜矿三相污物分离至其原状态即水相、有机相和固相,提高了萃取效率,保证了生产运行。
1 三相污物
1.1 组成和成因
在湿法炼铜的工艺过程中,在萃取和反萃取工艺段会产生铜矿三相污物,这种污物成乳化状,其主要包含了细微的悬浮颗粒、有机污染物,溶解的盐类、气泡、类石膏含硅物(胶状二氧化硅)等等固体悬浮物,有机相Organic和水Aqueous。
固体悬浮物大部分在酸浸工段随料液进入澄清池(用料液反复精滤也无法避免),其包括未分解的矿石颗粒及有机污染物,溶解的盐类,类石膏含硅物也会随之进入后续的萃取工段,部分固体细粒具有润湿性,易强烈吸附,聚集成为悬浮状的乳剂,这部分固体悬浮物及降解的萃取剂、溶剂油和水混合形成铜矿三相污物。铜矿三相污物的成分组成中一般含5%~10%固体悬浮物(以下简称固相)Solid;40%~60%水相Aqueous;50%~70%有机物Organic。铜矿三相污物进行完全烘干,并制样送检分析,从结论来看,其中的固相主要成分是二氧化硅,之后依次顺序是铁、锰、铝及其他。
1.2 铜矿三相污物的影响
铜矿三相污物长期存在,会占用澄清室的体积,进而影响了萃取的效率,一旦被夹带至电解工段,则会污染电解液,引起阳极板的烧坏,直接影响产品质量甚至停工。即使定期打捞,也会引起有机相流失,增加材料成本。而其固相污物如果处理不当仍然有大量溶剂油,去填埋会直接破坏环境,甚至会因为太阳暴晒引发火灾。
2 铜矿三相污物的处理方法
2.1 传统的处理方法
传统工艺中,主要使用板框压滤机,当液体通过过滤介质后,固体颗粒被截留从而到达固液分离的效果,随着生产中萃取剂污物的增加,很容易把滤布堵住,效率会越来越低,经常需要更换滤布。而且存在占地大,敞开式易形成二次污染,人员劳动强度高等不利因素,关键水相和有机相仍处于混合状态,当三相污物除去渣后回到萃取系统中,会产生如下的问题:
(1)pH值产生波动影响萃取的整体效率。
(2)回收有机物整体纯度不佳,影响整体工艺。
(3)有机物回收率不高,造成经济浪费。
(4)电解工段受到间接影响,铜板的质量不佳。
2.2 卧螺卸料沉降式离心机主要工艺参数
型号:Z4E-4/441SP3.10;处理量:6~8m³/h;长径比:4;锥角:8°;长宽高:3750×900×1200mm;重量:3000kg;转速:4000r/min;差速:1~20r/min;扭矩:2750Nm;分离因数:3380g。
2.3 物料主要工艺参数及处理要求
进料量 | 6~8m³/h |
温度 | ≤40℃ |
氯离子含量 | ≤1.5g/L |
pH | 0.5~2.0 |
H2SO4含量 | ≤35g/L |
有机物Organic | 50~70%v/v SG<0.85 |
水溶液Aqueous | 25~60%v/v SC>1.11 |
悬浮颗粒Solids | <10%v/v SG>2.6 |
分离后要求 | |
有机相回收率 | >97% |
水中的有机物 | ≤3%v/v |
有机相中的水含量 | ≤0.5%v/v |
2.4 三相卧螺卸料沉降式离心机工作原理
离心机由转鼓和螺旋输送器构成高速转动的转动件,由皮带传动,并通过齿轮箱带动使转鼓和螺旋之间产生速度差。
需要分离的物料通过中心供料管进入离心机内,在离心力的作用下,密度大的固体沉降到转鼓壁上。液体则因为其二相密度不同的清液形成同心圆柱,较轻的液相处于内层,较重的液相处于外层。不同液体环的厚度可通过调节溢流堰和可变叶轮来改变,即使有机相和水相含量有波动,依然可以在生产中进行精准动态改变以满足要求。沉积在转筒壁上的固体由螺旋输送器传送到转筒体的锥体端,从排料口排入固体集料箱,如果进料的固体含量较高,就要适当调高螺旋差速。
2.5 三相卧螺卸料沉降式离心机的特点
(1)能够将固体,有机相和水相一次分离到位,简化了生产工艺流程,确保分离效果和产品品质,显著减少了工艺设备的总投资。
(2)对物料的适用性能力强,能分离的固相粒度相对范围广(5~100μm),固相粒度出现偏离时也可以在生产中不停机调整分离效果。
(3)紧凑而简洁的设计,使用维护占地面积小,确保能极大限度利用工厂场地。
(4)机器运转可以实现PLC-DCS控制、能自动连续长期运转,减少人员配置。
(5)螺旋输送器叶片的前端采用了碳化硅SiC硬质合金保护加强,使用寿命更长。
2.6 经离心机分离处理后的效果
生产实践情况证明,经过离心机分离处理后,其效果见下表所示:
固渣Solid | 干度能达到≥75% |
有机相Organic | 含固量低于0.3%,含水量低于1% |
水相Aqueous | 有机物含量为1%~3% |
(1)生产工艺诉求是较大限度的获得足够纯净的有机相Organic,所以三相离心机的参数设置也是较大限度满足目前品质需求,得出的有机相回收率稳定在97%~98%,其纯净度也接近99%,这样非常纯净的有机物产品,对后续工艺继续使用有保障,足以保证使用效率。
(2)根据生产实践证明,三相污物在进入离心机前的混合罐内,假如少许的高岭土,能够有效净化有机相中的杂质,使固相能够加速凝聚,对于后续三相离心机能成功分离出纯净的有机相有较大的帮助。
2.7 三相卧螺卸料沉降式离心机使用注意事项
(1)按操作规程进行开停机。
(2)定期按流程进行清洗操作。
(3)注意按照操作规程进行定期加注润滑油脂。
(4)定期巡检,注意机器运转时的声音和检测轴承振动值,出现问题要及时排除。
(5)机器需要长期停止使用时,注意按照操作规程封存保护。
3 经济分析
3.1 经济效益
过去使用传统板框式压滤机仅能处理固渣,无法有效回收大量有机物。使用三相卸料卧螺沉降离心机可产生明显的经济价值。
平均每吨铜产量可以节约萃取剂0.5kg,溶剂油3kg。目前,公司每年设计生产电积铜3万t,按此计算,每年节约萃取剂15t,溶剂油90t。萃取剂和溶剂油成本分别为8万/t和1万/t,保守估计,年均节约成本超过200万,1~2年即足以收回成本。
3.2 环保效益
铜矿三相污物被分离后,有机相Organic返回至萃取工段,水相Aqueous将返回至中和池,两者均会被循环再利用。固渣综合处理后送至尾矿库进行干堆填埋。整体环保效益显著。
3.3 运行成本
(1)根据离心机操作规程,每天需要定量手动加注一次专用润滑油脂(约2g),每半年需要对内轴承加注一次专用油脂(40g),每年需要对齿轮箱更换一次齿轮箱油(约3L),年维护费用不超过1万元。
(2)离心机在正常运行20000h建议做一次维护保养,主要是检查轴承,并确认密封件以及皮带状况。
(3)三相离心机自动化程度高,全过程人机界面,通过PLC-DCS通讯至中控室可以远程直接一键启动后,智能自动运行,多重逻辑保护确保工艺生产设备安全运行,同比传统的铜矿三相污物处理方法可以节省大量人力成本。
4 结语
综上所述,通过使用三相卧螺卸料沉降离心机高效处理铜矿湿法冶炼中产生的铜矿三相污物,收回了大部分高品质的有机相Organic,使萃取剂和溶剂油的消耗分别控制在了2.5kg/t.Cu和10kg/t.Cu,并且保证了产品的质量。整个工艺的优化不仅有效回收了有机相Organic,并且减少了工艺的复杂度并降低了污染,并能够在有限的时间内就能实现成本回收,实现了经济效益和社会环境效益的双赢。