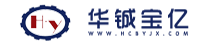
2011年政府颁布《产业结构调整知道目录(2011年本)》明确指出:限制新建氯醇法环氧丙烷和皂化法环氧氯丙烷生产装置。目前在建的氯醇法项目都是已经获批的,原则上今后不再批准新的氯醇法项目。新增产能将以大型的共氧化法装置为主。共氧化法克服了氯醇法三废污染严重、腐蚀大和需求氯气的缺点,大幅度提高了单套装置的生产规模,减少了污水的排放,生成的联产品也提高了环氧丙烷的生产经济性。
在共氧化法生产环氧丙烷装置生产过程中,伴随着丙烯环氧化反应发生的同时,也会生成少量的副产物,例如:苯甲醛、乙醛、苯酚和其他重组分。而甲基苯甲醇(MBA)在脱水生成苯乙烯的过程中产生的重组分更多,主要副反应:MBA→乙苯+重组分。这些重组分在工艺系统内经过碱洗系统碱洗后会包含部分钠盐(主要是苯甲酸钠和苯酚钠),称之为含钠燃料油,其组分为:燃料油 79%,水、钠离子 20%,铬、铜、灰分 1%。
现有工艺条件下,处理这部分含钠燃料油的方法就是将其收集后送至燃料油锅炉进行焚烧,从而达到处理目的,同时回收热量。研究表明钠是造成锅炉内对流烟道积灰的主要原因。随着钠含量的增加,换热器积灰量增多。钠在火焰高温区短时间内可能以原子或氧化物的形式存在,遇到CO2、SO2、O2、SO3生成硫酸钠、碳酸钠。另外钠的化合物熔点低,易与铁、铝、钙、硅的氧化物共融形成较低熔点的共融物,使炉衬腐蚀。共融物随烟气带入锅炉列管,为管束积灰提供了条件。所以在锅炉的正常运行过程中,这部分含钠燃料油燃烧后锅炉的积灰十分严重,大大降低列管的换热率,使蒸汽回收量减少,同时管道也容易堵塞,被迫停炉清洗,给连续生产带来了巨大的困难。因此处理含盐废液的焚烧系统需要对烟气中的盐类进行脱除,目前主要有两种脱除工艺,湿法脱除和干法脱除。此两种工艺均存在缺陷:湿法脱除需要消耗急冷水、无法进行能量回收,同时产生一定量的含盐水;而干法脱除需要增加更多的设备成本以及后期的运行成本。
1 湿法脱除工艺
(1)采用湿法脱除所用到的相关主要设备包括焚烧炉、急冷室、急冷循环泵、文丘里除尘器、洗涤循环泵、雾水分离器。
(2)焚烧后的烟气自焚烧炉出来直接进入布置在其下方的急冷室,在急冷室内高温烟气被迅速冷却至烟气饱和温度约85℃,烟气中的颗粒物在急冷室内被脱除一大部分,急冷后的烟气进入布置在急冷室下游的文丘里洗涤器,在此烟气流速被极大提高,文丘里洗涤器在喉口位置设置了洗涤水雾化喷嘴,高速流过的烟气与细小的雾化水滴在喉口处充分混合,烟气中颗粒被水滴捕捉,从而实现高效除尘。烟气在急冷室通过与急冷水的混合达到被迅速冷却的目的,急冷水通过急冷循环泵打入急冷室上方设置的急冷水雾化喷嘴,细小的水滴能增大与烟气接触面积从而提高烟气急冷速度,从喷嘴喷出的急冷水一部分被气化随烟气进入下游设备,一部分落入急冷室的水空间通过循环泵继续循环急冷,在急冷循环管道上接出一路排水管线,通过定量排水使急冷室内水的盐浓度维持在一定的范围内;洗涤水通过洗涤水循环泵打入文丘里喷嘴,被雾化成细小颗粒,与烟气混合后送入雾水分离器,在雾水分离器内烟气向上排入烟囱,水滴落入水空间通过循环泵继续循环洗涤,在洗涤循环管道上接出一路排水管线送入上游的急冷室,通过定量排水使雾水分离器内的水的盐浓度维持在一定的范围内,雾水分离器通过液位调节补水流量。
2 干法脱除工艺
(1)采用干法脱除的主要设备包括焚烧炉、烟气冷却段、余热锅炉、布袋除尘器、烟气再循环风机、锅炉吹灰系统。
(2)由于烟气中含有无机盐类,并且这些盐类的熔点均在800~900℃的范围内,在炉膛温度1100℃下,这些盐类均在烟气呈现熔融状态,当含有熔融状态盐的烟气流经余热锅炉时,熔融的盐类遇到温度比较低的换热管时会凝聚附着在管壁上,降低换热效率,甚至造成换热管局部受热不均爆管事故,影响系统安全运行。为了保证下游余热锅炉的安全可靠长周期运行,进入余热锅炉前烟气中的盐类需要凝固成固态盐,才能进入余热锅炉,这样余热锅炉就不会造成粘结性积灰。把熔融态的盐类凝固成固态就需要把烟气温度降至盐的熔点以下,并且还要有一定的过冷度和冷却时间。降低余热锅炉进口烟气温度有两种方法,一是引入外来冷源,如加入冷空气或喷水;二是采用余热锅炉排烟回流来降温;采用引入外来冷源的方法将会使热回收效率大大降低,因此不推荐采用,主要的工艺是通过烟气循环风机把余热锅炉的排烟引入余热锅炉进口来降低进口烟温。采用再循环烟气冷却方式,需要沿轴向分级补入,使高温烟气温度逐渐降低,这种急冷方式的优点是凝结的盐颗粒较大,降低了微小粉尘在余热锅炉管壁上积聚(静电吸附)的可能性,同时有利于吹灰。
为了降低钠在燃烧时对炉膛的影响,在含钠燃料油焚烧之前,先使用三相碟片式离心机将燃料油中的钠盐分离出来,再将除钠后燃料油送到锅炉内焚烧。
三相碟片式离心机用于分离两种液体和一种固体。固相自动间歇性排放,两液相均以内置向心泵带压排放。转鼓装在立轴上端,由电机驱动而高速旋转。转鼓内有一组互相套叠的碟片。碟片与碟片之间留有很小的间隙。物料由位于转鼓上部中心的进料管加入转鼓。当物料流过碟片之间的间隙时,固体颗粒在离心作用下沉降到碟片上形成沉渣,沉渣沿碟片表面滑动并脱离碟片并积聚在转鼓内直径较大的部位,经排渣口排出转鼓。轻液相沿锥形碟片向轴心流动至上部轻相向心泵,由轻相出口排出;重液相沿碟片流向转鼓壁,然后向上流经重相向心泵由重相出口排出。碟片的作用是缩短物料的沉降距离、扩大转鼓的沉降面积,转鼓中由于安装了碟片而大大提高了离心机的生产能力。
实际运行效果:
先在燃料油中加入醋酸和去离子水,使钠盐转化为醋酸钠。而醋酸钠易溶于水,从而实现了钠盐由油相至水相的转移。然后需要使用碟片式离心分离机进行各相分离,分离器出料为三相:
(1)含少量残余钠盐的油相,送至焚烧炉。
(2)富含钠盐的水相,送到废水处理。
(3)含有固体的浆相(或渣相),包括主装置催化剂带来的少量重金属(铜、铬),作危废外送。
3 结论
三相碟片式离心机相比传统的离心机具有以下特点:
(1)沉降面积高。
(2)可自动清理固相物。
(3)适用不同含固量的产品。
(4)适用产能范围广。
(5)可进行清洗。
(6)可连续操作。
能有效将共氧化法生产环氧丙烷工艺装置所副产燃料油中的钠除去,有效解决了含钠燃料油燃烧后锅炉的积灰严重的问题。应用到此装置的含钠燃料油除钠工艺,既能增加设备寿命,减少占地面积,又降低运行成本,创造了更高的经济效益。