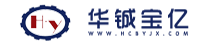
含油污泥是油田开发生产过程中,在钻井、压裂、试采、作业、原油处理、含油污水处理、原油储运等方面产生的主要污染物之一。随着原油开采的不断深入,我国各大油田每年都有大量的油泥产生,这些油泥得不到及时处理,将会对生产区域和周边环境造成不同程度的影响。油田含油污泥已被 列为危险固体废弃物(HW08),随着 对环保要求日趋严格,含油污泥减量化、无害化、资源化处理成为油泥处理技术发展必然趋势。
1 含油污泥来源及危害
油田、炼厂的污水处理场(如隔油池底、曝气池、浮选池等)存在着大量含油污泥。同时在原油脱水中,脱水罐、污油罐、储油罐等底部也存在大量油泥。根据其来源不同,可将其分为清罐油泥、落地油泥、作业油泥、炼厂油泥等。这些污泥成分复杂,属于多相体系,一般由油包水(W/O)、水包油(O/W)及悬浮固体组成,黏度较大,固相难以完全沉降,处理难度大。
含油污泥体积庞大,若不加以处理直接排放,将会对周围土壤、水体、空气造成污染。含油污泥含有大量的原油,造成土壤中石油类超标,土壤板结;散落和对方的含油污泥污染地表水甚至地下水,使水中COD、BOD严重超标;含油污泥中的油气挥发,使生产区域内空气质量总烃浓度超标;含油污泥中还含有硫化物、苯系物、蒽、芘、酚类等有害物质。因此,从环境保护和能源回收角度出发,对含油污泥进行处理非常重要。
2 含油污泥处理研究现状
含油污泥处置的重点和难点在于减量化,含油污泥性质复杂、种类繁多、产量大,不进行有效的减量化工作,就难以有效的对其进行无害化及资源化处理。减量化的关键在于含油污泥的除油和脱水。化学法是利用化学药剂处理含油污泥,提高除油脱水效率的一种方法。国内外现在对含油污泥的化学处理方式主要包括表面活性剂洗脱法、破乳剂脱水法、化学混凝法、溶剂萃取以及综合利用等方法。
2.1 表面活性剂洗脱除
表面活性剂具有亲水亲油双重特性和特殊吸附性能,能显著降低液-液界面的张力,从而能使油从污泥中脱除,具有操作简单、适应性强、经济高效的优点。马少华等合成了一种新型磺酸盐型阴离子表活剂,用其对油泥进行脱除研究。结果表明:油泥处理量为0.5g,处理温度为45℃,处理20min,稀释比为10:1时,脱除率高达99.60%。
张力文等考察了吐温80、吐温20、十二烷基苯磺酸钠、十二烷基硫酸钠四种表面活性剂对含油污泥的洗脱效果。当表面活性剂质量浓度大于100mg/L时,表面活性剂增溶能力吐温80较大;吐温80质量浓度为100mg/L,洗脱温度为25℃时,时间为4h,pH为6,脱油率可达到86.25%。
李明采用含表面活性剂的热碱水溶液洗涤处理大庆油田含油污泥,使用十二烷基苯磺酸钠和Na2SiO3与非离子表活剂进行复配。结果发现:十二烷基苯磺酸钠:Na2SiO3:平平加-20为1:2:1,在反应时间30min,反应温度为70℃,液固质量比为5:1的条件下,油回收率达到了99.35%,回收的油中含油89.82%。
Jing Guolin等研究了表活剂AEO-9、Tritonx-100、九水偏硅酸钠、平平加和十二烷基苯磺酸钠分别在液/固质量比、反应时间、反应温度等因素影响下的残油率。结果表明:九水偏硅酸钠在较佳工艺条件下处理含油污泥时,残油率只有1.6%。
2.2 破乳剂脱水法
破乳剂可以取代吸附在界面的天然乳化剂,降低界面膜的粘性、弹性和强度,加速液滴的聚结,使其在重力作用下沉降到底部,进而使其油水分离。
Mahmoud A.Abdul-Raheim等发现蔗糖脂肪酸酯聚氧乙烯醚可作为破乳剂处理含油污泥。研究结果表明:GA4000可脱去约90%水。
刘晓兵研究了DS-06/DL-11正反两种破乳剂的复配配比和实验效果。结果表明:DS-06/DL-11两种破乳剂以30:10复配破乳,污油脱水时间可大大缩短,且脱水效率高。现场应用结果表明,呼和浩特炼油厂加药量在复配浓度为180mg/L时,3天后污油含水率小于1%。
李培芳等通过对试验前后污油罐详细的含水量分析和罐顶及罐底的含盐量分析,研究了破乳剂QAD-03在胜利炼油厂污油中的使用情况。研究结果表明脱水后污油含水、含盐达到了常减压装置的原油加工要求,取得了良好的工业应用效果。
曾浩见等针对落地油泥清洗后产生的污油进行破乳处理实验研究,筛选出一种合适的破乳剂JL-1,其用量为50mg/L时具有较好的破乳效果,污油经过破乳处理后含水率小于5%。
彭柏群等研制了适用于高机械杂质含量污油的破乳剂DS-1。实验结果表明在大庆油田北二联合站水驱沉降罐上部水含量为31%,离心沉淀物含量为6.7%的污油中,投加0.4%污油破乳剂DS-1,在沉降温度为50℃的,经过4.5h后的脱水率可达97%,顶油水含量可降低至0.6%。
化学破乳剂破乳的特点是专一性强,一种破乳剂对某种乳化液有效,当改变对象后可能没有预期效果,适用面比较窄。
2.3 化学混凝法
混凝法是指在混凝剂作用下,使胶体和细微悬浮物凝聚成絮凝体,然后予以分离除去的方法。混凝剂的作用能产生电化学反应,起到脱除细小杂质和泥砂的效果,从而提高除油效率。
李凡修等通过添加絮凝剂处理含油污泥,研究了影响含油污泥脱水性能的主要因素。实验结果表明:PAC絮凝处理含油污泥可使比阻降至1.09×1012mg/kg,CPAM絮凝处理含油污泥可使污泥比阻降至0.11×1012mg/kg,助滤剂CaO与絮凝剂复配使用可降低污泥比阻。
王强采用聚合氯化铝/聚硅酸钠/LSH-703复合药剂为调质剂,对炼油污水处理厂含水率为95.50%~98.50%的含油污泥进行了调质工艺优化实验。结果表明:控制聚合氯化铝/聚硅酸钠/LSH-703投加量依次为120、10、100mg/L,在体系pH值为3.0、温度为60℃、搅拌时间为20min的优化条件下,含油污泥的含水率下降至65.00%。
王丹采用硅酸钠、聚合氯化铝、阳离子型聚丙烯酰胺为原料,制备无机高分子絮凝剂PCSM,结果表明絮凝剂PCSM脱油效果较好。
2.4 溶剂萃取法
溶剂萃取法选取合适的溶剂作萃取剂,利用“相似相溶”原理,溶剂与油泥充分混合发生传质后,将油从水中萃取出来,从而实现油-水-泥三相分离。
申明乐等采用溶剂的方法提取含油泥砂中的原油,将氯仿与含油泥砂混合,在提取器高压作用下挤出大部分原油,再连续通氯仿与含油泥砂加压洗提,可使泥砂中含油量<0.3%。
张秀霞等采用三氯甲烷萃取剂溶解油泥。实验结果表明溶剂体积:油泥质量为3:1,蒸馏时间45min,蒸馏温度400℃,可使油泥脱油率高达90%。
仝坤等采用溶剂萃取处理稠油罐底油泥。研究分别选用柴油、蒽油、酚油、轻质煤焦油和中温煤焦油作萃取剂,经过比较研究,认为轻质煤焦油作萃取剂较为理想。经过处理后的残渣中矿物油的质量分数≤2%,热值≥5000kJ/kg。
车承丹等采用石油醚浸提技术,对辽河油田沉降罐罐底油泥进行处理。含油污泥呈黑色,含油率为50.1%,含水率为35.03%。当温度为45℃,搅拌时间为5min,水加入量为20mL时,油去除率为93.7%。
溶剂萃取方法的优点是普遍适应性强,可应用于不同类型的油泥,能将大部分石油类物质提取回收。然而萃取剂价格昂贵,成本高,并且处理过程中损耗较大,因此普及推广难度大。此项技术的发展关键是要开发出性价比高的萃取剂。
2.5 其他综合利用方法
朱亚东等采用加拿大推出的一种生物降解产品污油降解素OIL GATOR处理污油,研究了处理剂用量,污油含水率及降解时间对大庆污油降解性能的影响。实验结果表明,OIL GATOR的较佳用量为污油量的80%~100%;随着降解时间的增加,降解效果显著,降解时间超过60d,降解素就能达到良好的使用效果。Li Xiaobing等用破乳剂Sx4056,表活剂石油磺酸盐,分散剂硅酸钠处理含油污泥,以残油率作为指标。研究结果表明:在较优条件下,残余的污泥中油的含量仅占0.28%。
韩萍芳等采用超声波技术对石化公司的污油进行了破乳脱水。研究结果发现:在超声波的作用下可以脱除污油中80%的游离水,当加入NSI破乳剂后超声波的处理效果更加明显,可以脱出94%的游离水,污油的含水率可以降到3.8%。
张玉梅等采用超声波破乳脱水的基本原理,考察了超声参数对炼油厂污油破乳脱水的影响。实验结果表明:在声强0.66W/cm2、频率10kHz、作用时间5min、破乳剂用量0.375mg/g、温度70℃、沉降4h的工艺条件,可使污油脱水率在96.3%。
3 结语
目前,我国含油污泥集中处置率低、处置水平低下、二次污染严重。含油污泥的处理已成为石油行业可持续发展的瓶颈。建议在以下几方面展开研究:
(1)各油田含油污泥来源、组成、特点及性质等均有不同,在实际应用过程中根据油田油藏特点、含油污泥性质,及时分级、分阶段处理。
(2)新技术的不断涌现,使含油污泥的处理技术呈现多样化发展。单独选用一种处理技术很难处理达标,因此在实际应用过程中,根据其自身特点、现场需求等,采用多种处理技术如物理-化学、化学-生物有机结合等方式,按照“减量化与再利用相结合”的思路,实现含油污泥的无害化处理。
(3)国外已开发出多种处理技术及配套设备,并在现场实现了规模试验或应用。因此,适当的借鉴国外一些 的处理技术、设备以及管理经验,开发出适于国内油田的经济有效的处理方式。